The Way We Color Our World

Is it film or is it paint? This is the question increasingly being asked in automotive, heavy truck, marine and other markets. Every major automotive OEM has major initiatives to identify, develop and use alternatives to paint. This is all good news for Soliant LLC, a global leader in exterior durable films. Soliant estimates that over 40 million exterior automotive components have been surfaced with dry paint film in the past five years, and expects to see explosive growth in the next three to five years. Applications will range from small trim components to fascias to roofing modules or body panels.
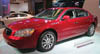
A Change of Perspective - Paint Film Use Grows
Paint Film HistoryPaint films appeared in the market for the first time in a significant way in the late 1980s. These films were laminated to aluminum and stainless steel coil and then roll formed or stamped. The films proved to be very durable, and have shown excellent durability in exterior environments. The use of films began to move toward plastic in the late 1990s as more metal parts were converted to plastic.
Automotive OEMs Push for Films
The Japanese OEMs were the first to implement films in a large way on plastic beginning in the late '90s. The growth of the product was limited initially by the lack of infrastructure for using the film in part-manufacturing operations. Initially, there were only a small number of companies who possessed the thermoforming or other processing know-how to use films effectively. However, as the major OEMs placed a higher emphasis on paint alternatives, the infrastructure began to develop and has grown substantially over the past 24 months. As this infrastructure came on line, the use of film and number of applications exploded.
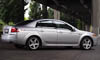
The film products offered today are changing the way we think about decorative finishes, and not just from the automotive industry. Films are being incorporated into recreation vehicles such as personal watercraft or ATVs. Mobile phones and other handheld consumer electronics also are using films. The film technology offers the various industries flexibility, efficiency and economy. In addition, the environment benefits substantially because of reduced volatile organic compounds, reduced energy consumption and increased use of recycling when compared to traditional paint methods.
The positive environmental impact of paint film versus paint has been well documented. Independent studies show that paint film is 10 times more effective in reducing VOC emissions compared to a state-of-the-art paint system. The Soliant coating lines are designed for 100% capture of ALL fumes, and are far more effective and efficient than a paint system. As environmental regulations become more stringent, the advantages that films offer will continue to grow. Each of the major automotive OEMs is pushing their supply base to eliminate/reduce VOCs from their processes. Automotive OEMs already using the film technology includes Acura, Audi, Chrysler, Ford, GM, Honda, Mercedes, Saab, Toyota and Volvo.
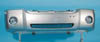
Film Manufacturing
Film manufacture has some similarities with paint manufacture but has some important differences. The manufacturing process begins much the same way as paint; formulating the clear and color compounds. The color compounds used for film manufacture use the same pigments, metal flakes, etc., as paint. However, this is where the similarities end.First, films are created as a two-dimensional product, which means that the chemistries used for film manufacture must have a thermoplastic nature until the film is formed into the three-dimensional shape during application. This explains why you can't simply use current paint chemistries to make a film.
Second, films are typically created in reverse of paint constructions. In a painting operation, a primer is typically applied first, followed by the color coat and clear coat. These may be applied wet-on-wet or in separate passes. Films start with the clear being cast on a PET carrier. The PET is heat stabilized so that it can convey the coating into an oven and dried. One advantage of this type of process is that the thickness of the coating can be very precisely controlled AND the coating mix can have a substantially higher solids level than paint. High solids reduce the VOC content from the outset and the confined space of a film dryer allows for more efficient capture of airborne VOCs. Just as in the case of painting, the clear and color layers can be coated wet-on-wet or in separate passes. After the clear and color coating, the appropriate adhesive or "primer" is applied to the back of the color coat. This structure can then be laminated to a variety of substrates including TPO, ABS, PC, PC/ABS, etc.
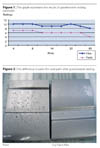
Film Advantages
Cost - Several studies have highlighted the actual cost savings associated with the use of film when looking at the system cost to produce decorated parts. These studies show that film can have savings of 15-35% depending on the part design. These savings come from improved yields, reduced energy consumption, reduced inventory and increased flexibility.
Performance - Films have been used since the late 1980s in a variety of exterior applications. These provide a reliable database of experience and performance in very challenging environments. Even after 15-20 years of use, the product still looks good and, in many cases, better than the paint surrounding it.
The thermoplastic nature of paint films and the adhesive or primer used turns out to offer big advantages; primarily it provides a very strong bond to the substrate being used. For example, film has improved chip resistance because of the tie layer and the fact that the film is thermoplastic.
The graph in Figure 1 shows the results of gravelometer testing. The scale is 0 to 10, with 10 being the best. As shown, the paint film consistently outperformed paint in gravelometer testing and it does not flake as paint does, which is why OEMs have replaced paint with paint film on cladding, rocker panels, etc. The number of pints in the Figure refers to the number of pints of gravel thrown at a painted sample; the graph shows that even under tremendous impact the paint film is more resistant. The gravelometer test used was GM9508P; Figure 2 shows the samples after testing.
Environment - The precise nature of the coating, the high solids composition and the dryer efficiency lead to dramatic VOC reductions in film manufacture versus painting. Film manufacture uses technology that has been developed for precision coatings in a variety of industries. The thickness can be very precisely controlled. The color solution (and clear for that matter) can be coated at very high viscosities and solids. This reduces the amount of solvents needed and, as a direct result, the amount of VOCs that are generated in the process. Further, no aerosol has to be generated to apply the paint. The color solution is "extruded" onto the carrier and conveyed into the drying ovens.
Just to provide a frame of reference, let's look at what these advantages mean to the environment. According to Gordon C. Miller, MSPH, C.I.H., C.H.M.M, Q.E.P., who presented a study on "Environmental Sustainability & Recycling in Action" at this year's annual GPEC (SPE's Global Plastics Environmental Conference) in Atlanta, "With the film process, the VOC emissions to the environment are reduced by 90-98%!" Just as a frame of reference, this would mean that if film were used on just five million cars per year, the VOC reduction would be the equivalent of eliminating the current emissions of Charlotte, Atlanta and several other similar-sized cities.
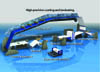
The energy savings also are significant. Some studies have suggested that the use of film can save the equivalent of several million gallons of gasoline annually. These savings are becoming more significant as we see escalating costs of natural gas and electricity.
Recycle - Film provides the ability to recycle the entire product back into the system. Since the film is thermoplastic in nature, the film can be recycled with extruded sheet or injection molding resins without harm. Soliant's films are designed for use with less expensive olefin resins that are recyclable. Again, the ability to recycle contributes to the cost savings from film use.
Current Applications
Current automotive market applications include rocker panels, body side moldings, fascias, roofstrips, grilles, pillars, IP trims rings and various bezels. Soliant typically supplies the entire color palettes including tint coats, pearlescents and metallics. These color matches have the same criteria as paint.Many of the current applications were developed to take advantage of the performance advantages of films, particularly resistance to chipping on impact, as highlighted earlier. Honda and Toyota were the first to recognize the potential benefits of film on TPO rocker panels, with parts being in production since 1998. GM has also incorporated film into several rocker panel and stone shield designs to improve performance or avoid costly urethane paint protection films.
Paint films manufactured by Soliant can be easily integrated in customers' manufacturing processes such as injection and compression molding, thermoforming and extrusion. This integration makes it possible to use the same paint film on multiple applications on a single vehicle. Doing this improves the economic benefit of film and ensures color consistency on the range of parts used. For example, Toyota uses paint film on three different parts on the current Avalon. Film is used to manufacture both the rocker panel and body side moldings using an insert/injection molding process. The roofstrip also incorporates paintfilm in the extrusion of an olefin-based substrate. Three different parts, one film.
As paint film has become more cost effective over time, it has increasingly competed against paint in larger and more price-sensitive applications such as fascia and other body panels. Another major advantage is the avoidance of the large capital outlay for automotive paint facilities and their rising costs of operation, particularly due to ever-tighter environmental regulations and increasing energy costs.
The Next Generation
Soliant is now introducing the next generation of paint film to the industry that offers improved scratch and mar properties as well as improved gloss and distinctness of image of the finish. The products further reduce the system manufacturing cost and are also being improved to widen the processing window. These combined improvements are expected to open the door for larger applications in fascias and body panels.Films are also being developed to serve as the decorative "skins" for large composite body panels like roof modules, fenders, lift gates, etc. These skins can be used with a variety of glass-reinforced composites that offer the strength and stiffness of steel, but the weight and energy transparency of plastics. For example, using composites in roof modules saves weight and allows the manufacturer to incorporate satellite radio and GPS antennae into the module itself, without having external systems. And the film "skins" solve the traditional issues of painting a glass-filled material.
The painting of structural composites, particularly those incorporating glass fibers, presents several challenges. The use of film eliminates the issues with painting glass-filled materials and provides a way to provide body color on the part.
Some production with these systems is already happening in Europe, and is expected to expand quickly as the technology is further validated.
So the next time you are looking at a vehicle, boat or shaver, see if you can tell the difference. You might like what you see.
Looking for a reprint of this article?
From high-res PDFs to custom plaques, order your copy today!