AN FT ONLINE EXCLUSIVE: Learning to Speak Robotese
Man-machine interfaces have been slow to develop in the paint shop. Paint lines are still dominated by old fashioned knobs and buttons. Even the paint robot is a device that people go to school to learn to operate. Now one small Cleveland firm is helping to improve that with a product that allows paint operators to do tricks with robots and their tools without knowing much robot programming at all.
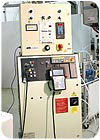
Imagine if every time you wanted to send an e-mail, you needed to write an assembly language program on your PC. The rapid growth of everyday devices from iPods to TIVO has been due in part to ease with which users can work them to do complex things easily. We appreciate that clicking “search” in Google lets loose a daunting series of instructions into cyberspace – thousands of commands running somewhere in the background, invisible to us.
In the words of Jeff Raskin, one of the smart guys who helped develop the original Apple McIntosh computer, “We have become accustomed to the ways that products work to the extent that we come to accept their methods as a given, even when their interfaces are unnecessarily complex, confusing, wasteful, and provocative of human error.”
And he should know since Apple pioneered basic tools that allow us to do complex things with better interfaces – like the mouse and the little picture icon we click on.
In the paint shop, man-machine interfaces have been slower to develop. Paint lines are still dominated by old fashioned knobs and buttons. Even the paint robot is a device that people go to school to learn to operate. Now one small Cleveland firm is helping to improve that with a product that allows paint operators to do tricks with robots and their tools without knowing much robot programming at all.
The Artomation e-CASO system is a graphic, friendly interface that translates operator instructions into the complex commands recognized by the robot. Want to make the path wider? Just click and stretch it and the robot responds. It is, in effect, a “translator for robotese.” In fact, it combines the robot motion with dozens of inputs and outputs of ancillary devices; paint pumps, spray gun controls and dispensing equipment along with the robot signals to produce a single unified paint program.
This simplifies the task of using a paint robot and puts it back in the hands of painters and not just engineers. Changes happen faster, and cost efficiencies improve.
The e-CASO interface is an extension of the work Artomation did to make working with their own machines easier. Artomation is a leading manufacturer of 2-, 3- and 4- axis gantry machines that are used to paint production parts, as well as the PanelPro line of test panel paint machines.
“We wanted a simple interface for panel painting” explains Artomation president John McDonough. “Mechanical interfaces like twisting dials and setting pressure regulators are prone to inaccuracy and lack the repeatability that’s needed for today’s complex coating systems,” says McDonough. “But we wanted something intuitive. You want to switch from a horizontal pattern to a vertical one – click on the picture and the software does it. You want to add a spray gun trigger point you simply click the spot on the path where you want to trigger.”
One of Artomation’s good customers, PPG Industries, was so fond of its Artomation PanelPro control system that when the company decided to add a robot to one of its facilities it asked Artomation to build an interface that could drive the robot.
The result is a system that controls not only the robot, but also the rotary atomizer, pumps and fluid delivery system as well. The robot, a Fanuc paint robot still needs to be programmed initially using traditional programming methods, but then the Artomation interface allows operators to make changes, and work with the programs without needed to program or use a teach pendant. Motion files can be called up in to a familiar Windows interface and manipulated by the operator. Different motion paths can be selected and modified by stretching or shrinking them to fit the application. At each “node” in the path, the operator can change paint settings, speed and the distance of the spray gun to the part.
Some of the variables that can be changed node-by-node include:
Aside from the programming features provided by the interface, the plain-speaking software has a host of friendly features that make working with equipment easier. Just as new versions of Windows allowed users to give meaningful names to files, the software allows operators to view detailed error messages, easily manipulate files and save descriptive information and instructions.
Artomation is looking to build on the translator, adding new phrases that will allow it to change tools, do increasingly complex tasks, even speak multiple robot languages. But in the meantime we can take some comfort in the fact that learning to speak to robots has gotten measurably easier.
For more information, visit www.artomation.com.
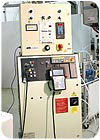
Imagine if every time you wanted to send an e-mail, you needed to write an assembly language program on your PC. The rapid growth of everyday devices from iPods to TIVO has been due in part to ease with which users can work them to do complex things easily. We appreciate that clicking “search” in Google lets loose a daunting series of instructions into cyberspace – thousands of commands running somewhere in the background, invisible to us.
In the words of Jeff Raskin, one of the smart guys who helped develop the original Apple McIntosh computer, “We have become accustomed to the ways that products work to the extent that we come to accept their methods as a given, even when their interfaces are unnecessarily complex, confusing, wasteful, and provocative of human error.”
And he should know since Apple pioneered basic tools that allow us to do complex things with better interfaces – like the mouse and the little picture icon we click on.
In the paint shop, man-machine interfaces have been slower to develop. Paint lines are still dominated by old fashioned knobs and buttons. Even the paint robot is a device that people go to school to learn to operate. Now one small Cleveland firm is helping to improve that with a product that allows paint operators to do tricks with robots and their tools without knowing much robot programming at all.
The Artomation e-CASO system is a graphic, friendly interface that translates operator instructions into the complex commands recognized by the robot. Want to make the path wider? Just click and stretch it and the robot responds. It is, in effect, a “translator for robotese.” In fact, it combines the robot motion with dozens of inputs and outputs of ancillary devices; paint pumps, spray gun controls and dispensing equipment along with the robot signals to produce a single unified paint program.
This simplifies the task of using a paint robot and puts it back in the hands of painters and not just engineers. Changes happen faster, and cost efficiencies improve.
The e-CASO interface is an extension of the work Artomation did to make working with their own machines easier. Artomation is a leading manufacturer of 2-, 3- and 4- axis gantry machines that are used to paint production parts, as well as the PanelPro line of test panel paint machines.
“We wanted a simple interface for panel painting” explains Artomation president John McDonough. “Mechanical interfaces like twisting dials and setting pressure regulators are prone to inaccuracy and lack the repeatability that’s needed for today’s complex coating systems,” says McDonough. “But we wanted something intuitive. You want to switch from a horizontal pattern to a vertical one – click on the picture and the software does it. You want to add a spray gun trigger point you simply click the spot on the path where you want to trigger.”
One of Artomation’s good customers, PPG Industries, was so fond of its Artomation PanelPro control system that when the company decided to add a robot to one of its facilities it asked Artomation to build an interface that could drive the robot.
The result is a system that controls not only the robot, but also the rotary atomizer, pumps and fluid delivery system as well. The robot, a Fanuc paint robot still needs to be programmed initially using traditional programming methods, but then the Artomation interface allows operators to make changes, and work with the programs without needed to program or use a teach pendant. Motion files can be called up in to a familiar Windows interface and manipulated by the operator. Different motion paths can be selected and modified by stretching or shrinking them to fit the application. At each “node” in the path, the operator can change paint settings, speed and the distance of the spray gun to the part.
Some of the variables that can be changed node-by-node include:
- Gun triggering
- Atomizing air pressure
- Shaping air pressure
- Electrostatic KV
- Bell speed
- Fluid flow
- Gun velocity
- Gun to part distance
- Pump operation
Aside from the programming features provided by the interface, the plain-speaking software has a host of friendly features that make working with equipment easier. Just as new versions of Windows allowed users to give meaningful names to files, the software allows operators to view detailed error messages, easily manipulate files and save descriptive information and instructions.
Artomation is looking to build on the translator, adding new phrases that will allow it to change tools, do increasingly complex tasks, even speak multiple robot languages. But in the meantime we can take some comfort in the fact that learning to speak to robots has gotten measurably easier.
For more information, visit www.artomation.com.
Looking for a reprint of this article?
From high-res PDFs to custom plaques, order your copy today!