Zinc-Rich Primers With Micaceous Iron Oxide
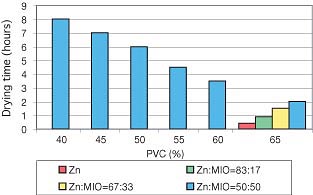
MIO pigment is used in paints to provide long-term durability. MIO paints have been used continuously since the early 1900s to protect steel1.
MIO, also known as specular haematite and flaky haematite, is a natural mineral ore that, after it's refined, consists mainly of Fe2O3. MIO differs in form and shape from the well-known iron oxides that are used as pigments for red, yellow, brown and black pigmentation. MIO shows a flaky, lamellar structure and is dark gray with a metallic sheen. The term "micaceous" is used because the lamellar particles are similar to mica2,3.
MIO is insoluble in water, organic solvents and alkalis and is only slightly soluble in strong acids at elevated temperatures. It is nonreactive with most chemicals and is heat-stable up to its melting point of over 1,500°C.
MIO is used widely in protective coatings due to its outstanding anticorrosive properties. When MIO is incorporated into a coating at an appropriate level, the flakes align parallel to the substrate surface, producing a shield or barrier of overlapping plates. The flakes are impermeable-a physical barrier is formed to the ingress of the water, oxygen and ions that corrode steel and degrade the binder system. MIO flakes are strong UV absorbers and very weather-resistant. This protects the surface of the binder system from the degrading action of UV and other weathering elements. MIO reinforces the binder matrix and increases the substrate adhesion and inter-coat adhesion.
The size of MIO flakes (normally 40 to 50 µm long and 5 to 10 µm thick) dictates a dry-film thickness in excess of 50 µm to achieve a shield of overlapping flakes. For this reason, MIO is normally found in high-film-build intermediate and finishing coats.
Recent developments in MIO technology have led to the introduction of a range of ultra-thin pigments with a flake thickness of only 1 to 2 µm. They are increasingly being used in film applications, particularly shop primers, where they provide cost and environmental benefits4.
Ultra-thin MIO pigments can also replace zinc dust in zinc-rich primers. The unique chemical and physical properties of the pigment may produce a packing structure that would enable zinc levels to be reduced. This pigment offers formulators an opportunity to reduce environmental impact while maintaining anticorrosion performance, and-unlike many environmentally friendly technologies-at a significantly reduced formulation cost5.
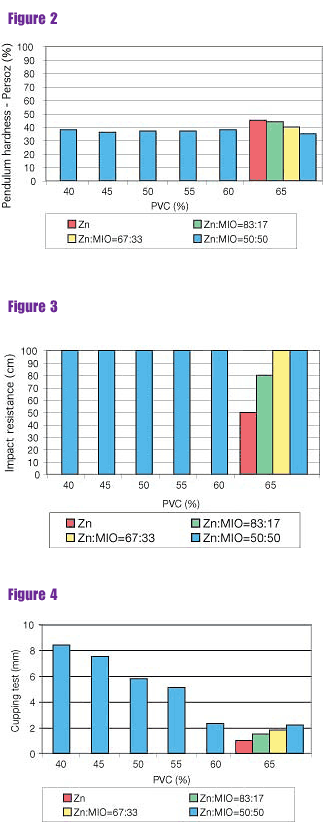
Figure 3: Influence of PVC and Ratio of Zn Dust and MIO-Results of Impact Resistance (after 28 days)
Figure 4: Influence of PVC and Ratio of Zn Dust and MIO-Results of Cupping Test (after 28 days)
Primers based on spherical zinc dust and MIO
The preparation of zinc-rich primers was based on a semisolid epoxy resin, a polyaminoamide adduct-like hardener, spherical zinc dust and the MIO.Paints were formulated with a pigment volume concentration (PVC) from 40 to 65%; the volume ratio of zinc dust and MIO was 1:1. The partial replacement of spherical zinc dust by MIO was examined with PVC = 65%; the ratio between spherical zinc dust and MIO was changed to 83:17, 67:33 and 50:50, respectively. The pearl mill was used for preparing the primers.
The basic properties of paint films were evaluated. The anticorrosive effect of single-layer paints and the paint systems were also determined. Such characteristics as drying time, pendulum hardness, cupping test, impact resistance, bending test and adhesion were tested over four weeks.
New degreased and ground steel panels were used for the tests. The size of the panels was 100 by 150 by 1 mm. Single-layer coatings of zinc-rich epoxy primers with a dry thickness of 60 ± 5 µm were prepared. Protective paint systems consisted of one coat of zinc-rich epoxy primer and two-component acrylic polyurethane as the finish coat (dry-film thickness of 160 ± 15 µm). In all cases, the panels were prepared in triplicate and stored for four weeks for hardening at /23 ±2/ °C and /50 ±5/ % relative humidity.
The single-layer coatings and the paint systems were exposed to:
1. Salt-spray (fog) testing according to ISO 9227
2. Humid atmospheres containing SO2-cyclic accelerated corrosion tests: eight hours in a humidity cabinet with SO2 and 16 hours in the ambient atmosphere-ISO 3231.
Anticorrosive protection of the paint systems was evaluated according to ASTM D 1654-92, D 610-85 and D 714-87. Heubach rating was used for testing of anticorrosive effects-100 is the best and 0 is the worst.
The adhesion of the paint systems was evaluated as cross cut test ISO 2409. The adhesion was tested before the beginning of corrosion tests and after completion of these tests.

The properties of cured paints
The PVC and the mutual ratio of spherical zinc dust and MIO influenced the drying time considerably. Primers based on a combination of spherical zinc dust and MIO (1:1) with a PVC of 40% needed the longest time for this stage: eight hours (Figure 1, page 27). The pendulum hardness was lower when the content of MIO increased (Figure 2).Micaceous iron oxid positively influenced the mechanical properties of the films. The coatings prepared from primers based on the combination of spherical zinc and MIO had excellent impact resistance (Figure 3). The results of the cupping test and the bending test deteriorated step by step at the range of PVC from 40 to 65 (Figures 4 and 5).
It follows from the results of testing the primers with PVC = 65% that the higher the content of MIO, the better the impact resistance, the better cupping test results and the better the bending test. All coatings produced excellent adhesion.
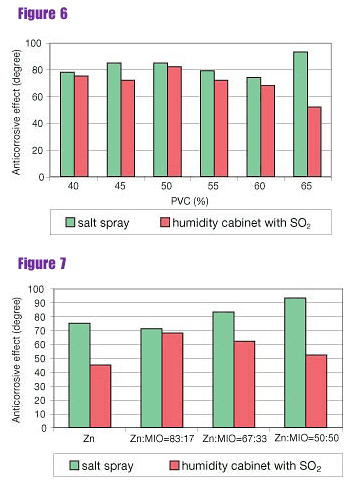
Figure 7: Anticorrosive Effect of Single-Layer Zinc-Rich Primers - PVC = 65%-Results of Pendulum Hardness (after 28 days)
The anticorrosive effect
Salt spray (fog) test-It follows from the results of testing single-layer primers exposed to salt spray that the content of MIO and PVC significantly influenced the anticorrosive effect. The anticorrosive effect at the range of PVC from 40 to 50% first increased and then decreased when PVC was 55% and 60%. The best anticorrosive effect was found in the formulation with PVC at 65%, at a combination of spherical zinc dust and MIO of 50% each.The barrier mechanism of lamellar MIO probably played a greater role than the electrochemical mechanism of zinc dust and later barrier mechanism of the zinc corrosion products (Figures 6 and 7, following page). A similar trend was observed with the paint systems (Figures 8 and 9, following page). Differences in anticorrosive effects were lower in the case of paint systems because the results were influenced by the top coat.
Humidity cabinet with sulphur dioxide-It follows from the results of testing single-layer paints exposed to a humidity cabinet with SO2 (Figure 6) that the barrier mechanism of the binder is evident at PVC = 40%. The optimal anticorrosive effect is achieved at PVC = 50% when the anticorrosive effect had a degree 82. As PVC was increased, the film became more porous and the anticorrosive effect decreased.
Single-layer paints from the primer based on spherical zinc dust only provided a low anticorrosive effect-degree 45 (Figure 7).
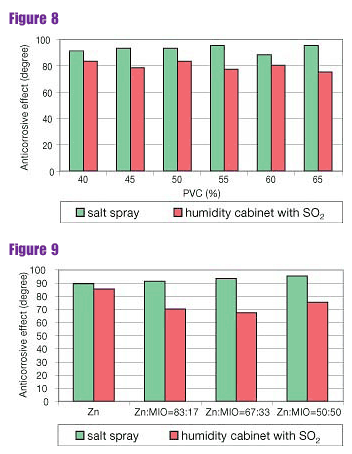
Figure 9: Anticorrosive Effect of Paint Systems - PVC= 65%- Results of Cupping Test (after 28 days)
It follows from the results of testing paint systems that the top two-component polyurethane enamel influenced the anticorrosive effect significantly (Figures 8 and 9).
All paint systems had excellent adhesion before the testing in corrosion chambers (degree 0). The adhesion of the paint system with the spherical zinc dust only was worse after 1,512 hours of exposure in both corrosion environments (degree 2). The paint systems containing MIO had excellent adhesion after completion of the corrosion tests.
Sidebar: Results at a glance
The drying time of zinc-rich primers containing MIO was longer and hardness was lower, but impact resistance, cupping test and bending test results were better.The formulation based on the combination of spherical zinc dust with the MIO at the ratio 1:1 and PVC = 50 % had the best anticorrosive effect. MIO positively influenced the adhesion of paints after the exposition in corrosive environments.
It was possible to reduce the content of zinc dust in dry film to 49.8% by weight; 45% by weight of zinc dust could be spared compared with zinc-rich primer based on spherical zinc dust only.
These results document that the use of micaceous iron oxide at the formulation of zinc-rich primers is advantageous for both ecological and price reasons. A partial replacement of spherical zinc dust by micaceous iron oxide is advantageous.
Looking for a reprint of this article?
From high-res PDFs to custom plaques, order your copy today!