Nanoparticles of Cerium Oxide - Application to Coatings Technologies

There are advantages brought by cerium oxide nanoparticles for meeting the performance needs of the wood coating industry, particularly for the high-performance field.
As commonly known, we use the name "nanomaterial" to describe a material or a composition built from nanoparticles, which are active as such in the application. The typical size of these nanoparticles is lower than one hundred nanometers (100 nm).
A nanomaterial, under the definition used in this paper, is a dispersion of nanoparticles in a host matrix (e.g., polymer, coating, cosmetic formulation, etc.). Then it is possible to describe three different systems:
- nano primary particles;
- nano secondary aggregates composed of several primary particles; and
- nano tertiary aggregates composed of several secondary particles.
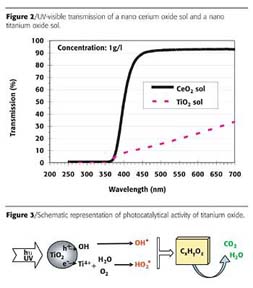
Cerium Oxide Nanoparticles
Today, cerium oxide is largely used in the catalysis field (mainly for diesel engines), and in chemical and mechanical polishing (CMP). However, cerium oxide is also well known for its optical properties and ability to filter ultraviolet (UV) rays. Moreover, Rhodia expertise ensures good size control from 5-nm diameter up to 100 nanometers. We are able to obtain stable sols of cerium oxide nanoparticles with diameters of 10 nm. These sols appear as a clear liquid, since the particles are small enough to be totally transparent. For instance, at the same solid concentration (1g/l) and for similar particle size, a titanium dioxide sol appears milky (Figure 1).Despite their small size, cerium oxide nanoparticles are very effective in term of UV filtration (Figure 2). According to theory, cerium oxide shows a UV cut-off threshold at around 370 nm, similar to that of nano titanium oxide. Cerium oxide and titanium oxide are both semi-conductors (with a band gap around 3.0 - 3.2 eV) and present the same classical UV absorption mechanism: under UV-light illumination, the absorption of a photon with a higher energy than the band gap creates an electron-hole pair.
In the case of titanium oxide, these holes and electrons migrate to the surface of the particles (rather than recombining together inside the particles). When holes and electrons join the surface, they can react with oxygen, water or hydroxyls to form free radicals. This process is currently named "photocatalysis" (Figure 3).
These free radicals are oxidant entities and can cause the degradation of organic molecules, in particular polymers, which can be an important issue for protective coatings.
In contrast, cerium oxide absorbs UV without being photoactive. Indeed, cerium oxide has a localized electron (4 f orbital) while titanium oxide has less localized electrons than cerium oxide (3 d orbital). So the cerium-oxygen bonding is more ionic than the titanium-oxygen bonding, and logically, the charge carriers (holes and electrons centres) creation is lower than in the case of titanium oxide. Moreover, cerium oxide shows a very fast recombination of charge carriers before they can migrate to the surface (because of crystal defects, oxido-reduction reaction), so, there is no further creation of free radicals. Due to the combination of these two phenomena, cerium oxide does not show any photocatalytic effect.
In other respects, one can see in Figure 2 that cerium oxide presents properties of transparency in the visible spectrum from 400 up to 800 nm higher than those of titanium oxide. This result is in good agreement with the refractive index values of these two materials (2.1-2.2 for cerium oxide and 2.5-2.7 for titanium oxide).
Thus far, one can consider cerium oxide as an excellent candidate for meeting the needs of the protective coating field. However, even if we have now defined a satisfactory chemical composition and size, with proper UV-filtration and transparency but without photocatalytic effect, it is still necessary to reach a good state of compatibility of these nanoparticles within waterborne and solventborne wood stain formulations.
To overcome this issue, Rhodia has developed a set of proprietary treatments that can be used to obtain alkaline aqueous cerium oxide sols (from 100 up to 300 g/l) and totally stable organic sols up to 300 g/l, both perfectly stable on the nano scale and easy to handle and formulate in wood stains.
Both aqueous and solvent-based nanometric cerium oxide systems are especially adapted to wood coating technologies and named RhodigardTM nanotechnology.
Application to Coatings Technologies
Wood is a living material and requires care and protection. In order to meet this requirement, especially in terms of aesthetics and durability, the coatings industry uses high-quality products. Cerium oxide nanoparticles, properly dispersed in coating formulations using the specific chemistry described previously, combine the advantages of organic ultraviolet (UV) absorbers with those of mineral additives. The cerium oxide nanoparticles ensure the durability of the UV absorption function whilst improving the hardness and strengthening the organic binders currently used in wood technology. Since the nanoparticles do not scatter light, the coating remains transparent. The transparency (i.e. no coloration, no whitening) is an important requirement for the wood coating industry; since wood is a natural material, the coating must be as neutral as possible. When the durability is targeted, coloured pigments are often added to help in this way, but this negatively impacts the aesthetics of the end product. Organic UV absorbers are also efficient, but their actions are limited because of progressive destruction of active molecules (migration, leaching, photochemical activity).Experimental
Aqueous and organic wood stain formulations were prepared by simple mixing of standard wood coatings formulations with the solvent- or waterborne (pH >7) nano cerium oxide dispersion. The waterborne system is an acrylic-polyurethane dispersion. The solventborne formulation is an alkyd formulation. Coatings (300 g/m2) were applied by brush on pine panels.Scratch Resistance
The test is carried out with a "sclerometer" (BRAIVE) equipped with a tungsten tip. The applied pressure is adjusted with a calibrated spring. The measurement, (result in grams, a non-SI unit), is the minimal pressure required to scratch the wood coating.Hardness and Abrasion
Hardness testing, performed according to the Persoz method, corresponds to the measurement of the energy absorption by the film when submitted to repeated loadings. The result (expressed in seconds) is the number of oscillations of a pendulum in contact with the tested film when it is inclined 12° at the beginning and 4° at the end of the test. This is a fairly complex experiment involving hardness, friction and mechanical losses. In other words, it characterizes the visco-elasto plasticity behaviour of the film. The higher the result, the better the film properties.
Abrasion resistance is a key property for coatings. One can simulate a very practical situation using a simple testing device, where an abrasive material is moved at a controlled velocity under a constant pressure. The measurement of the surface gloss, before and after the test, is a good indication of the abrasion resistance of the coating.
Tensile Properties
In order to characterize the mechanical properties of the modified coating, a free film is formed through the deposition of a coating layer onto a non-sticky surface (glass). Dog bone specimens are cut and tested on a tensile machine. The yield stress, tensile strength and elongation are recorded at the breaking point.
Results
After drying at room temperature, hybrid systems (organic binder containing mineral particles) are obtained, with homogeneous distribution of cerium oxide nanoparticles throughout the organic binder, as shown by TEM micrographs (Figure 4).
Indeed, each of the "black spots" shown in the micrograph is an elementary nanoparticle of cerium oxide dispersed at nanometric scale in the dry film of the polymer. This excellent dispersion of the nanoparticle in the organic matrix ensures very good UV protection, and improves other properties of the organic coatings under the influence of nano-scale physical effects.
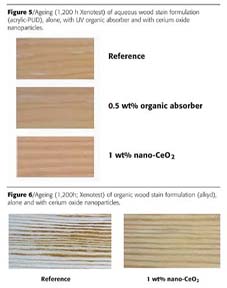
Durability
After 1,200 hours of exposure in a climatic chamber (Xenotest 1200) a 300 g/m2, formulation shows the effects of bleaching, cracks and delamination of the protective film. The addition of an organic UV absorber will delay these effects but does not prevent them. The UV organic absorber can also migrate to the surface, be destroyed by UV radiation and gradually lose efficiency (Figures 5 and 6).
Unlike organic UV absorbers, cerium oxide nanoparticles are perfectly stable under UV radiation and exhibit a permanent protection effect, both in the case of waterborne and solventborne formulations. Moreover, under the same conditions, the addition of 1 wt% of cerium oxide nanoparticles will preserve the physical and mechanical integrity of the film, as illustrated in the following discussion.
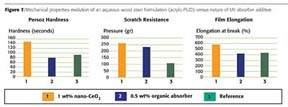
Mechanical Properties and Water Resistance
The results are summarized in Figures 7 and 8, and Table 1. The surface mechanical properties (hardness and scratch resistance) are clearly improved by cerium oxide nanoparticles. The bulk characteristics of the organic host matrix are also strongly modified in the presence of cerium oxide nanoparticles: tensile strength, elongation-at-break or yield stress are significantly improved. The precise mechanisms that lead to the improvement of both the surface and the bulk mechanical properties of the films are, at present, unknown. The homogeneous distribution of cerium oxide nanoparticles throughout the matrix does not support the hypothesis of the formation of an inorganic surface network to explain the reinforcement of the polymer film surface. Therefore, it is probable that a modification of the structural organization of the polymer chains around the particles occurs during the drying.
Finally, the introduction of cerium oxide nanoparticles into the organic matrix results in a significant modification of hydrophilic properties of the coatings, leading to an improvement in water resistance. The contact angle of a water droplet characterizes the water resistance of a surface. This important parameter is significantly increased on addition of cerium oxide nanoparticles (Figure 9). It is interesting to note that the initial improvement in water-repellence properties is further enhanced after ageing under Xenotest conditions.
Water-repellence and water-barrier properties are of primary importance for the durability and the stability of wood constructions. The action of rain and humidity on outdoor constructions is a key factor in the degradation of the coatings because photo-degradation and final failure of the protective coating is the result of the combined action of UV, oxygen and water molecules. Moreover, water penetration in the coating leads to a lack of adherence of the coating onto the wood substrate, causing macroscopic failure. In this respect, a water absorption test on pine panels was performed, comparing a reference to a cerium oxide colloid modified alkyd formulation. The water absorption of the reference is 72 g/m2 and decreased to 45 g/m2 for the cerium oxide containing coating.
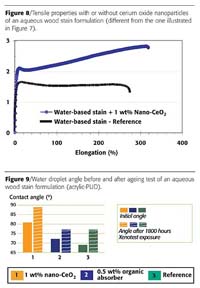
Conclusion
The proper management of nanoparticles synthesis is not only key for the size control and the stability of a mineral colloid, but also to guarantee the compatibility with the organic coatings. A universal UV absorber mineral additive must be compatible and efficient with all kinds of coatings used in industry. When this goal is achieved upstream, one can then benefit from the permanent effects of the main function of the cerium oxide (e.g., UV absorbance) and also from nanoscale physical effects: scratch resistance, strength and hydrophobicity, even at concentration as low as 1 wt%.These results demonstrate how nanotechnologies may contribute to the improvement of our day-to-day life through the enhancement of wood construction durability and consequently lower maintenance, without major changes for the coatings industry.
Acknowledgements
The authors are grateful to O. Sanseau and R. Sellier for technical expertise and TEM observations, to S. Meeker for his help in reviewing the text.
This paper was presented at the Nano and Hybrid Coatings conference sponsored by The Paint Research Association, January 2005, Manchester, UK. Conference proceedings can be obtained by contacting Janet Saraty, Conference Administrator, at j.saraty@pra.org.uk.
For further information, contact Bruno Echalier, + 33 4 72 13 19 68, fax + 33 4 37 91 81 04; or e-mail Bruno.echalier@eu.rhodia.com.
Looking for a reprint of this article?
From high-res PDFs to custom plaques, order your copy today!