Understanding Defoamer Chemistry

Prefer the magazine experience? Subscribe to our digital edition here.
Anyone watching a child blow bubbles through a straw into their drink can observe that a pure liquid, like water, will not form foam. A mixture, like milk, will form a stable foam on top of the drink. Gas trapped in the liquid will form bubbles, which move to the top of the drink and eventually pop. In a coating, gas entrapped in the liquid medium, either during processing or application, will cause defects when the coating is applied. Foam in production can make processing and filling challenging, while foam in a final coating will not only cause visual defects but weaken the coating.
Foam in coatings can be affected by many different factors: the composition of the coating itself, the way the coating is made and the way the coating is applied. With so many different influences at play, it is not surprising that there is no silver bullet defoamer on the market that can eliminate foam in every system. Understanding the choices of defoamers available in the market, along with the advantages and drawbacks of each, allows formulators to choose optimal chemical and processing conditions for coatings without defects caused by foam.
In liquid coating media, the entrapped foam is unique due to the high surface interface between the gas and liquid phase stabilized by surface-active components in the liquid phase. Shear is necessary to formulate these coatings, and even the gentlest coating application will introduce some air into the system. The same substances in these coatings that stabilize foam are also the substances that give coatings their desired end properties, so it would be unreasonable to remove all foam-stabilizing components from water- or solvent-based coating systems. Instead, to break the lamella and control foam through the lifetime of a coating, an additive designed to defoam the coating can prevent foam in each stage of the coating life cycle.
Defoaming additives work by bringing controlled incompatibility into the system. The ideal defoamer is incompatible enough with the bulk media that it will move to the lamella and break the foam; at the same time it is not so incompatible that it will create a microstructure on the dried surface and give the appearance of cratering (Figure 1). Small changes in both chemistry and processing will greatly change the correct defoamer choice for a coating system.
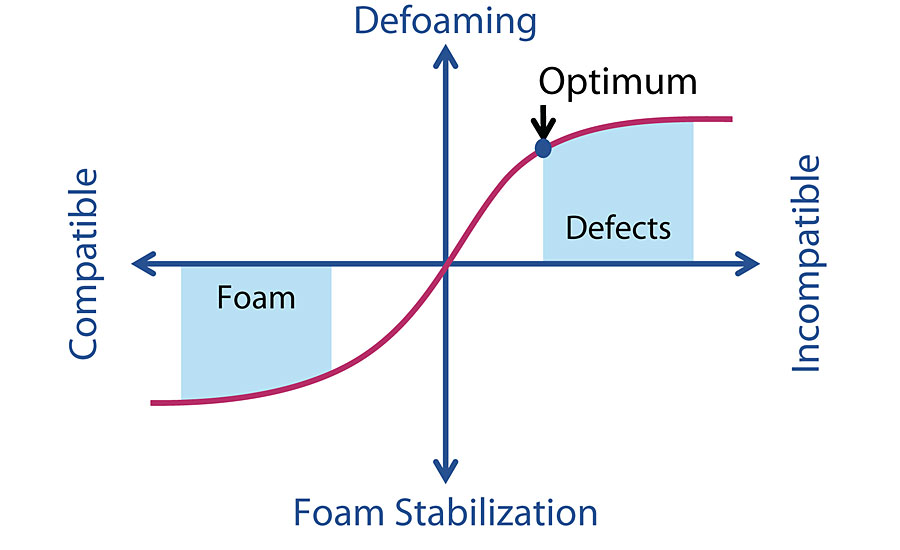
Compatibility is Important
The compatibility is determined by several factors. The ideal chemistry is the first characteristic that is important to identify. Mineral oil defoamers are often the most cost efficient. These defoamers make up a large segment of the market and can provide sufficient defoaming. There are, however, some undesirable impacts on a coating that can occur with using a mineral oil defoamer. Because a drop in gloss can be expected, mineral oil defoamers are best suited for high-PVC/low-gloss formulations. There can also be an oily residue that comes to the surface of the coating with the use of mineral oil defoamers.
The increase in popularity of high-gloss systems, along with the need for a more efficient defoamer, led to the expansion of newer defoamer chemistries. Silicone defoamers are more cost prohibitive but can be used in more sensitive coatings, as they will not have a negative impact on gloss or color acceptance when used with color pastes.
The possible modifications on the high molecular weight polydimethylsiloxane backbone gives the opportunity to modify the compatibility easily (Figure 2). The “specific incompatibility” necessary for the silicone defoamers can be achieved in various ways based on the diverse possibilities that silicone chemistry provides. Modifying the basic silicone chain with different organic side chains makes it possible to control the compatibility. In this way, polysiloxanes become hydrophilic by introducing polyether chains (R) based on ethylene oxide, thereby becoming more compatible in polar systems in general. Polyethers based on propylene oxide result in more hydrophobic structures.
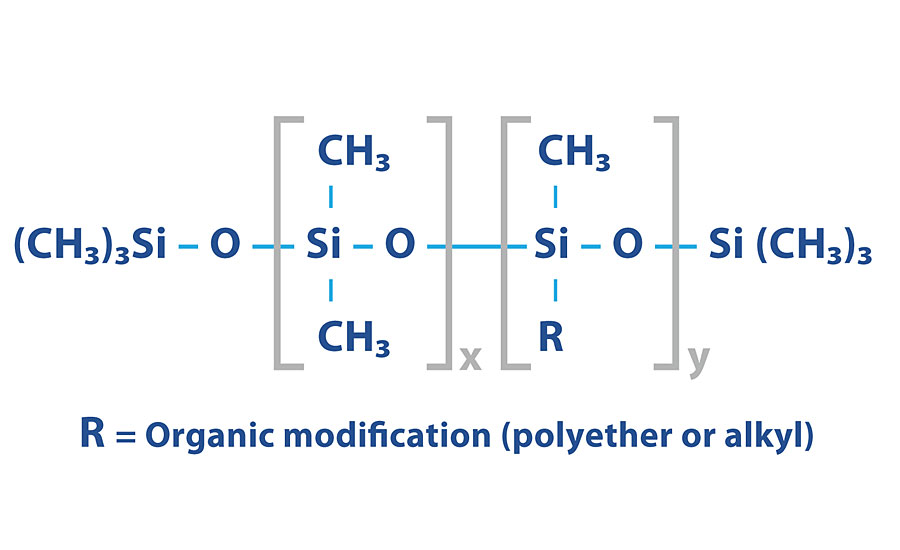
The efficiency and large variance in possibilities make silicone defoamers a very attractive option. However, there can be some instances when the use of a silicone chemistry is not desired. Some applications can be hesitant to use silicone in formulating because of potential issues with recoatability and surface slip increase that can be attributed to the silicone. While you still may be able to get away with low levels of such chemistry and not have much negative impact, it can be requested to avoid altogether. Silicone additives can also have stability issues in instances of extremely high or extremely low pH. Silicone defoamers work best in the pH range of 5-9. Outside of this range, it may be advantageous to evaluate a third chemistry option.
Polymeric defoamers are higher in cost and activity than mineral oil defoamers but often cheaper than silicone-based defoamers, and should be considered when silicone may be inappropriate to incorporate into a system. The acceptable pH range for polymeric defoamers is wider (3-12) than what is acceptable for silicone defoamers. Additionally, processing polymeric defoamers can be easier for incorporation than silicone defoamers.
As formulations continue to become more complex so too does the defoamer portfolio. Finding the correct product that is the appropriate amount of incompatible so that it can properly defoam without causing negative effects like surface defects or gloss reduction requires testing and screening. While the evolution of coatings formulations continues to lead to the expansion of the defoamer portfolio, the new developments in defoamers continue to stretch the limits of a product’s broad compatibility.
The number of variations in defoamer synthesis allows for a vast potential in differentiation, but can also lead to combinations that are balanced in a way to be used across many formulations. BYK-1781 is a product that has a well-designed silicone/polyether ratio. This formula optimizes the interaction of compatibility and efficiency, and produces a high-quality performance in the final coating.
The silicone component of BYK-1781 gives the product great performance in eliminating microfoam. The efficiency in testing continues to outperform other products of similar chemistry. However, the specific modifications to the product prevent any of the negative side effects that typically can be seen with highly efficient/highly incompatible defoamers. This eliminates any loss in gloss or propensity for surface defects that can be observed in other silicone defoamers (Figure 3). What is also unique about BYK-1781 is that this performance translates across several different waterborne coatings systems: acrylics, UV systems, polyurethanes, clear coats, pigmented systems, etc.
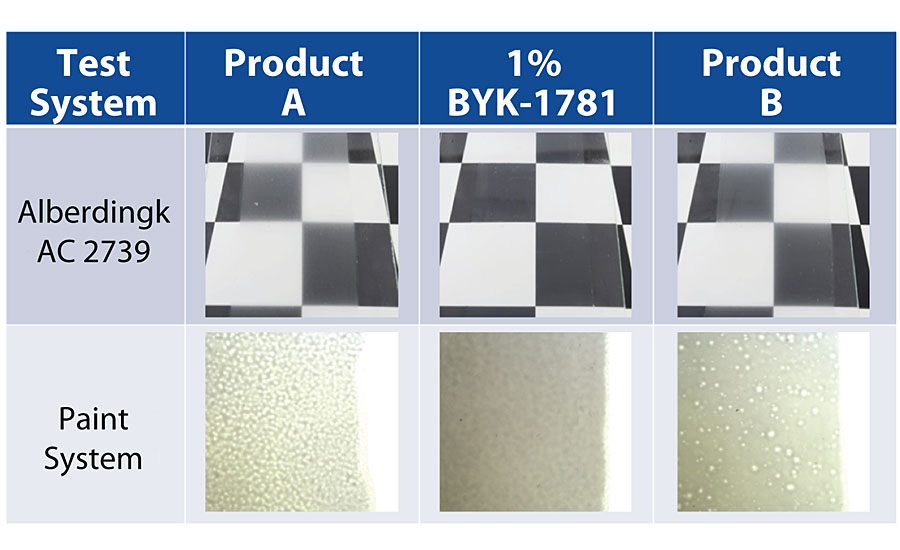
The Importance of Hydrophobic Particles
The second factor in selecting a defoamer is the presence or absence of hydrophobic particles in the defoamer (Figure 4). Mineral oil defoamers will contain hydrophobic particles to break the lamella. In more active defoamers, hydrophobic particles can be added to extend the activity of the defoamer in a finished coating. Hydrophobic particles have a rough surface. They help to lower the entry barrier of the defoamer droplet. This is the so-called “pin-effect.” As coatings sit on the shelf, defoamers can lose their effectiveness as the active ingredients become solubilized into the resin. Hydrophobic particles (silica, urea or polymeric) will not undergo this process as readily and can help retain the activity of the defoamer over time.

Understanding Shear
The third factor in choosing a defoamer is the shear needed to incorporate the defoamer for optimal performance. The shear used to make the coating will incorporate the defoamer and compatibilize it over time. Figure 5 shows what can happen if the incorporation of the defoamer is not correct. If too much shear is used in processing, the defoamer will be fully compatibilized and the defoaming effect will be lost. If too little shear is used, the defoamer will not be dispersed and will cause cratering. Defoamer concentrates will need more shear to compatibilize than emulsified defoamers but will also need a lower loading of defoamer in the coating to see an effect.
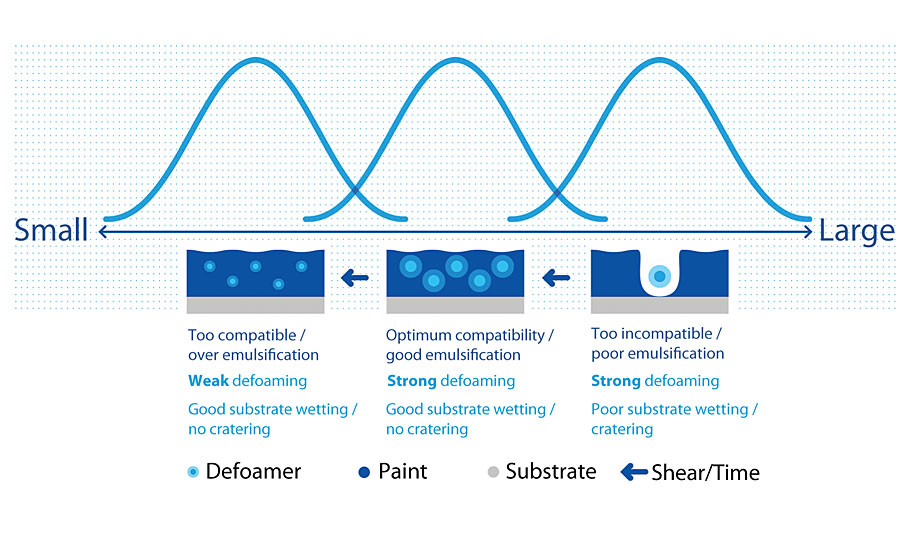
This last point is also critical when selecting a defoamer. Many defoamers will be classified by where in the formula production process they can be included. For defoamers that are highly effective and require more shear to incorporate, it will likely be necessary to add these to the formula during the grind phase or in the millbase. Defoamers that may be easier to handle but less effective will likely be suggested to be added during the let-down or under low shear.
A simple experiment can be put together to show just this impact. A screening can be done by incorporating a millbase defoamer and a let-down defoamer into the same system under varying shear conditions. Table 1 summarizes the effect shear during incorporation has on performance. The data shows a few things. The higher density achieved with the millbase defoamer shows that its efficiency is more than the let-down defoamer. You can also see with better incorporation the defoamer becomes more compatible. This decreases efficiency slightly but has a much greater impact on preventing surface defects. More variation in defoamer performance can be seen with the let-down defoamer. Here, more shear further emulsifies the defoamer into the system, and a decreased performance can be noticed. Since there is no need to improve compatibility from a surface defect standpoint, this causes more defoamer to be added to the formula in order to achieve a similar performance. This is important to keep in mind when moving a formulation from lab bench to production batch. Changes in blade speed or vessel diameter can alter the shear and change the performance of the defoamer.
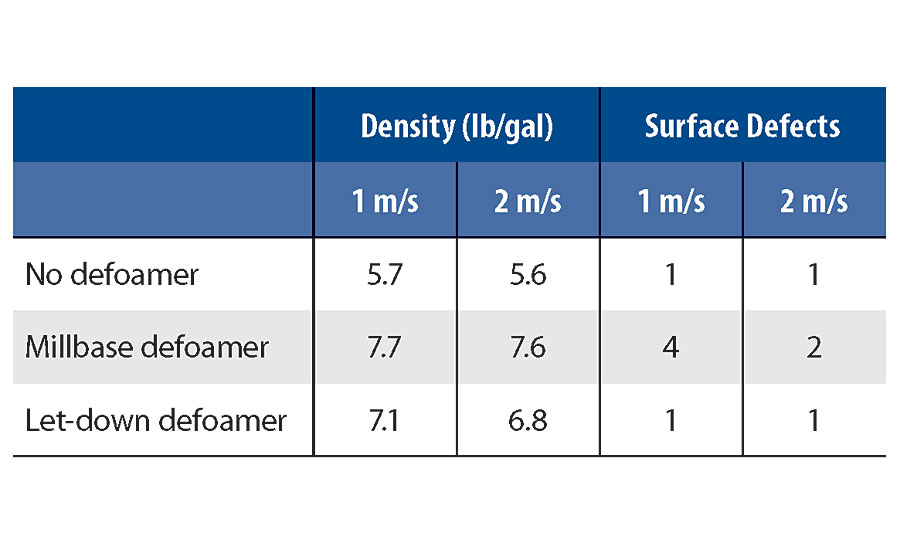
Scaling Up
In many instances, transferring to production can be the greatest hurdle in coatings formulation. This is typically because all the factors that can be controlled on a lab bench are shifted to a fixed pot, blade and mixing speed. This can cause problems with the defoamer performance as we have demonstrated, and can make finding the correct product challenging. New products like BYK-1640 continue to be developed to combat this common problem. This new polymeric defoamer is designed for waterborne systems in the 30-85 PVC range. The chemistry allows for easy incorporation in both the millbase and the let-down. When included in the let-down it provides efficient defoaming when even compared to all defoamer chemistries, including silicone, silicone emulsion and mineral oil. Figure 6 shows test results from defoamer screenings evaluating different defoamer chemistries in different binder systems.
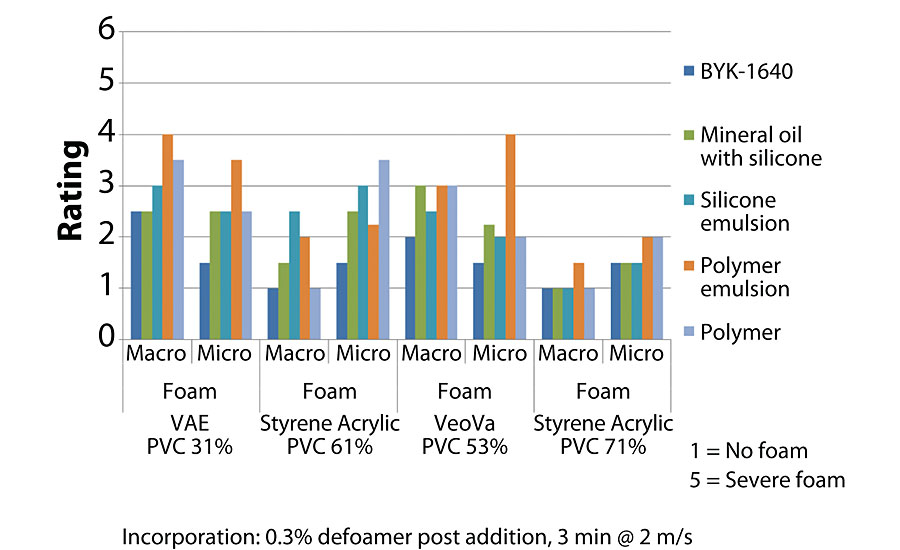
Conclusion
Using the right defoamer will lead to many desired effects in the final coating performance. First and foremost, the foam will be eliminated and the appearance will be at its best. There are also additional benefits. For instance, durability of a coating can be improved with the elimination of foam. There is also a lower propensity for dirt pickup if the surface is free of defects like craters or foam marks. While the amount of a defoamer that goes into a formulation may be small, the amount of work that goes into development, and the performance it provides, can be great.
Looking for a reprint of this article?
From high-res PDFs to custom plaques, order your copy today!