The Next Generation of Zinc-Rich Coatings
Improved Versatility and Performance via Self-Healing Functionality

First demonstrated in polymerized resins via a ring opening metathesis polymerization (ROMP)-based system by White et al.,1 self-healing functionality utilizing microcapsules has been demonstrated to improve the performance of a range of protective coatings.2-4 In these coatings applications, a healing agent is released from microcapsules embedded in the coating film after damage. Once in the site of damage, the generally hydrophobic healing agent renders the damage site more hydrophobic, thereby limiting further moisture ingress, and upon curing, seals the edges of the damage, thus maintaining the coating’s adhesion to the substrate and limiting undercutting. The effect of designing microcapsule-based self-healing functionality into protective coatings is that the lifetime of traditional coatings and their underlying substrates (Figure 1) can be extended in instances where mechanical failure of the coating is the dominant failure mechanism. In these cases, damage to the coating is arrested by the healing functionality, thereby decreasing the rate of onset of the level of failure that might require coating maintenance, repaint or asset replacement (Figure 2). For owners and operators maintaining assets in the most corrosive environments, the life extension afforded by self-healing functionality presents a compelling value proposition due to the potential for longer coating maintenance cycles and less-frequent downtime. Together, these improvements could contribute to a significant decrease in operational costs over the life of the asset.
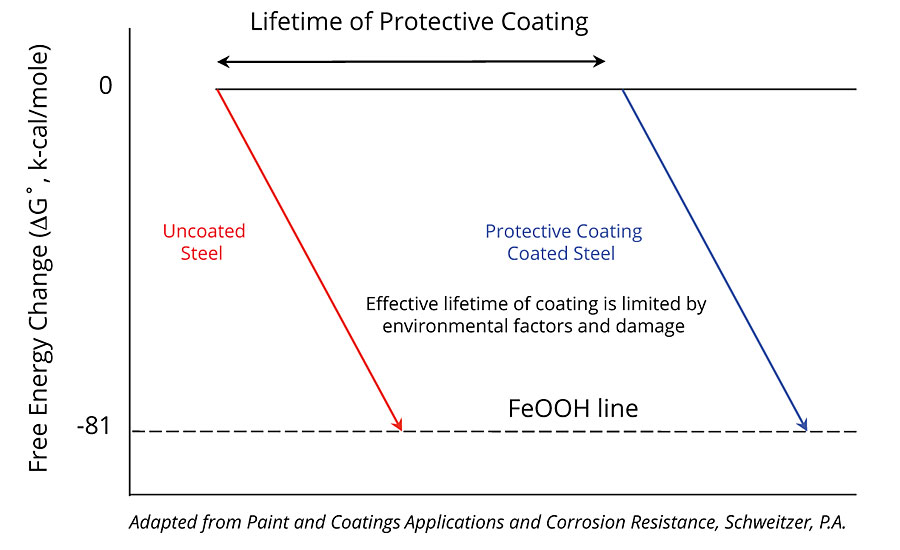
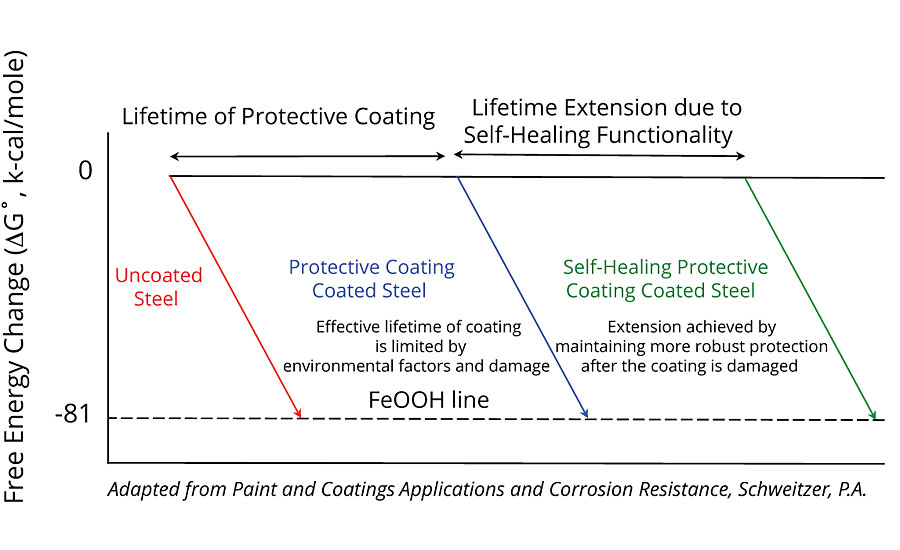
Since zinc-rich primers are used extensively in the most corrosive environments, they represent a natural target for improvement via self-healing functionality. Zinc-rich coatings are typically used for the protection of steel substrates via sacrificial oxidation. Depending on the specifications of the coating, various sizes and shapes of zinc particles have been used as electrochemically active pigments, and organic binders have included epoxies, polyurethanes and alkyd resins, while inorganic binders are typically alkyl silicates capable of polycondensation in the presence of moisture.6 The pigment volume concentration (PVC) of zinc-rich coatings is generally greater than the critical pigment volume concentration; a characteristic that is essential in ensuring a high degree of electrical connectivity between zinc particles and between the zinc particles and the underlying substrate.
In this article, we report on the evaluation of microcapsule-based self-healing functionality in a range of organic zinc-rich primers with a view towards assessing potential synergies between the maintenance of the coating’s adhesion to the substrate after damage afforded by the incorporation of the self-healing additive, and the protection due to the sacrificial oxidation of zinc particles incorporated into the coating.
Design of Coating Systems and Electrochemical Characterization
To assess the efficacy of self-healing functionality incorporated into zinc-rich primers for the corrosion protection of steel substrates, we started our evaluation by employing electrochemical characterization techniques to compare a commercially available SSPC Paint 20, Level 2 type coating (Figure 3a), with a version of the same coating incorporating AMPARMOR™ 2000, a self-healing additive based on the microencapsulation of an epoxy-based formulation (Figure 3b). The coatings were then applied to cold-rolled steel (CRS) substrates via a conventional spray application process at a dry film thickness (DFT) of 75 microns as per the specifications of the commercial coating. After allowing 7 days for curing, the coated substrates were then scribed using a 186-micron scribe tool and allowed 24 hrs to equilibrate at room temperature prior to electrochemical characterization. A set of un-scribed substrates was also evaluated.
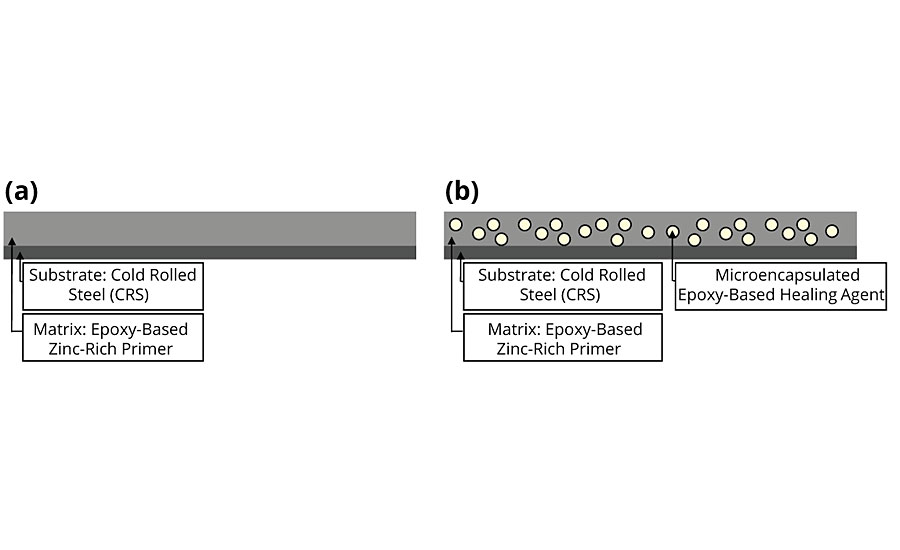
Electrochemical characterization was performed using a three-electrode electrochemical set-up in 3 wt.% NaCl solution and a VMP3 multichannel potentiostat (Biologic, USA). A glass cylinder was affixed to the coated metal surface to be evaluated by a rubber O-ring clamped to the substrate and filled with 3 wt.% NaCl solution. The reference electrode (standard silver/silver chloride electrode) and counter electrode (platinum wire) were then inserted into the electrolyte solution. The working electrode was connected to the sample (coated metal substrate) to be tested. The total tested area was 7 cm2. The open circuit potential (OCP) was measured for 15 min to ensure that the system was stable and at equilibrium before making impedance and polarization measurements. Impedance measurements were carried out at OCP by applying a 10 mV sinusoidal voltage and varying the frequency from 0.1 Hz to 100 kHz. Low-frequency impedance (log|Z|0.1Hz) was monitored as a function of salt fog exposure. Polarization measurements were recorded at OCP by scanning the electrical potential from -1.0 V to 1.0 V at a scan rate of 0.166 mV/s.
The low-frequency impedance results for the un-scribed control and the version incorporating the self-healing additive are shown in Figure 4a. Both samples exhibited a decrease in impedance with initial salt fog exposure due to the penetration of electrolyte through pores in the coating. As the exposure continued, the impedance exhibited an upward trend, presumably due to improved barrier properties afforded by zinc oxides and hydroxides formed as a result of oxidation of the zinc particles present in both formulations. When both coated substrates were scribed using a 186-mm scribe tool, the impedance measured prior to salt fog exposure (t = 0) was lower relative to the un-scribed panels due to the exposure of the substrate. However, the impedance for the sample containing the self-healing additive was initially higher due to the formation of a barrier at the site of damage. Furthermore, while the control exhibited a rapid initial decrease in impedance due to additional electrolyte ingress at the scribe, such ingress was mitigated for the self-healing formulation, which exhibited no decline in impedance with salt fog exposure (Figure 4b).
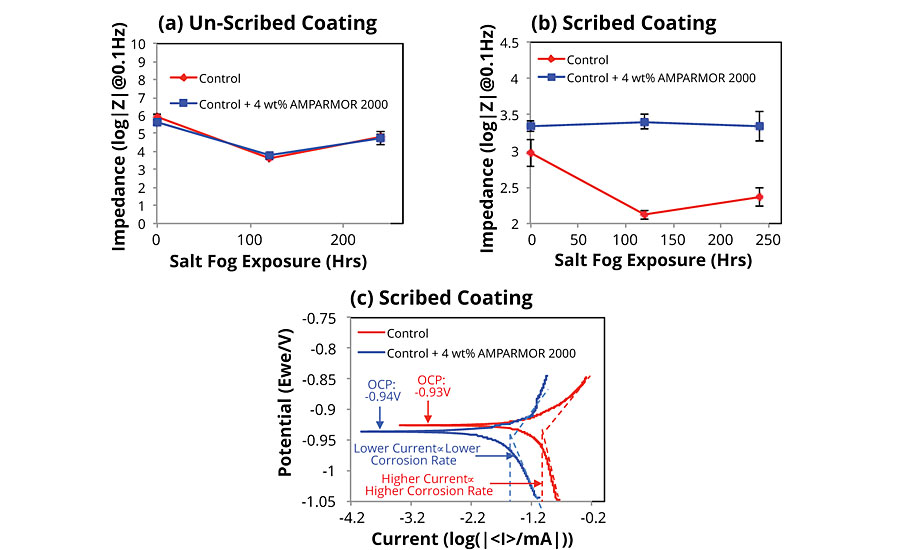
In addition to making the electrochemical impedance measurements discussed above, we performed linear polarization measurements on a separate set of scribed panels prepared identically to those used for the impedance measurements discussed above. Open circuit potentials of -0.93V and -0.94V were measured for the control and self-healing zinc-rich coatings respectively, relative to the standard silver/silver chloride electrode. Both values were noted as closer to the corrosion potential of zinc (-0.98V to -1.03V) and much lower than the corrosion potential of steel (-0.6V to -0.7V), suggesting that the underlying steel substrate was protected by the sacrificial oxidation of zinc in both the control and self-healing coating formulations. Also of note, was the observation that the oxidation rate of zinc in the self-healing coating was found to be four times slower relative to the control coating as determined by Tafel extrapolations from their corresponding polarization curves. The slower oxidation rate is likely due to a decline in the oxidation of zinc particles at the site of damage due to a minimization of electrolyte ingress. The control of the ingress of electrolyte at the site of damage has two important implications for the design of improved zinc-rich primers leveraging self-healing functionality. First, less zinc may be needed to provide sacrificial protection at the site of damage. Second, since less zinc is oxidized at the site of damage, the availability of and therefore the protection afforded by the un-oxidized zinc may be extendable over a longer duration.
Accelerated Corrosion Testing via Salt Fog Exposure
To assess whether the improvement in corrosion resistance observed via the electrochemical testing discussed would translate into improved performance in a typical accelerated corrosion test, we evaluated CRS panels coated with control and self-healing zinc-rich primer formulations. One set of CRS panels was coated using a conventional gravity-feed gun as was done for the electrochemical testing, while a second set was coated using an airless spray gun (Graco Proshot HD Cordless Airless Sprayer, 517 tip, 0.017-in. opening) to elucidate the effect of higher pressures associated with the application of such a highly pigmented coating formulation on the performance of the self-healing additive incorporated into the self-healing coating formulation. After curing for 7 days at room temperature, the panels were scribed, allowed to equilibrate at room temperature for 24 hrs prior to exposure to ASTM B117 conditions. This initial sample set comparing the primer formulations was tested out to 500 hrs.
The adhesion loss results for the panels prepared via conventional and airless spray are shown in Figures 5 and 6 respectively. For both application methods, the performance of the self-healing zinc-rich primer comprised of the same commercially available SSPC Paint 20, Level 2 type coating discussed above and post-added 2.5 wt.% of AMPARMOR 2000 microcapsules was evaluated relative to the commercially available control excluding the capsules. For both control and self-healing formulations, adhesion loss of the coating was evaluated at scribe widths of 186 μm and 500 μm. After a total of 500 hrs of exposure, all the samples exhibited some adhesion loss and visible corrosion (Figures 5a-c and 6a-c). Regardless, however, of the coating application method (conventional vs. airless) the self-healing samples incorporating 2.5 wt.% of AMPARMOR 2000 exhibited significantly less adhesion loss and visible creep around the scribes. Further, no significant difference in the improvement in performance due to the self-healing additive was observed between samples coated via conventional and airless application equipment, indicating that the increased pressure associated with airless application did not rupture the capsules, thereby compromising the self-healing performance.
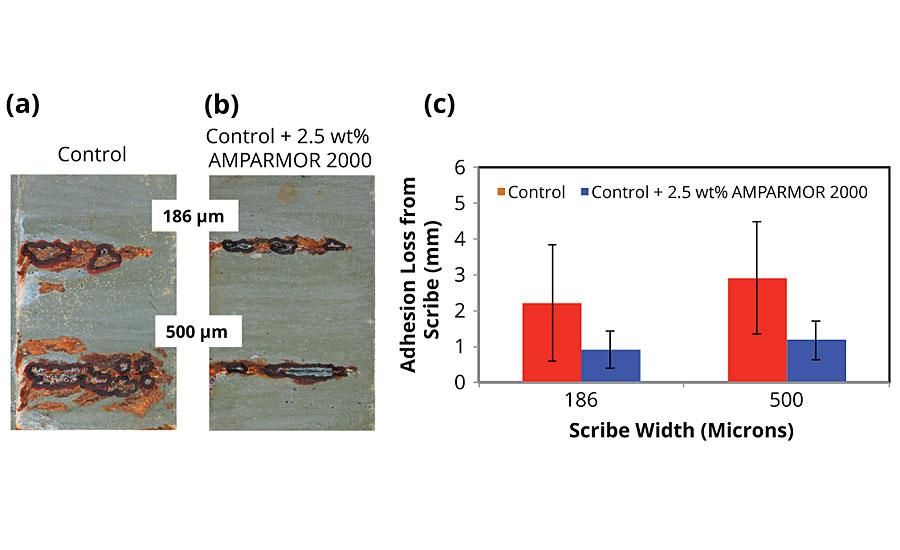
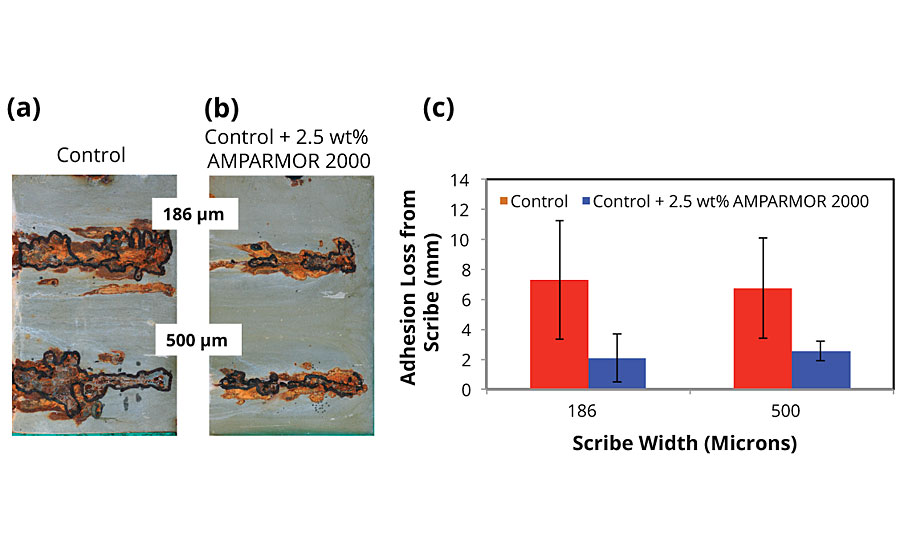
Multi-Coat Systems
Our study was then extended to two-coat systems comprised of a zinc-rich primer layer and an epoxy-polyamide build coat. The control system did not contain any self-healing additive (Figure 7a), while the self-healing system incorporated AMPARMOR 2000 microcapsules only in the zinc-rich layer (Figure 7b).
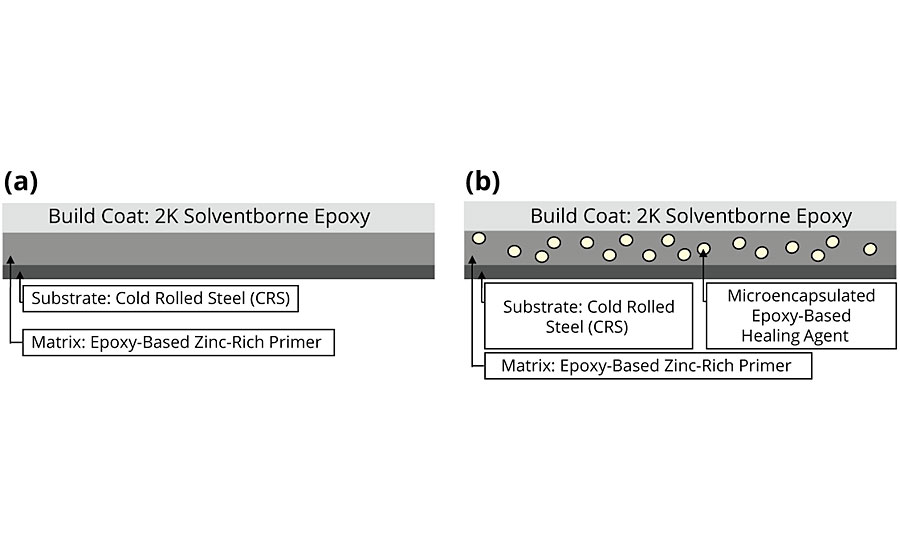
A summary of the results obtained for the comparison between the two-coat control and self-healing systems on CRS is provided in Figure 8. All coating formulations for the control and self-healing systems were applied via conventional spray, and the panels were scribed using 156-μm and 500-μm scribe tools prior to salt fog exposure. Regardless of the scribe width, after 1,000 hrs of salt fog exposure (ASTM B117), the performance improvement for the coating system incorporating the self-healing additive was significant. While the control coating exhibited nearly 8 mm of adhesion loss around the scribes, the self-healing system, which contained 4 wt.% of AMPARMOR 2000 microcapsules in the zinc-rich primer, exhibited a 75% decrease in adhesion loss at roughly 2 mm.
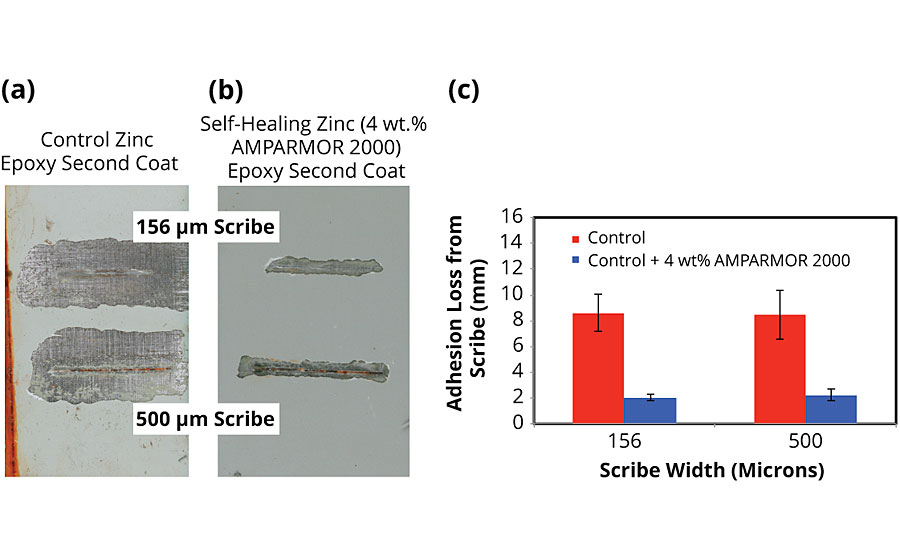
Similar performance improvements were observed for identical coating systems applied on blasted steel substrates (SSPC-SP10). Owing to improved adhesion as a result of the rougher 2.5 mil profile of the SSPC-SP10 substrate, the blasted steel panels were exposed to ASTM B117 conditions for 2,000 hrs. While the control exhibited a maximum adhesion loss of up to 16 mm around the 500-micron scribe, the self-healing system exhibited a decrease in adhesion loss of 87.5% to less than 2 mm around scribe damage of the same size (Figure 9).
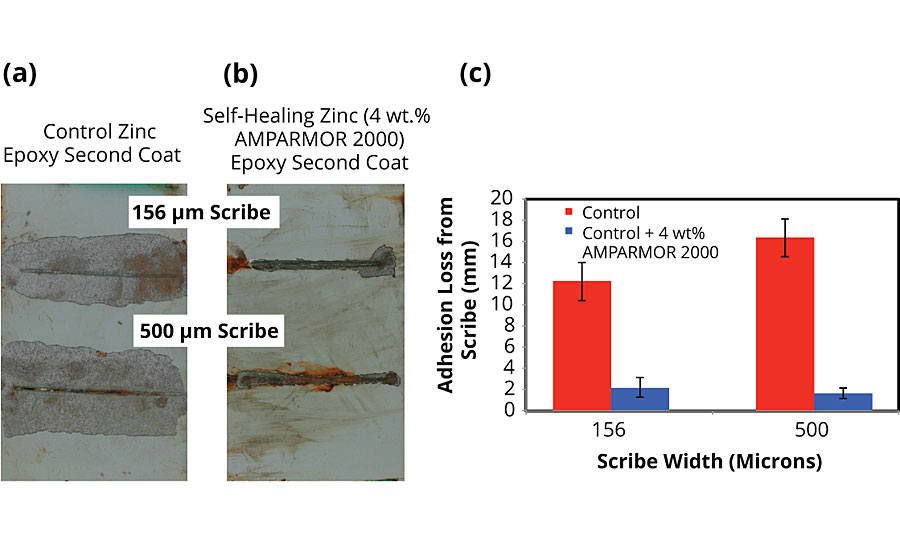
Conclusions
Key takeaways of our evaluation of AMPARMOR 2000 as additives for improved zinc-based protective coating systems include the following:
- · The incorporation of these self-healing additives results in improved adhesion maintenance and corrosion resistance in single-coat and multi-coat organic zinc-based systems.
- · The performance improvement observed appears to be due to the maintenance of adhesion of the coating system after damage, leading to less moisture ingress and germane adhesion loss and corrosion creep. Furthermore, it appears that because the polymerized healing agent contributes to passivation and protection at the site of damage, the zinc present in the system is oxidized at a lower rate, presumably extending the sacrificial protection capability of the system over a longer period of time.
- · The incorporation of the self-healing additives at a loading of up to 4 wt.% had no effect on the open circuit potential suggesting that the connectivity of the zinc particles to each other and to the substrate was not affected by the presence of the self-healing additives.
- · With the incorporation of AMPARMOR 2000 into the zinc-rich primer, excellent adhesion maintenance and corrosion resistance was observed even on low-profile substrates such as lightly abraded CRS. As such, these self-healing zinc formulations can be expected to exhibit superior performance in field maintenance conditions where surface preparation may be at SSPC-SP3 or worse thereby significantly improving the versatility of protective coating systems utilizing epoxy zinc-rich primers.
- · Beyond the work described in detail here, the incorporation of AMPARMOR 2000 into zinc-rich primers has consistently led to improvement in adhesion maintenance and corrosion resistance for a broad range of coating systems containing organic zinc-rich primers. For the range of multi-coat systems incorporating zinc-rich primers we have evaluated, an average corrosion rating improvement of 400% was observed (Figure 10).
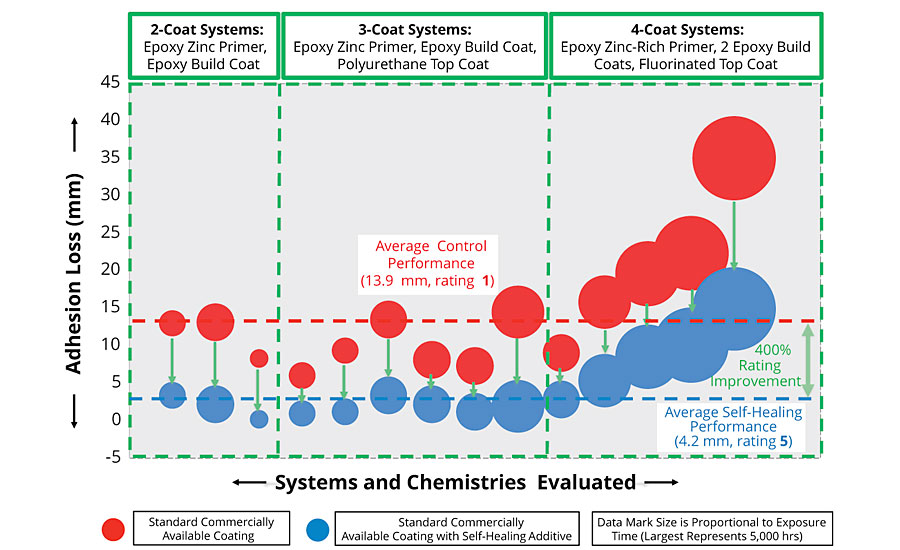
References
1 White, S.R.; Sottos, N.R.; Geubelle, P.H.; Moore, J.S.; Kessler, M.R.; Sriram, S.R.; Brown, E.N.; Viswanathan, S. Autonomic Healing of Polymer Composites, Nature, 2001, 409, 794-797.
2 Wilson, G.O.; Andersson, H.M. Self-Healing Systems for High-Performance Coatings, Paint and Coatings Industry, May, 2012.
3 Wilson, G.O.; Ebbert, B.R.; Andersson, H.M. Improved Corrosion Resistance in Powder Coatings via Microencapsulated Self-Healing Agents, Paint and Coatings Industry, March, 2017.
4 Wilson, G.O.; Andersson, H.M. Improved Protective Coatings via Self-Healing Functionality, Asia Pacific Coatings Journal, 2018, February Issue, 26-18.
5 Paint and Coatings, Applications and Corrosion Resistance; Schweitzer, P A, Ed; CRC Press, Taylor & Francis Group, Boca Raton, 2006.
6 Bierwagen, G.; Allahar, K.; Hinderliter, B.; Jung, H. Zn-rich Coatings Revisited. 2007.
Looking for a reprint of this article?
From high-res PDFs to custom plaques, order your copy today!