The Paint System Procurement Process

One important step in constructing a paint system is the procurement process. The procurement process can be broken into four basic steps: prequalifying bidders, preparing specifications, evaluating bids, and selecting the bidder and awarding the contract.
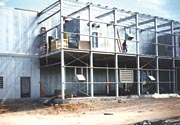
Qualifying contractors
System houses or installation contractors should be prequalified prior to soliciting bids for the project. The contractors should be experienced with the system type, have a strong focus in mechanical contracting, be financially and organizationally solid, and match the owner's expectations for quality, safety and operational efficiency.If a turnkey approach is used, the design and fabrication capabilities and experience will also have to be evaluated. A field of approximately six bidders should be prequalified with a goal to shortlist the field to three. Too few bidders may result in a less-than-competitive price; too many bidders confuse the process and waste the owner's and bidder's time and resources.
A quick word-of-mouth check with paint and chemical suppliers as well as a Web site visit can help choose bidders to prequalify based on the expected project budget and process complexity. The short-listed bidders should be comparable to each other, have a size and experience matched to the project scope and budget, and be able to meet the owner's expectations.
To prequalify bidders, a questionnaire or comparison spreadsheet can be formulated to gather information in the following areas:
Organization-The contractor's organization should match the scope of the project and the owner's infrastructure requirements. If the organization is too small, the project may suffer from a lack of resources or overwhelm the contractor with detail. If the contractor is too large, the project may take a low priority to larger, higher-risk projects, and less experienced personnel may be assigned to the project.
Experience and design capabilities-The contractor's experience should include projects similar in nature or scope to that being proposed. The depth of experience with different types of systems should also be examined to limit the possibility that the contractor will try to "shoehorn" the system into its particular specialty rather than use the best concept or equipment.
Project management capabilities-The contractor's project management capabilities are important to assure that the project is completed in an orderly and timely fashion. The project manager's typical responsibilities include: acting as the primary contact for the contractor, preparing and updating the project schedule, overseeing the contractor's personnel and subcontractors for quality of workmanship and adherence to specifications, fielding and resolving any questions or concerns the owner may have regarding the project, processing change orders and preparing progress reports. Having the same project manager involved from the beginning to the end of the project will help maintain project continuity.
Fabrication capabilities-A paint system involves various equipment, not all of which may be manufactured by the contractor. The owner should ascertain what equipment is designed and built by the contractor and what equipment will be outsourced. The more equipment is outsourced, the more the contractor will be challenged to maintain control over the project. In-house fabrication capabilities also permits timely delivery of equipment or material resulting from the all-too-often changes or damages encountered during the course of the project.
Installation capabilities-Top-quality installation is important to the eventual success of the system. Even with the best equipment, if sloppy installation procedures are followed, corners are cut, and the proper tools not used, the equipment may not function properly, may require additional maintenance or wear out prematurely. Many installation shortcuts are not known for years and can cause problems that are expensive to correct.
Select a contractor that uses its own experienced mechanical and electrical field personnel to install the equipment. Project control is greatest when the personnel are familiar with the equipment being installed. Crews should be dedicated to installation and consist of millwrights, electricians, pipefitters, welders and riggers. They should be accustomed to working away from home and not be shop personnel temporarily reassigned.
The owner should be aware of the licenses required to construct the project to avoid possible project delays if it is started without proper licensing. The state's licensing Web site should be consulted to establish what licenses apply and to check that the contractor's license is current. Additionally, the local municipality should be consulted regarding licensing requirements.
Service capabilities-Timely and experienced service after the sale is important to properly inspect and maintain the equipment. Production downtime can quickly eat into the owner's profits.
Training-How well training is provided will determine how quickly the system will reach its full potential and how quickly problems can be diagnosed and resolved. Having a thorough understanding of the system will also allow the operator to know the system's limitations as well as how to adjust and adapt it to new processes. The training should begin early in the project with operator site visits to similar facilities. Training should continue with observation and discussion during installation to familiarize the maintenance personnel with construction details hidden in the final product. Working side by side with the startup technicians will provide invaluable experience with troubleshooting procedures. After startup, formal training on the equipment should be conducted using the operations and maintenance manual as a syllabus. Paint, chemical and special equipment vendors should be included as part of the formal training process.
Safety-In today's litigious business environment, it can't be assumed that the contractor will be solely responsible if someone is harmed during the course of the project. In addition to verifying insurance policies, the owner must ascertain that the contractor has an active and adequate safety program. The Experience Modifier, a number assigned to the contractor by the state in which it does business, will help determine the relative safety record of the contractor.
Insurance-Insurance requirements will be an extremely important part of the project specifications and serve to protect the owner and its investment.
Warranty-Warranties can vary widely between vendors. Most cover only workmanship, with the repair or replacement at the contractor's discretion. Labor and shipping are not generally included. Most warranty periods are for one to two years, and some can be extended. The warranty description should detail what it includes and does not include.
Financial-The contractor's financial stability helps ensure that it will be able to meet all its obligations during the project's construction, the warranty period and for years to come with respect to service, upgrades and spare parts.
References and site visits-Request a list of all projects completed during the last five or more years. A short description of the scope of work should be included, as well as a description of the product, project goals, approximate cost and contact person. The list should be evaluated for diversity of projects, similarity to the owner's project and similarity of process or product.
During the prequalification stage, ask to visit the contractor's previous projects that are similar to yours. The visit should include a tour with the contractor's personnel to review process and construction features of the system but should also include time with the system owner away from the contractor's personnel for an "unbiased" opinion.
In addition to contractor-provided references, agencies such as the state Attorney General's office and the Better Business Bureau can be consulted to see if there's a history of litigation or dissatisfied customers. Also, trade organizations such as the Powder Coating Institute, Electrocoat Association and the Chemical Coaters Association International can be contacted for references.
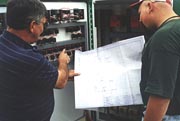
Preparing specifications
Preparation of detailed specifications for a system may seem complicated and cumbersome, but the specifications help assure a certain level of workmanship will be provided and that an "apples to apples" comparison between bidders will be easier. The specifications should identify the critical parameters and establish minimum requirements, yet allow the contractor to utilize options that mutually benefit all parties. The specifications should be concise, easily understood by everyone and applicable to the project.Specifications for the bid package, which can be altered in any fashion to meet the project's scope, can be divided into four basic sections:
- Scope of work
- Instructions to bidders
- Technical specifications
- General specifications
A full description of the product, or products, to be painted should be provided to the paint system contractor. The information should include dimensions of the largest part and as many of the parts as information is available.
Production rates are based upon the part quantity, weight and/or area per some time period, such as an hour, shift or day.
The paint to be used is determined by the performance requirements of the product.
The coating processes are the steps required to successfully meet the paint performance requirements. The process is typically determined jointly by the owner and suppliers of paint, chemicals and equipment, and identifies the times, temperatures, humidity and other conditions that must be met. Although the process varies widely, it typically includes, but is not limited to, chemical and/or physical treatment of the product surface to clean it and create a profile to enhance paint adhesion, drying, paint application, curing, cooling and pollution abatement.
The fifth P is the plant, or physical area that will be utilized to house the system. This information must be gathered and transferred to the contractor to determine a system layout and configure the equipment as well as plan the specifics of system installation.
Instructions to bidders-The instructions to bidders answers "who, where, when and how" the bids should be prepared to ensure that they meet the scope of the work and that they can be compared to other proposals.
The contractor should provide a detailed proposal that states how the system will meet the specifications, as well as describe the equipment design, construction, components, serviceability and installation. Bidders should follow the specifications but also offer exceptions that can result in process improvement or cost savings. All exceptions should be clearly presented and separately listed, including all cost and schedule impacts on the base bid. Also, the contractor's project management and/or installation personnel should visit the site.
Technical specifications-The technical specifications provide the information on the specific equipment to be incorporated into the system. The technical specifications need to be detailed in the presentation of process requirements and minimum design standards but general enough to allow suppliers to provide their standard designs and work methods. Doing so shifts some of the liability for the design and workmanship to the experts supplying the equipment.
General specifications-General specifications, as the name implies, are more general in nature and can apply to almost any capital project undertaken by the owner. They include: owner-specific specifications, workmanship and material specifications, and administrative specifications.
Owner-specific specifications are specific to the plant where the paint system is to be installed and may exist as corporate-wide specifications for companies with multiple plants. Generally prepared by facilities or maintenance personnel, these specifications allow very little leeway with regard to methods and materials. They are important to maintain similarity between manufacturing equipment and enable greater familiarity and faster response with respect to repair and replacement as well as common spare parts inventory. The owner-specific specifications also cover on-site contractor safety rules, identify temporary utilities and facilities for installation crews, material delivery and storage instructions, and what equipment may be supplied by the owner.
Like the technical specifications, workmanship and material specifications cover minimum requirements for material and workmanship but are more general in nature than the technical specifications and can apply to a range of equipment. Standard specifications for many areas of work are available from groups such as Construction Specifications Institute (www.csinet.org) and the American Institute of Architects (www.aia.org) and can be used as applicable to the project.
Administrative specifications cover a wide variety of issues, including: insurance, documentation, taxes, change orders, legal, performance and project management.
Evaluating bids
The best way to compare and evaluate bids is to construct a "comparison spreadsheet," listing pertinent and important parameters from the specifications in one column and the contractor-specific information in adjacent columns. The spreadsheet can be sent digitally to the individual contractors for completion and, when returned, compiled into one master sheet, which easily compares the three bids. The spreadsheet should be as detailed as possible and can typically be 10 to 15 pages long.Awarding the contract
The selection of a contractor should be based upon provision of the greatest value, not the least cost. The cost of potential production shutdowns for repairs should be factored heavily when considering supplier selection. Extended periods of shutdown can lead to expensive production delays. It is important to do it right the first time.If the specifications have been properly constructed, the resulting price range should be close. The least-cost bid, especially if it's far below the other contractors, may indicate an "under bid," and the contractor may try to make up costs during the course of the project by cutting corners. The comparison spreadsheet will easily point out differences but cannot be relied upon to show the best value. Detailed analysis of the differences is required and follow-up questioning of the contractor is recommended. For example, if one contractor's washer pumps are larger than another, it can mean a better value with built-in flexibility, or it could mean that the particular piping design is not as efficient as the next contractor's and requires a larger size to overcome dynamic head.
The final contract should summarize the scope of work; identify the involved parties and contacts; identify the project name and location; reference all the pertinent documents; and list the cost, payment schedule and project schedule. Dated signature lines should be provided for principals from each organization. Pertinent documents, such as the specifications, the contractor's proposal and drawings, and any other documents or terms and conditions that may be pertinent to the project should be attached as appendices.
Contracts are drafted to allocate responsibilities, set standards and identify remedies between the parties. The allocation is based upon the simple fact that someone must pay for all elements of the project. The contract should be fair and constructed to provide and encourage a "win-win" philosophy between the owner and contractor. It is in the owner's best interest to keep the supplier viable to ensure future upgrade capability, on-going service and availability of spare parts.
Unreasonable or unfair contracts that attempt to assign all the project risks from the owner to the contractor merely raise the probability of change orders and disputes. Disruptions and disputes on a construction project are expensive to all involved, and if it proceeds to court, it will be in an American legal system that is slanted against the drafters of unfair contracts. Disputes can be avoided or minimized by early recognition of the problem, good communication between the owner and contractor, accurate definition and documentation of the problem, fair assessment of the cost and schedule impacts, and agreement to work together to reach an equitable solution.
Proper planning, dedicated information gathering, thorough investigation of suppliers, diligent documentation and a commitment to establishing a win-win, team-supported environment will spell success.
Looking for a reprint of this article?
From high-res PDFs to custom plaques, order your copy today!