Styrene Sulfonate
an Excellent Stabilizer for Acrylic Emulsion Polymerization

Sodium p-styrenesulfonate (SPINOMAR® NaSS) is a water-soluble monomer manufactured via a bromine intermediate (Scheme 1). The most attractive properties of NaSS are good surface activity (Figure 1), thermal stability (Figure 2) and radical polymerizability (Table 1). The principal use of NaSS is producing acrylic fiber by emulsion polymerization. PolyNaSS® is the NaSS monomer polymerized, and has excellent thermal stability, transparency and dispersing power, so it has been used as a finishing agent for clothes, dispersants, anti-statics, separation membranes, scale inhibitors and oil field chemicals etc.1
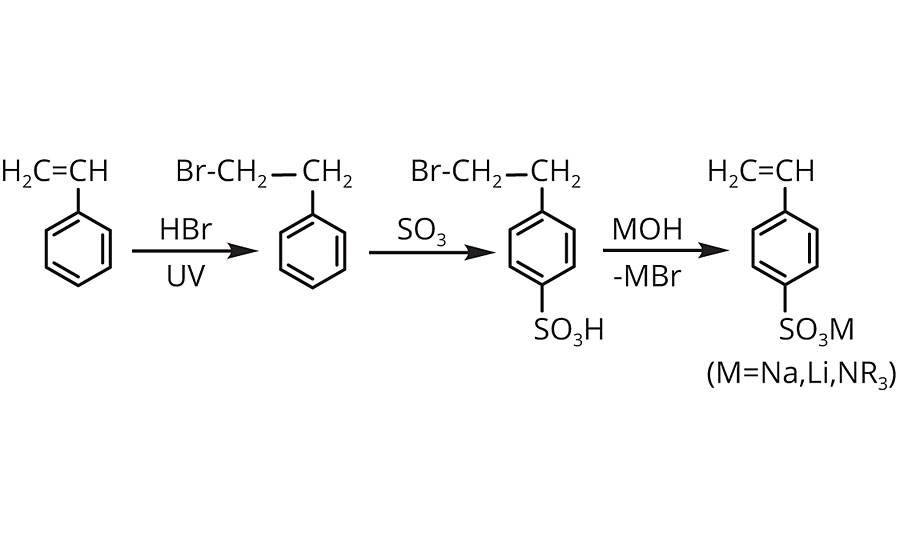
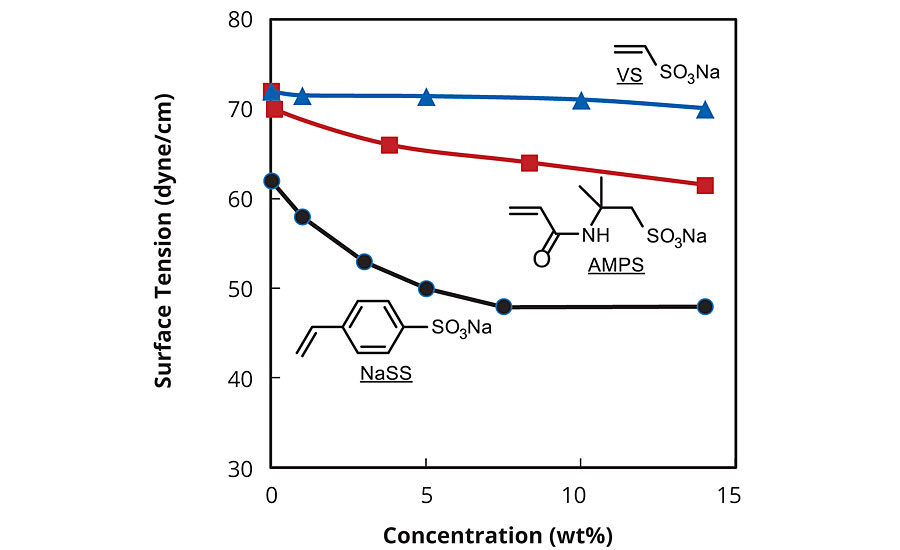

NaSS would be an ideal monomer for emulsion polymerization of acrylate due to its excellent polymerizability and surface activity.2,3 Covalently introduced sulfonate moieties would remarkably enhance the colloidal stability (Figure 3).
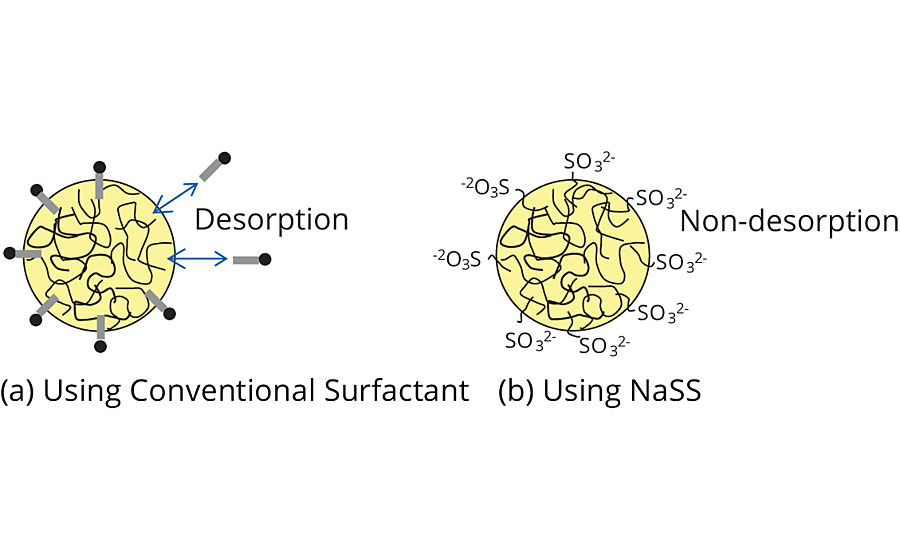

Experimental
Emulsion Polymerization
The formula for acrylic/styrene emulsion is described in Scheme 2. All reactions were conducted under N2 atmosphere.
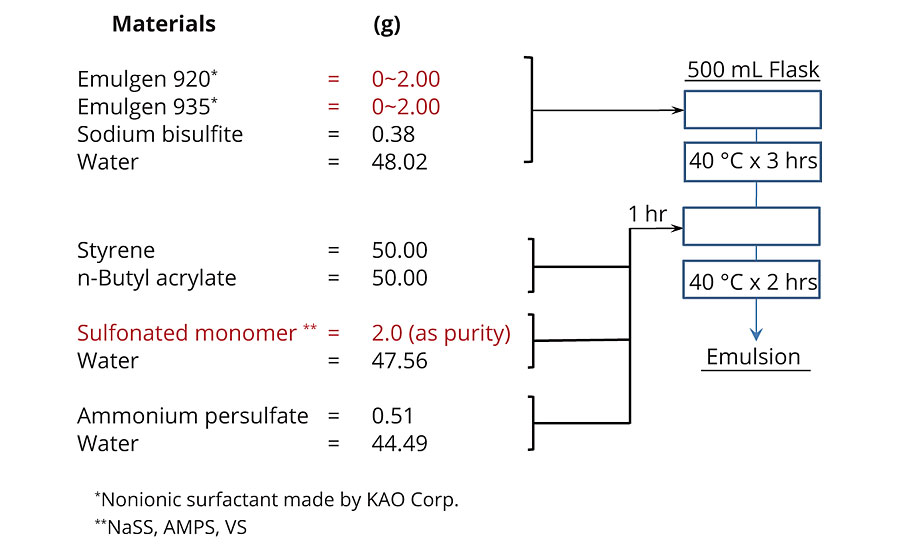
Characterization
Mechanical Stability
If no coagulation was observed after vigorous agitation of emulsion by a homogenizer at 5,000 rpm for 10 min, it was judged to be “good”.
Foaming
30 mL of diluted emulsion (3wt% solid) was put into a 100 mL measuring cylinder and shaken 10 times. The foam volume was then measured.
Water Absorbing Capacity of Film
About 5-mm-thick fluid film was dried at 20 ºC for 20 hrs and dried further at 70 ℃ for 2 hrs to prepare the sample. It was cut in a 20×20 mm piece, then dried in a sulfuric acid desiccator for 20 hrs. This test piece was immersed in 20 ℃ distilled water for 48 hrs. Water absorbing capacity was determined from the weight increase.
Results and Discussion
Coagulation was observed in all standard samples by the mechanical stability test within 10 min. But the stability was remarkably enhanced by decreasing non-ionic surfactant when NaSS was used as a stabilizer (Figure 4). This could be due to increasing NaSS incorporation by decreasing the surfactant. Sodium vinylsulfonate (VS) and Sodium 2-Acrylamido-2-methylpropane sulfonate (APMS) didn’t show such improvement in the same way.
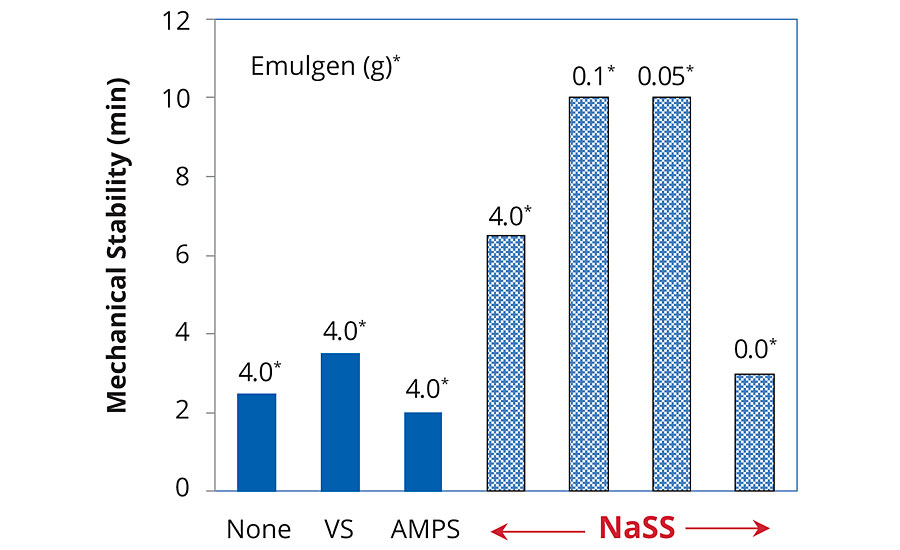
The standard emulsion using NaSS showed slightly lower foaming (Figure 5). This indicated that the concentration of free surfactant might be lower due to smaller particle size.
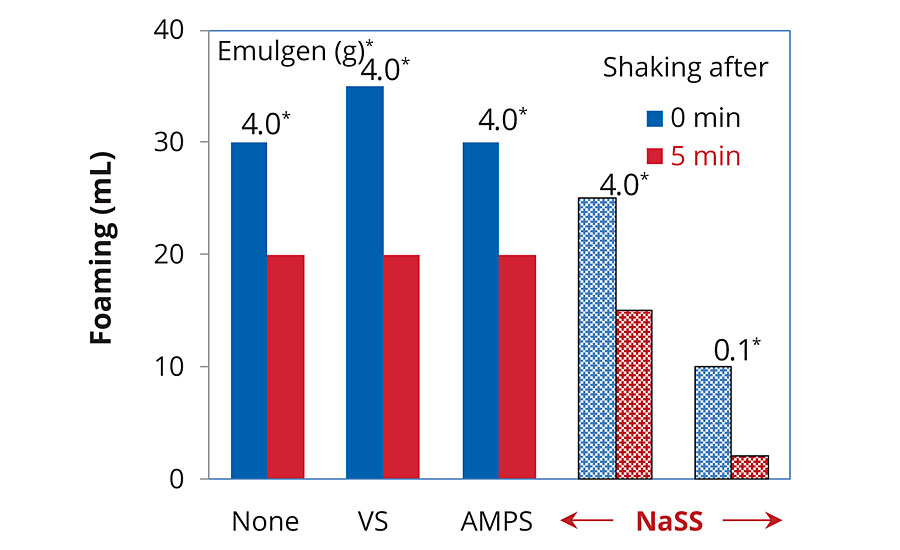
Water absorption could be decreased by reducing non-ionic surfactant when NaSS was used as a stabilizer (Figure 6). Furthermore, the water absorption could be suppressed by stepwise dosing of NaSS.2
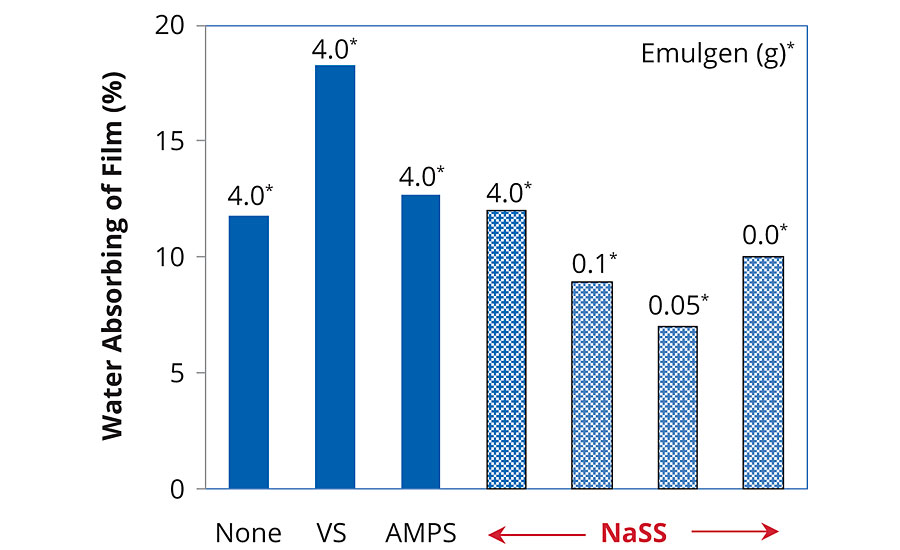
Conclusions
In this experiment, NaSS showed the best performance in terms of mechanical stability, foaming and water absorption. This was attributed to the good polymerizability and surface activity of NaSS. But there is still room for improvement, especially water resistance. We are currently examining the improvement by using new monomers such as styrene sulfonate amine salt or divinylbenzene sulfonate (Table 2).
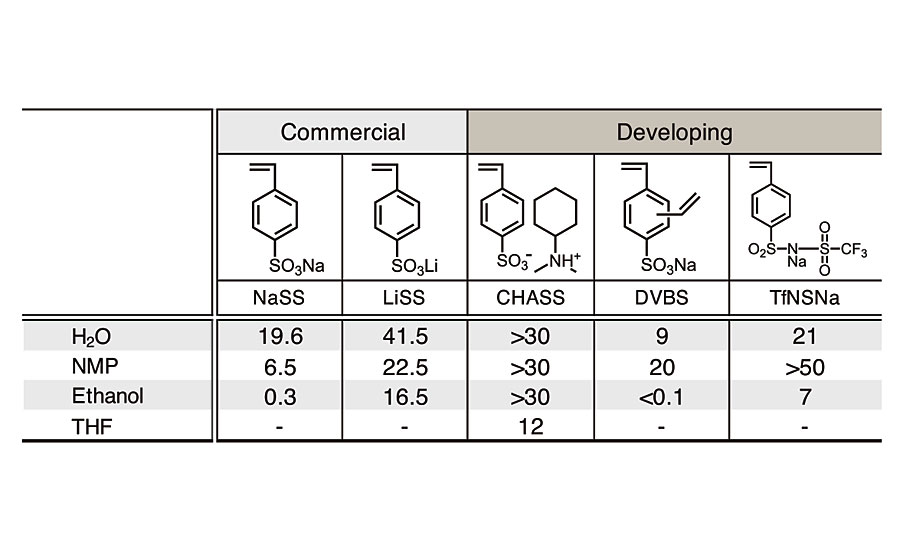
References
1 Maitra, J. Am. J. Polym. Sci., 2014, 4 (2) 25-31.
2 Okubo, M. J. Adhe. Soc. Jap., 1982, 18 (12), 530-535.
3 Bilgin, S. Polymer 2017, 117, 64-75.
Looking for a reprint of this article?
From high-res PDFs to custom plaques, order your copy today!