Fast-Dry DTM Alkyd Emulsion
with Excellent Corrosion Resistance

Solventborne alkyds continue to be widely used due to their balance of application and film performance attributes. Many resin suppliers have developed waterborne alkyds, dispersions or emulsions, but all have fallen short of solventborne performance. Performance gaps include dry time, gloss, adhesion, corrosion and humidity resistance. Low-VOC regulations continue to drive the alkyd market away from traditional solventborne alkyds. Exempt solvents have helped to extend their usefulness, but waterborne alkyd technology has failed to fill the gap on performance requirements for low-VOC coatings. Polynt has developed novel technology that bridges this performance gap, offering fast dry and excellent corrosion at near-zero VOC. This DTM alkyd emulsion closes the performance gap seen with current waterborne alkyd technologies and allows the paint formulator the opportunity to develop high-performance waterborne alkyd paint at near-zero VOC.
Low-VOC Driver
Use of solventborne alkyds continues to decrease 2% each year due to environmental concerns and the need for lower-VOC coatings. KNG predicted the use of solventborne alkyds would decrease from ~859 MM pounds in 2011 to ~781 MM pounds by 2016.1 Waterborne alkyd consumption has been growing and was forecast to grow 3% per year, from ~49 MM pounds in 2011 to 55.5 MM pounds in 2016. However, the growth of 6.5 MM pounds of waterborne alkyds does not replace the decline of ~78 MM pounds during that same five-year period. Thus, solventborne alkyds are being replaced by other low-VOC technology (most likely acrylic latex resins) much faster than with waterborne alkyds. Due to current performance shortcomings of alkyd resins in the marketplace, we believe that accelerated growth of waterborne alkyds could be achieved through improved performance.
Current Technology
Solventborne alkyds continue to be popular due to their versatility, ease of application, good adhesion to metal (even poorly prepared metal) and lower costs. High-solid alkyds were developed to address the need for lower VOC. To obtain higher solids at a useful viscosity, the molecular weight of the alkyd resins was lowered. This lower molecular weight has negative impact on dry time and overall coating performance, including corrosion protection.
Water-reducible alkyds were developed to offer options for even lower VOC than obtained with high-solids alkyds. Water-reducible alkyds typically utilize trimellitic anhydride or other raw materials that add carboxylic acid groups to the alkyd backbone. They are supplied at 70-75% NV in hydrophilic solvents, and the acid groups are neutralized with amine to make the alkyd water dispersible. Coatings with water-reducible alkyds can be formulated to 250-320 g/L VOC. However, water-reducible alkyd coatings also have limited shelf life due to the hydrophilic nature of the alkyd due to hydrolysis, which lowers the performance of the coating. Both high solids and water reducibles have been used for many years to achieve lower-VOC coatings not obtainable with conventional solids alkyds.
Two forms of waterborne alkyds are currently in the marketplace: alkyd emulsions and core shell dispersions. Alkyd emulsions are formed by adding surfactants, anionic and/or nonionic, to molten alkyd resin and then adding water under shear. An alkyd emulsion contains very little to no organic solvent, inverting from a water-in-oil to an oil-in-water mixture. Typically 5-10% surfactant levels are used to form an alkyd emulsion. These higher surfactant levels have shown a negative impact on dry time, gloss, corrosion and humidity resistance. An alkyd emulsion has more hydrolytic stability due to the surfactants surrounding the alkyd (Figure 1).
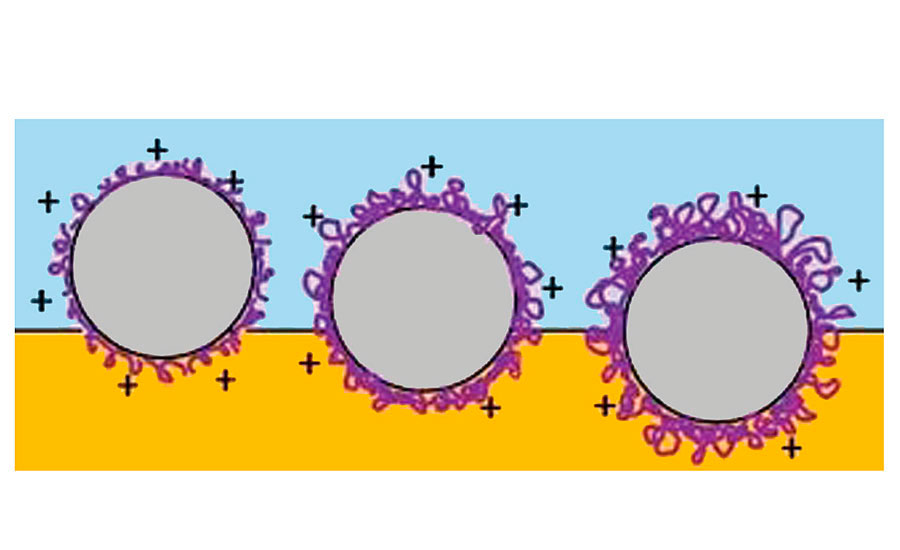
FIGURE 1 » Illustration of an alkyd emulsion
The second waterborne alkyd technology in the marketplace involves polymerizing a higher-Tg acrylic shell around an alkyd core; this technology is referred to as core shell alkyd dispersion (Figure 2). During manufacturing, an extremely low-molecular-weight alkyd is copolymerized with a high-Tg, hydrolysis-resistant acrylic monomer, grafting the acrylic to the alkyd. Acid functionality is built into the acrylic shell, which is then salted with an amine to make the acrylic-modified alkyd water dispersible. The acrylic shell surrounds the alkyd, protecting it from hydrolysis, making the core shell hybrid dispersion more shelf stable than a typical water-reducible alkyd. This core shell hybrid dispersion has faster dry times than an alkyd emulsion due to the high-Tg acrylic shell. Unfortunately during polymerization, a lot of homopolymer of acrylic monomers occurs (not attached to the alkyd). The high acid value of the acrylic homopolymer, and the fact that the alkyd core is lower molecular weight than typical, results in water sensitivity and poor corrosion resistance.
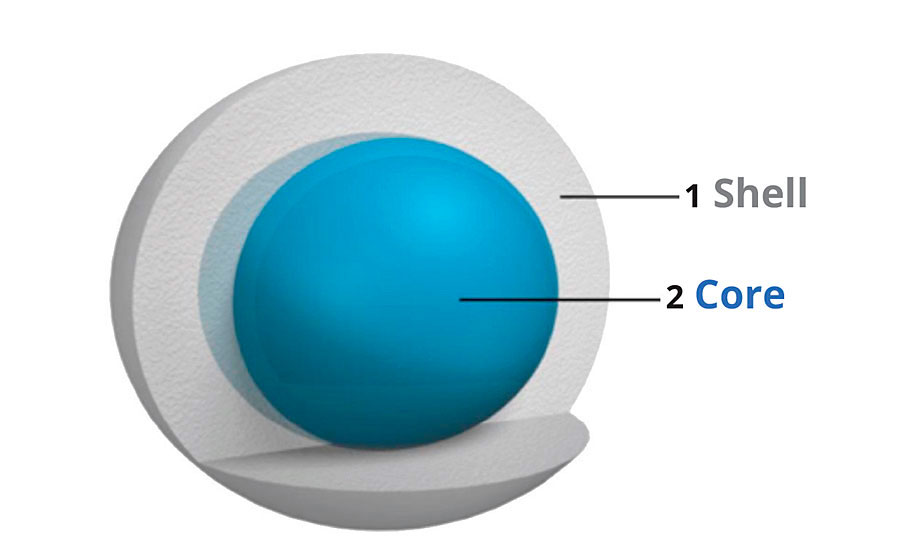
FIGURE 2 » Illustration of a core shell acrylic-modified alkyd dispersion
Ten customers who currently use waterborne alkyds were interviewed in 2014. They reported that the commercial waterborne alkyds either dried fast, but had poor corrosion performance, or they dried too slowly for their end use applications, but had good corrosion performance. Low gloss and water sensitivity were also identified as issues with the current waterborne alkyd technology. Our goal was to bridge this performance gap and leapfrog over the existing waterborne alkyd offerings. The objectives of this product development were established from these customer interviews as follows:
- 300 hrs salt spray on CRS;
- 60° gloss greater than 80%;
- Tack-free dry time less than 6 hrs;
- Through-dry time less than 12 hrs;
- Hardness development – greater than 40 seconds Koenig.
Samples of two competitive alkyd emulsions and two competitive core shell alkyd dispersions were obtained and tested for dry time, gloss, hardness, salt spray and condensing humidity resistance to benchmark against the newly developed product. The first alkyd emulsion had tack-free time of about 2 hrs and through-dry time of ~9 hrs (Table 1). Salt spray performance after 300 hrs at 1.5 and 2.0 mils DFT was marginal for scribe creep and blistering, and showed some face blistering. When tested 16 hrs on QCT humidity, the film had severe blistering and total loss of wet adhesion (Figure 3).
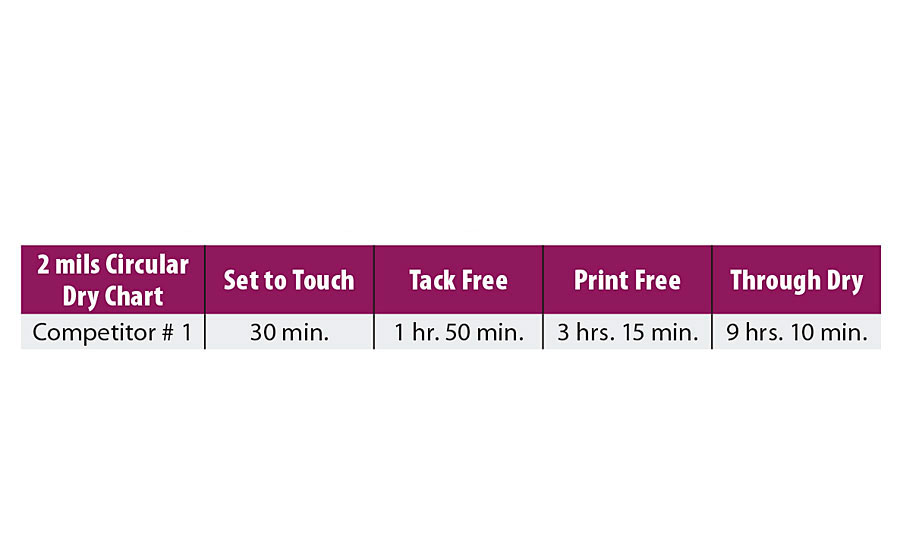
TABLE 1 » Dry time of competitive alkyd emulsion #1
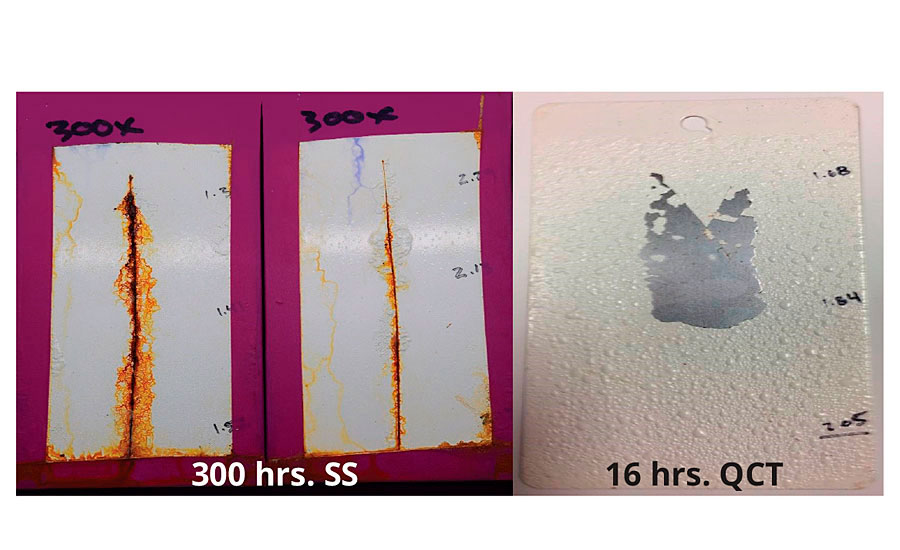
FIGURE 3 » Performance of competitive alkyd emulsion #1
The second competitive alkyd emulsion was also tested as above in the same white paint formulation. Tack-free time was a little slower at 3 hrs with the same through-dry time of ~9 hrs (Table 2). Gloss was also a little low at 76%. Salt spray performance after 300 hrs was also marginal for scribe creep, with some face rusting. QCT humidity testing at 16 hrs did not show blistering, but still had no wet adhesion (Figure 4). We concluded that high levels of surfactants or type of surfactants detract from salt spray and humidity resistance of the coating.
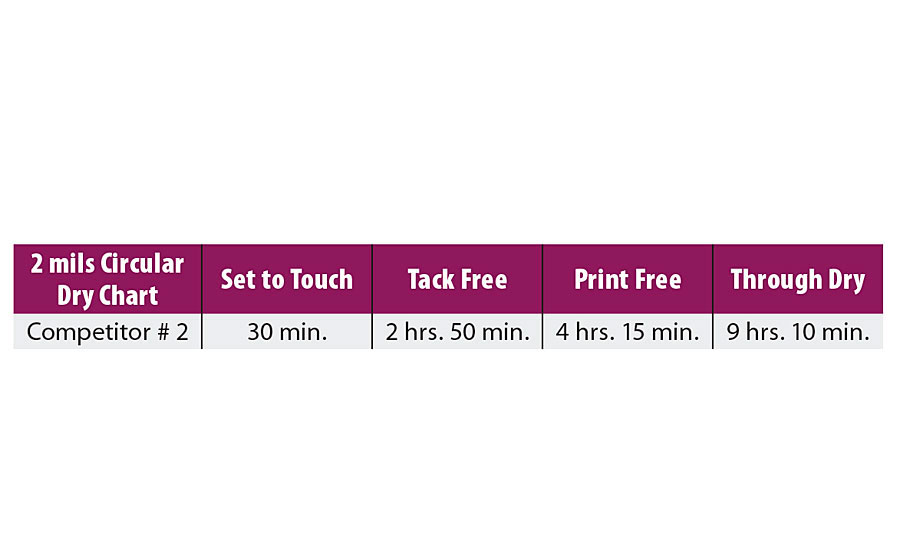
TABLE 2 » Dry time of competitive alkyd emulsion #2

FIGURE 4 » Performance of competitive alkyd emulsion #2
Two competitive core shell acrylic-modified alkyd dispersions were tested in the same white paint formulation. Through dry was extremely fast, three hours or less, as would be expected due to the high-Tg acrylic modification (Table 3). However, salt spray performance was very poor. Figure 5 represents 300 hrs salt spray test, but the test panels looked this bad after only 100 hrs.
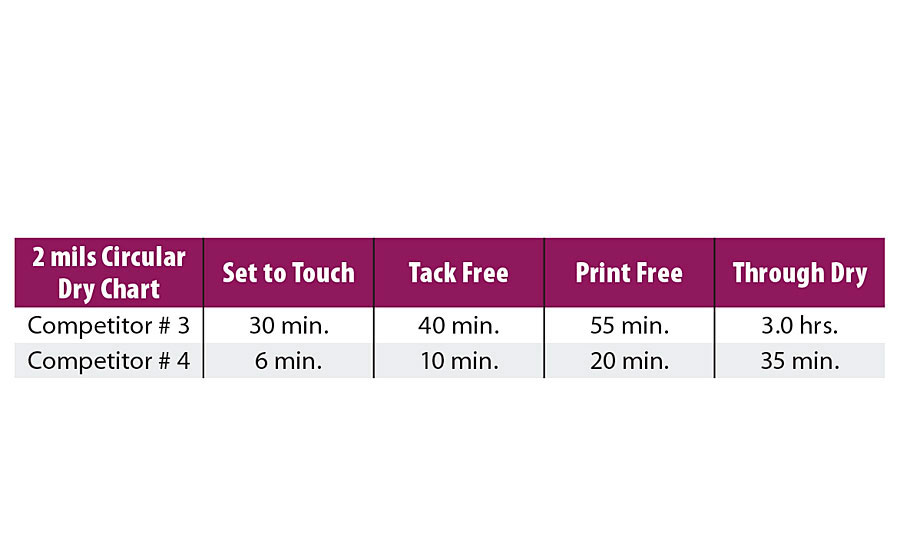
TABLE 3 » Dry time of competitive core shell acrylic-modified alkyd dispersions
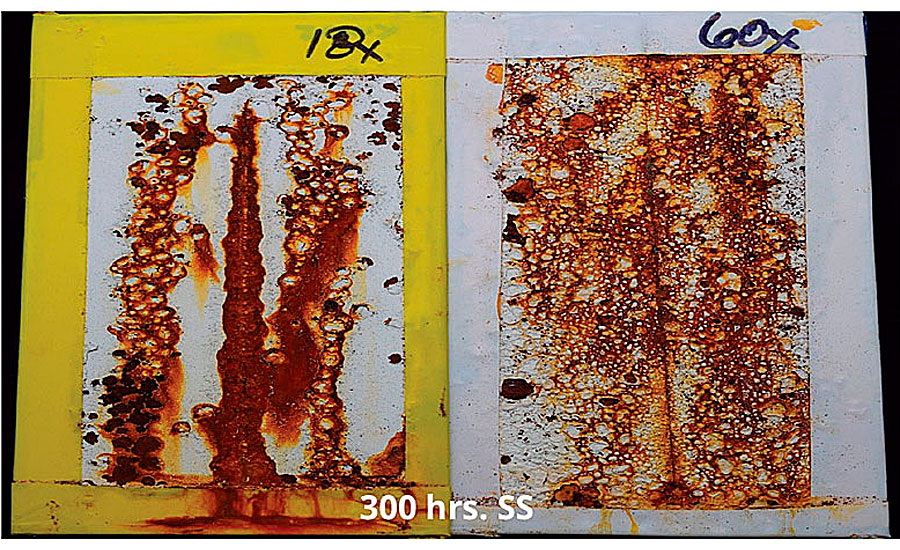
FIGURE 5 » Performance of competitive core shell acrylic-modified alkyd dispersions
Current waterborne alkyd technologies fall short. Alkyd emulsions have decent corrosion protection, but poor water resistance and slower dry times. Core shell dispersions have very fast dry, but very poor corrosion performance. Paint companies that provide waterborne alkyd coatings do so because they need to provide a near zero-VOC coating, not one with outstanding performance. Typically when lower VOC is required, there is some sacrifice in performance. Our goal with this new product development is to bridge the performance gap, leapfrogging over existing waterborne alkyd technologies.
Novel Technology
With the above objectives in mind, Polynt has developed a new alkyd backbone to enhance performance in water (Tables 4 and 5). Based on many years of alkyd knowledge and expertise, R&D chemists modified an alkyd backbone to improve alkyd emulsion stability (acid functionality was critical), hardness development (higher-Tg hydrophobic polyols and acids used) and corrosion protection. For improved corrosion resistance, the higher-Tg hydrophobic components were critical, along with the proper choice of surfactants and surfactant levels (use as little as possible while maintaining hot box stability). Many newer surfactants and reactive surfactants are in the marketplace specifically for alkyd emulsions. Also critical for best corrosion resistance was selection of the pigment dispersant in the paint formulation. Last, a process was developed to successfully emulsify the hydrophobic, high-Tg, high-molecular-weight/viscosity needed so that said alkyd could be inverted into water and relatively high solids could be obtained. These initiatives combined led to the performance of a short-oil chain-stopped alkyd in water that is comparable to commercial solventborne alkyds.
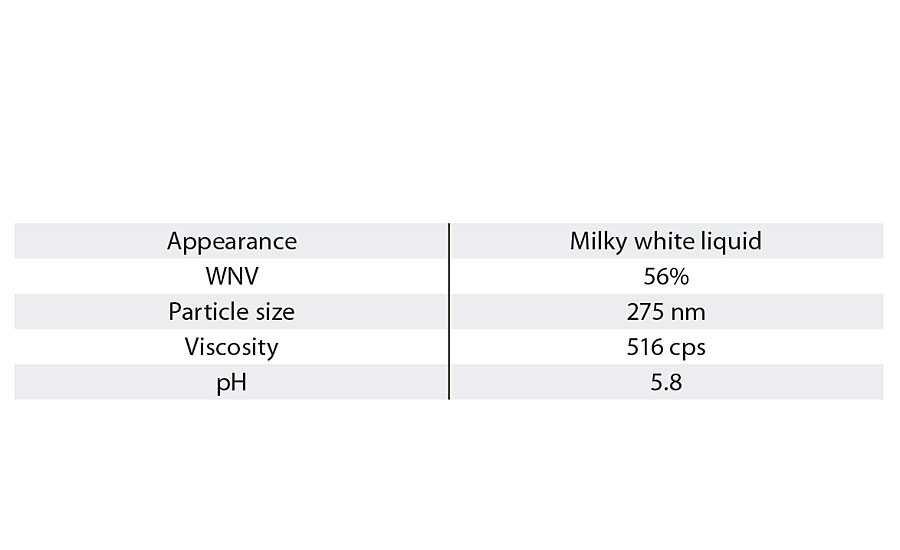
TABLE 4 » Characteristics of waterborne short-oil chain-stopped alkyd emulsion
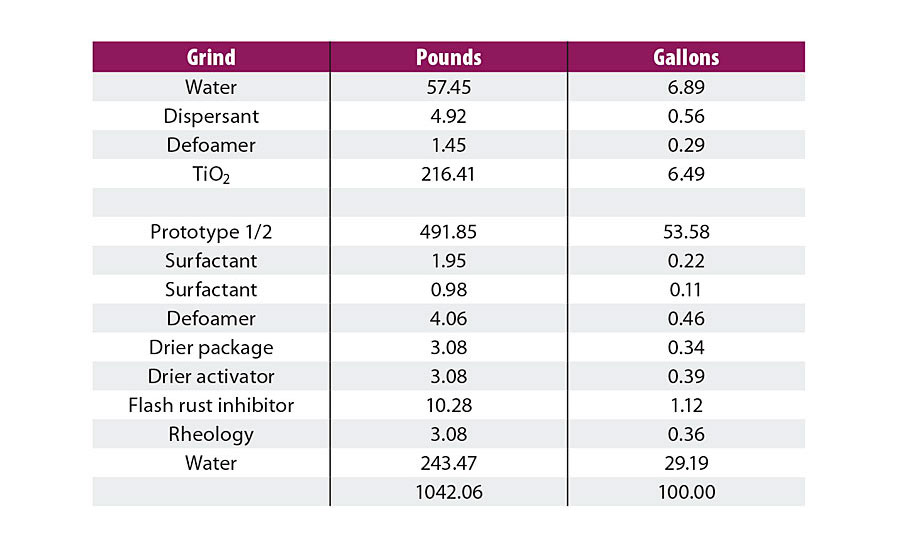
TABLE 5 » Typical white starting-point formulation used for all waterborne alkyds tested
The newly developed DTM short-oil alkyd emulsion was tested for dry times, hardness development, 300 hrs salt spray at both 1.5 and 2.0 mils DFT, and condensing humidity. Through dry was around 6 hrs, better than the competitive alkyd emulsions (Table 6). Koenig hardness after two weeks was 41 secs, showing better hardness development than the competitive alkyd emulsions, but not as hard as the acrylic-modified core shell dispersions. Salt spray performance was outstanding after 300 hrs, and there was no effect on adhesion after 16 hrs condensing humidity (Figure 6). Performance of the developmental DTM short-oil alkyd was comparable to solventborne performance.
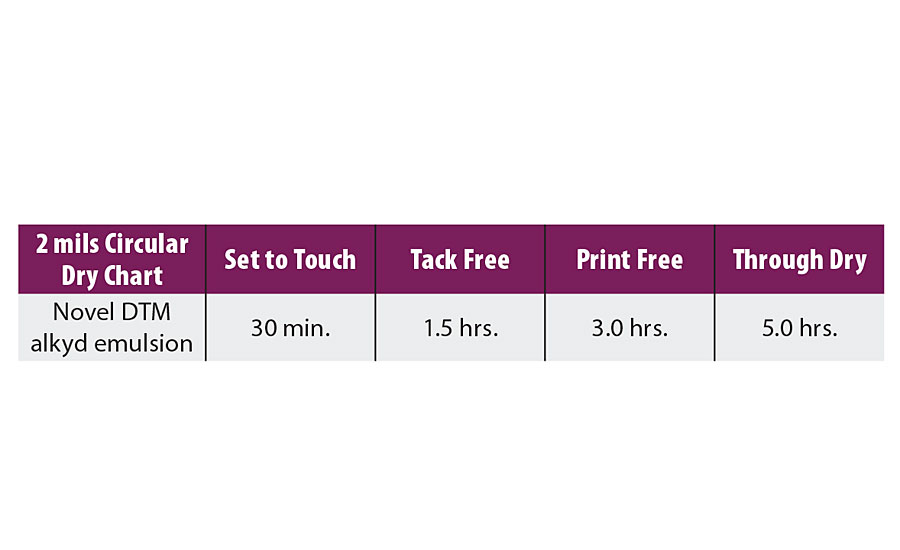
TABLE 6 » Dry time of novel DTM alkyd emulsion
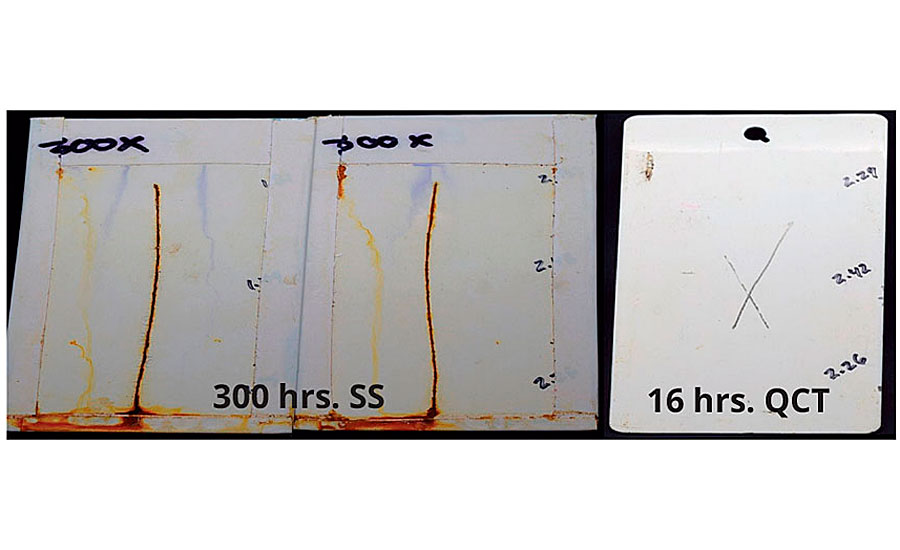
FIGURE 6 » Performance of novel DTM alkyd emulsion
Benchmarking Study
The new DTM alkyd emulsion was tested against the four competitive alkyd emulsions/dispersions as well as a commercial water-reducible alkyd, commercial water alkyd paint, and two commercial, conventional-solids, chain-stopped alkyds. VOC, dry times, 60° gloss and Koenig hardness comparisons are shown in Table 7. Other test results are shown in Figures 7-9 and Table 8.
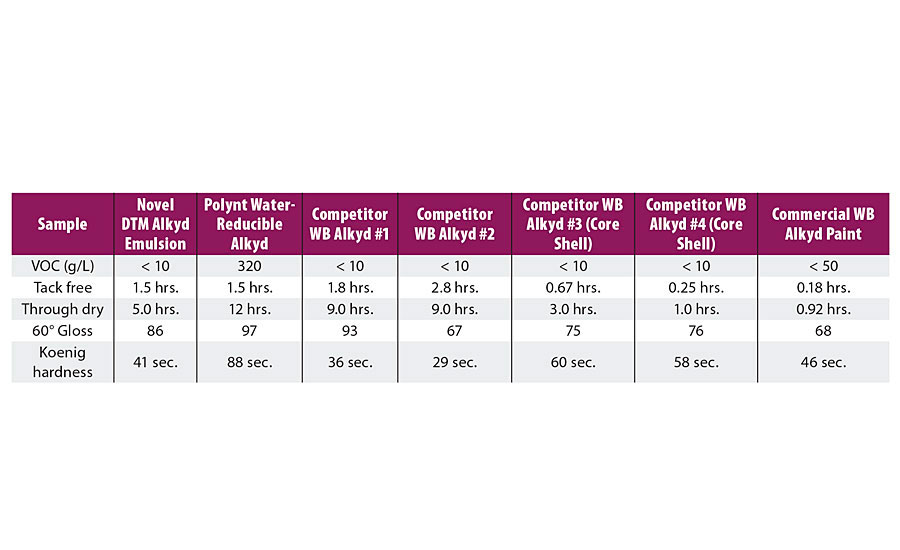
TABLE 7 » Benchmarking data for VOC, dry times, gloss and hardness
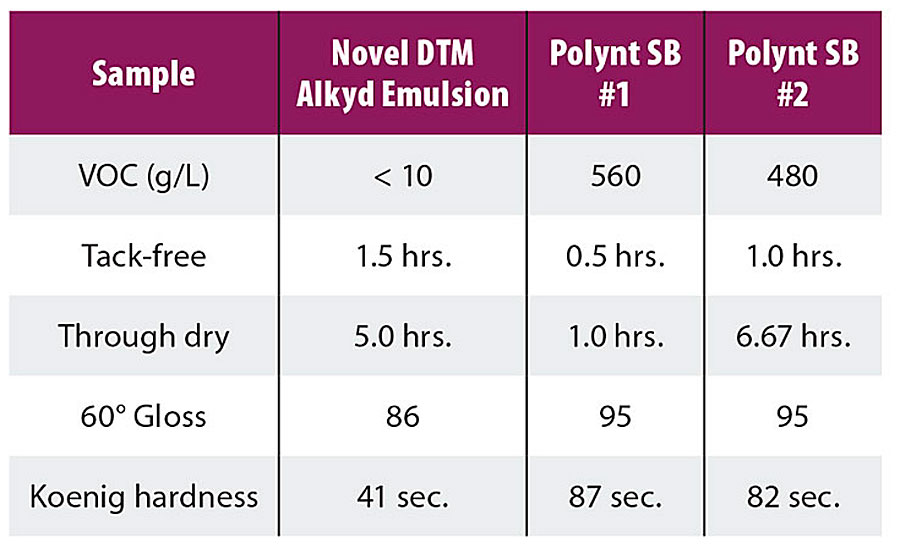
TABLE 8 » Dry time of novel DTM alkyd emulsion versus commercial, conventional-solids, chain-stopped alkyds
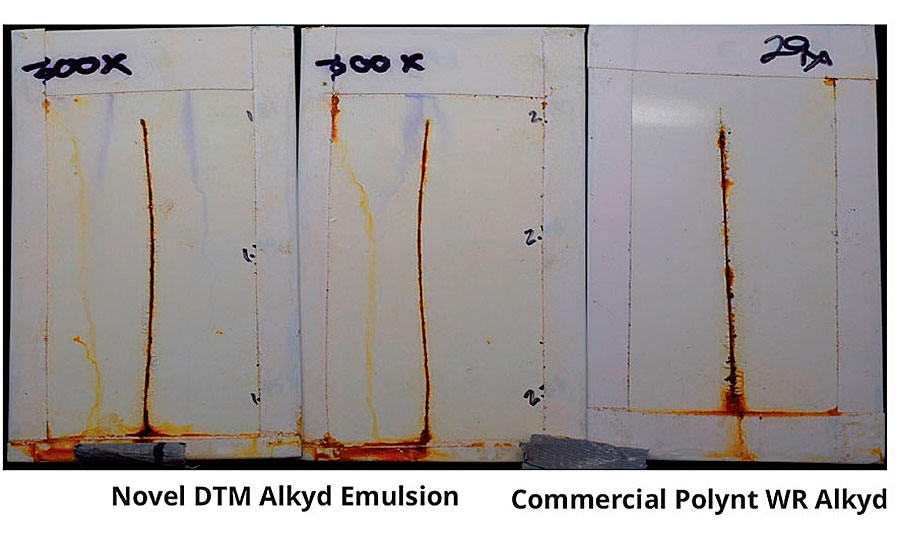
FIGURE 7 » Novel DTM alkyd emulsion versus water-reducible alkyd
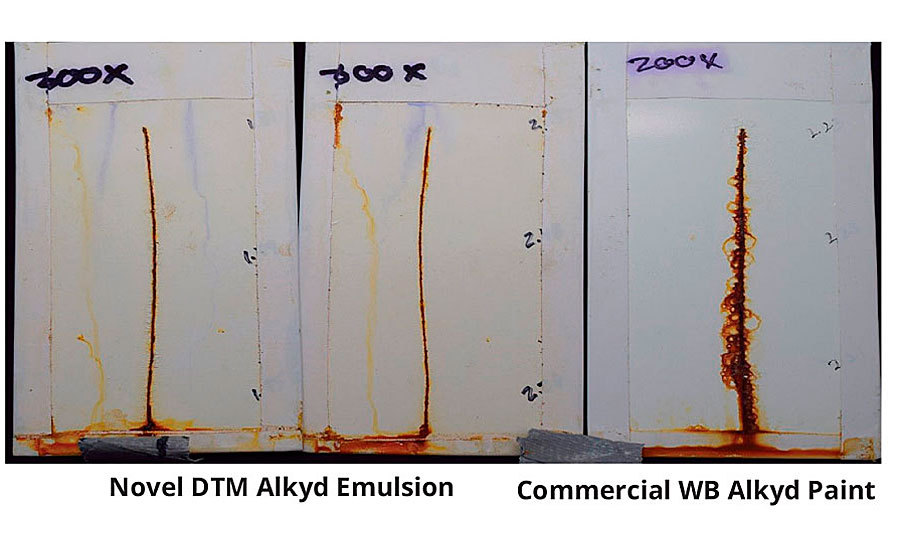
FIGURE 8 » Novel DTM alkyd emulsion versus commercial waterborne alkyd paint
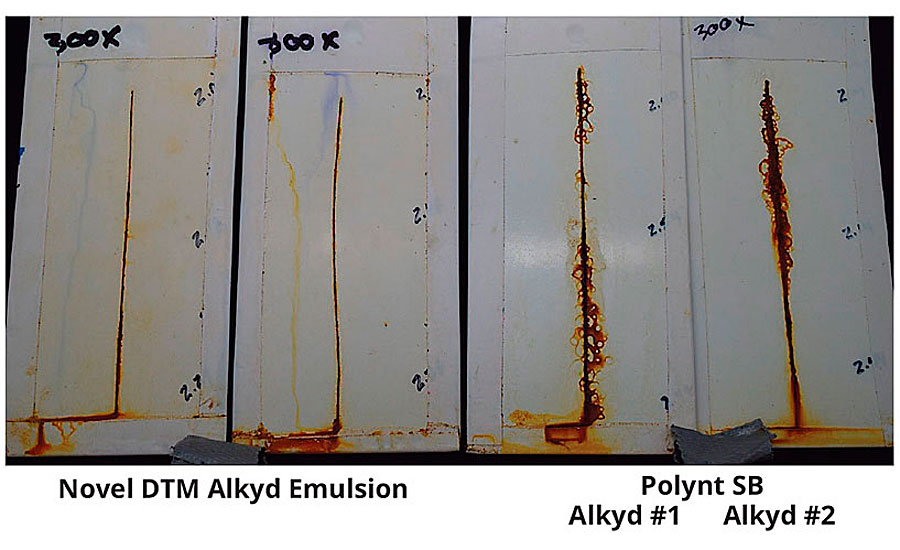
FIGURE 9 » Novel DTM alkyd emulsion versus commercial, conventional-solids, chain-stopped alkyds
Conclusion
The combination of a high-Tg, hydrophobic, high-MW alkyd with the proper surfactants and levels can produce a highly corrosion-resistant DTM alkyd emulsion when formulated with select pigment dispersants. Formulation of this alkyd emulsion into waterborne DTM paint at near-zero VOC can produce coating performance comparable to solventborne, conventional-solids, chain-stopped alkyds. This new DTM alkyd emulsion can close the performance gap between commercial waterborne alkyds and conventional solventborne alkyd technologies with regard to gloss, adhesion, and corrosion and humidity resistance at near-zero VOC.
Reference
1 US Paint & Coatings Industry, 2011-2016 - Kusumgar, Nerlfi, & Growney.
Looking for a reprint of this article?
From high-res PDFs to custom plaques, order your copy today!