The Next Generation of Coil Coating

courtesy of DuPont

Shanghai Stadium’s metal exterior protected by PVF coating.

Aluminum roof protected by DuPont Tedlar PVF film on a coastal hotel in South Carolina.



The excellent properties of polyvinylidene fluoride (PVDF) are well understood in the coatings industry and with users of painted metal. During the current PVDF shortages, coating producers have turned to FEVE, SMP and other resin systems that have also long held market position. Each chemistry has its own strengths and weaknesses that translate to coating properties for the end user. Another viable coil coating base chemistry is polyvinyl fluoride (PVF). PVF may be less known in the coating space, but has a long history in exterior metal protection, as well as a range of other applications. It is a remarkable material with outstanding flexibility, chemical resistance and durability; proven superior in many demanding applications where protection and long-lasting aesthetics are required despite environmental stressors such as salt spray, humidity, rain, intense sunlight, chemical exposure and corrosive elements.
PVF is manufactured by DuPont, the company that invented all fluoropolymers. DuPont™ Tedlar® PVF film has a long history in exterior applications, with nearly half a century of proven performance in harsh environments. PVF coatings have demonstrated similar performance advantages as film and are used in high-value commercial projects globally as a superior alternative for premium coatings that protect and maintain a lasting new look in demanding outdoor environments. Tedlar PVF has no supply constraints and is manufactured in the US.
This polymeric material is chemically like polyethylene, but with one hydrogen atom substituted with a fluorine atom at each repeat unit (Figure 1). The remarkable strength of the carbon-fluorine bond, arising from the high electronegativity of the fluorine atom and its tendency to draw electrons and tighten the surrounding atomic bonds, makes fluoropolymers such as PVF extremely inert.
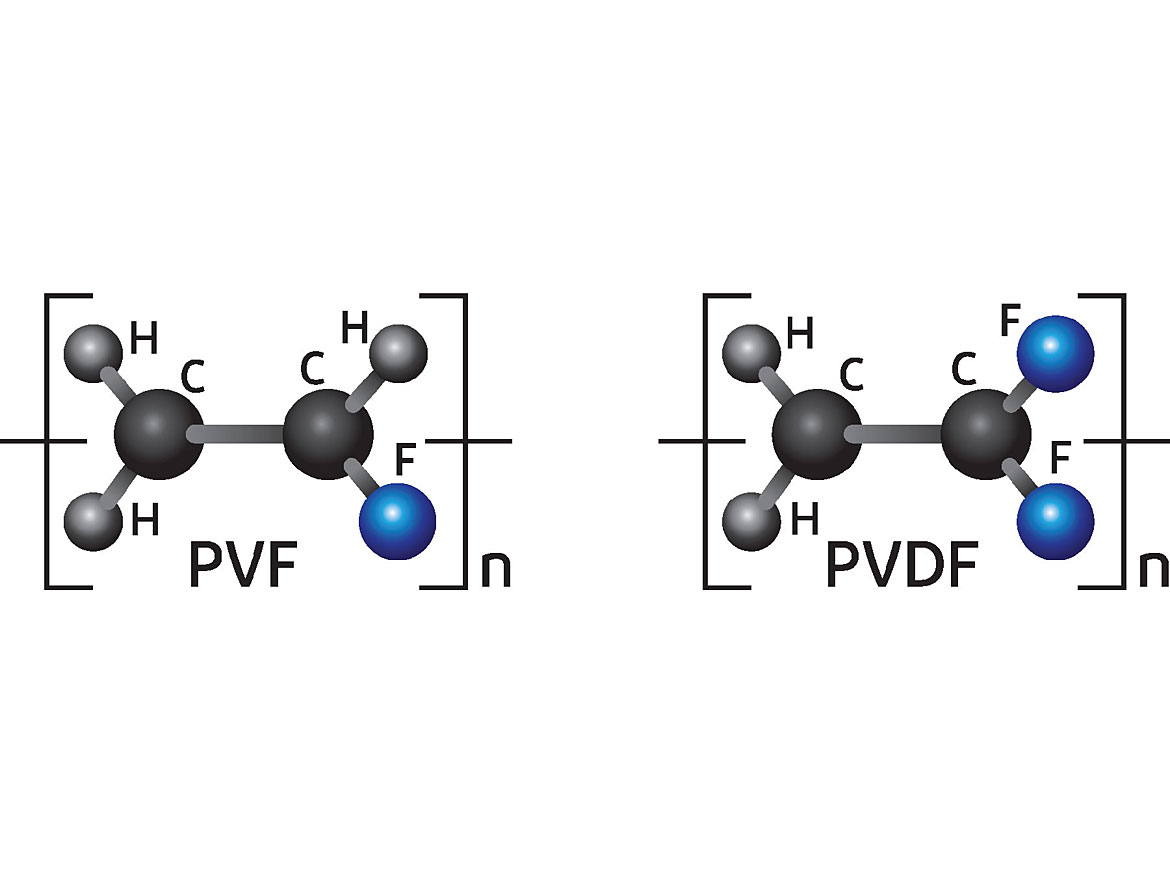
Among the various classes of fluoropolymer, PVF is unique in that the benefits gained by the incorporation of fluorine do not come at the expense of mechanical performance. In fact, the semi-crystalline nature of PVF films provides a favorable combination of strength and ductility. When laminated to a substrate such as metal, it is ideal for applications requiring either hot or cold forming post-lamination, such as roofing, since a PVF-based film or coating can sustain strain and aggressive bends without cracking or compromising integrity on bent areas.
To achieve a similar degree of formability, other fluorinated materials such as PVDF require additives to reduce crystallinity,1 which may penalize their chemical resistance or performance outdoors. Typical PVDF coil coating paints contain acrylics, often based on polymethyl methacrylate (PMMA). Since acrylics are thermodynamically miscible with PVDF, the incorporation of acrylics alters the crystallinity of the polymer. As acrylic is added to PVDF, the crystalline PVDF domains decrease in concentration, enabling more plastic deformation before fracture. However, if too much acrylic is added, the formability of the materials is decreased due to the fundamentally brittle nature of PMMA. An optimum ratio of PVDF and PMMA is 70:30, since this composition provides the maximum ductility.1-3 While small additions of acrylic to fluoropolymers can have some beneficial impact on synthesis or adhesion, too much acrylic will decrease chemical resistance and UV stability.3 PVF does not require any acrylic to achieve formability — only small amounts are sometimes added to coatings for achieving durable adhesion. PVF films are typically made without any acrylic, so the maximum chemical resistance, flexibility and weatherability are achieved.
Owing to superior durability outdoors, PVF products are prime candidates for applications that demand the longest lifetimes in the harshest conditions without cracking, fading or staining. PVF films have been extensively used in architectural applications such as siding, roofing and facades. It has demonstrated color fastness and retention of surface aesthetic in these applications over decades around the globe.4,5
In harsh environments where other materials have failed, such as in tight bending on metal roofing ridges, metal siding installed in close proximity to ocean, and interiors and exteriors of corrosive chemical handling facilities, PVF has demonstrated outstanding resilience. Relative to premium coatings such as SMP, PVDF and FEVE, metal products protected with PVF films generally offer longer warranties and no geographic limitations. In fact, in side-by-side weathering tests of PVF films and common coating materials, such as PVDF and acrylic, PVF has generally exhibited better color stability and retention of surface appearance (Figure 2).6
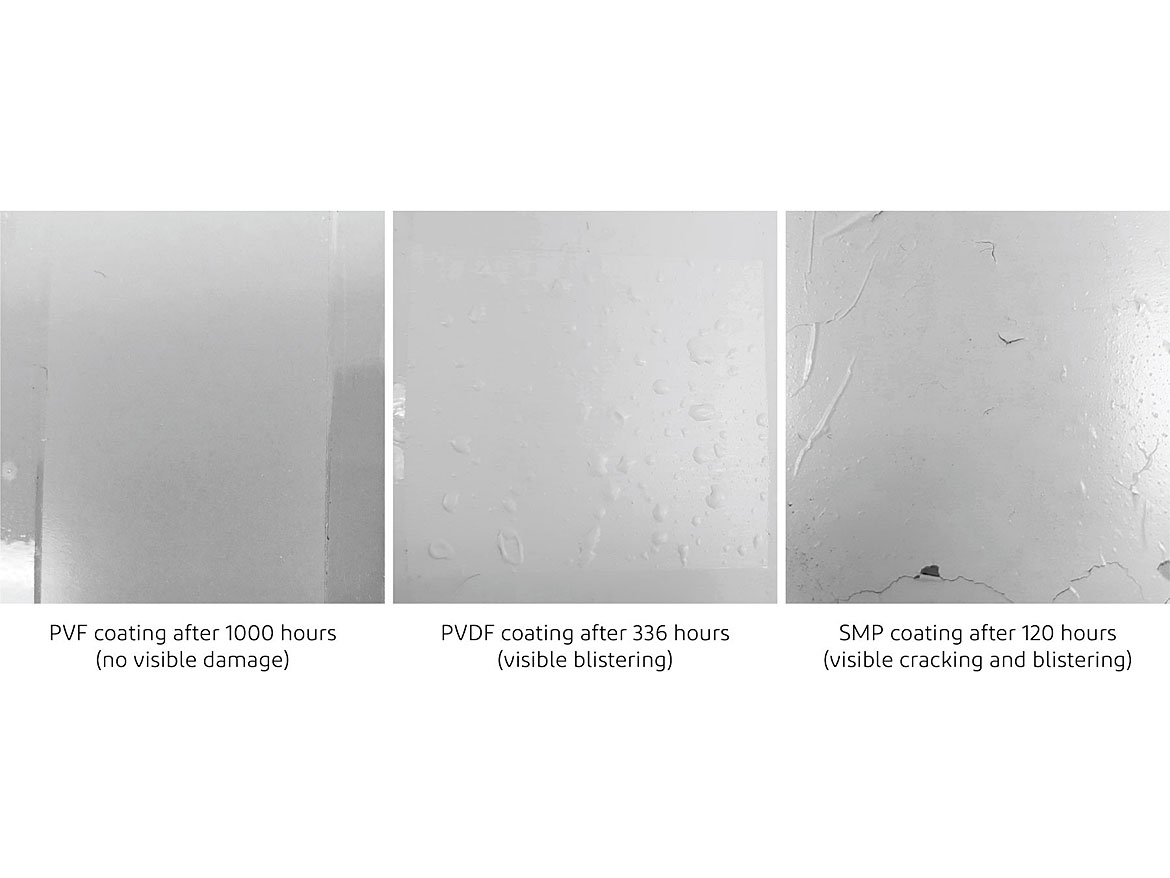
Beyond building and construction, PVF films have also set the standard for performance and reliability in several other outdoor applications. For example, PVF has dominated the premium product line of environmental barrier films for solar panel backsheets for decades. Whereas other polymers may severely discolor (polyester) or crack (PVDF, polyester) well short of expected solar panel service lifetimes, PVF films demonstrate decades of proven reliability free of defects like cracks, blisters or stains.7-8 PVF has also been extensively used in the aircraft industry due to flammability performance and light-weighting. The durability, chemical resistance and cleanability of the polymer have made it the choice material for premium wallcovering, and graphics and signage protection.
Like PVF films, PVF coatings offer similar performance advantages over other materials in the premium coating line, such as silicone-modified polyester (SMP), PVDF and FEVE. Unlike films, PVF coatings have additional color and aesthetic flexibility, and generally include some acrylic to optimize adhesion to a variety of primers without substantially compromising chemical resistance and formability. At the heart of the materials is time-tested PVF resin. When combined with pigments designed for outdoor applications, PVF coatings will exhibit excellent retention of aesthetic and functional performance over decades of service in the harshest environments. PVF technology is the basis of the next generation of protective metal coatings, meeting the needs of demanding environments with best-in-class aesthetic and protective functionality.
For those looking for a best-in-class coating solution without supply constraints, PVF is the best choice to protect architectural metal.
For more information, click here.
References
1 Fluorinated Polymers: Volume 2: Applications, Editors: Bruno Ameduri, Hideo Sawada, Royal Society of Chemistry, 2016, 151. DOI https://doi.org/10.1039/9781782629368
2 Tanaka, A.; Sawada, H.; Kojima, Y. Application of Poly(vinylidene fluoride) and Poly(methyl methacrylate) Blends to Optical Material. Polym J 22, 463-467 (1990). https://doi.org/10.1295/polymj.22.463
3 Wood, K. Fluorocarbon Resins for Coatings and Inks in Coating Materials and Surface Coatings, edited by Arthur A. Tracton, CRC Press, Taylor & Francis Group, Boca Raton, FL, 2007.
4 M. Services, Meeting the Requirements for Building Exteriors that Can Stand the Test of Time, New York Festival of Construction, New York, NY, 2021.
5 Tracy, J. Importance of Material Selection on Building Structure Aesthetics and Performance, Metal Con, Tampa, FL, 2021.
6 Ebnesajjad, S. Polyvinly Fluoride: Technology and Applications of PVF, Elsevier, 2013, 300-301.
7 DuPont Global PV Reliability 2019 Field Analysis. https://www.dupont.com/content/dam/dupont/amer/us/en/photovoltaic/public/documents/DPVS_Field_Study_Analysis-1.pdf.
8 J. Tracy et al., "Survey of Material Degradation in Globally Fielded PV Modules," 2019 IEEE 46th Photovoltaic Specialists Conference (PVSC), 2019, pp. 0874-0879, doi: 10.1109/PVSC40753.2019.8981140.
Looking for a reprint of this article?
From high-res PDFs to custom plaques, order your copy today!