Flexible, Non-Contact Film Thickness Measurement

A new measurement and control technology designed to quickly and accurately measure uncured powder thickness has enabled quality and process engineers in Europe over the past several years to rapidly optimize their powder coating applications. The system has allowed them to minimize the need for the safety margins commonly applied to the powder quantity settings, resulting in large reductions in material consumption. In addition, the continuous measurement of coating thickness immediately after it is applied provides another layer of protection to detect quality problems before the parts are cured. Called Advanced Thermal Optics (ATO), the sensing means behind the system enables for highly accurate film thickness to be measured with a non-contact means on cured or uncured organic powder and powder enamel in a way that is extremely adaptable to the production environment. The data captured by the ATO system is processed with state-of-the-art signal processing to quickly generate very precise film thickness measurement data.
This patented technology was developed by Winterthur Instruments AG (Winterthur, Switzerland), and their flagship product, the Coatmaster, is now being used in a variety of industrial coating thickness measurement applications with over 220 units installed (Figure 1). The nature of the technology allows it to measure almost any type of coating on virtually any substrate, so in addition to powder materials, its application base includes liquid paints, adhesives, lubricants and thermal spray coatings. However, since powder materials are highly sensitive to the heating and cooling effects that are core to the system, the Coatmaster is extremely powerful when used to measure uncured powder film thickness. For example, the latest version of the system can produce a film thickness “heat map” of the uncured powder coating thickness for a 32-inch by 70-inch area only 15 seconds after the powder is applied.
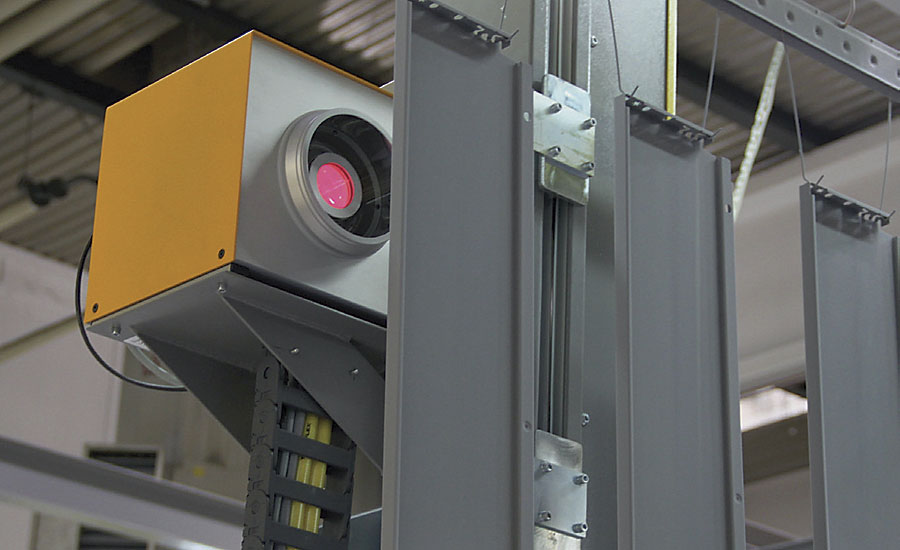
The ATO technology behind the Coatmaster works in the following way. A light pulse is emitted that very slightly warms the surface. Then, high-speed infrared sensors detect the rate at which the material cools. Using proprietary algorithms, the Coatmaster is able to translate this rate of cooling to a highly accurate film thickness measurement. The time to take a reading varies by application, but is typically 100-300 ms, and individual point readings can occur as quickly as once every 1.5 seconds. Depending on the application, the standard deviation is typically between 0.1% and 2% of the actual film thickness. The Coatmaster’s LED positioning system offers a single-point marking with a diameter between 1 and 50 mm. In this way, the measuring point can be precisely positioned even on the smallest objects, curves or complex shaped parts. From this, the Coatmaster calculates the average value of the measured range and displays it as a measurement result. Since the measurement is based on this heating-cooling effect, which is detectable in almost all coatings, it is for the most part material and substrate independent, which means that the system can measure a wide range of coating-substrate combinations. Organic powder over metal or MDF and powder enamel over metal are common applications, and it is possible to measure thicknesses of 1,000 microns or higher.
One of the unique aspects of the ATO technology used in the Coatmaster compared to approaches of other systems used for non-contact film thickness measurement is the implementation flexibility it allows in a manufacturing environment. The system is very forgiving in terms of its location with respect to the part and the speed of the part being measured. It can read from distances as close as 2 inches or as far as 48 inches, and has a measurement area that ranges from 1 to 50 mm. It can read parts moving on a conveyor up to 350 ft/min and can read off angle as much as 70 degrees. This flexibility allows it to measure parts that rotate or shift when moving on the conveyor with minimal loss of accuracy. The Coatmaster can also measure coatings on components with highly complex shapes including threaded rods, corners and angles on narrow edges, and internal and curved surfaces.
The data-capturing capability of the system is impressive, but this is only of value if this data can be used effectively. To this point, the system comes with built-in quality control software that will track the measurements and identify trends, providing warnings or alarms when readings are out of a tolerance range. The system can be used only with the industrial PC interface, or can be integrated with a PLC. The open-architecture nature of the product allows it to be easily integrated into either plant monitoring systems or directly into the application equipment to enable closed-loop control of the coating process. Manufacturers of automotive components, architectural components and other products have all used this closed-loop approach to substantially reduce their film thickness variation. This not only reduces defects, but also allows for substantial reduction in material consumption by enabling a target set point.
This ability to reduce variation in thickness is especially beneficial in powder. Since powder application tends to drift over time due to batch-to-batch material variation, environmental changes or powder gun wear, having the ability to detect this and adjust in real time allows the system to be dialed in much more precisely. Since powder materials tend to be fairly forgiving in terms of film thickness, many applications may run either with only a minimum film thickness requirement or with a broad film thickness range, such as 3 mils +/- 1 mil. If by controlling the process better with real-time film thickness feedback, a variation of +/- 0.4 mils is achievable, the process can be adjusted to target a film thickness of 2.4 mil, which is a 20% material savings (Figure 2). In fact, plants in Europe have realized savings as high as 28% as observed in the following case study. “The Coatmaster provides us with quantitative and immediate feedback on investment decisions. In this way, we can selectively and safely reduce layer thicknesses to the lower tolerance threshold. Last year, thanks to the Coatmaster, we reduced our powder consumption by a total of 28%, clearly exceeding our expectations.” Says Kai Altenburg, Head of Surface Technology at Ernst Schweizer Metallbau, a manufacturer of architectural components.
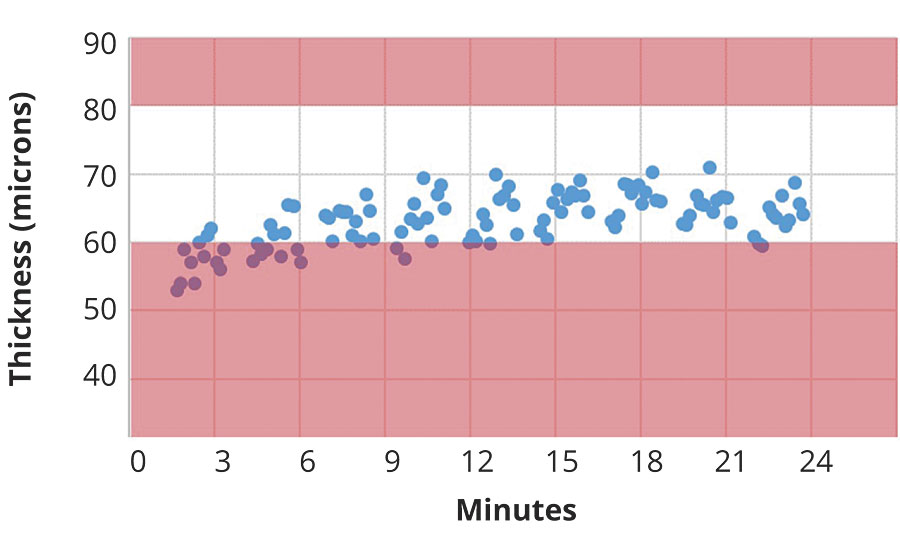
The Coatmaster is now being introduced in North America and is available in multiple configurations. There is a version designed for systems where the measurement system is static or requires minimal movement, a version designed to be integrated into a robot or more complex automation, and a handheld, battery-operated version called the Flex that is now available (Figure 3). For uncured powder over metal, a version called the Coatmaster 3D is available. With this system, the part is tracked and measured for 1-2 seconds after being slightly warmed by lights. The data is processed for 10-12 seconds and a heat map of the film thickness is created, showing variations in coating thickness for areas as large as 32” x 60” (Figure 4). This can be used to provide immediate feedback to manual applicators or as a means to more rapidly and thoroughly adjust and automated coating process.
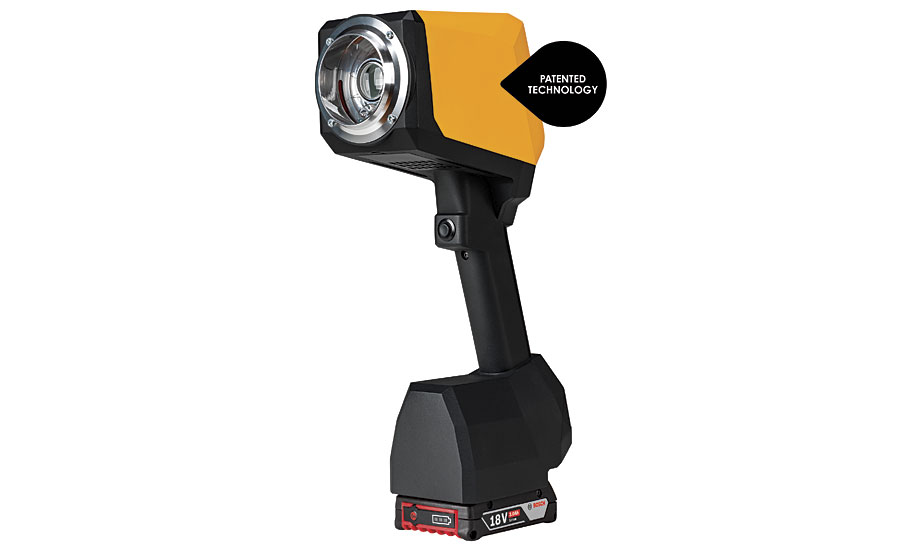
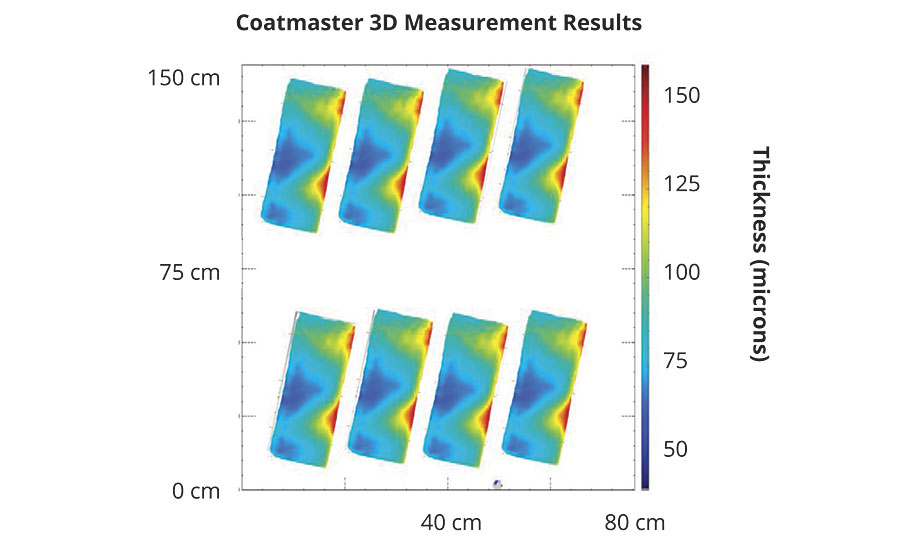
The flexibility, responsiveness and accuracy of the new technology implemented in the Coatmaster allows for process control of powder applications that have never previously been achievable.
For more information, email info@coatmasterus.com or visit www.coatmasterus.com.
Looking for a reprint of this article?
From high-res PDFs to custom plaques, order your copy today!