Quality Control Testing of Titanium Dioxide Industrial Coating Bases
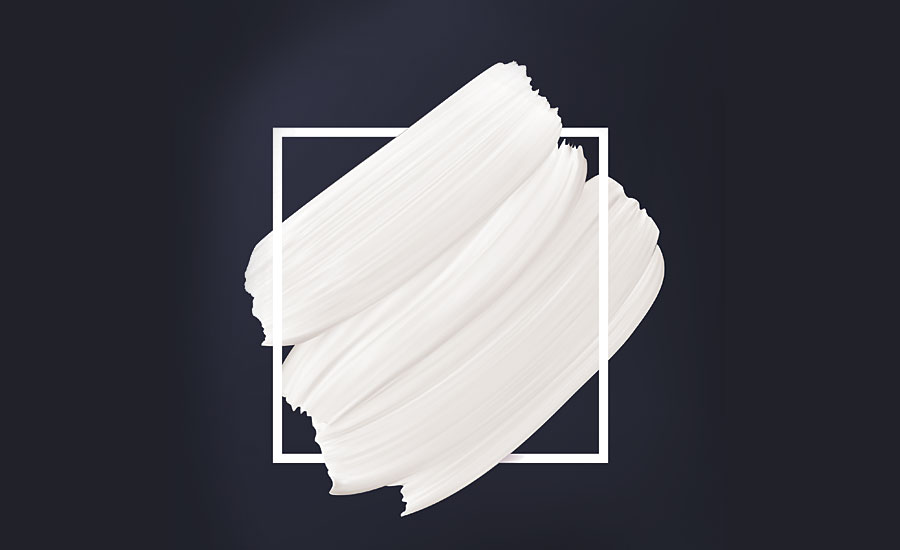
For suppliers and coating companies, quality control tests that achieve accurate, repeatable measurements are essential. Without valid testing, product quality inevitably suffers, starting a cascading avalanche of negative implications that can span from lost time and increased costs to damaged reputations and declining sales. Unfortunately, these highly accurate measurements can be difficult to achieve, much less duplicate across multiple instruments in several locations.
Take, for example, quality control testing for titanium dioxide (TiO2) industrial coating bases - the most common pigment in coatings, which is used to ensure longevity of paints and continued protection of the substrate, in addition to improving aesthetic appeal, opacity and durability. The production process to take titanium dioxide and develop industrial coating bases begins as the titanium dioxide powder first enters a factory. As soon as the raw material arrives, it undergoes an initial round of quality tests to ensure the powder meets the facility’s strict quality requirements.
In order for these tests to have merit over time, especially when using multiple instruments across several sites, high inter-instrument agreement is incredibly important. In fact, it’s essential. Without stringent instrument specifications, both the validity of testing and product quality will suffer.
Paint and coating professionals are tasked with finding solutions to any breakdowns in production quality. Arguably, it all comes back to technology. Currently, testing equipment used throughout the coatings industry for titanium dioxide includes whiteness meters and spectrophotometers, which are used to generate data on a variety of corresponding quality control measures, including whiteness, color expression, contrast ratio, strength and resistance to weathering. The choice between these two, paired with the quality of the instrument utilized, dramatically impacts the end result.
For companies relying on whiteness meters to conduct quality control tests on titanium dioxide powder, the advantages are clear: simple operation and low price. It is an attractive solution, but what is being sacrificed? Whiteness meters generally adopt RGB 0/45 optical filter structure, which is limited in the information it provides (Figure 1). Because of this, whiteness meters provide only whiteness data calculated with tristimulus values and cannot provide reflectance data, which limits options for other testing calculations that may be desired and could have otherwise been calculated using reflectance curves.
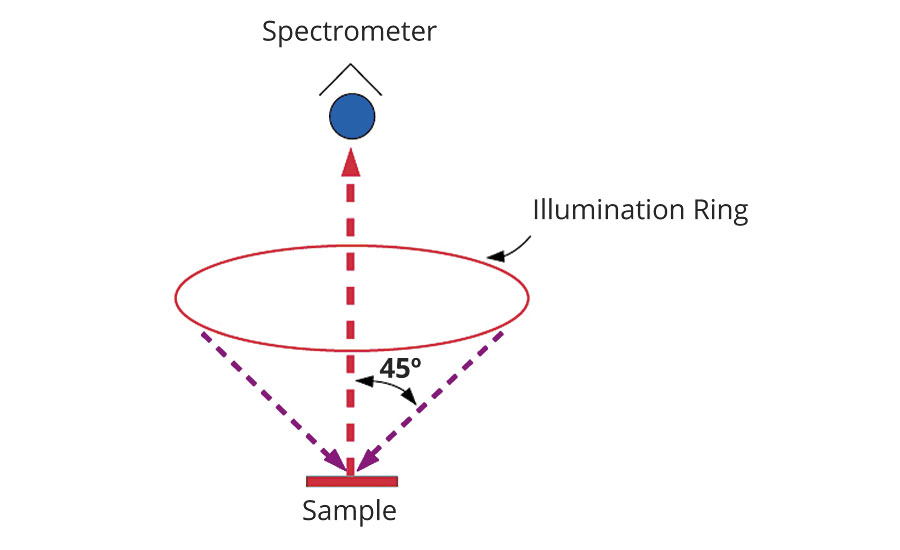
Furthermore, and perhaps most importantly, data from whiteness meters is inconsistent — often necessitating repeated testing that wastes time, impacts costs and increases workload. Part of this inconsistency can be attributed to calibration. Whiteness meter manufacturers fail to provide calibration services, which may seem trivial, but in reality, this means that after a few years of use, data from these meters is unreliable and effectively unusable.
On the other hand, a significant improvement in quality control testing of titanium dioxide can be seen by companies who rely on spectrophotometers, such as the Datacolor 800V, which has begun to gain wider recognition as a superior solution among titanium dioxide manufacturers and coatings companies.
Thanks to the technology’s high inter-instrument agreement, manufacturers can easily control quality, while coatings companies can set permissible deviation standards for their suppliers. With a D/8 geometric angle and dual-beam-type benchtop spectrophotometer, coatings plants also enjoy many benefits beyond inter-instrument agreement, including ease of sharing data between stations, highly accurate and repeatable measurements, increased data reliability thanks to regular onsite calibration and maintenance services, and the ability to run multiple tests on the same equipment (Figure 2).
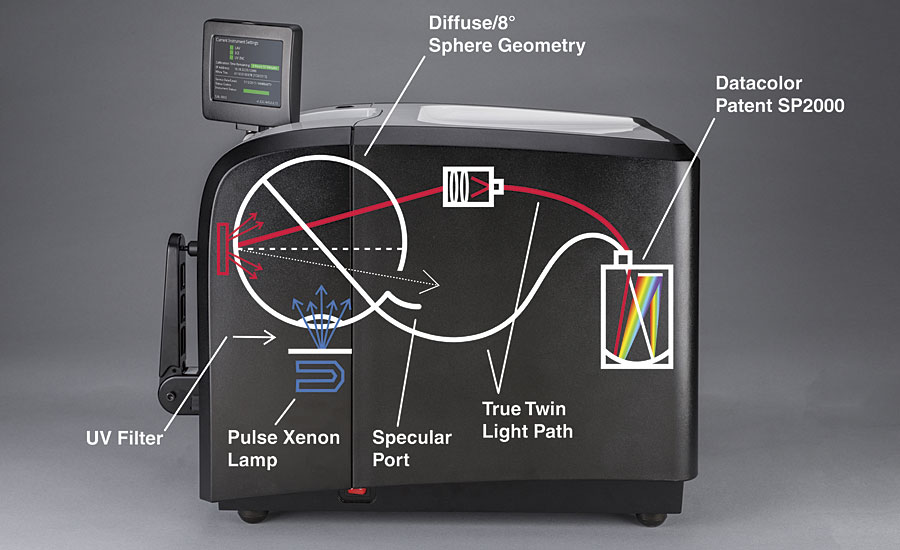
Because of the increased accuracy of data, measurements from spectrophotometers can be compared against standards, without the need to conduct parallel tests, effectively saving time and money in the process. Furthermore, annual spectrophotometer testing and calibration certification ensures the data generated is highly repeatable and accurate.
Despite the high level of inter-instrument agreement achievable with spectrophotometers, in certain cases, it still may not be sufficient for suppliers to meet their quality control requirements of titanium dioxide bases. In these instances, where even superior agreement is needed, it is necessary to turn to a custom software solution, such as Datacolor TOOLS V2.0. When paired with a company’s spectrophotometers, a comprehensive software solution can effectively eliminate disagreement between two instruments on a given standard, resulting in two standards that are colormetrically identical. This is especially helpful when a manufacturer has very stringent tolerances, and a large percentage of these tolerances are taken up with the difference in instruments.
Consider this scenario: two spectrophotometers (A and B) exhibiting disagreement when measuring the same titanium dioxide sample. The user would first measure the working standard on instrument A against the digitally stored master standard. The software would then provide information on the difference between the master standard and the measured working standard. This information, along with the measured working standard, is sent to instrument B. Once the working standard is measured on instrument B, the data is analyzed by the software solution, creating a new virtual master standard that is colormetrically identical to the original digital standard on instrument A. Thanks to this solution, whether a titanium dioxide batch is measured on instrument A or instrument B, the results will be identical.
This level of accuracy and repeatability is essential to the quality control side of manufacturing and directly impacts the end product. Even beyond titanium dioxide industrial coatings, the value of high-end instrumentation capable of superior inter-instrument agreement is indisputable across the spectrum of quality control needs experienced throughout the paint and coatings industry. By starting with the right high-quality instruments, suppliers and coatings companies can curtail the breakdown of inaccurate, unrepeatable quality control measurements and achieve consistent results that ultimately save time, money and reputations.
Author’s Note:
This article is based on the paper, “Quality Control Testing for Titanium Dioxide Industrial Coatings Bases,” written by Holly Ling Bing, Paint Applications Manager, Datacolor Shanghai.
Looking for a reprint of this article?
From high-res PDFs to custom plaques, order your copy today!