Next-Generation Liquid Polybutadiene Polymer

Historically, the majority of coatings were solvent based, but with growing emphasis on reduction of volatile organic compounds (VOCs), such systems are under significant pressure. Where an application still demands the performance of a solvent-based coating, reduction of VOCs while maintaining critical application properties, such as viscosity, has become increasingly important.
The modern coatings formulator now faces the significant challenge of minimizing solvent while achieving an aesthetically acceptable, defect-free film at minimal cost. A common approach is to increase solids content, but the resulting effect is typically an increase in product viscosity, which may lead to difficulty during coating application.
Alkyd surface coatings continue to be one of the most highly consumed types of coatings globally, despite the increasing use of other polymer film formers. The success of alkyd resin systems is a result of their relatively low cost, versatility and familiarity with end users. They can be tailored to meet a variety of end-use requirements through the choice and ratio of reactants and/or modifiers. Producers continue to develop new and improved systems for high-solids formulations to meet increasingly stringent air pollution regulations.
Various alternative approaches may also be used to adjust the final coating formulation in order to lower the viscosity so that less solvent is needed to bring the paint to within the required application viscosity. Liquid polybutadienes (LPBds) are highly reactive liquid hydrocarbon polymers that can be formulated into solvent-free or low-solvent coating formulations. These polymers are similar in many respects to natural drying oils but due to their high level of unsaturation, the cure rate of certain grades is faster than many natural oils and can be accelerated by the use of metal driers. In comparison to natural oils, the LPBd films are typically lighter in color, harder and more chemically resistant. They have proven to be particularly suited to primer coat applications, exhibiting adhesion and excellent corrosion resistance on steel substrates.
Further research into the range of potential properties delivered by incorporating LPBds within solvent-based coatings has been performed. In this study we focus on the benefits delivered through incorporation of a newly developed liquid polybutadiene grade (LPBd-B) in a solvent-based alkyd coating when compared to other commercially available liquid polybutadiene grades. New LPBd-B has a lower molecular weight and higher 1,2 vinyl content than commercial product, LPBd-A.
Results demonstrate how the next-generation LPBd‑B delivers improved compatibility within the resin system, enabling potentially greater formulation changes and even moving closer to a solvent-free system. Our study also shows that it is possible to lower viscosity while simultaneously enhancing the coating’s performance properties.
Compatibility Between Liquid Polybutadiene Polymers and Alkyd Resins
Three common coating long oil alkyd-based resins were assessed; one based on linseed oil at 100% solid content, and two at 70% solids in white spirit (one based on linseed oil and one on soya oil). Blends, prepared at specific ratios, were dispersed for 5 min on a high-speed disperser at 2,000 rpm. The blends were then transferred into glass containers for assessment of storage stability. One lot was left at room temperature, the other was placed in an air oven at 40 °C for 24 hrs. The compatibility between LPBd polymers in alkyd binder systems was assessed, and a visual inspection after 24 hrs and 7 days was conducted. Good compatibility was obtained in all three alkyd resins with both LPBd products.
The following study is mainly focused on work with solvent-based Alkyd Resin 1 (100% long linseed oil). Its compatibility with different LPBd polymers was intensely evaluated. Following this screening, a maximum load of polymer in Alkyd Resin 1 was determined. To complete the assessment, each blend was brushed on foil paper to highlight any potential film defects.
Benefit was observed from new LPBd-B over LPBd-A, with greater compatibility in Alkyd Resin 1. A higher loading in the resin can be achieved with new LPBd-B without adverse effects on the visual aspect of the coatings (Figure 1). Brush out on foil paper showed no film defects in wet or dry state.
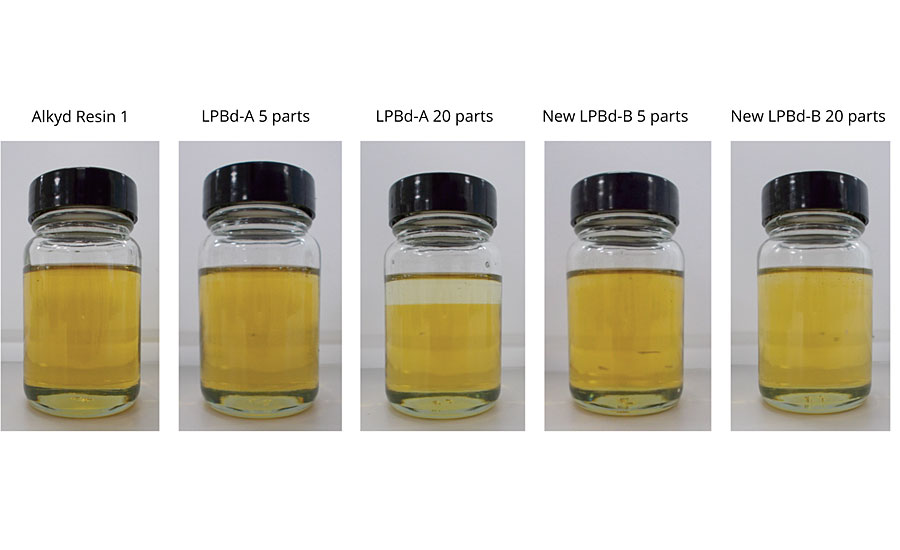
Effect on Rheology
A blend rheology profile was determined on a rheometer (Figure 2). The viscosity of Alkyd Resin 1 decreased as the temperature increased. Similar behavior was obtained when adding either LPBd-A, new LPBd-B or solvent (i.e. white spirit). A blend based on solvent (20 parts) had the greatest diluent effect on the alkyd resin.
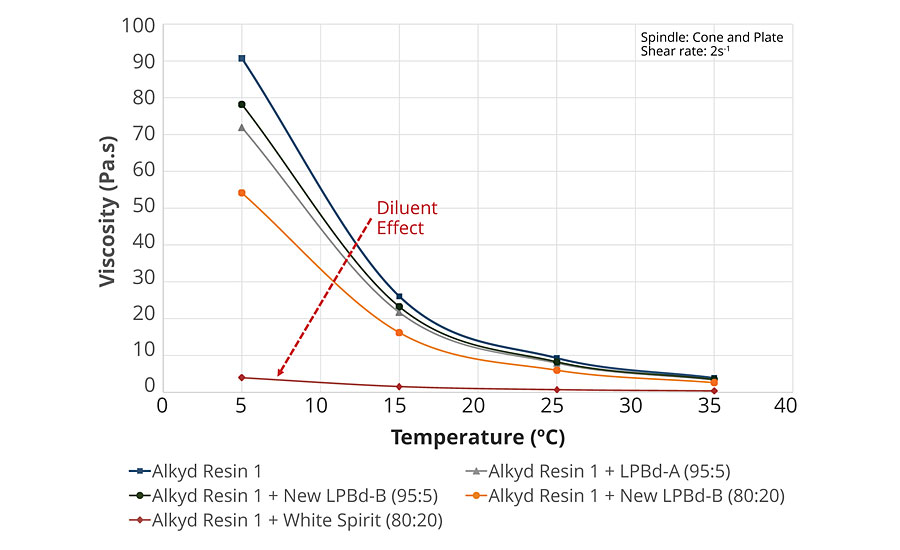
Application Properties in Clear Coatings
To evaluate application benefits, Alkyd Resin 1 was formulated in a clear coating; LPBd-A and new LPBd-B were added at different ratios. Application properties, including drying time, rheology and hardness, were assessed. Additional information was collected with a substrate penetration assessment and a study to move towards a 100% solid content system with lower VOC content.
Drying Time
A series of formulations was prepared to assess the effect of liquid polybutadiene polymers on drying time (Table 1). Alkyd Resin 1 was partly replaced by LPBd‑A or new LPBd-B. Viscosity of each preparation was adjusted by adding white spirit to achieve equivalent viscosity at room temperature.
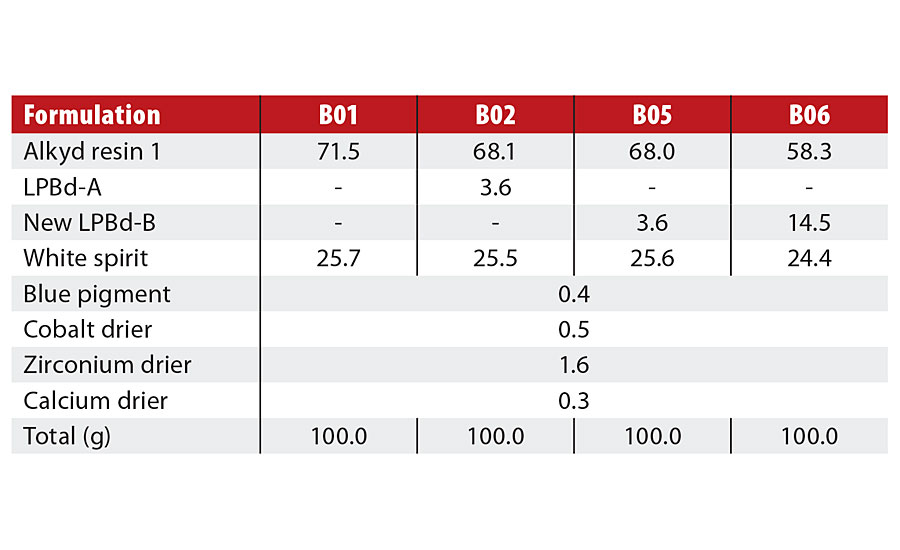
Each formulation was applied on glass panels at 75 µm wet film thickness. The drying time was assessed simultaneously with a linear drying time recorder. The open time and complete through cure were determined by visual assessment of the scratched surfaces of each dried coating (Table 2).
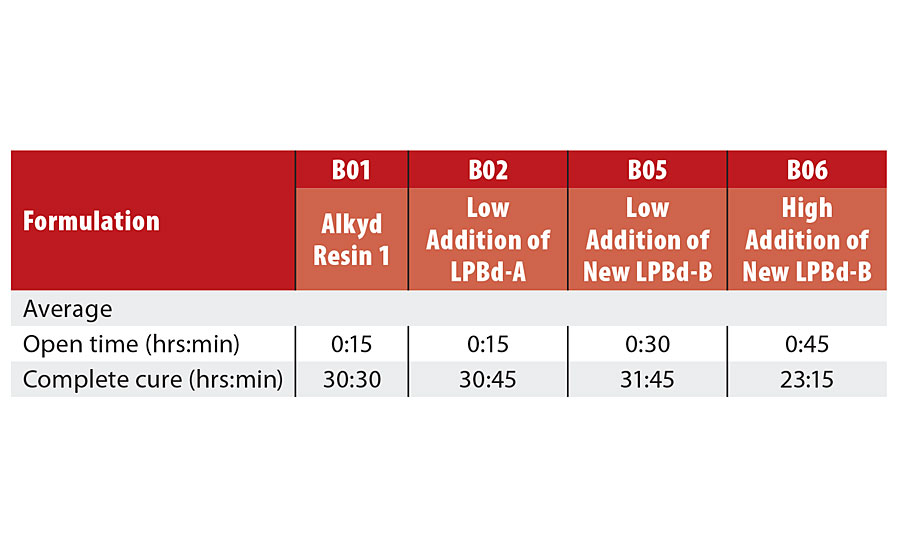
The open time was slightly increased by the addition of the new LPBd-B, while LPBd-A did not show significant impact compared to the control sample, containing only Alkyd Resin 1.
The complete cure was very slightly increased by a low addition of LPBd-A or new LPBd-B compared to the control recipe. Significant differences were observed with high addition of new LPBd-B, giving a shorter complete cure time.
Hardness
To assess hardness, a series of formulations was developed by replacing parts of the Alkyd Resin 1 and parts of white spirit by LPBds. Viscosity was not adjusted, to emphasize the potential benefit of LPBd.
The hardness of the coatings was assessed by a pencil hardness method. 100 µm wet film thickness (wft) was applied on glass panels with a flat applicator. The coatings were allowed to dry 7 days and 14 days prior to testing (Table 3).
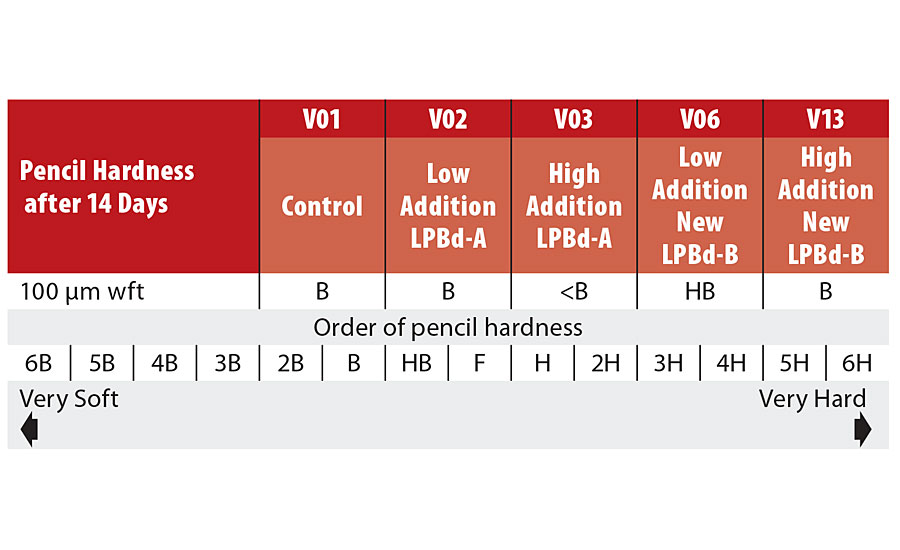
Adding LPBd-A in the clear coating did not present any benefits in pencil hardness. The coating was similar or lower in hardness compared to control (no additive in Alkyd Resin 1). The incorporation of new LPBd-B allowed an increase of pencil hardness at a low-level addition. A higher addition level did not show benefit in hardness properties. It was noticed that a higher addition of LPBd tended to slightly lower the pencil hardness of the clear coating.
Assessment of Penetration into Substrates
In order to assess substrate penetration, oak panels were selected. A series of blends was prepared with the aim of highlighting any additional potential benefits from use of LPBd.
Each blend was transferred to a glass container. Oak panels were immersed for 15 min in the coating solution, then excess coating was removed. Each oak panel was allowed to set at ambient temperature prior to cutting a cross section at 1.5 cm or 3.5 cm depth from the bottom of the panel. The test pieces were sanded, then digital microscopy was used to examine each cross section. Both surface and end grain migration were evaluated. (Figure 3).
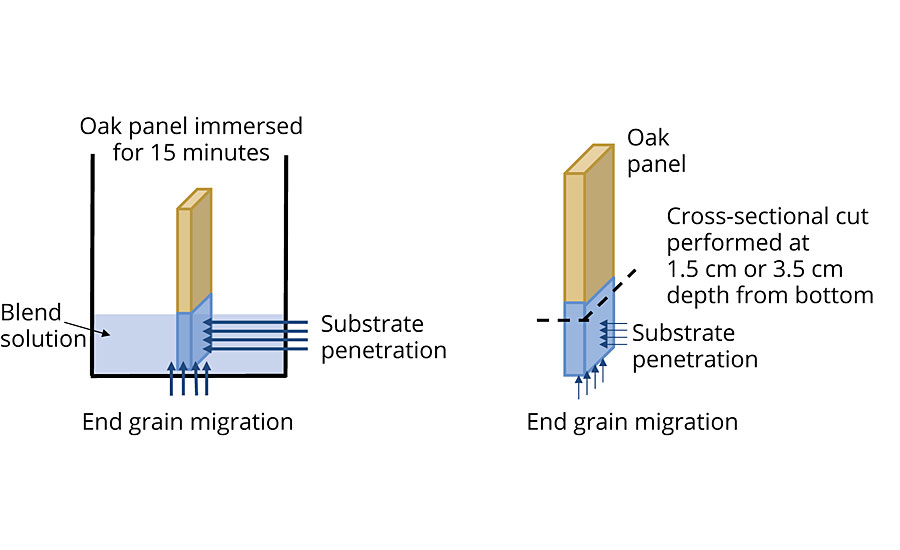
According to the digital microscopy of a cross section at 1.5 cm depth, it was found that surface substrate penetration would mostly occur within the control blend. Adding five parts of LPBd-A into the clear coating allowed better coverage of the wood piece and significantly, complete end-grain migration was observed. There is some evidence that, by adding five parts of new LPBd-B, the end-grain migration was improved further compared to the control formulation. To achieve full coverage, new LPBd-B, required 20 parts addition.
A further cross section at 3.5 cm depth was conducted to identify the behavior of blends more deeply into the grain of the wood. In the control specimen, substrate penetration was observed along with some end-grain migration in limited areas. Addition of LPBd-A at five parts gave a similar profile of wood penetration to the control blend, but no end-grain penetration was noted. Despite giving a lower wood penetration at five parts addition, new LPBd-B gave a similar end-grain migration compared to the control. It was noticed that the end-grain migration was present along the specimen. At 20 parts addition however, more significant wood penetration was observed with new LPBd-B compared to control, with more significant end-grain migration visible along the specimen (Figure 4).
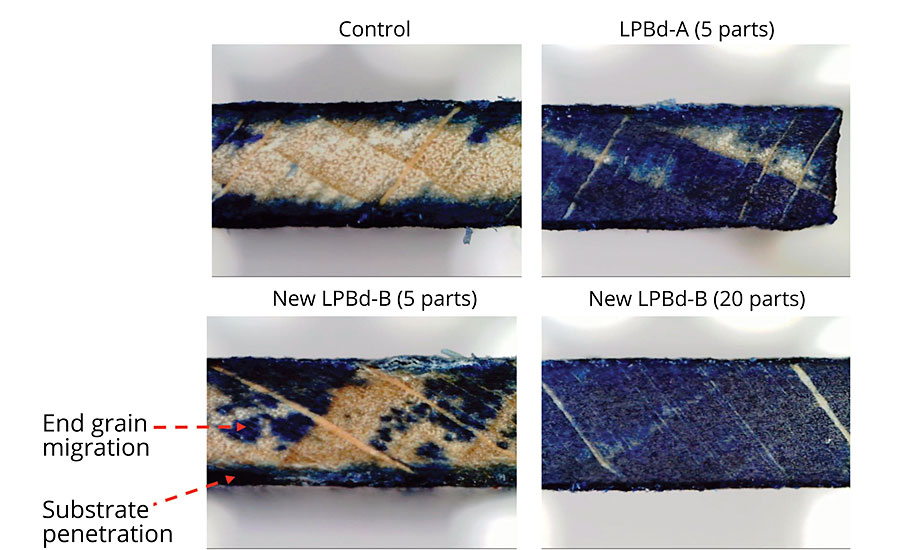
Volatile Organic Compounds (VOCs)
One way to reduce VOCs in a solvent-based coating is to increase the solids content. A series of formulations was developed, replacing the amount of white spirit by LPBd-A, new LPBd-B or Alkyd Resin 1. This moves the recipes towards higher solids content and allowed evaluation of 100%-solids-content systems.
Levels of metal driers and antiskin agent were adjusted and calculated on %w/w on total resin weight. Each formulation was applied on a glass panel with a flat applicator at 50 µm and 100 µm wet film thickness. Coatings were allowed to dry for 24 hrs at room temperature prior to observation.
In order to compare the different systems, a control formulation at 65% solids content was assessed and gave good film forming behavior on glass at 50 µm and 100 µm. By increasing the total solids content with addition of Alkyd Resin 1, a good film was formed at low 50 µm thickness, whereas wrinkling defects were observed at 100 µm. The wrinkling effect would be most likely due to rapid surface drying. An adjustment of metal drier levels in the formulation should eliminate this defect.
Introducing LPBd-A to increase the total solids content of the clear system gave film defects at both thicknesses. This result confirmed the initial outcomes following the compatibility study, i.e. at high loading, LPBd-A cannot be incorporated homogenously. Benefits were clearly noticed with the introduction of new LPBd-B to achieve a higher solids content system. Clear, transparent films were obtained with no visual defects at both thicknesses (50 µm and 100 µm).
Moreover, increasing the solids content had an impact on the viscosity of the clear systems. The diluent effect of LPBd is confirmed with reference to formulations V15 (LPBd-A) and V17 (new LPBd-B). The increase was more significant with the Alkyd Resin 1 (formulation V21), which could lead to application issues associated with the high viscosity.
To determine VOC content in those formulations, GC-MS analysis was performed according to an internal test method. Results and chromatograms from GC-MS analysis clearly demonstrated a drop of VOC in formulations with a higher solids content. Replacing white spirit by LPBd in Alkyd Resin 1 significantly reduced the amount of VOC in the formulation. Limited differences were observed between the resins added to replace the solvent content, i.e. in V15, V17, and V21 (Figure 5).
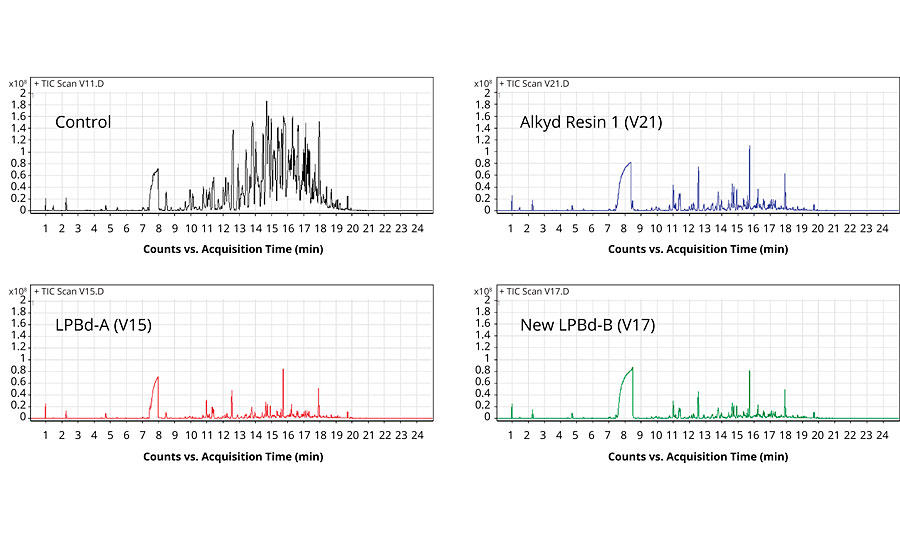
As expected, by increasing the solids content with addition of polymer resins, the total amount of VOC decreased. White spirit is obviously a major contributor to VOC in the formulations tested.
Conclusion and Further Work
This study has confirmed benefits from use of liquid polybutadiene polymers in solvent-based coatings with additional enhancements seen from a new liquid polybutadiene. Results demonstrate that it is possible to reduce the VOC content of a solvent alkyd coating by increasing the solids content using additions of liquid polybutadiene. This 100%-solids-content liquid polymer type suggests a move closer to 100% solids content is achievable. It was additionally shown that incorporation of a new LPBd increased wood penetration, end-grain penetration in particular. Other advantages noted were longer open time during drying of clear systems, coupled with a potential for faster through cure. The ability to harden the dry film was also possible by selecting the appropriate addition level of liquid polybutadiene.
Application properties were enhanced by use of a newly developed liquid polybutadiene polymer, without adverse effects on other critical properties such as gloss level, color or outdoor exposure.
We have demonstrated the benefits of a development liquid polybutadiene product in one specific binder system used in solvent-based coatings. Further work is planned to explore the use in other binder systems and evaluate performance on different critical substrates including oily, metal and poorly prepared surfaces.
Looking for a reprint of this article?
From high-res PDFs to custom plaques, order your copy today!