A Must to Ensure Consistent Quality
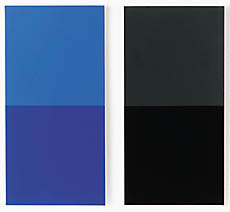
Color and Gloss Influence the Visual Perception
Figure 1 shows a black paint drawdown with the same pigmentation, but different degrees of gloss. It is obvious that the side with the higher degree of gloss is visually perceived as darker and more saturated than the matte side. For this reason it is very important to measure both surface effects separately. Otherwise, the visible difference may be interpreted as a difference in color, although the real reason is a difference in gloss. This could lead to the wrong conclusion, as the remedies are different. The hue is influenced mainly by the type and/or amount of pigmentation, whereas gloss is dependent on the degree of dispersion, the additives used, and the application parameters, for example.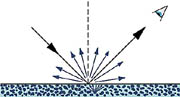
Color and Gloss Measuring Instruments
How can both effects be measured? On the first surface, part of the incident light is directly reflected following the reflection law: angle of incidence = angle of reflection (see Figure 2). The directly reflected light is responsible for the image forming quality of the surface, such as how glossy and brilliant a surface appears. The other part of the light penetrates the coating and is absorbed or diffusely scattered by the pigments within the bulk of the material. This scattered light exits the coating and is uniformly scattered in all directions. The diffused component causes the color impression.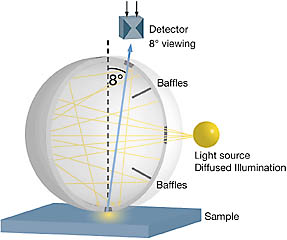
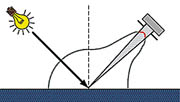
The table shows the color as well as the gloss values of the matte and the glossy side of the black paint drawdown in Figure 1. The values clearly show that there is no difference in the hue. There is only a very slight total color difference of dE* 0.28. The visible difference is solely caused by the difference in gloss: 90.6 gloss units on the glossy side and 2.5 gloss units on the matte side.
To completely describe and analyze visual mismatches, color and gloss need to be objectively measured. Today’s modern technologies allow us to combine both measuring systems in one instrument. The color-guide gloss simultaneously measures color and 60° gloss according to international standards. This cuts the time for measurement and evaluation in half, and optimizes process control.
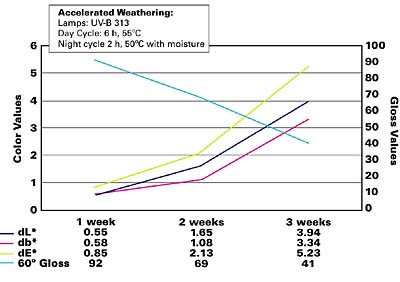
Color and Gloss Measurement for Weathering Studies
The combined color and gloss measurement plays an important role in weathering studies for the development of new paint systems or for the evaluation of raw material replacement in existing formulations. External influences like UV light, temperature and humidity can cause the raw materials to degenerate. This can lead to changes in color, loss of gloss, embrittlement, flaking and chalking. Weathering tests are conducted outside under natural conditions or in the laboratory using accelerated weathering tests. Changes in color and gloss are determined by regularly comparing the weathered samples to the original standard. The total color difference, dE*, is usually evaluated. Acceptable changes depend greatly on the hue. Brilliant colors tolerate greater deviations than dark and achromatic colors. In order to obtain additional information about the yellowing of the hue, often the db* is documented. The b* value represents the yellow/blue amount — the greater the deviation on the b* value, the more the paint yellowed. In case of light colors, the dirt pick-up is also rated. For this purpose, the change in lightness (L* value) is recorded. Figure 5 shows the results of an extreme accelerated weathering test with an alkyd resin. It is obvious that the 60° gloss value rapidly decreases and the color deviations dE*, dL*, and db* greatly increase.

Measurement of Color and Gloss to Analyze and Optimize the Process
Besides raw materials, process parameters in the paint production influence the appearance of the end product. Color, for example, greatly depends on the film thickness. Most of the products are pretreated and get darker thereafter. If the film thickness is too low the substrate will shine through and influence the color. Furthermore, heat-curing systems, such as acrylic, polyester, epoxy or alkyd-resins, are greatly influenced by the baking process. A chemical reaction between the raw materials occurs. Only the appropriate curing process can guarantee an optimally crosslinked paint system with the desired properties. If the temperatures are too high, there will be a yellowing or a change in the hue, because the pigments are only stable up to a certain temperature.The degree of gloss is greatly influenced by the crosslinking: not enough, optimally or too much. Overcuring will reduce gloss and the surface will appear matte. Figure 6 shows such an example. An industrial paint system was cured at 150°C. The visual comparison to the standard shows a reduced brightness and brilliance — seemingly a color deviation. However, a more detailed analysis with the combined color and gloss measurement showed the following result. The color deviation of dE* = 0.5 measured with a sphere instrument is extremely small and lies within the acceptable tolerance. Visually the sample looks “lighter” caused by the reduced gloss value. That means that the color is off specification, but the gloss changed, which could be adjusted by reducing the oven temperature.
The color-guide gloss can help to determine the cause of a mismatch, optimize the painting process and analyze deviations at the site.
For more information on color-measuring devices, contact BYK-Gardner USA, 9104 Guilford Road, Columbia, MD 21046; phone 800/343.7721; fax 800/394.8215; visit www.byk gardner.com; e-mail custserv@bykgardnerusa.com.
Looking for a reprint of this article?
From high-res PDFs to custom plaques, order your copy today!