Improving Water Resistance of Water-Based Coatings Using Reactive Surfactants, Part 2
Reactions, Test Protocols, and Surfactant Properties

Davizro / iStock / Getty Images Plus, via Getty Images.
Picking up from last month’s column, we will continue with the study of using a reactive surfactant to create a styrene-acrylic emulsion. This month we will cover testing protocols and our first emulsification process. In future articles, we will cover some process changes, how the incorporation of the reactive surfactant changes the properties, and finally some scrub test results showing improved water resistance of the resin.
Coagulum/Clot Content
The finished emulsions were filtered through a 200-mesh screen to collect the filterable solids. Coagulum/clot adhering to the agitator, thermocouple, and reactor were also collected. The coagulum/clot content of the latex was determined by gravimetric method according to ASTM D1489.
Solid Content
The solid content of the latex was also determined by the gravimetric method according to ASTM D1489.
Particle Size
Average particle size of latexes was determined in a Zetasizer NS from Malvern.
Mechanical Stability
The mechanical stability of the emulsions was performed according to ASTM D1417.
Critical Coagulation Concentration
The critical coagulation concentration (CCC) of the emulsions was performed by titrating the dispersion with 0.1-wt% solids with a 1 mol/L CaCl2 solution and measuring the resultant particle size. The onset of the increase in particle size is the CCC.
Incorporation of the Reactive Non-Ionic Surfactant
The incorporation of the reactive non-ionic surfactant was estimated measuring the amount of free surfactant in the emulsion by high-performance liquid chromatography (HLPC).
Paint Formulation
The paint formulation we used had pigment volume concentration (PVC) of 30%, estimated VOC around 25 g/L, and its ingredients are presented in Table 1.
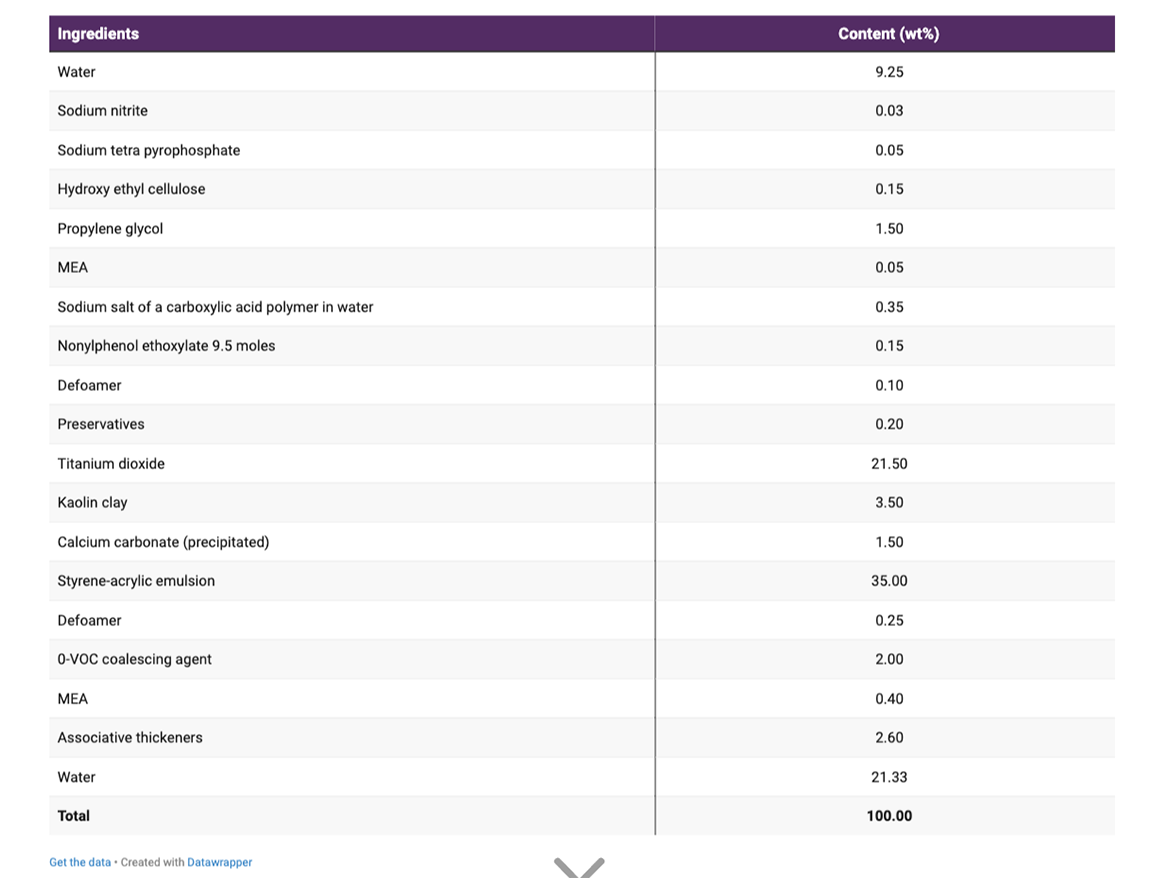
Wet Scrub Resistance
Paint films were applied at a wet thickness of 180 mm (~7 mils) to polyvinyl-chloride panels by using a film applicator. Films were dried for 7 days at 25 ± 2 °C and 60 ± 5% RH. The wet scrub resistance test was performed according to the ASTM D2486. The data shown is an average of six repeated measurements for each paint.
Results and Discussion
Properties of Reactive Non-Ionic Surfactant
The first part of these experiments was to develop a reactive surfactant to replace at least part of conventional surfactants used in emulsion polymerization. This was to improve the water resistance of the final coatings.
The starting point of this project was to understand whether the conventional anionic surfactant or the conventional non-ionic surfactant was more incompatible with the emulsion resins used in architectural coatings and, due to this, prone to migrate and segregate.
To understand this, the relative energy difference (RED) between the Hansen Solubility Parameters of each type of surfactant used in emulsion polymerization and resins used in architectural coatings was evaluated. Conventional anionic surfactants based on lauryl-ether sulfate, and conventional non-ionic surfactants based on ethoxylated-lauryl alcohol were used in these evaluations. In this case, a RED value lower than 1 means that the surfactant is compatible with the latex, while a RED value higher than 1 means that the surfactant has poor compatibility or is incompatible with the latex and the higher this value, the higher the incompatibility between the surfactant and the latex. Figure 1 shows the RED values for vinyl-acrylic and all-acrylic latexes.
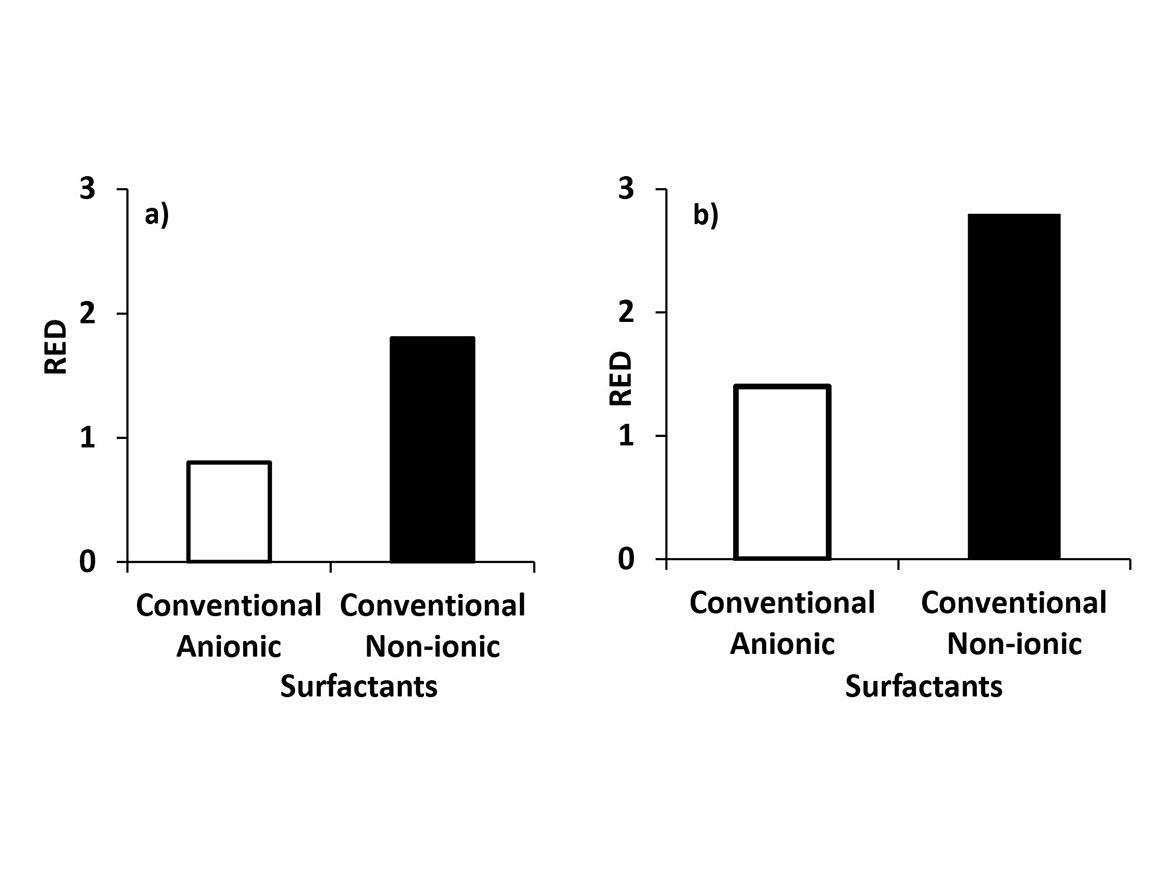
According to these results, the non-ionic surfactant presented higher values of RED being more incompatible with typical resins used in architectural water-based paints than the anionic surfactant, and due to this, a reactive non-ionic surfactant was synthesized in this work. Its properties are presented in Table 2. The properties of a conventional APE-free non-ionic surfactant used in emulsion polymerization, used as a standard in this article, are also presented in Table 2.
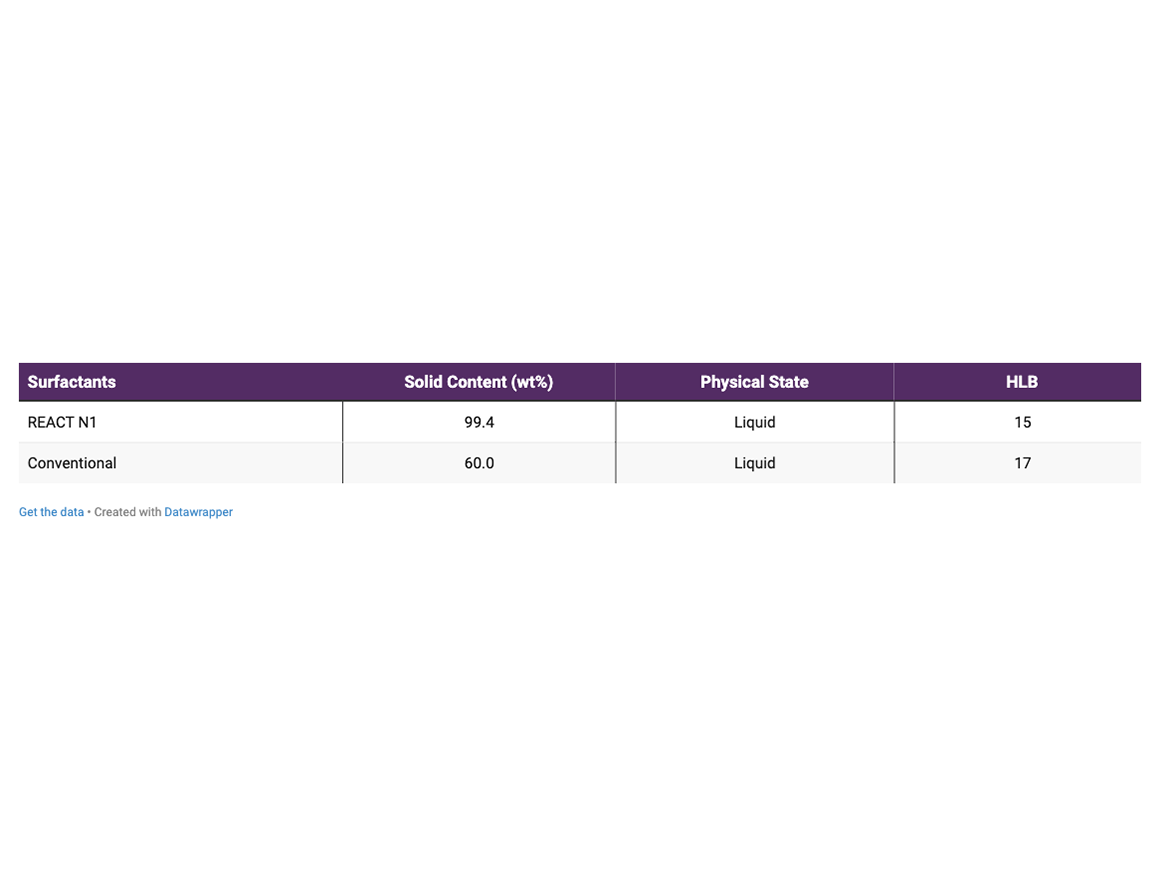
The reactive non-ionic surfactant is a prototype named A Reactive Non-Ionic Surfactant 1 (REACT N1). It has unsaturation in the beginning of its hydrophobic portion. Reactive surfactant with this configuration can adsorb and pack on the particle surface like a conventional surfactant before its co-polymerization with the main monomers. After its co-polymerization with the main monomers, it can stabilize the particles better than a reactive surfactant with unsaturation in the hydrophilic portion of the surfactant.
REACT N1 has solid content higher than 90 wt%, is a liquid at room temperature, and has HLB about 15. The conventional non-ionic surfactant is also a liquid at room temperature, with a solid content about 60 wt%, and HLB of 17.
Curves of the surface tension as a function of concentration of a conventional non-ionic surfactant and REACT N1 are presented in Figure 2. These curves show that REACT N1 has lower critical micelle concentration (CMC) and surface tension at CMC than the conventional non-ionic surfactant. According to these data, REACT N1 behaves as a conventional surfactant before its co-polymerization, and is more hydrophobic and efficient for adsorbing and packing at air-water interface than the conventional non-ionic surfactant.
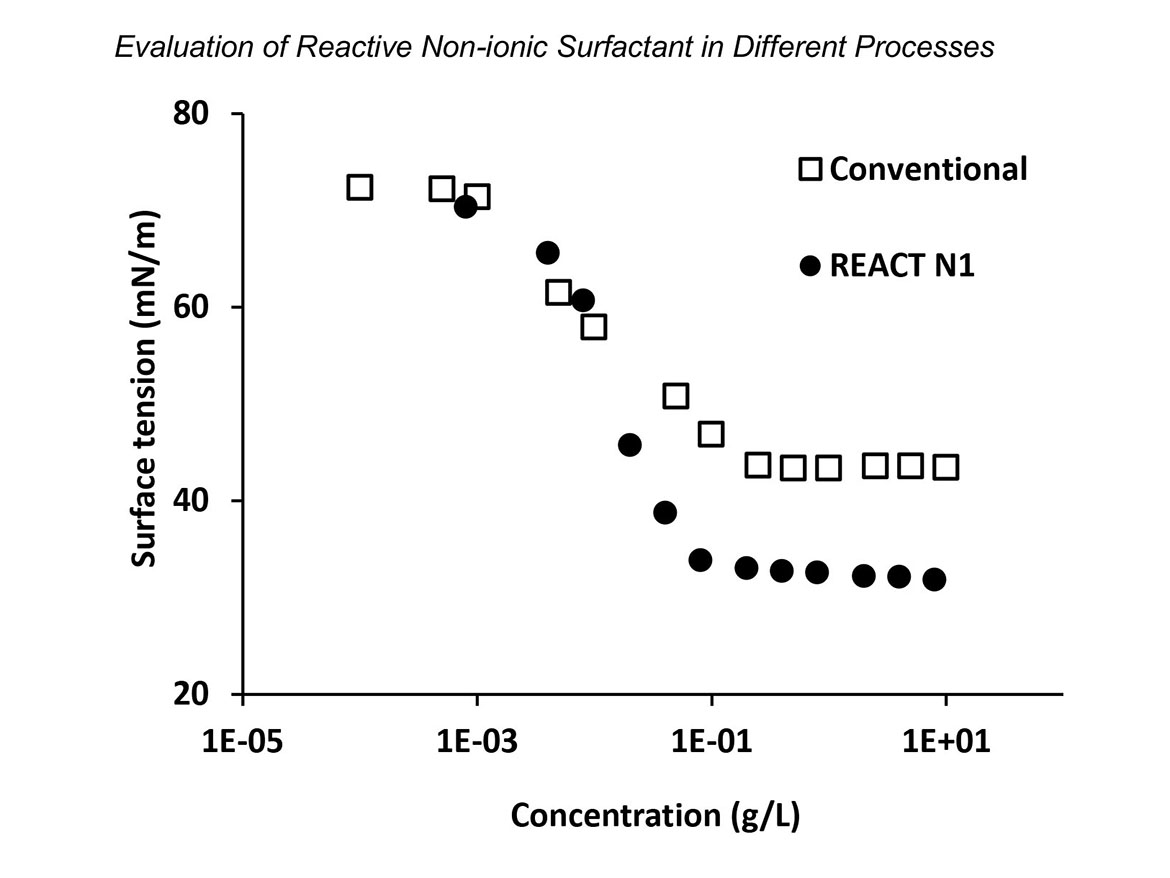
References
- Vanderhoff, J.W.; Bradford, E.B.; Carrington, W.K. The Transport of Water through Latex Films, J. Polym. Sci. 1973, 41, 155-174.
- Aramendia, E.; Mallégol, J.; Jeynes, C.; Barandiaran, M. J.; Keddie, J. L.; Asua, J. M. Distribution of Surfactants near Acrylic Latex Film Surfaces: A Comparison of Conventional and Reactive Surfactants (Surfmers), Langmuir 2003, 19, 3212-3221.
- Aramendia, E.; Barandiaran, M. J.; Grade, J.; Blease, T.; Asua, J. M. Improving Water Sensitivity in Acrylic Films Using Surfmers, Langmuir 2005, 21, 1428-1435.
- Noyes, N. Non-Leaching Reactive Surfactants for Architectural Latex Binder, PCI,2018, 34, 36-41.
- Fithian, P.; O’Shaughnessy, M.; Lubik, M.; Mark, S. Redox for Main Polymerization of Emulsion Polymers, PCI, August 2017.
Looking for a reprint of this article?
From high-res PDFs to custom plaques, order your copy today!