Nanotechnology for Waterborne Paint Improvement
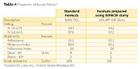

What Is BIPHOR?
Biphor is a new family of aluminum phosphates or polyphosphates made by a patented wet chemistry process.8 It is a "green chemistry," zero-effluent product made under mild temperature and pressure conditions that do not create any environmental problems during the fabrication process.Due to its chemical nature, BIPHOR residues in the paint industry or in the final user location may be safely discarded in the environment as a fertilizer component. It is produced as slurry as well as a dry powder. In both cases it is easily dispersed in water, forming stable dispersions that have stable rheological properties.
BIPHOR is completely different from existing aluminum phosphates or polyphosphates in many aspects.
- It does not have a definite stoichiometry, thus it is better thought of as a crosslinked ionic polymer than as a salt.
- Since the stoichiometry is not definite, various grades of BIPHOR can be prepared by changing the fabrication process, and thus the final product composition.
- BIPHOR is made under very rigid pH control, and it is nearly neutral, thus avoiding environmental and toxicological problems.
- It is also exempt from corrosion problems associated with some aluminum phosphates found in the marketplace and used in the transformation of iron oxides into iron phosphate in metal-protecting paints.
- The non-stoichiometry, together with the non-crystallinity of BIPHOR (both slurry and powder) and the carefully controlled water content of dry BIPHOR powder, allow for easy swelling control that is essential for its performance, following the mechanism that will be described.
- The nano-sized particles are easily dispersed and are stable towards settling, which is very important for making uniform paint dispersions with BIPHOR.
- BIPHOR nanoparticles are strongly compatible with latex particles, by the mechanisms of capillary adhesion (in the dispersion drying stage) followed by ion-cluster mediated electrostatic adhesion (in the dry film). This compatibility is so high that bicontinuous networks are formed in many cases.
- BIPHOR is also strongly compatible with many other particulate solids commonly used as paint fillers, such as the various silicates, carbonates and oxides found in formulated waterborne dispersions. This contributes to the cohesion and strength of the dry paint film.
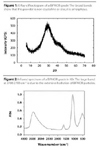

How BIPHOR Works
To understand how BIPHOR performs within a drying paint film, it is interesting to compare it to the current industry-standard white pigment, titanium dioxide. A basic TiO2 waterborne paint is made out of a suitable latex dispersion and pigment particles. The latex particles are responsible for making a coalesced film filled with the pigmented particles, which are responsible for the film hiding power. Many additives are also used: inorganic fillers, which decrease the requirements of resin and pigment; coalescing agents that improve resin film formation; and dispersants and rheological modifiers that prevent pigment and filler caking, thus improving the paint shelf-life together with the rheological paint properties.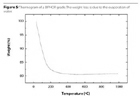
A typical dry film of a paint formulated with BIPHOR is represented in Figure 7. There are many large differences compared to the previous case.


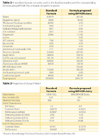
Application Tests
In these tests, a standard market formulation of a semi-matte acrylic paint was chosen, and TiO2 was progressively replaced with BIPHOR. Water content and other paint components were adjusted as required. The majority of the modifications in the formula are related to a decreased use of thickener/rheology modifier, dispersant, acrylic resin and coalescing agent.Table 2 describes an example of one of the standard formulas used in this work, together with the corresponding BIPHOR formula. The standard formula in Table 2 is currently being used by one of the market leaders in the Brazilian architectural paint market.
In the formula in Table 2, a replacement of 50% TiO2 (on a weight basis) was made, obviously keeping the opacity and whiteness conditions of the dry film. In addition, the other properties of BIPHOR as a rheological modifier and also as a film-structuring agent were explored.
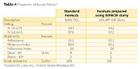
Several field test applications were also made, and an example is shown in Figure 9. Some of these application tests have been monitored for quite some time now and they are revealing great color stability and resistance to chalking. This can be attributed to the complete photochemical inertness of BIPHOR (as compared to TiO2), bringing in a bonus for those paints formulated with BIPHOR.

Conclusion
BIPHOR is now completing the development stage with outstanding results. The introduction of BIPHOR in waterborne paints leads to improved visual performance and durability at a reduced cost. cAcknowledgments
FG acknowledges PADCT/CNPq for supporting the Instituto do Milênio de Materiais Complexos (Millenium Institute for Complex Materials).References
- Beppu, M.M; Lima, E.C.D.; Sassaki, R.M.; Galembeck, F. Self-opacifying aluminum phosphate particles for paint film pigmentation.; J. Ctgs. Technol. 1997, 69 (867): 81-88.
- Lima, E.C.D.; Beppu, M.M.; Galembeck, F.; Valente, J.F.; Soares, D.M. Non-crystalline aluminum polyphosphates: Preparation and properties. J. Brazilian Chem. Soc. 1996, 7 (3): 209-215.
- Beppu, M.M.; Lima, E.C.D.; Galembeck, F. Aluminum phosphate particles containing closed pores. Preparation, characterization, and use as a white pigment. J. Colloid Interface Sci. 1996, 178 (1): 93-103.
- Monteiro, V.A.D.; de Souza, E.F. ; de Azevedo, M.M.M.; Galembeck, F. Aluminum polyphosphate nanoparticles: Preparation, particle size determination and microchemistry. J. Colloid Interface Sci. 1999, 217 (2): 237-248.
- de Souza, E.F.; da Silva, M.D.C.V.M.; Galembeck, F. Improved latex film-glass adhesion under wet environments by using an aluminum polyphosphate filler. J. Adhes. Sci. Technol. 1999. 13 (3): 357-378.
- de Souza, E.F.; Bezerra, C.C.; Galembeck, F. Bicontinuous networks made of polyphosphates and of thermoplastic polymers. Polymer 1997, 38 (26): 6285-6293.
- Lima, E.C.D.; Beppu, M.M.; Galembeck, F. Nanosized particles of aluminum polyphosphate. Langmuir 1996, 12 (7): 1701-1703.
- Galembeck, F. "Produto e processo de fabricação de um pigmento branco baseado na síntese de partículas ocas de ortofosfato ou polifosfato de alumínio", Brasil, PI0403713-8, 2004.
- Giannelis, E.P. Polymer layered nanocomposites. Adv. Mater. 1996, 8 (1): 29-35.
Looking for a reprint of this article?
From high-res PDFs to custom plaques, order your copy today!