Reducing Adhesion Failures in the Automotive Industry

Image courtesy of Henniker Plasma.
Plasma pre-treatment is a crucial step for improving the quality and durability of automotive assemblies and components. It enhances the adhesion and compatibility of different materials that are used for encapsulation, printing, or painting processes. By applying plasma to the surface of low-energy materials, it removes contaminants and creates functional groups that increase the surface energy and reactivity. This results in a stronger and more uniform bond between the materials, reducing the risk of failure and defects.
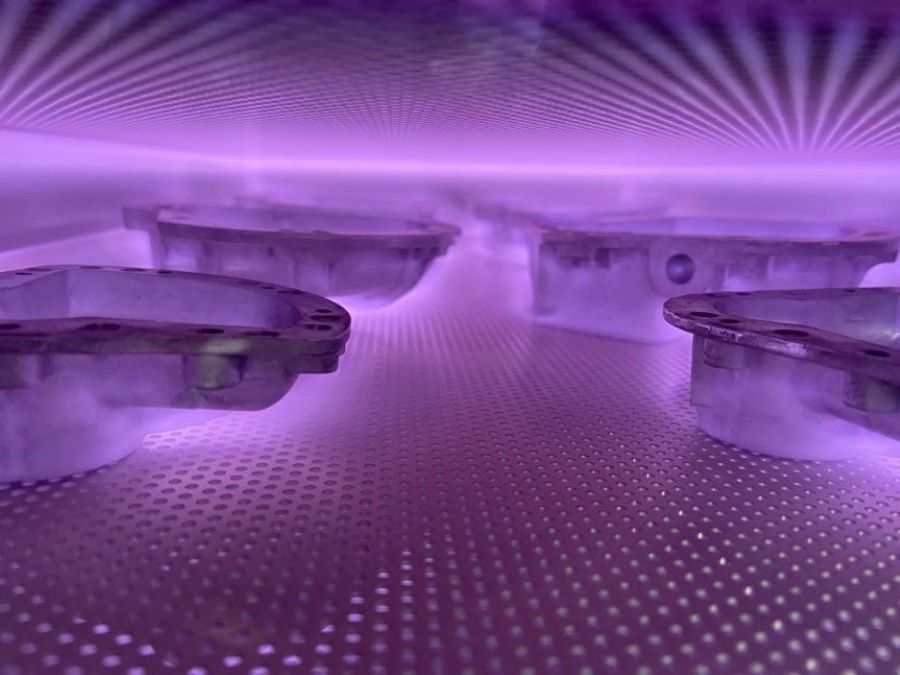
Improved Wettability of Exterior Components Prior to Painting
Plasma treatment can remove contaminants and increase the surface energy of parts such as bumpers, spoilers, and mirrors, resulting in better paint adhesion and appearance.
Plasma Activation of Topper Pads Prior To Laminating
Topper pads are foam or fabric inserts that provide comfort and noise reduction in car seats. Plasma can activate the surface of the pads, improving the bond strength and durability of the laminating material.
In-Line Atmospheric Plasma Treatment of Circuits to Improve Wire Bond Adhesion
Wire bonding is a method of connecting electrical components on a circuit board using thin wires. Plasma can clean and activate the surface of the circuit board and the wires, enhancing the reliability and performance of the wire bonds.
Improved Adhesion of Electronic Connectors Prior to Encapsulation
Electronic connectors are used to join electrical circuits in various devices and systems in a car. Plasma can improve the adhesion between the connector and the encapsulant, which protects it from moisture, dust, and corrosion.
Localized Treatment of Headlight Assemblies to Prevent Moisture Ingress
Headlights are exposed to harsh environmental conditions and need to be sealed properly to prevent fogging and water damage. Plasma can treat the edges of the headlight lens and housing, creating a stronger seal and preventing moisture ingress.
Atmospheric In-Line Plasma Pre-Treatment
The Henniker Cirrus atmospheric plasma system is a powerful and versatile tool for surface treatment of various materials. It uses a jet of energized compressed air to activate, clean, and modify the surface properties of polymers, metals, glass, and ceramics. The Cirrus system can be easily integrated into an assembly line, where it can perform localized plasma treatment on specific areas of the parts.
In-line plasma treatment is different from vacuum plasma treatment because it does not require a chamber or enclosure. Instead, the plasma is generated in a nozzle or jet that can be moved along the material surface. This makes it faster and more flexible for continuous or large-scale applications. Some examples of in-line plasma treatment uses are improving adhesion of paints, glues, or inks on plastics, metals, or textiles; depositing thin films of functional materials on glass, ceramics, or semiconductors; and sterilizing medical devices or food packaging.
In the automotive industry, the Cirrus system can improve the adhesion of the bond line and the electrical connection posts of a component before gluing it to another part. The picture below shows how the Cirrus system is used with a robot arm to apply plasma treatment on an automotive part.
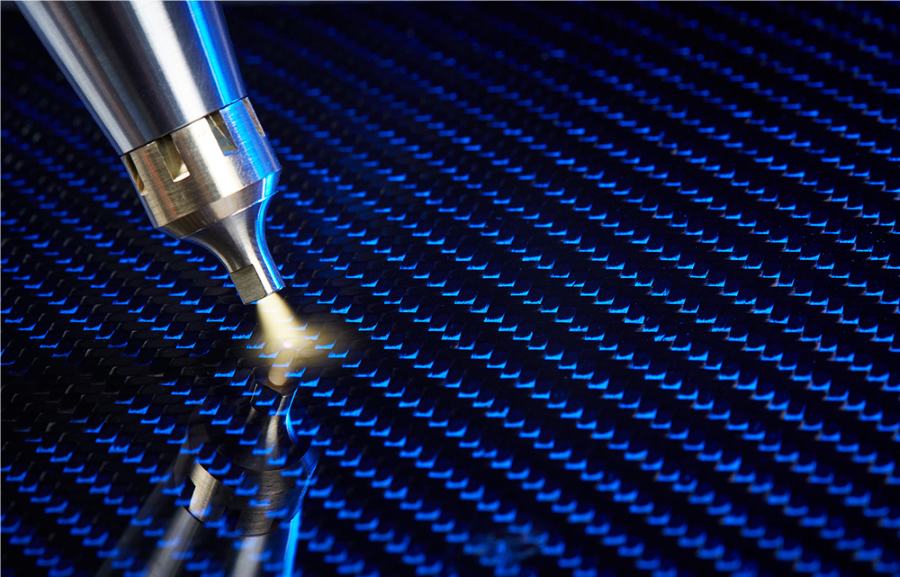
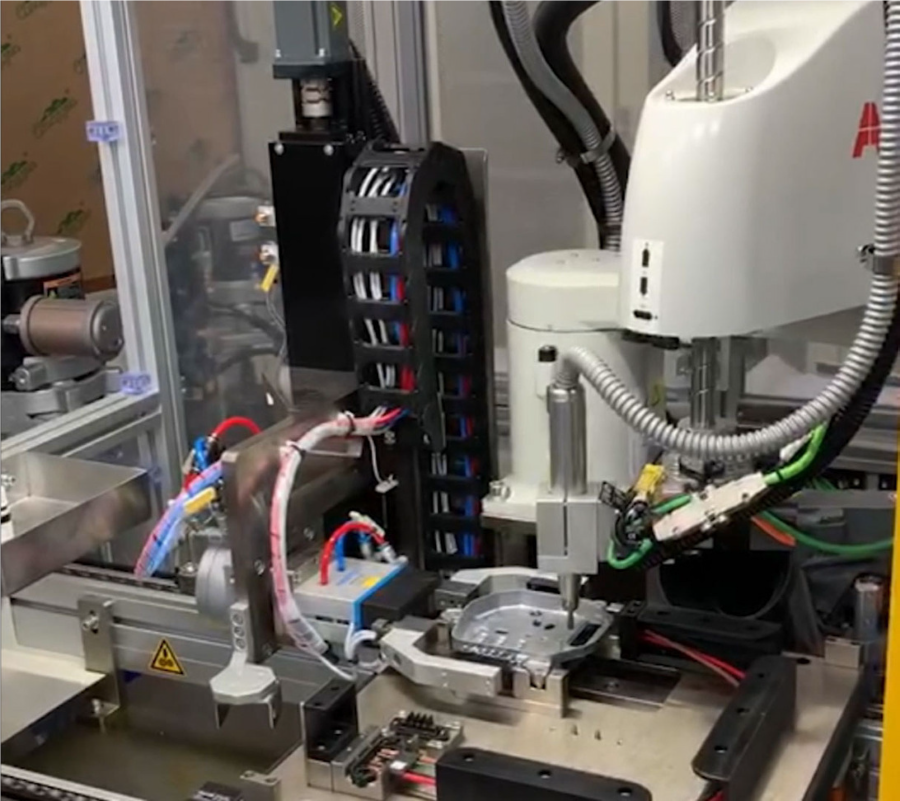
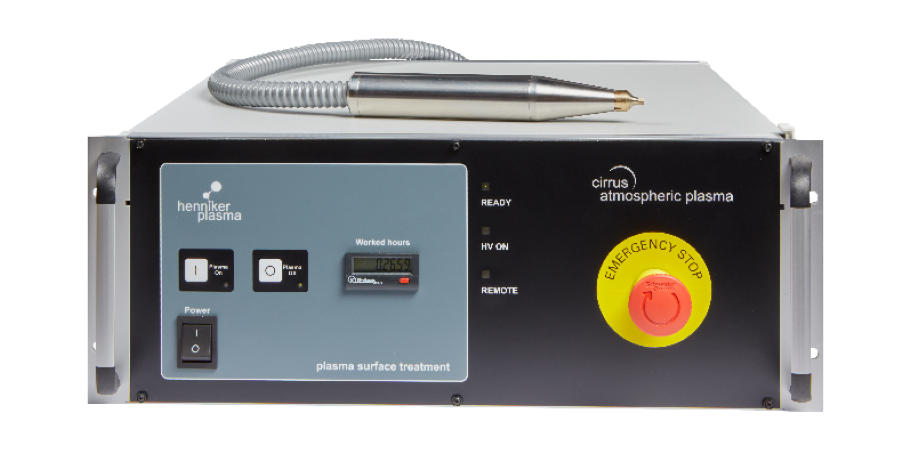
Advanced Vacuum Plasma Treatment
One of Henniker’s recent projects involved enhancing the paint adhesion on PDC sensors for a major car manufacturer. The PDC sensors are exposed to harsh environmental conditions and require a durable and uniform coating.
Using their Nebula system, Henniker Plasma developed a surface activation process that effectively increased the wettability and adhesion of the PDC sensors. The process was optimized to deliver consistent and reliable results for batch processing. Henniker Plasma collaborated with the client throughout the project to ensure their satisfaction and quality standards.
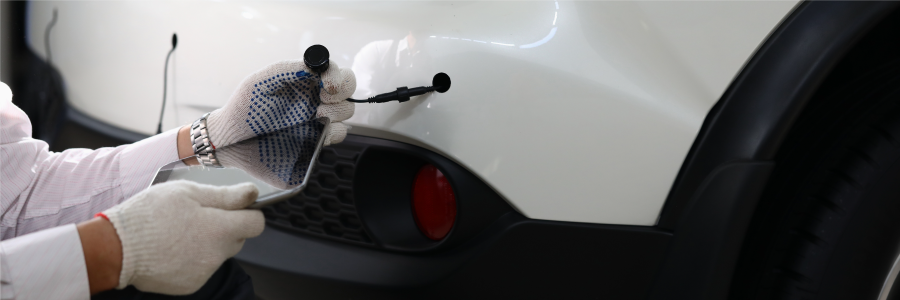
Treatment Parameters
The sensor membranes, made from aluminium alloy with an acryl powder coating, were placed into the manufacturer’s specialized coating tray for the treatment trials. Henniker performed two treatments of varying process times for comparison. They were treated for 180 and 90 seconds, respectively, at 100% power. The pressure was set at 0.3 mbar using air as the process gas. The customer requested a surface energy value above a 41 mN/n threshold.
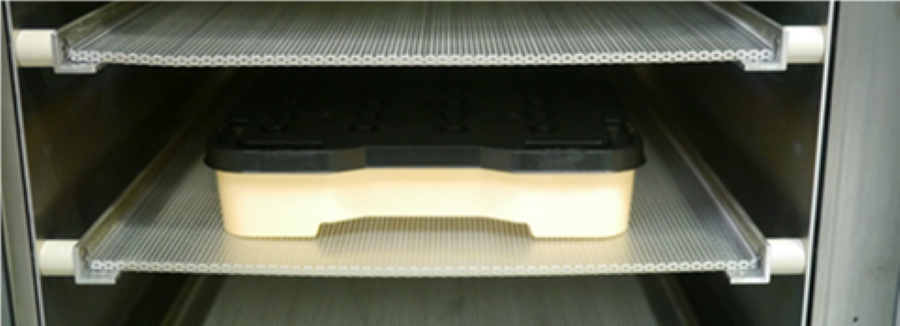
Contact Angle and Surface Energy Results
Contact angle tests are a method of measuring the wetting properties of a surface. They involve placing a drop of liquid on the surface and observing the angle formed between the edge of the drop and the surface. The smaller the angle, the more wettable the surface is. Tests can be conducted on various materials to compare their hydrophobicity and hydrophilicity.
Contact angle measurements of the sensor membrane protruding above the tray cover were made in order to determine the effectiveness of the plasma treatment. Three measurements were recorded from three separate sensors across the coating trays to determine treatment uniformity.
Plasma treatments of 180 and 90 seconds were analyzed, and each produced a measured reduction in contact angle; the 90-second treatment increased the surface energy to 56 ± 1 mN/m, sufficiently above the required 41 mN/m threshold set by the customer. The low degree of error from each result indicates the plasma treatment was uniform across the whole coating tray. Ageing tests demonstrated that slight hydrophobic recovery occurred, with both treatments surface energy values remaining above the 41 mN/n threshold 24 hours post-treatment.
Crosshatch Test Results
The crosshatch adhesion test (DIN EN ISO 2409) is a widely used method for determining the coating adhesion and is a simple and effective way to evaluate the quality of the paint. The test involves making a series of cuts on the painted surface and then applying a tape to peel off any loose paint. The process samples were prepared in different ways: without mechanical abrasion, with mechanical abrasion (scotch bright), and after plasma treatment. The client then tested and verified the samples using the crosshatch test method. The samples were rated based on the percentage of paint that remained on the surface after the test.
The crosshatch test-cut method used clearly demonstrated the enhanced bonding to the plasma activated surfaces after treatment.
Henniker provided the customer with a Nebula Advanced Plasma System, which included an additional barcode scanner for traceability, able to deliver a uniform increase in surface energy across the whole array of sensors in under five minutes. They were very satisfied with the outcome and reported enhanced performance and reliability of their sensors.
For more information on Plasma Treatment for the automotive industry visit: Reducing Adhesion Failures in the Automotive Industry - Henniker Plasma (plasmatreatment.co.uk).
*All images courtesy of Henniker Plasma.
Looking for a reprint of this article?
From high-res PDFs to custom plaques, order your copy today!