New Ambient-Curing Resins for High Heat and Corrosion Resistance

Methyl/phenyl silicone resins are a well-known technology for excellent corrosion protection and heat resistance up to 650 °C. Currently, these coatings require curing at elevated temperatures, which limits their application on large objects, reducing their scope to smaller pieces such as exhaust mufflers, chimney and oven components, and small industrial stoves. A new generation of methyl alkoxy silicone resins has been developed that cures under ambient conditions, while maintaining corrosion protection at permanent high temperatures. The high content of alkoxy functional groups, in combination with specific tin-free and heavy metal-free catalysts, allows the hydrolysis – condensation reaction, and therefore crosslinking the system – at ambient temperature. These new low-VOC resins represent a novel technology, enabling application on large industrial structures such as heat exchangers, distillation columns or industrial vessels, mostly without interrupting operations. This article also reviews some specific considerations when formulating these coating systems such as curing conditions and application methods. Performance application data is also presented.
Introduction
One of the common characteristics of silicone resins is their capacity to provide heat resistance on substrates that are exposed to high temperatures due to their inorganic character. Depending on the contained type and amount of organic modification, they can resist temperatures up to 650 °C.
Silicone resins are modified with methyl and/or phenyl groups. Given their inorganic character and low organic modification, they provide permanent resistance against oxidation to metallic structures that are exposed to temperatures above 250 °C, such as exhaust mufflers, chimneys or industrial stoves.
Today, there are different grades of commercially available options of methyl/phenyl-modified silicone resins that typically cure at approximately 250 °C in 30 min. This type of curing limits their application on large structures like heat exchangers, distillation columns or industrial vessels.
Due to the mentioned limitations, a new generation of methyl/phenyl silicone-based resins has been developed that cures under ambient conditions. They comprise a relatively high content of alkoxy functionals and oligomeric character. The resulting coating will then be cured by a hydrolysis-condensation mechanism.
Chemistry of Ambient Cure Methyl/Phenyl Silicone Resins
Silicones are organic silicon compounds known as polyorganosiloxanes. This product group can be defined simply as follows:
- they are polymers;
- silicon is directly bonded to carbon;
- there is at least one oxygen atom connected to the silicon.
The silicones occupy a hybrid position between inorganic and organic compounds, specifically between silicates and organic polymers. The siloxane link (Si-O-Si), also found in silicates, is responsible for the “inorganic” character. The organic properties arise from the direct link between silicon and carbon. 1
Usually methyl/phenyl silicone resins contain up to 95% of siloxanes within their framework. In the case of the typical oven-cured silicone resins, the siloxanes have low to no alkoxy functionality, thus polymer structures of high molecular weight. The few remaining alkoxy functionalities crosslink at approximately 250 °C and 30 min of curing time.
The new ambient-curing silicone resins are different from the previous generation, primarily because of the oligomeric character. This means that they contain low-molecular-weight siloxane structures and higher alkoxy functionality. This characteristic also allows them to have a high solid content (up to 100%) and low viscosity (Table 1). The functional groups available within the resins are methoxy, ethoxy or combinations of both. In order to crosslink and achieve further resin polymerization by condensation, such functionals must be hydrolyzed in a first reaction mechanism, leading to the formation of silanol groups. Then, these silanol groups will react between each other in an alcoholic condensation reaction mechanism. Once this step is finalized, the resin achieves its polysiloxane character and liberates alcohols as a reaction by-product. Reaction mechanisms for both silicone resin types are shown in Figure 1 and Figure 2.
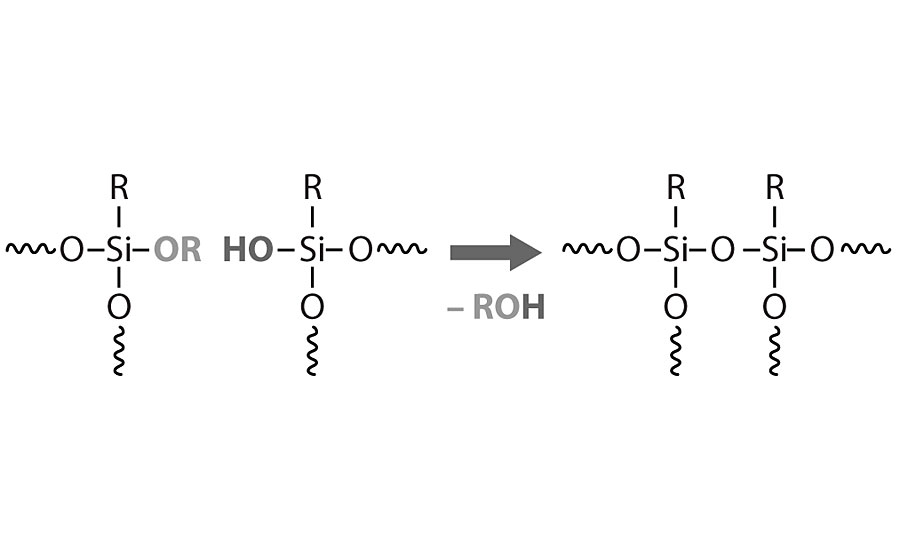
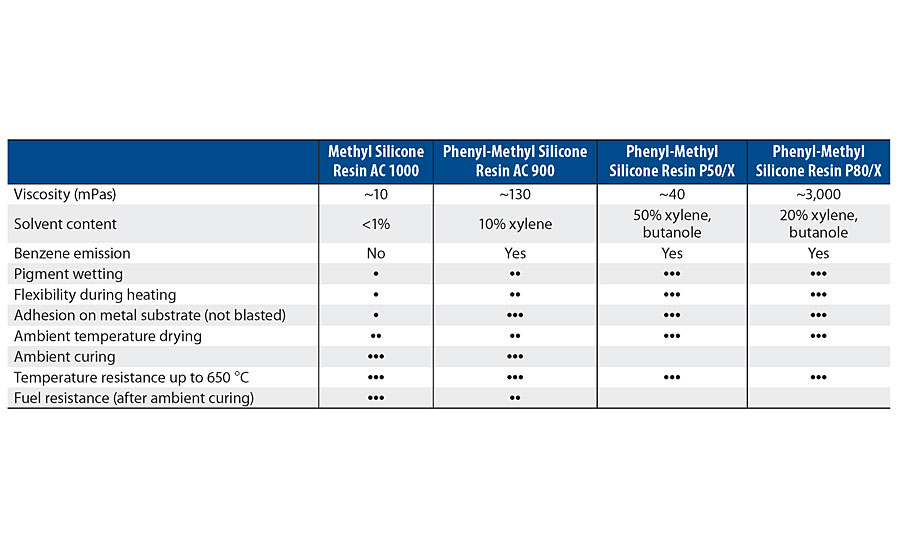
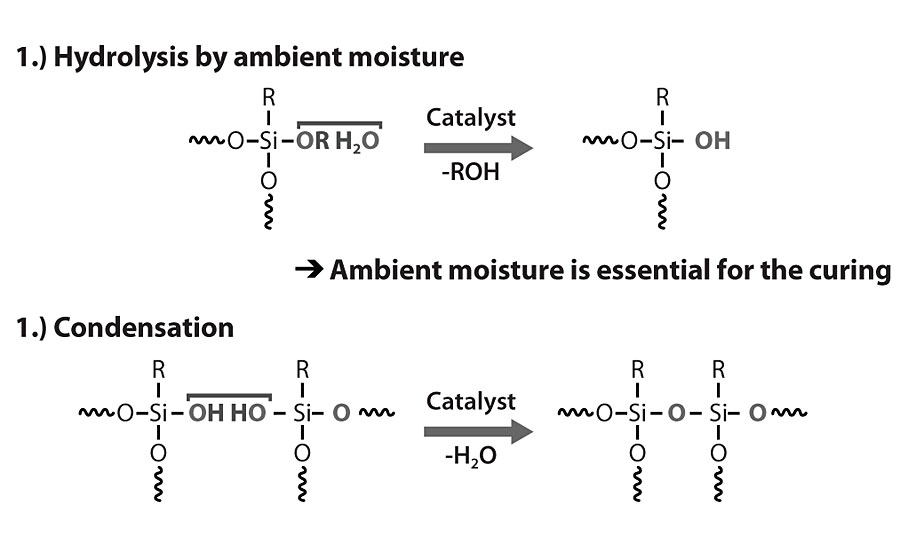
The influence of the organic methyl and/or phenyl groups is reflected mainly on the thermal stability and hardness of the coating, but also in the compatibility of the resin with pigments and fillers. Figure 3 shows the influence of the methyl or phenyl groups on the resin mechanical properties.
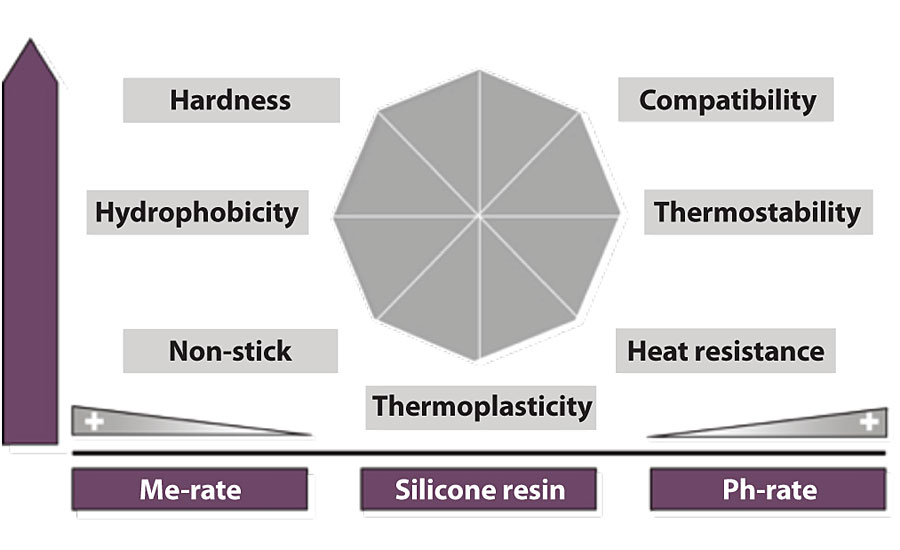
Formulation of High Heat-Resistant Anti-Corrosive Coatings with Ambient-Cure Silicone Resins
The property profile of coatings based on silicone resins is strongly dependent on the formulation. Inorganic pigments and fillers with a high heat resistance, such as oxides and spinels or inverse spinels, are mandatory (Table 2). Lamellar metallic and mica effect pigments increase the heat stability additionally, up to 650 °C. Moreover, the pigment volume concentration plays an important role for the performance. The coating should be formulated like a primer, hence with a high PVC.
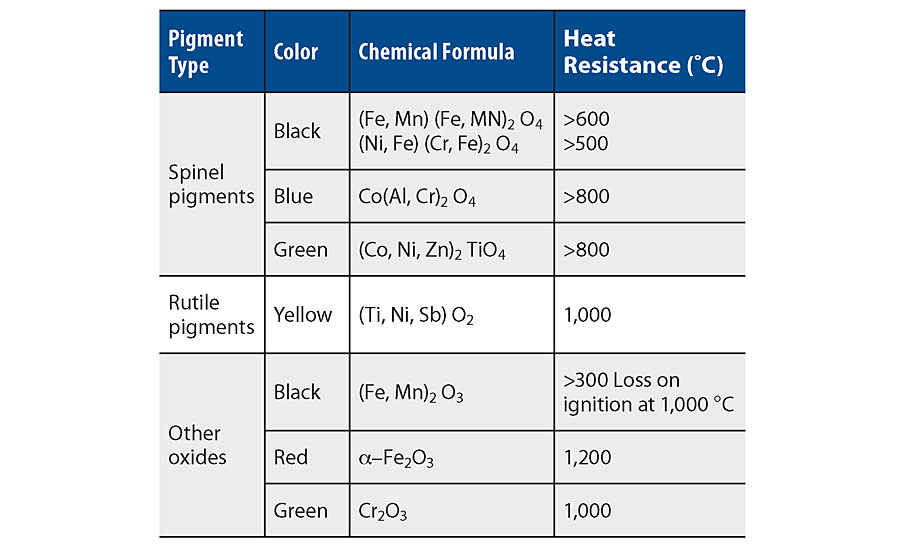
Also, very important is the use of laminar fillers, for example mica. This will provide flexibility and barrier properties on thermal expansion while alternating temperatures. Figure 4 shows a clear example of the coating brittleness when such type of fillers is underutilized (or too sparsely used) in the formulation.
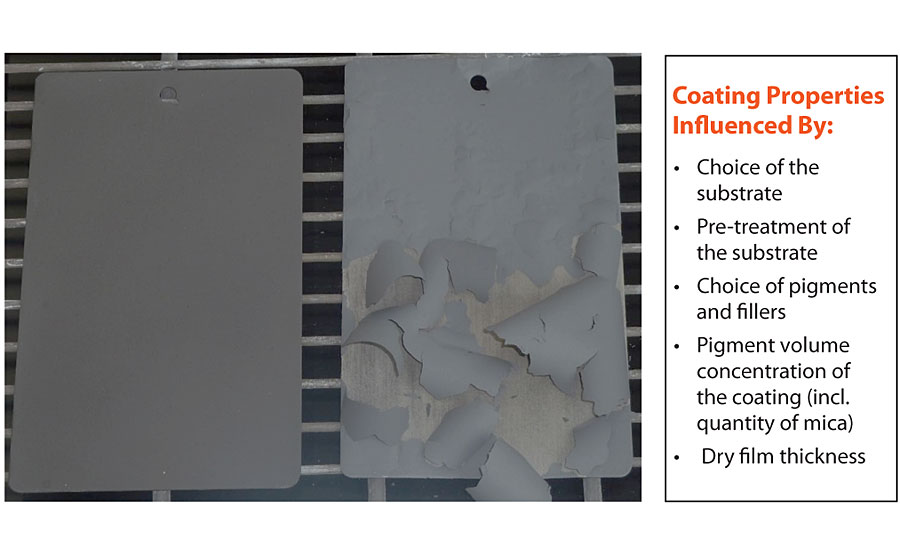
At temperatures above 400 °C, the organic components of the resin are almost completely burned off. At 650 °C frits can be sintered and inorganic composites are formed, which are very hard and chemically inert but at the same time very brittle.
As mentioned previously, the reactivity of these silicone resins allows catalytic curing at ambient temperature. Catalysts such as titanium compounds are recommended as first choices (Figure 5).
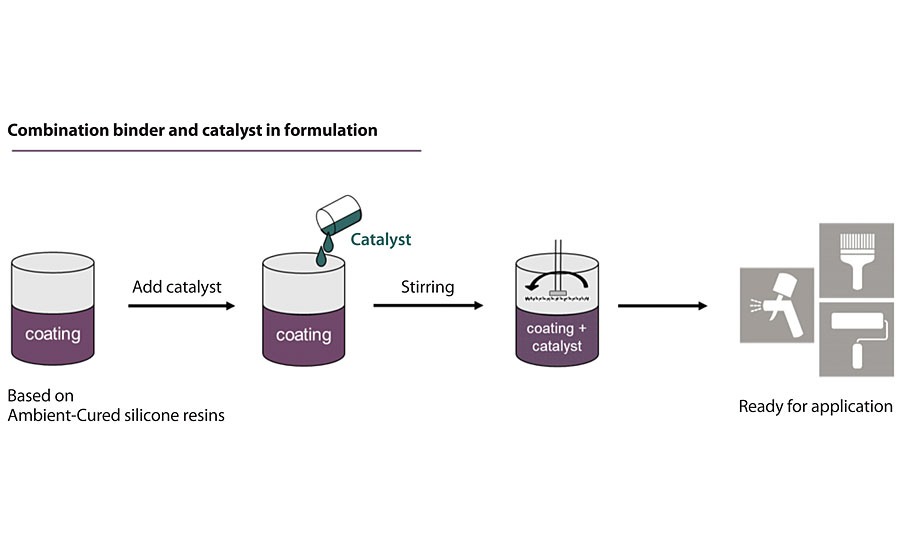
AC 900 also needs the use of the catalyst TMG (tetramethylguanidine), a strong base, accelerating the reaction speed. The recommended mixing ratio of the titanate with the TMG is preferably 1:1.
The recommended dosages of both catalysts are 0.5-2.0%, depending on the formulation. Higher relative humidity levels will lead to faster reaction. The addition of catalyst is recommended just before the application (two-pack).
Performance Highlights
When formulated and fully cured, the applied silicone-based coating can provide the following performance properties:
Coating Performance
- Excellent corrosion resistance
- Early resistance against chemicals (Figure 6)
- Permanent resistance against oxidation and weather resistance
Heat Stability
- Outstanding long-term heat stability
- High hardness under heat (low thermoplasticity)
- Superb resistance against yellowing at permanent heat stress
Both grades of AC silicone resins can be used to formulate heat-resistant coatings. However, there are differences in their technical profile. AC 900 has better pigment wetting properties and better compatibility with other resins. With this resin it is possible to formulate more flexible coatings – an especially important property in the stages of heating up and cooling down.
AC 1000 is average in wetting of pigments, but the stability of bright colors under heat stress is better due to the low tendency for yellowing. This resin shows extremely low smoke formation during the first heating.
Summary and Conclusions
The use of ambient-curing silicone resins shows a good alternate option to formulate high heat-resistant coatings compared to the traditional oven-curing or ambient-drying silicone resins. Their high solid content and low viscosity enables the formulation of significantly lower-VOC coatings. In addition, a lower smoke and odor development is characteristic for these resins. When formulated and properly cured, the resulting heat-resistant coating can provide excellent corrosion and early chemical resistance along with long-term heat stability. This set of performance attributes enables their application on chemical plants, power generation and waste incineration equipment, along with other large industrial structures without the need of increasing down time due to coating operations and reducing the amount of energy consumption while curing.
References
1 Technical Background Silicone Resins. TEGO Journal. Evonik Degussa. 2nd Edition. 2013.
2 Silikophen AC Formulation Manual. Evonik Corporation. April 2014.
Looking for a reprint of this article?
From high-res PDFs to custom plaques, order your copy today!