Oxidizable Phenolic Urethanes

A novel line of sustainable, bio-based, air drying resins has recently been introduced that will help solventborne coatings formulators to meet increasingly restrictive VOC regulations. Known as oxidizable phenolic urethanes, or OPUs, these products can be used to modify and improve upon the properties obtained from conventional solventborne systems, including reduced dry time, enhanced toughness, mar resistance, high gloss and improved chemical resistance.
This article will briefly review the chemistry of traditional oxidizable vehicles, phenolic resins and urethanes to appreciate how this novel resin technology transforms all three to produce improved results in the application and performance of VOC-compliant paints and coatings.
Chemistry
In one hybrid molecule, oxidizable phenolic urethanes combine the properties of fast-drying unsaturated hydrocarbons, the chemical and scratch resistance of phenolics, and the toughness of urethanes. Generically, the molecule can be represented as shown in Figure 1.
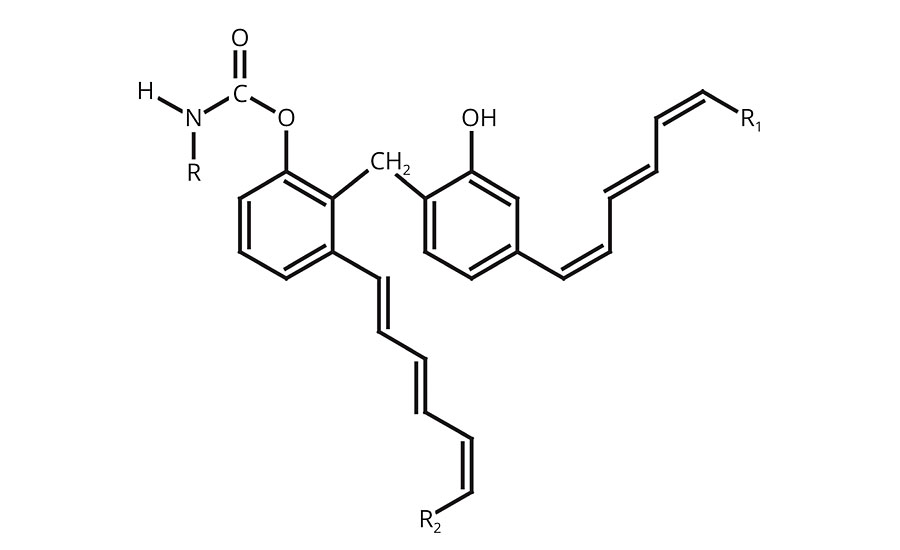
The highly unsaturated hydrocarbon pendant chains allow drying, via oxidation, similar to other oxidizable vehicles such as drying oils, alkyds, oil-modified urethanes and uralkyds.
The phenolic portion contributes to quick film hardness, improved gloss, thermal stability, and excellent chemical, solvent and moisture resistance.
The urethane chemistry provides a unique combination of toughness, abrasion, scratch and mar resistance, and an outstanding balance of hardness and flexibility.
A review of the chemistry, application and properties of oxidizable vehicles, phenolic resins and polyurethanes will aid our appreciation of how OPUs contribute to coatings and paints.
Oxidizable Vehicles
Oxidizable vehicles include drying oils, alkyd resins, oil-modified urethanes and uralkyds. To better appreciate how these vehicles cure, it is helpful to review their chemistry and their propensity to oxidize.
Drying Oils
Drying oils used for coatings applications are naturally occurring materials and are broadly classified as vegetable oils and marine oils. They include highly unsaturated vegetable oils (linseed, tung, etc.) and cooked vegetable oils, which are pre-polymerized, or pre-oxidized, semi-drying oils (soya, sunflower, etc.). Drying oils are still in use as film formers to produce household paints for indoor applications.
Chemically, all oils are triglycerides - compounds of one molecule of glycerin and three molecules of long-chain fatty acids. Fats are also triglycerides but differ from oils in that they are solids rather than liquids at room temperature. The various oils differ greatly in drying properties, as well as other characteristics, depending on the kind of fatty acids contained. The predominant fatty acids found in vegetable oils are 18 carbons in length with varying degrees of unsaturation. They include stearic, oleic and linoleic (Figure 2).
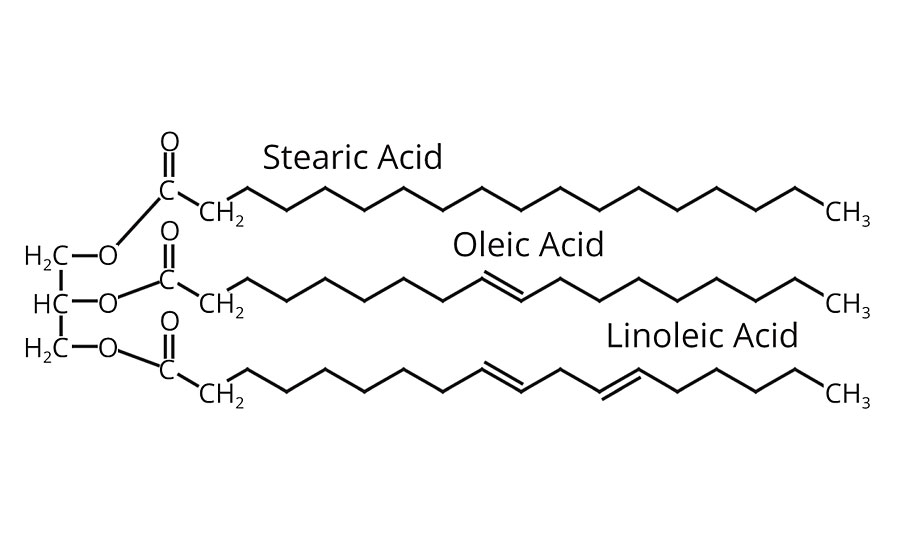
The double bonds in the unsaturated fatty acids are chemically reactive sites. They are the points at which oxygen reacts with the oil to produce drying. Consequently, oils containing saturated acids (i.e. stearic) are non-drying (coconut, cottonseed, etc.), while oils containing acids with three double bonds (linolenic) dry most rapidly (linseed, safflower, etc.). All natural oils contain mixtures of various fatty acids. Hence, the drying and other properties of an oil are determined by the kinds of fatty acids it contains and their amounts.
The fatty acids discussed above are predominantly found in oils such as linseed, safflower, soya, cottonseed, coconut and tall oil. The double bonds are isolated on separate carbon atoms. On the other hand, the fatty acids found in oils such as tung (China wood oil), oiticica and dehydrated castor oil contain double bonds on adjacent carbons in sequence, which makes them more reactive (Figure 3).
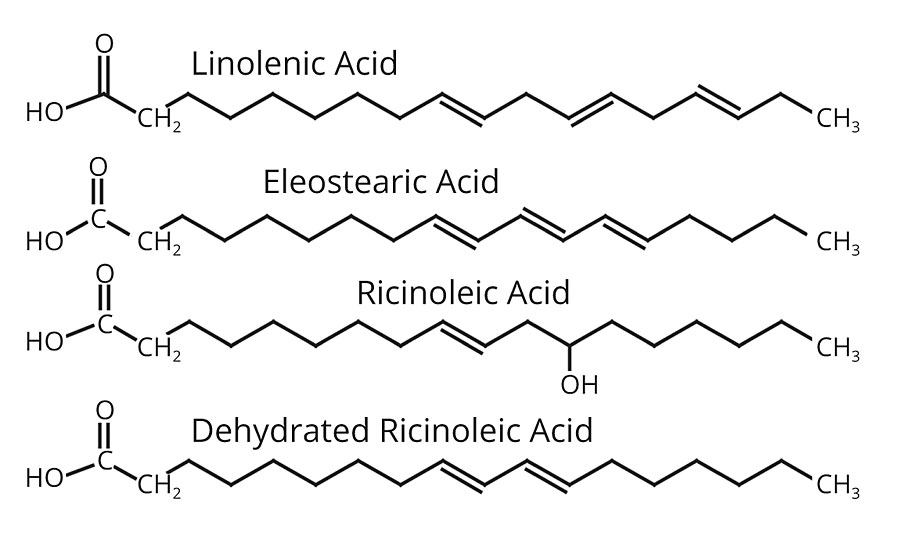
These double bonds are conjugated and allow faster drying and heat polymerization (heat bodying) properties. Because of their better drying properties, tung, oiticica and dehydrated castor oils are classified as hard oils, whereas linseed, safflower, soya, cottonseed and coconut are known as soft oils.
The acid that distinguishes castor oil is ricinoleic acid. Like oleic acid, it contains only one double bond and accordingly, is non-drying. The difference is that a hydrogen is replaced by a hydroxyl group, and the presence of the OH group is key to dehydration and conjugation to make a valuable drying oil. When castor oil is heat treated with mineral acids, or acid salts, water is split off at the OH group. This results in the removal of both the OH group and a hydrogen atom, and the introduction of a second double bond, which is conjugated relative to the original double bond. Consequently, drying properties are achieved.
Alkyds
Alkyds are a class of polyester resins derived from the reaction of an alcohol and an acid or acid anhydride; hence the term alk-yd from “alcohol and acid.” They are typically manufactured from acid anhydrides, such as phthalic anhydride or maleic anhydride, and polyols, such as glycerin or pentaerythritol. Additionally, they are also modified with unsaturated fatty acids, mainly unsaturated C18 from vegetable oils, to give them air drying properties. Modifying fatty acids come from vegetable oils such as soya, sunflower, coconut, dehydrated castor, linseed, tung and tall oil (resinous oil by-product from pulp and paper manufacturing).
As with drying oils, the unsaturated oils within alkyds react with oxygen from the atmosphere, which causes the oils to polymerize or crosslink with each other. The drying speed of the coating depends on the amount and type of drying oil employed. The more unsaturated the oil, the faster the reaction with oxygen.
Alkyd resins are produced via two processes – the fatty acid process and the alcoholysis process. In the alcoholysis process, raw vegetable oil, high in unsaturation, is combined with additional polyol and heated to cause transesterification of the triglycerides into a mixture of mono- and di-glyceride oils (Figure 4).
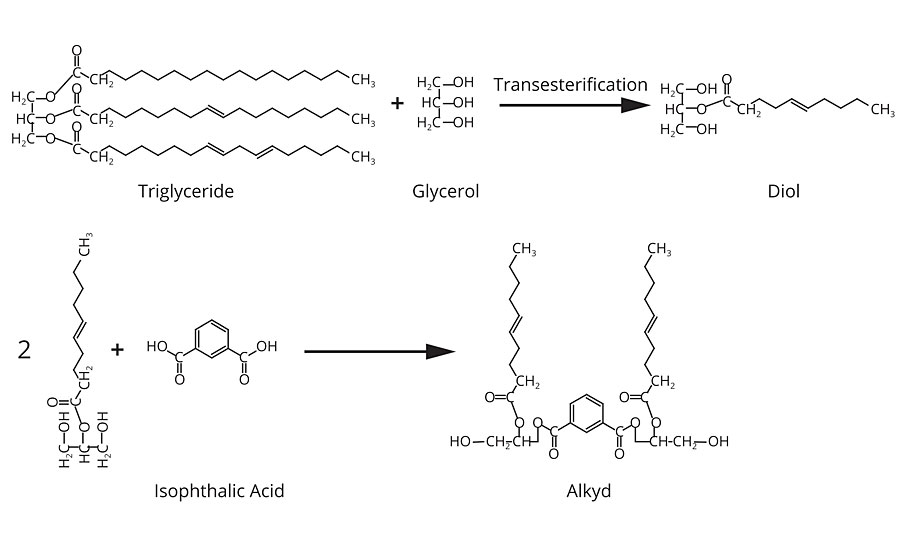
To this resulting mixture acid anhydride is added to build molecular weight of the resin. The resulting product is a polyester resin to which pendant drying oil groups are attached.
In oil-modified urethanes, the alcoholysis of oil with glycols (trimethylol propane) produces monoglycerides (2 OH groups) and diglycerides (1 OH group). Generally, about 20% monoglycerides and 80% diglycerides are produced. The monoglycerides are chain extenders when reacted with diisocyanates.
Phenolics
The earliest commercial synthetic resin was based on a phenol formaldehyde resin with the commercial name Bakelite and is formed from the reaction of phenol with formaldehyde. These resins belong to the class of condensation polymers. In the formation of such polymers, two or more ingredients react to form a polymer and, in the process, parts of the molecules are eliminated as a by-product. In the case of most phenolic resins, the reactants are phenolic materials (phenol and substituted phenols) and aldehydic materials, and water is eliminated.
Phenol can react with formaldehyde at any one of three possible sites at the ortho and para positions (sites 2, 4, and 6), allowing up to three units of formaldehyde to attach to the ring. Formaldehyde can react with up to two phenols. Thus, the theoretical functionality of phenol is three, the theoretical functionality of formaldehyde is two, and the actual functionality that is found in the polymer depends upon the phenol to formaldehyde ratio.
Once the phenol monoalcohol (hydroxymethylphenol) is formed, the course of the reaction depends on the reaction conditions, particularly on the pH. What happens is very different in an acidic system than in an alkaline one and, thus, it is usually convenient to consider them as two different types of resins.
Hydroxymethylphenol is capable of reacting with either another free ortho or para site, or with another hydroxymethyl group. The first reaction forms a methylene bridge, and the second forms an ether bridge.
In acidic systems phenol alcohols are probably still formed. However, they condense so rapidly that they cannot be isolated from the reaction mixture. By adding a small amount of acid catalyst to phenol (something miscible, such as PTSA) and slowly adding formaldehyde, the formaldehyde will react between two phenols to form a methylene bridge, creating a dimer. This dimer is contained in bisphenol F, which is itself an important monomer in the production of epoxy resins (Figure 5).
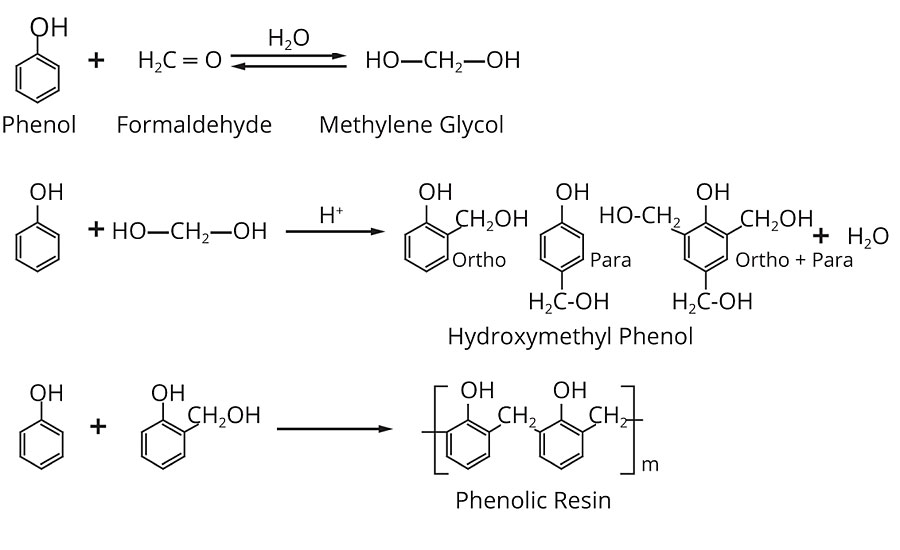
Hydroxymethyl phenols will crosslink on heating to around 120 °C to form methylene and methyl ether bridges. At this point the resin is starting to crosslink, to form the highly extended three-dimensional web of covalent bonds that is typical of polymerized phenolic resins. It is this highly crosslinked nature of phenolics that gives them their hardness and thermal stability, and that makes them impervious to most chemical attack and solvation.
Urethanes
Polyurethanes are the most prolific family of high-quality film formers. The chemistry is based on the reaction between a di- or poly-isocyanate monomer, or pre-polymer, and a di- or poly-hydroxyl pre-polymer. This results in a unique combination of the properties of toughness: outstanding balance of hardness and flexibility; abrasion, scratch and mar resistance; solvent resistance; high gloss and clarity.
Several chemical reactions enter into both the formation and curing of urethane coatings. Foremost in resin manufacture, and also useful in film forming, is the reaction of an isocyanate group with hydroxyl groups present in polyesters, polyethers, alcoholated drying oils and castor oils. Polymer formation is made possible by using di- or polyfunctional isocyanates and hydroxyl-terminated compounds. Typical is the reaction between 2,4 toluene diisocyanate (TDI) and a polyether, such as polypropylene glycol, to form an isocyanate-terminated polyurethane (Figure 6).
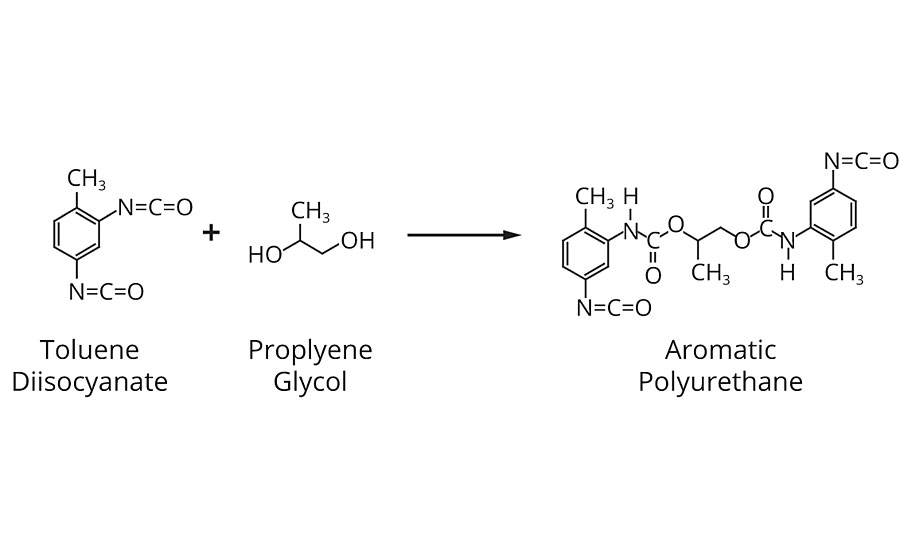
Oxidizable Phenolic Urethanes
A review of the chemistry, application and properties of oxidizable vehicles, phenolic resins and polyurethanes was essential to appreciate how OPUs contribute to coatings and paints. These resins are capable of exhibiting the benefits afforded by all three in one hybrid molecule (Figure 7).
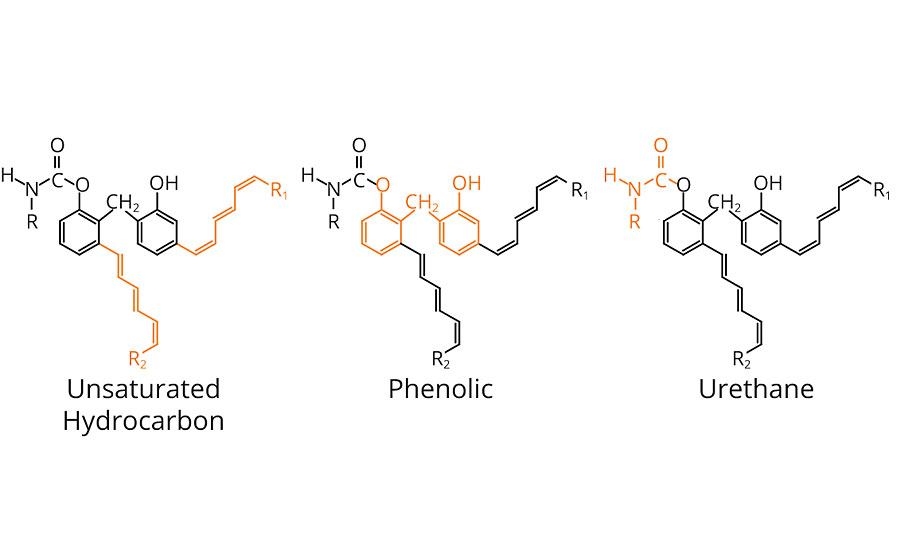
The highly unsaturated hydrocarbon side chains in OPUs contribute to quick cure (oxidation) and compatibility with drying oils, alkyds, oil-modified urethanes and uralkyds. With the appropriate drier combination, set time, tack free time and dry time are improved significantly.
The phenolic portion in OPUs contributes to quick film hardness, improved gloss, thermal stability, and excellent chemical, solvent and moisture resistance.
The urethane chemistry within OPUs contributes a unique combination of toughness; abrasion, scratch and mar resistance; clarity; and an outstanding balance of hardness and flexibility. Further, the addition of the urethane’s polarity, as well as the unsaturated hydrocarbon side chains, allow these products to be compatible, and readily diluted, with both oxygenated and non-polar solvents.
In Table 1, note the low viscosity, dry time and hardness achieved with various high-solids OPUs.

Conclusion
The unique hybrid chemistry of oxidizable phenolic urethanes combines the drying property of fast-drying oleoresinous vehicles, the chemical resistance of phenolics, and the toughness of urethanes. As a modifying resin for vegetable oils, alkyds, oil-modified urethanes or uralkyds, a coatings formulator can expect to achieve low VOC, low viscosity, fast drying and super hard finishes for a myriad of applications including paints, varnishes and stains.
Looking for a reprint of this article?
From high-res PDFs to custom plaques, order your copy today!