Digital Transformation in Automotive Painting
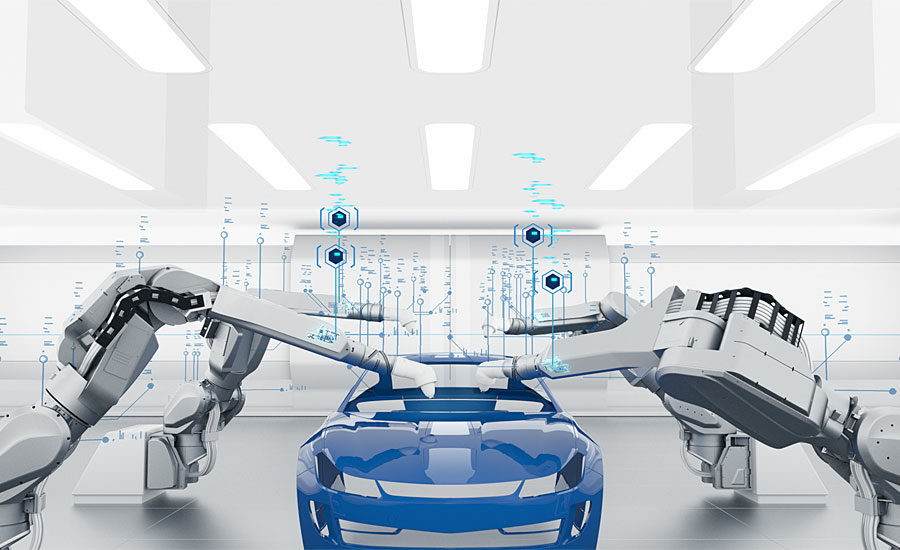
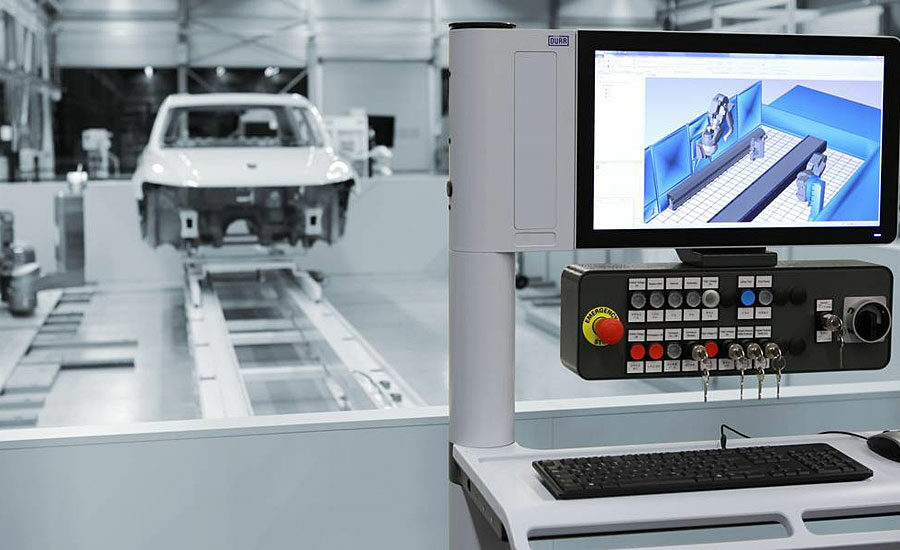


We talk about digital transformation when organizations adopt new and innovative ways of doing business to achieve value. Manufacturers are able to improve operational performance, increase revenue and maintain customer satisfaction. During this process, the use of digital tools establishes a radical rethinking of how an organization uses new technologies, people and processes to change the business performance.
Consider a global OEM that produces cars with the highest quality standards in its painting process; the materials and techniques used are superior. The level of automation and connectivity allows them to collect data from the shop floor. This raw data is filtered, classified and validated, resulting in clean and ready-to-use data by the digital tools.
The rapid growth of microelectronics and communications gives way to a hyperconnected industry; the production of Big Data is inevitable. Large volumes of structured and unstructured data are transformed into smart data every minute, and the possibilities it affords can no longer be ignored.
Companies are preparing their IT infrastructure, or at least considering making a substantial investment, by seeing a large increase in the volume of data they could produce and its value. The IT infrastructure must be fast enough to push large amounts of data through the stream, store large amounts of cognitive learning and secure enough to block unwanted access.
Big Data is used to solve business challenges, taking into account the complex manufacturing relationships across the supply chain. OEMs are looking for more data to control costs, optimize consumption of resources, and manage sustainability efforts amid changing regulations.
More and more companies realize the benefits of becoming an organization driven by artificial intelligence and machine learning. Intelligent methods of data analytics gives machines the ability to analyze patterns and learn from these patterns to perform specific tasks on their own.
Equipment Analytics and Maintenance
Statistics have been used for years to help companies correlate and classify their data to make analytical predictions, decision trees and linear regression. Industry 4.0 explores, among other fields, predictive analytics, machine learning and deep learning; where opportunities have emerged to use predictive models in manufacturing, reducing downtime and defects.
For the automated painting process, cognitive tools such as DXQequipment.analytics use analytics techniques for pattern correlation with historical values to predict behavior.
Software models like this IIoT enabler are linking signals with process events to trigger actions recorded in the system database and can recognize similar situations before they happen. Some of these tasks are intended to anticipate deviations in process conditions; others simply send predictive tasks to the DXQequipment.maintenance to avoid failures that can cause production stoppages.
Supervisory Controls
Another player in the painting process is the Manufacturing Execution System (MES), which does a nice job of collecting failures, product quality data and process values. The MES reports the status of the equipment as well as sends instructions, which keeps good track of the material flow and traceability of the product. It interconnects the Enterprise Resource Planning and the Product Lifecycle Management with the shop floor, and helps reduce scrap, optimize the use of raw materials and support management to make informed decisions.
In addition to offering the MES all-in-one solution DXQcontrol for paint shops, it also has the tools to face the smart factory; as in DXQplant.analytics. The analytics engine combines the quality data with the traceability of the product, linking the types of defects of the paint application with the areas marked for repair, the vehicle identification, the conveyance, the place of incidence, and the physical conditions of the booth at specific date and time, etc. On that premise, an application that provides all the smart data correlation available to plant personnel.
For more information, visit www.durr.com.
Looking for a reprint of this article?
From high-res PDFs to custom plaques, order your copy today!