Efficient Grinding and Classifying of Powder Coatings
Introduction
The quality of powder coatings is influenced by many factors. One of the most important is particle size distribution. High product quality requires a narrow particle size distribution with a sharp and well-defined top cut and a low amount of fine particles. The produced particle size distribution is influenced by the material properties of the powder coatings and by the process technology of the powder coatings grinding system.
The width of the particle size distribution also depends on the design and the efficiency of the grinding system. Important factors include the dimensions of the mill, to avoid overmilling; the type of grinding elements, to achieve a high grinding intensity; optimized airflow conditions; and a highly efficient classification. Following is a description of the powder coatings production process and the most important influences on that process.
Powder grinding system
The described grinding system is made by Neuman & Esser GmbH, Grinding and Classifying Systems (Übach-Palenberg, Germany)1. The main process steps of the system are feeding, grinding of the powder coating chips inside the impact classifier mill, or ICM, and separation of the powder coatings from the airflow.The feeding of chips out of a vessel is done by a dosing rotary airlock. The chips are transported by airflow into the ICM, where the grinding and classification process takes place. The ICM grinds the powder with hammers that have a tip speed of up to 130 m/s. The solids are comminuted in the milling chamber at the exterior circumference of the grinding disc and the profiled grinding surface of the internal wall of the housing.
An internal circuit transports the ground particles to an impeller wheel classifier, which is integrated in the housing of the ICM. The classifier allows particles with the desired size to pass. Coarse particles are rejected and transported again into the grinding zone. The main task of this classifier is to determine the top size of the product. A high cut sharpness of the integrated air classifier guarantees a well-defined top size free of spattered particles. Furthermore, the internal classification achieves a short residence time inside the mill and avoids overmilling of the product. Final product with the desired particle size will not be transported into the grinding zone again, thus producing a narrow particle size distribution.
Depending on the plant's concept, the product that leaves the classifier mill is either separated from the transportation airflow by means of a cyclone or, if a reduction of fine particles is required, an additional classification process step is installed. This is realized by a cyclone classifier, which produces good flow properties in the product.
A residual dust collector (RDC) separates the very fine particles from the airflow after the cyclone, where particle size is in the range of a few microns. A fan produces the airflow for the transportation of the solids through the system.

Particle size distributions
Different particle size distributions produced by an ICM are shown in Figure 1. Frequent values of the top size are from more than 100 µm to less than 40 µm and of the x50-value between 50 µm and 30 µm. To produce a product with a low x50-value, the grinding elements need to have a high intensity with a high tip speed. This will shift the particle size distribution to the fine side and increase the amount of fine particles.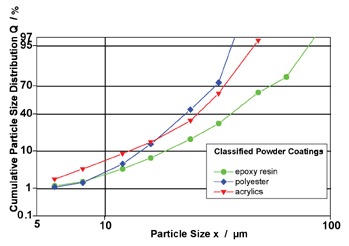
The material properties depend on the powder coating components that are used and the extrusion process, which fixes the brittleness or ductility of the material. Brittleness or ductility is described by the physical parameter, called elastic modulus. A brittle material is characterized by a low elastic modulus. It increases with increasing ductility.
New applications in the automotive industry require a low top size and a very small amount of fine particles. In some cases, the amount of particles below 10µm is even less than 3%, or about 1.5% below 8 µm.
To avoid a decrease in product quality, the high amount of fine material has to be reduced. This requires a classification process behind the impact classifier mill. It is done by an additional classification using a cyclone classifier. In the case of grinding system retrofits, a change from a separation process to a classification process can be done by the exchange of the vortex finder of the cyclone and the installation of a classifier rotor and a secondary air inlet at the bottom of the cyclone housing. Due to the design of the classifier housing, an easy cleaning is guaranteed. Some examples of classified particle size distributions produced by a cyclone classifier are shown in Figure 2.
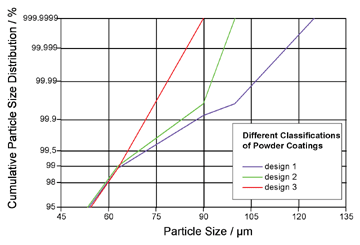
A highly efficient classification process avoids deflected particles or particles that are too coarse, which will have a negative influence on the quality of the powder coated surface. Figure 3 shows the results of classifications with different geometrical situations inside an impact classifier mill. In this case, differences in the top size of the particle size distribution is about 35 µm, although the x50-value has the same particle size.
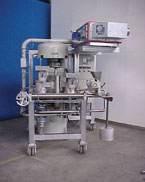
Grinding systems for small batches
Grinding systems for powder coatings often have throughputs in the range of several hundred kilograms per hour to more than 1 metric ton per hour. Thus the production of comparable particle size distributions is difficult. Reproducibility of particle size distributions produced by the laboratory is difficult to achieve in production. Therefore, a new, small laboratory grinding system and the compact grinding systems ICM 3.8 and ICM 4.8 have been developed2.These grinding systems allow for fast production of small product quantities, which are necessary for the easy development of new powder coatings or the production of specimen samples for customers. Table 1 lists standard values for charge quantities and throughput for these ICM Systems.
Both compact systems are a link between the laboratory mill in the research laboratory and the production plant. It is a complete process unit that consists of an aggregate for the air-cooling, a pneumatic dosing device by means of rotary airlock, the classifier mill ICM 4.8, the downstream cyclone CAR 6 and a filter for the fine dust separation. The installation of an air classifier instead of a cyclone leads to a lower amount of fine particles to achieve good flow properties. Such a design with an air classifier is shown in the photo.

- Small space requirement: 1.95 meters by 2.44 meters and a height of 2.52 meters.
- Roller seating assures good mobility of the plant.
- Fast cleaning is obtained by easy-opening mechanism and easy disassembly or changing of built-in parts.
- Throughput range includes larger laboratory and smaller production quantities (Table 1), so that material samples for the customer's check can be produced more easily.
- Steep particle distributions are generated that can additionally be optimized by the use of a cyclone classifier.
Summary
Economic efficiency demands highly efficient production of powder coatings. This requires highly efficient process units to minimize the losses, such as those described above. Especially important for product quality is a narrow particle size distribution with a well-defined top size and a low amount of fine particles. Furthermore, grinding systems for small batches, as mentioned above, with low maintenance and fast, user-friendly cleaning are necessary.This paper is reprinted with permission from Vincentz Verlag. It was first published in Powder Coating Europe 2002.
Looking for a reprint of this article?
From high-res PDFs to custom plaques, order your copy today!