Seaworthy Powder Coating Solutions
Reducing the amount of fuel used by ships could have a significant impact on pollution, as well as save substantial amounts of money. One way to achieve this goal is to use coatings that prevent the growth of marine organisms. By eliminating the surface resistance caused by the buildup of these organisms on the hulls of marine vessels, such coatings can reduce the amount of fuel needed to propel the vessel. New powder coatings and thermal spraying devices are making it easier and more cost-effective to apply these coatings to today’s marine vessels.
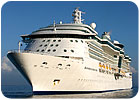
“Water, water everywhere, nor any drop to drink…” laments the ancient mariner in the poem of the same name. Though many of us remember this line from our school days, few of us recall the next line, “The very deep did rot.” Even without remembering the text, many of us today would repeat the ancient mariner’s complaints: The water around us is barely fit to drink, and the pollution problem indeed runs deep. Polluted coastal waters cost the world economy more than $12.5 billion dollars annually in death and disease. At least part of the problem stems from the burning of fossil fuels, which account for 80% of the world’s total energy supply. Total world consumption of these fuels is estimated to be the equivalent of 10,000 million tons of oil per year. And the problem is increasing. The world’s emerging economies, like China and India, are expected to double their per capita energy use in the coming decade. It is not surprising that scientists now believe that the burning of these fuels will dramatically alter marine life.
It is estimated that the shipping industry uses 350 to 410 million tons of fuel annually, resulting in millions of tons of carbon dioxide emissions. Global emissions of CO2 from shipping are believed to be twice the amounts emitted from aviation. Reducing the amount of fuel used by ships could therefore have a significant impact on pollution, as well as save substantial amounts of money.
One way to achieve this goal is to use coatings that prevent the growth of marine organisms. By eliminating the surface resistance caused by the buildup of these organisms on the hulls of marine vessels, such coatings can reduce the amount of fuel needed to propel the vessel. New powder coatings and thermal spraying devices are making it easier and more cost-effective to apply these coatings to today’s marine vessels.

The patent-pending powder coating contains a network of evenly dispersed active cupric oxide and silver ions in a polymer matrix that is fully melted when applied with a proprietary thermal spray process. The polymer matrix serves to hold the cupric oxide in place for years. With conventional paints that contain cupric oxide, the particles closest to the surface quickly ablate, leaving a space so that water gets leverage on the surface of the paint. This ablation is accelerated, limiting coating life. With the new powder coating, the active ingredients are always strongly held and available in the coating, and the coating leaches at less than 1/10 the rate permitted by the EPA, while providing superior protection. Even if there should be some break or “tear” in the coating, a nylon-modified fuse bond epoxy between the hull and coating will maintain the coating’s integrity.
To enhance the action of the cupric oxide, the new marine coating has micro-channels in the surface. These micro-channels serve to increase the effective surface area of exposed cupric oxide - like microscopic plastic “fists,” with the fingers tightly holding the copper oxide. Water swirls around the fist and between the fingers, touching copper at many points, but the fist never releases its grip on the copper.
“Copper has been used to protect boat coatings for centuries. The secret was to develop a matrix that would hold the copper and silver oxides in place and prevent them from quickly wearing away,” said Andrew Mazzone, president of Xiom Corp. Testing at the Florida Institute of Technology has confirmed the results that can be achieved with the new coating (see Figure 1).
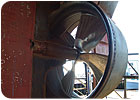
The gap between the propeller blade tips and the nozzle barrel is designed to ensure that the propellers do not come into direct contact with the Kort nozzle barrel due to metal shrinkage or expansion caused by pressure. However, this gap also reduces the amount of thrust available to the vessel.
A new thermally applied spray coating and proprietary automated spraying device can be used together to coat Kort nozzle barrels with a thermoplastic composition that reduces the clearance between the propeller blade tips and the interior of the Kort nozzle (see Figure 3). The coating is applied at a minimal thickness over the entire interior of the cylinder. A thicker coating is applied to the area in which the propeller blades rotate, ensuring that the inside diameter of the nozzle is equal to the diameter circumscribed by the blade tips: There is no gap between the propeller blade tips and the wall of the Kort nozzle barrel. A zero-degree gap results in increased pressure and momentum while preventing cavitation (the bubbles that form when a liquid is being pumped), dampening sound and eliminating “blow-by” (unburned fuel and exhaust gases that escape around the piston rings and enter the crankcase, potentially compromising engine performance). The concept is similar to that used in jet engines, where a coating is used to bridge the gap between the jet engine housing and the fan blades.
When the coating is applied on the inside surface of a Kort nozzle, the available thrust is increased with no additional energy input. The coating makes the nozzle more efficient, substantially reducing fuel consumption and protecting the structure from corrosion. The coating can be used on both new and used Kort nozzles and can stand up to a concentration of water movement that normally produces severe wear on the inside of the nozzle, which further reduces efficiency.
The proprietary thermal spray device designed for coating Kort nozzles uses specialized software and a robotic arc to follow the contour of the wall of the Kort nozzle and remediate concentricity imperfections that may exist as a result of wear or from manufacturing. Kort nozzles are rarely manufactured concentric; machining a perfectly concentric barrel would be time-consuming and expensive. The coating can be applied while the vessel is out of the water and the Kort nozzle is still installed on the vessel, reducing the labor and time associated with removing the nozzle from a vessel to apply the coating.
A sea trial recently was conducted on a 75-ft steel fishing boat operating out of New Bedford, MA. The vessel’s 6-ft-diameter Kort nozzle had been coated with the new zero-degree clearance coating. The fuel savings were approximately 16%. The vessel’s normal fuel consumption averaged 510 gallons per day at 4.3 knots pulling a drag line. With the modified Kort nozzle, the vessel averaged 430 gallons of fuel per day pulling a drag line at 5 knots against a 35 knot wind.
According to Charlie Quinn, captain of the vessel, “Usually the gap is ¾-1 in. between the blade and nozzle. We took the Xiom coating and spray welded it onto the nozzle and got the gap down to ¼ in. We saved 15-20% on fuel and got more thrust with less rpm, as well as less wear and tear on the engine shaft for the boat’s first trip. Because we’ll be using less fuel, we’ll be able to travel farther and spend more time out on the water.”
For more information, call 866.688.9466 (XIOM) or 631.643.4400, or visit www.xiom-corp.com.
Do you know of an innovative new product that should be featured in our Innovation Spotlight? If so, contact Managing Editor Kristi Grahl at 248.366.6981 or grahlk@sbcglobal.net.
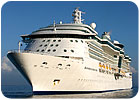
“Water, water everywhere, nor any drop to drink…” laments the ancient mariner in the poem of the same name. Though many of us remember this line from our school days, few of us recall the next line, “The very deep did rot.” Even without remembering the text, many of us today would repeat the ancient mariner’s complaints: The water around us is barely fit to drink, and the pollution problem indeed runs deep. Polluted coastal waters cost the world economy more than $12.5 billion dollars annually in death and disease. At least part of the problem stems from the burning of fossil fuels, which account for 80% of the world’s total energy supply. Total world consumption of these fuels is estimated to be the equivalent of 10,000 million tons of oil per year. And the problem is increasing. The world’s emerging economies, like China and India, are expected to double their per capita energy use in the coming decade. It is not surprising that scientists now believe that the burning of these fuels will dramatically alter marine life.
It is estimated that the shipping industry uses 350 to 410 million tons of fuel annually, resulting in millions of tons of carbon dioxide emissions. Global emissions of CO2 from shipping are believed to be twice the amounts emitted from aviation. Reducing the amount of fuel used by ships could therefore have a significant impact on pollution, as well as save substantial amounts of money.
One way to achieve this goal is to use coatings that prevent the growth of marine organisms. By eliminating the surface resistance caused by the buildup of these organisms on the hulls of marine vessels, such coatings can reduce the amount of fuel needed to propel the vessel. New powder coatings and thermal spraying devices are making it easier and more cost-effective to apply these coatings to today’s marine vessels.

Figure 1. These images illustrate test results obtained from the Center for Corrosion and Biofouling Control at the Florida Institute of Technology, Melbourne, FL. The test was performed on a series of 4 x 8-in. static immersion panels that were held 3.3 ft (1 m) under the surface in the Indian River Lagoon in Florida from May 24, 2006 to June 1, 2007. The front and back of the control panels was uncoated and exhibited extensive macrofouling from barnacles and tubeworms; the other panels, which remained relatively free of macrofouling, were coated with the new protective powder coating.
Powders in a Polymer Matrix
One such advance is an environmentally safe, self-cleaning, marine vessel hull protective powder coating. Developed for both steel and fiberglass boat bottoms, the coating significantly reduces maintenance costs and fuel consumption caused by marine growth. The polymer/cupric oxide-based coating contains no tributyl tin (TBT) or volatile organic compounds (VOCs), and it does not ablate or wear away. It is estimated that the new marine coating will last five times longer than conventional paints, reducing the need for scraping or repainting the hull.The patent-pending powder coating contains a network of evenly dispersed active cupric oxide and silver ions in a polymer matrix that is fully melted when applied with a proprietary thermal spray process. The polymer matrix serves to hold the cupric oxide in place for years. With conventional paints that contain cupric oxide, the particles closest to the surface quickly ablate, leaving a space so that water gets leverage on the surface of the paint. This ablation is accelerated, limiting coating life. With the new powder coating, the active ingredients are always strongly held and available in the coating, and the coating leaches at less than 1/10 the rate permitted by the EPA, while providing superior protection. Even if there should be some break or “tear” in the coating, a nylon-modified fuse bond epoxy between the hull and coating will maintain the coating’s integrity.
To enhance the action of the cupric oxide, the new marine coating has micro-channels in the surface. These micro-channels serve to increase the effective surface area of exposed cupric oxide - like microscopic plastic “fists,” with the fingers tightly holding the copper oxide. Water swirls around the fist and between the fingers, touching copper at many points, but the fist never releases its grip on the copper.
“Copper has been used to protect boat coatings for centuries. The secret was to develop a matrix that would hold the copper and silver oxides in place and prevent them from quickly wearing away,” said Andrew Mazzone, president of Xiom Corp. Testing at the Florida Institute of Technology has confirmed the results that can be achieved with the new coating (see Figure 1).
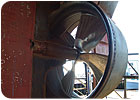
Figure 2. A Kort nozzle provides increased control of the water turbulence passing through it.
Closing the Gap
One other way to reduce the fuel consumption of marine vessels is by improving the hydro-drive device known as a Kort nozzle, which is used on thousands of fishing boats, supply vessels, inland river boats and passenger boats around the world. This nozzle is a cylindrical tube that surrounds a screw propeller and provides increased control of the water turbulence passing through it (see Figure 2). Designed according to the principles of physics regarding fluid velocity, the Kort nozzle has a wide diameter at the intake and is thinnest at the center where the propeller turns. The diameter is also thinner at the outlet than at the inlet so that there is an increase in net velocity and energy of the water flow, leading to greater propeller efficiency.The gap between the propeller blade tips and the nozzle barrel is designed to ensure that the propellers do not come into direct contact with the Kort nozzle barrel due to metal shrinkage or expansion caused by pressure. However, this gap also reduces the amount of thrust available to the vessel.
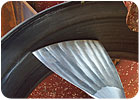
Figure 3. Coating Kort nozzle barrels with a thermally applied spray coating can eliminate the gap between the propeller blade tips and the wall of the Kort nozzle barrel, thereby making the nozzle more efficient.
When the coating is applied on the inside surface of a Kort nozzle, the available thrust is increased with no additional energy input. The coating makes the nozzle more efficient, substantially reducing fuel consumption and protecting the structure from corrosion. The coating can be used on both new and used Kort nozzles and can stand up to a concentration of water movement that normally produces severe wear on the inside of the nozzle, which further reduces efficiency.
The proprietary thermal spray device designed for coating Kort nozzles uses specialized software and a robotic arc to follow the contour of the wall of the Kort nozzle and remediate concentricity imperfections that may exist as a result of wear or from manufacturing. Kort nozzles are rarely manufactured concentric; machining a perfectly concentric barrel would be time-consuming and expensive. The coating can be applied while the vessel is out of the water and the Kort nozzle is still installed on the vessel, reducing the labor and time associated with removing the nozzle from a vessel to apply the coating.
A sea trial recently was conducted on a 75-ft steel fishing boat operating out of New Bedford, MA. The vessel’s 6-ft-diameter Kort nozzle had been coated with the new zero-degree clearance coating. The fuel savings were approximately 16%. The vessel’s normal fuel consumption averaged 510 gallons per day at 4.3 knots pulling a drag line. With the modified Kort nozzle, the vessel averaged 430 gallons of fuel per day pulling a drag line at 5 knots against a 35 knot wind.
According to Charlie Quinn, captain of the vessel, “Usually the gap is ¾-1 in. between the blade and nozzle. We took the Xiom coating and spray welded it onto the nozzle and got the gap down to ¼ in. We saved 15-20% on fuel and got more thrust with less rpm, as well as less wear and tear on the engine shaft for the boat’s first trip. Because we’ll be using less fuel, we’ll be able to travel farther and spend more time out on the water.”
Cleaner Waters
Advanced powder coatings and application technologies are providing new levels of performance, economy and safety in the marine industry. Boat and ship owners can now enjoy reduced maintenance and fuel costs, and all of us can look forward to cleaner waters.For more information, call 866.688.9466 (XIOM) or 631.643.4400, or visit www.xiom-corp.com.
Do you know of an innovative new product that should be featured in our Innovation Spotlight? If so, contact Managing Editor Kristi Grahl at 248.366.6981 or grahlk@sbcglobal.net.
Looking for a reprint of this article?
From high-res PDFs to custom plaques, order your copy today!