The Right Choice
It is the customers’ expectations in the end product that set the standards for the coating producers. But to produce high-end products, high-value pigments are needed, and they come at a price.
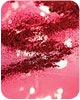
Coatings are mixtures of components with highly diverse properties. In addition to solid particles, the coatings in different solvents contain dissolved or dispersed polymers, polyelectrolytes and surface-active substances in varying quantities. Coatings are highly sophisticated colloidal systems whose complex interactions determine the properties of the coating in its liquid state and in its finished state after application. The requirements for coatings are increasing. It is the customers’ expectations in the end product that set the standards for the coating producers. But to produce high-end products, high-value pigments are needed, and they come at a price. Eventually, the choice of pigments is based on what provides the best possible combination of coloristics, quality and economics. A systematic approach can make it easier to identify the optimal solution from among the numerous raw materials available in the market. This article describes the most important aspects that should be considered in this evaluation process.
The process of coating manufacturing offers several possibilities for optimization. However, it is important to bear in mind that all process steps are interactional, and therefore cannot be viewed isolated from each other. The pigments and their properties are especially important because they directly influence the quality of the formulation and the cost of the coating.
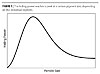
The decisive physical parameter is the particle size, which has two effects. It influences the hiding power of organic pigments, which reaches a peak at a certain particle size, depending on the individual pigment (Figure 1); and, with an increase in the particle size, the color strength diminishes (Figure 2).
These two parameters should be used to determine the proper particle size at which both sufficient hiding power and good color strength are guaranteed. On this basis, the minimum coating thickness is calculated, as shown in Figure 3. In order to minimize the required pigment amount, a common practice is to select a pigment particle size that ensures the highest color strength. To optimize the hiding power, a compromise must be found that provides good hiding power and color strength. Generally, the optimum is reached with a slightly smaller particle size than the particle size that would be necessary to achieve optimum hiding power. With detailed knowledge of these pigment parameters, it is possible to optimize cost in two ways: by lowering the film thickness, as coating costs are proportionate to the thickness of the applied coating, and by reducing the pigment content.
Subsequent to synthesis and precipitation, pigments often undergo a physical post-treatment to tailor their properties. This is referred to as “finish”. It can consist of a thermal treatment, or the use of solvents and/or additives. The finish changes pigment characteristics such as crystalline phase, particle size, distribution of particle size and particle shape, and directly influences the application properties of the pigments. Table 1 provides an overview of the possible variants.
For instance, a pigment finish leading to a significant enlargement of the particles with a narrower distribution of the particle size improves the rheological properties of the pigments in the mill base. This, in turn, allows increasing the filling grade in the coating system, which will further optimize its hiding power.
Pigments with optimized opacity have been designed for high-end coatings, such as opaque plain colors for industrial and automotive coatings. They have proven themselves as a good choice to substitute for pigments containing heavy metals.
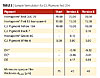
In order to reach the required hiding power with organic pigments, a common practice is to add carbon black as a supplementary pigment. However, it makes the shades duller and darker. Another possible solution is the addition of complementary pigments. Using organic pigments results in a slight shift in the shade but the final result is still significantly purer than when using carbon black. Complementary pigments with optimized hiding power are ideal. Only a small amount is required to produce the desired results.
Table 2 shows how complementary pigments modify the hiding power of C.I. Pigment Red 254. In Version A of the above example, Hostaperm® Green 8G was used to increase the hiding power. In Version B carbon black was used. The direct comparison of the two results shows that the green pigment, when used in the same amount and the same thickness as the carbon black, produces a much purer shade. Thus optimizing the hiding power makes it possible to minimize the thickness of the coating, or to apply the coating with the same thickness but with a reduced pigmentation.
The method of using complementary pigments, as well as pigments with optimized hiding power, is mainly used to optimize opaque plain colors for automotive and industrial coatings, and to substitute pigments containing heavy metals.
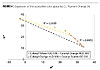
It is generally assumed that in the CIELAB color space, the pigment mixture is located in-between the shades of the pigments contained in the mixture. This assumption is not fully correct, since the differences are increasing with the distance between the pigments in the color space. For the evaluation, a* and b* according to the CIELAB system are represented in a XY graph. Based on these data, the maximum color space is calculated, and the space separating the pigments is indicated. In terms of coloristics, the pigments in the inner area are theoretically dispensable because they do not contribute to the maximum color space. However, it should be kept in mind that black pigments and inorganic pigments such as iron oxides would be necessary for cost optimization.
However, it has to be noted that the data do not allow drawing any conclusions about full shades. It is also not possible to make a statement about the metamerism of possible new mixtures, and how they compare to existing formulations. Another element that has also been disregarded is price and other product properties, such as weatherfastness. These aspects could be taken into consideration when the database used for the calculation is set up.
Figure 4 illustrates how C.I. Pigment Orange 36 can enlarge the available color space in a system where highly fast organic pigments provide the desired level of fastness. The black line represents mixtures of C.I. Pigment Yellow 184 and C.I. Pigment Red 168. Analyzing the available color space makes it possible to pre-select the pigments and avoids the use of unnecessary pigments, thus reducing complexity. By the same token, optimizing the existing system while maintaining or increasing the number of pigments may also open a new color space. It could be used for additional shades, a decision that especially pays off in lucrative color spaces. Also, the optimization of a color system requires less product tailoring. Therefore the main field of application for color space analysis is the optimization of tinting systems in which the number of products used is crucial, for example POS tinting systems.
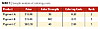
The direct comparison of coloring costs, as shown in Table 3, confirms this assumption. Initially, Pigment A seems to be more economic than Pigment B. Yet, due to its lower color strength, Pigment A generates significantly higher coloring costs for the pigment processor despite its lower price. For this reason, Pigment B is economically more efficient. Pigment C shows by far the worst results in this comparison. However, this pigment might offer other benefits, such as high weatherfastness. Hence in applications where a special property is required, higher coloring costs might be justified.
Keeping in mind that a coating contains several other ingredients in addition to pigments, the decisive factor is the cost of the total formulation (which, in most cases, is the final product), and not only the cost of an individual raw material. In addition to the coloring costs of an individual pigment, the cost of optimizing the total formulation using pigments, binders and additives should be taken into consideration as required. For instance, it should also be checked whether a cheaper pigment generates additional costs because additional additives and/or binders might be required.
The goal of the sample formulation in Table 4 is to determine the formulation costs of a yellow-shade coating in the yellow color range. The requirement for the thickness of a covering layer was 90 µm. The percentage of C.I. Pigment Yellow 184 was increased to enhance the hiding power. While this does not change the cost of the total formulation, it produces a better cost per surface ratio [$/m²]. Of course this is only useful if the price paid by the final customer is based on the coated surface.
Another point to consider is that flawed products, delivery problems and lack of quality consistency create additional work and cost. All of these weaknesses lead to hassles in the production process, and they also affect the quality consistency that the pigment processor is able to achieve. All of that generates additional cost for the pigment user. Pre-testing can be done with dispersing studies in order to rule out possible differences that might appear in the production process. Because the evaluation process described in this article disregards fastness differences, a proper preselection of pigments should be done in advance. A proper way of evaluation is to define clear limits for the technical suitability. Only suitable pigments should be taken into consideration. This makes it easier to decide between different Colour Indices that all feature a sufficient level of fastness. Also, comparing products of the same Colour Index makes it easier to select the best suitable pigment variant where more than one is commercially available (for example C.I. Pigment Yellow 74, which is available as opaque and transparent).
Of course, for a proper comparison of alternative products of the same pigment quality but from competing suppliers, additional key factors must be taken into consideration, such as the consistency in delivery and quality (influence on production costs), product package agreements (influence on yearly costs), total number of products (complexity), etc.
For more information, visit www.clariant.com.
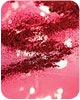
Coatings are mixtures of components with highly diverse properties. In addition to solid particles, the coatings in different solvents contain dissolved or dispersed polymers, polyelectrolytes and surface-active substances in varying quantities. Coatings are highly sophisticated colloidal systems whose complex interactions determine the properties of the coating in its liquid state and in its finished state after application. The requirements for coatings are increasing. It is the customers’ expectations in the end product that set the standards for the coating producers. But to produce high-end products, high-value pigments are needed, and they come at a price. Eventually, the choice of pigments is based on what provides the best possible combination of coloristics, quality and economics. A systematic approach can make it easier to identify the optimal solution from among the numerous raw materials available in the market. This article describes the most important aspects that should be considered in this evaluation process.
The process of coating manufacturing offers several possibilities for optimization. However, it is important to bear in mind that all process steps are interactional, and therefore cannot be viewed isolated from each other. The pigments and their properties are especially important because they directly influence the quality of the formulation and the cost of the coating.
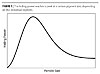
Color Strength, Coloristic Behavior and Hiding Power
Coating thickness is primarily determined by the hiding power of each individual pigment in the coating, as well as by its interactions. Film thickness should be as thin as possible in order to save costs. The lowest achievable film thickness depends mainly on opacity, but also on other properties, such as leveling.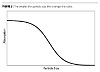
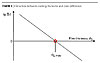
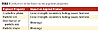
For instance, a pigment finish leading to a significant enlargement of the particles with a narrower distribution of the particle size improves the rheological properties of the pigments in the mill base. This, in turn, allows increasing the filling grade in the coating system, which will further optimize its hiding power.
Pigments with optimized opacity have been designed for high-end coatings, such as opaque plain colors for industrial and automotive coatings. They have proven themselves as a good choice to substitute for pigments containing heavy metals.
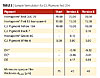
Colored Pigments and Their Hiding Power
For physical reasons, organic yellow, orange and red pigments naturally have a low level of light absorption. Unlike blue or green shades, the light absorption in these lighter organic pigments is low, especially in the long-wave range of the visible light spectrum. Inorganic pigments are different. They stand out by good hiding power, as their refractive index is lower than the index of organic pigments. For this reason, the difference between the refractive index of inorganic pigments and binders is bigger than the difference in the refractive index between organic pigments and binders. Also, the hiding power increases accordingly. However, inorganic pigments characteristically have a duller shade than organic pigments.In order to reach the required hiding power with organic pigments, a common practice is to add carbon black as a supplementary pigment. However, it makes the shades duller and darker. Another possible solution is the addition of complementary pigments. Using organic pigments results in a slight shift in the shade but the final result is still significantly purer than when using carbon black. Complementary pigments with optimized hiding power are ideal. Only a small amount is required to produce the desired results.
Table 2 shows how complementary pigments modify the hiding power of C.I. Pigment Red 254. In Version A of the above example, Hostaperm® Green 8G was used to increase the hiding power. In Version B carbon black was used. The direct comparison of the two results shows that the green pigment, when used in the same amount and the same thickness as the carbon black, produces a much purer shade. Thus optimizing the hiding power makes it possible to minimize the thickness of the coating, or to apply the coating with the same thickness but with a reduced pigmentation.
The method of using complementary pigments, as well as pigments with optimized hiding power, is mainly used to optimize opaque plain colors for automotive and industrial coatings, and to substitute pigments containing heavy metals.
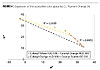
Maximizing Color Space
To identify the color space, which is accessible through pigments and pigments mixtures, a set of standard conditions was established. All pigment preparations were adjusted to a color depth of 1/25, which creates the visual impression that the pigment concentration is the same in all color variations and allows comparing the different pigments and their colors. This particular color depth is typical for architectural paints and represents a compromise between brighter variations, which are difficult to produce in a laboratory, and deeper shades, which are more difficult to compare. An opaque white dispersion was used to avoid systematic errors.It is generally assumed that in the CIELAB color space, the pigment mixture is located in-between the shades of the pigments contained in the mixture. This assumption is not fully correct, since the differences are increasing with the distance between the pigments in the color space. For the evaluation, a* and b* according to the CIELAB system are represented in a XY graph. Based on these data, the maximum color space is calculated, and the space separating the pigments is indicated. In terms of coloristics, the pigments in the inner area are theoretically dispensable because they do not contribute to the maximum color space. However, it should be kept in mind that black pigments and inorganic pigments such as iron oxides would be necessary for cost optimization.
However, it has to be noted that the data do not allow drawing any conclusions about full shades. It is also not possible to make a statement about the metamerism of possible new mixtures, and how they compare to existing formulations. Another element that has also been disregarded is price and other product properties, such as weatherfastness. These aspects could be taken into consideration when the database used for the calculation is set up.
Figure 4 illustrates how C.I. Pigment Orange 36 can enlarge the available color space in a system where highly fast organic pigments provide the desired level of fastness. The black line represents mixtures of C.I. Pigment Yellow 184 and C.I. Pigment Red 168. Analyzing the available color space makes it possible to pre-select the pigments and avoids the use of unnecessary pigments, thus reducing complexity. By the same token, optimizing the existing system while maintaining or increasing the number of pigments may also open a new color space. It could be used for additional shades, a decision that especially pays off in lucrative color spaces. Also, the optimization of a color system requires less product tailoring. Therefore the main field of application for color space analysis is the optimization of tinting systems in which the number of products used is crucial, for example POS tinting systems.
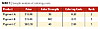
Cost Analysis
The commonly used parameters to determine efficient pigmentation are the price per kilogram of pigment and the color strength – which amount of the pigment is needed for each gram of white pigment. This differentiation is quite common in the industry. This is often supported by an organizational differentiation between commercial and technical departments. However, it makes more sense to calculate what it would cost to reach a certain standard color depth. The coloring cost, which combines both commercial and technical properties, is defined as the ratio between price and color strength.The direct comparison of coloring costs, as shown in Table 3, confirms this assumption. Initially, Pigment A seems to be more economic than Pigment B. Yet, due to its lower color strength, Pigment A generates significantly higher coloring costs for the pigment processor despite its lower price. For this reason, Pigment B is economically more efficient. Pigment C shows by far the worst results in this comparison. However, this pigment might offer other benefits, such as high weatherfastness. Hence in applications where a special property is required, higher coloring costs might be justified.
Keeping in mind that a coating contains several other ingredients in addition to pigments, the decisive factor is the cost of the total formulation (which, in most cases, is the final product), and not only the cost of an individual raw material. In addition to the coloring costs of an individual pigment, the cost of optimizing the total formulation using pigments, binders and additives should be taken into consideration as required. For instance, it should also be checked whether a cheaper pigment generates additional costs because additional additives and/or binders might be required.
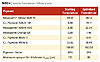
Another point to consider is that flawed products, delivery problems and lack of quality consistency create additional work and cost. All of these weaknesses lead to hassles in the production process, and they also affect the quality consistency that the pigment processor is able to achieve. All of that generates additional cost for the pigment user. Pre-testing can be done with dispersing studies in order to rule out possible differences that might appear in the production process. Because the evaluation process described in this article disregards fastness differences, a proper preselection of pigments should be done in advance. A proper way of evaluation is to define clear limits for the technical suitability. Only suitable pigments should be taken into consideration. This makes it easier to decide between different Colour Indices that all feature a sufficient level of fastness. Also, comparing products of the same Colour Index makes it easier to select the best suitable pigment variant where more than one is commercially available (for example C.I. Pigment Yellow 74, which is available as opaque and transparent).
Of course, for a proper comparison of alternative products of the same pigment quality but from competing suppliers, additional key factors must be taken into consideration, such as the consistency in delivery and quality (influence on production costs), product package agreements (influence on yearly costs), total number of products (complexity), etc.
Conclusion
The systematic approach described in this article allows the identification of the best suitable products, which are specific for each customer, in a relatively easy manner. Using pigments with optimized hiding power can reduce the required coating thickness. Adding complementary pigments can also enhance the hiding power. In this field, C.I. Pigment Green 36 has established itself as an almost universally applicable solution. Determining how the maximum color space can be obtained with a minimal range of pigments reduces complexity. Optimizing formulation efficiency, while taking into consideration the total cost, avoids superficial savings that in the end might create additional costs somewhere else in the process.For more information, visit www.clariant.com.
Looking for a reprint of this article?
From high-res PDFs to custom plaques, order your copy today!