Powder Coating Masking Fundamentals

How much time are you spending on masking before your parts get powder coated? Are you looking at a bunch of different masking products, unsure of what to actually use? If you’re looking to learn the fundamentals of masking before powder coating, this post is just what you need.
Surface Prep Before Masking
Before we get to masking, an absolute must is surface prep. In order to achieve the best masking and powder coating results, the surface that’s getting coated must be clean. One of the most common ways of prepping metal is by blasting in order to remove any existing finish, smooth out a lot of the defects and create a more adhesive surface for powder coating. This would then be followed by washing/pre-treating the surface with products specifically formulated for the oils associated with your fabricating process in order to remove any dirt, dust, oil or grease.
For this post, we used Simple Green All-Purpose Cleaner, but you can also use denatured alcohol. Most powder coating shops tend to put their parts through an extensive pre-treatment process
Having a clean surface is ABSOLUTELY VITAL when it comes to masking, especially when using adhesive tapes. This is the most common source of masking tape failure.
Tape It: Masking Flat Areas on Surfaces
When it comes to masking of flat areas on surfaces, high-temperature masking tapes tend to be the go-to option for most powder coaters. Surface prep will be absolutely critical before using any tape. A few more tips for achieving best results with masking tapes include:
- Wear gloves in order to avoid oil from your fingers from contaminating the surface and the tape.
- Apply pressure with a squeegee or roller to get adhesive linked to the metal to prevent any leakage.
- Remove the tape soon after part is done baking.
For powder coating, you'll want to ensure you're using the most appropriate high-temperature masking tape. To keep it simple, here are the recommended tapes that powder coaters use:
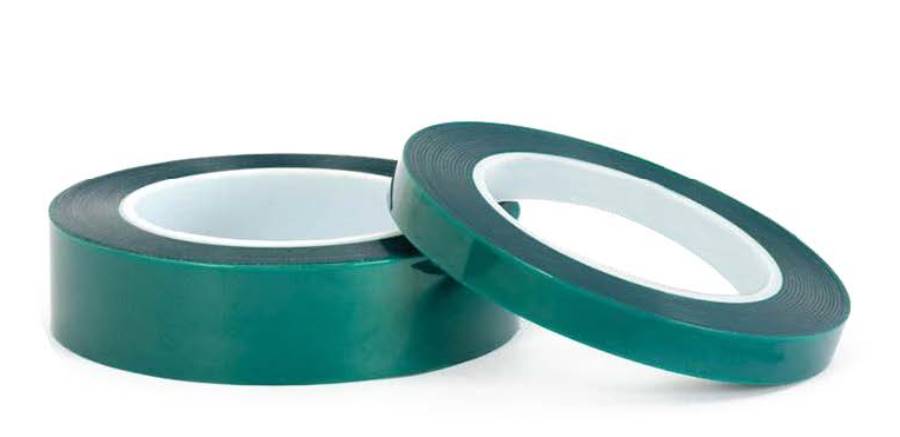
Green Poly Tape (400F) – Most Popular Option

Glass Cloth Tape (500F) – Great for thicker coats and higher temperatures
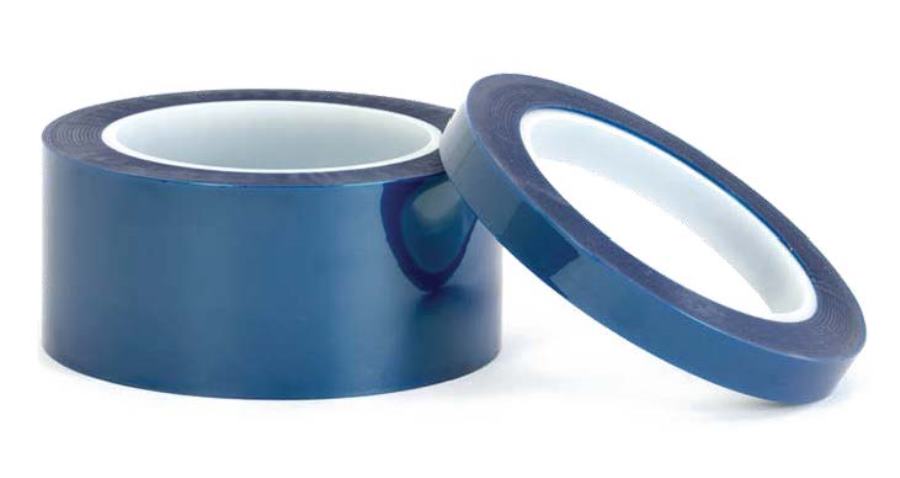
Blue Poly Tape (400F) – Thinner tape, making it ideal for curved, uneven surfaces
Plug It: Masking Threaded and Non-Threaded Holes
Masking holes, especially threaded holes, prior to powder coating is necessary for most coating projects and will eliminate the need for secondary ops involving thread chasers and taps. For this section, we're going to keep this fairly basic, as we have another post that goes more in-depth, but if you’re needing to mask off a threaded hole prior to powder coating, here’s how:
Masking Blind Holes
For blind holes, you’ll most likely want to use a silicone tapered plug. Blind holes require some form of high-temp push plug, as it's the only way to install.
Masking Through Holes
For through holes, you’ll most likely want to use silicone pull plugs as it will mask on both ends. Click here for more options on masking leading/exit threads. Whether masking a blind hole or a through hole, creating a tight seal on the leading threads is going to be vital towards keeping all threads clean.
Cap It: Masking Bolts, Studs, Rods and Tube Ends
When masking tube ends and exposed bolts before powder coating, you want to use a silicone cap that has a tight fit. The cap you'll want to choose will have an inside diameter (id) that is .030" smaller than the outside diameter of the part you're trying to mask.
If the part you're masking is long and requires the cap to be much longer, than we suggest also using silicone tubing.
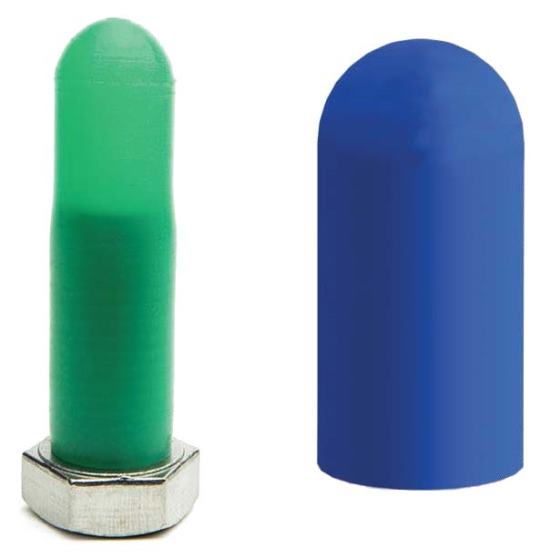
Conclusion
Masking prior to powder coating doesn’t need to be difficult. In essence, you’re either going to cap it, pug it, or tape it depending on what you’re masking. This guide was a basic overview of what to use to mask. Below you'll find other great resources to help take your powder coating skills to the next level.
For more information, visit https://www.echosupply.com/.