Retro-Reflective Powder Coatings

Drive anywhere at night, and you’ll see light from your vehicle’s headlights bouncing back at you from license plates, road signs, highway markers, railroad cars and other surfaces. This effect, known as a retro-reflectivity, typically is achieved by using retro-reflective tape. However, retro-reflective tape is costly to produce on a linear-foot basis, and it does not provide a corrosion-resistant surface. Tape also cannot provide a reflective surface on complex fabrications such as fire hydrants, mailboxes, bicycle frames and rims, sign posts, and fencing.
While some powder coatings have provided what is commercially known as a “reflective” surface, this usually has meant simply a high gloss level. This type of reflection, where light is “scattered” or diffused, is not retro-reflection.
Recently, North Coast Polymers in Port Clinton, OH, has created and patented a process using retro-reflective elements and a new formulation of powders to create a retro-reflective surface with powder coatings. Using this cost-effective process, all surfaces that can be powder coated - including metals, plastics, wood and glass - can be made to reflect light at night, thereby improving safety.
The Process
The process begins the same as most powder coating operations. The part is pretreated normally, then the coating is applied through spraying or a fluidized dip and is subsequently baked. While some proprietary nuances are involved, the process involves minimal line adjustments and up-front costs. There are few changes in the overall powder coating process.The reflectivity of the coating rivals that of the tape seen on stop signs and other highway safety items. The color of the reflection is a bright white, no matter what daytime color option is used. Red, yellow, green and even black all reflect a bright, luminous white at night.
In addition to retro-reflection, the powder also provides improved salt spray resistance. Parts that have been coated in this process have passed well over 4,000 hours of ASTM B 117 (salt spray) testing. The substrates that have been tested in this manner were simply cold rolled steel panels, with no other pretreatment than a basic iron phosphate cleaner/sealer, typical of the pretreatment that most coaters use. The powder itself both chemically and mechanically bonds to any substrate to create excellent adhesion. Hot dipped galvanized panels have exceeded 6,000 hours in the same corrosion test and were pulled only because all other comparable coatings had failed at the scribe.
The coating must be applied at a minimum of 3.5 mils and can be applied as heavily as 20 mils through electrostatic spraying of a cold part.
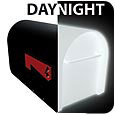
The Progress
North Coast Polymers is currently using the new process to produce retro-reflective mailboxes at its 40,000-ft2 facility in north central Ohio. The U.S. Federal Highway Safety Administration (FHWSA) is evaluating the coating for possible additional uses. North Coast is also working with the national highway safety director of Germany to investigate coating guardrails in that country to improve safety, and perhaps replace the need for hot dipped galvanization, which is environmentally unfriendly and quite costly.Through technology licensing and other arrangements, the company hopes to see retro-reflective powder coatings take over a substantial share of the market from tapes in the coming years.
“We believe that nighttime safety could improve drastically as a result of this coating,’’ says Aaron Bates, vice president of North Coast.
For more information about the retro-reflective powder coating process, call North Coast Polymers at 419.734.2122 or e-mail rekraft@msn.com or ab3000_1@hotmail.com.
Looking for a reprint of this article?
From high-res PDFs to custom plaques, order your copy today!