Improving the Water Resistance of Water-Based Coatings Using Reactive Surfactants
Part 1

Davizro / iStock / Getty Images Plus, via Getty Images.
In this and the next few columns, I will be covering work done to improve the water resistance of water-based emulsions by replacing conventional emulsion surfactants with surfactants that will react into the polymer matrix. I would like to thank Juliane P. Santos, Bruno S. Dário, Natália F. de Paula, Larissa C. C. de Almeida, Camila O. Guimarães, Ana Carolina Alves dos Santos, Raquel da Silva, and Fabricio G. Pereira for their experimental work that will be included.
The replacement of conventional surfactants with reactive surfactants in emulsion polymerization is a promising strategy for improving the water resistance of water-based coatings. However, the appropriate use of reactive surfactants in emulsion polymerization to balance stability and water resistance is still a challenge. Optimizations of the formulation and process variables are usually required to maximize the incorporation of reactive surfactants in the latex particles along the polymerization reaction in order to improve the water resistance of the final coatings.
In this work, the properties and application of a new reactive non-ionic surfactant will be presented. The molecule was designed to react with the key monomers used in emulsion polymerization. It was also made to have a surface activity similar to conventional non-ionic surfactants. The effect of the surfactant content, initiator type, and polymerization temperature on the incorporation of the reactive non-ionic surfactant in styrene-acrylic latex will be explored. Optimized formulation and process allowed the incorporation of 70-85% of the reactive non-ionic surfactant in latex particles of 80 nm, while using low content of the reactive non-ionic surfactant.
Latexes polymerized with the reactive non-ionic surfactant presented excellent mechanical stability and generated less clot in the reactor in comparison to latexes polymerized with conventional non-ionic surfactants. Semi-gloss paints formulated with the latexes polymerized with the reactive non-ionic surfactant presented up to 90% higher wet-scrub resistance than paints formulated with a styrene-acrylic latex, which is considered a benchmark in water resistance.
To the best of our knowledge, the group of Professor Vanderhoff was a pioneer in observing that diffusion of water in coalesced films of water-based emulsion resins stabilized only by reactive stabilizer was similar to that of polymers obtained from polymerization routes that do not use surfactants. Additionally, the diffusion of water in coalesced films of styrene-butadiene latex stabilized by conventional surfactants was 30-times higher in comparison to the same latex previously washed out to remove the conventional surfactants.
These results are interesting since they showed that conventional surfactants used in emulsion polymerization contribute to the poor water resistance of latex films and water-based coatings. Moreover, these results suggest that replacing conventional surfactants with reactive surfactants is a promising strategy for developing water-based emulsions and water-based coatings with water resistance close to solvent-based coatings, especially for coatings applications that require outstanding water resistance such as exterior architectural paints, floor coatings, and adhesives.
One important challenge for developing reactive surfactants is to choose an un-saturated group with appropriate reactivity with the main monomers. Other challenges related to the use of reactive surfactants are to quantify their incorporation on latex particles, and develop emulsion polymerization processes that maximize their incorporation, while using a low dosage of reactive surfactants.
This work comprehends the development of a reactive non-ionic surfactant with un-saturation in the hydrophobic portion of the surfactant, a method for quantifying the incorporation of the reactive surfactant in latex particles, and the effect of different processes on the incorporation and properties of latexes and paints.
Experimental Section
Materials
Industrial-grade inhibited monomers and potassium persulfate (99 wt%) were used in the polymerizations with thermal initiation. A formaldehyde-free sulphur-based reducing agent and potassium persulfate were used as the reducing agent and oxidizing agent, respectively, in the polymerizations with redox initiation.
The conventional anionic surfactant used in all polymerizations was a sodium salt of sulfated fatty alcohol ethoxylate (28% in water, 0.27 g/L CMC). The conventional non-ionic surfactant used in the emulsion polymerizations was a fatty alcohol ethoxylated, (HLB 16.9, cloud point 80 °C, 60% in water, 0.64 g/L CMC). The reactive non-ionic surfactant used in the emulsion polymerizations was named REACT N1 (REACTive Non-ionic surfactant 1).
Industrial-grade monoethanolamine (MEA) was used to neutralize the emulsion resins. All the materials employed in paint formulations were used as received.
General Procedure for Emulsion Polymerizations
Emulsion polymerizations were performed in a 1-L cylindrical glass reactor. Polymerizations were conducted at 60 ± 5 °C and 80 ± 2 °C. The monomeric composition and formulations used in the main polymerizations are described in Tables 1 and 2, respectively.
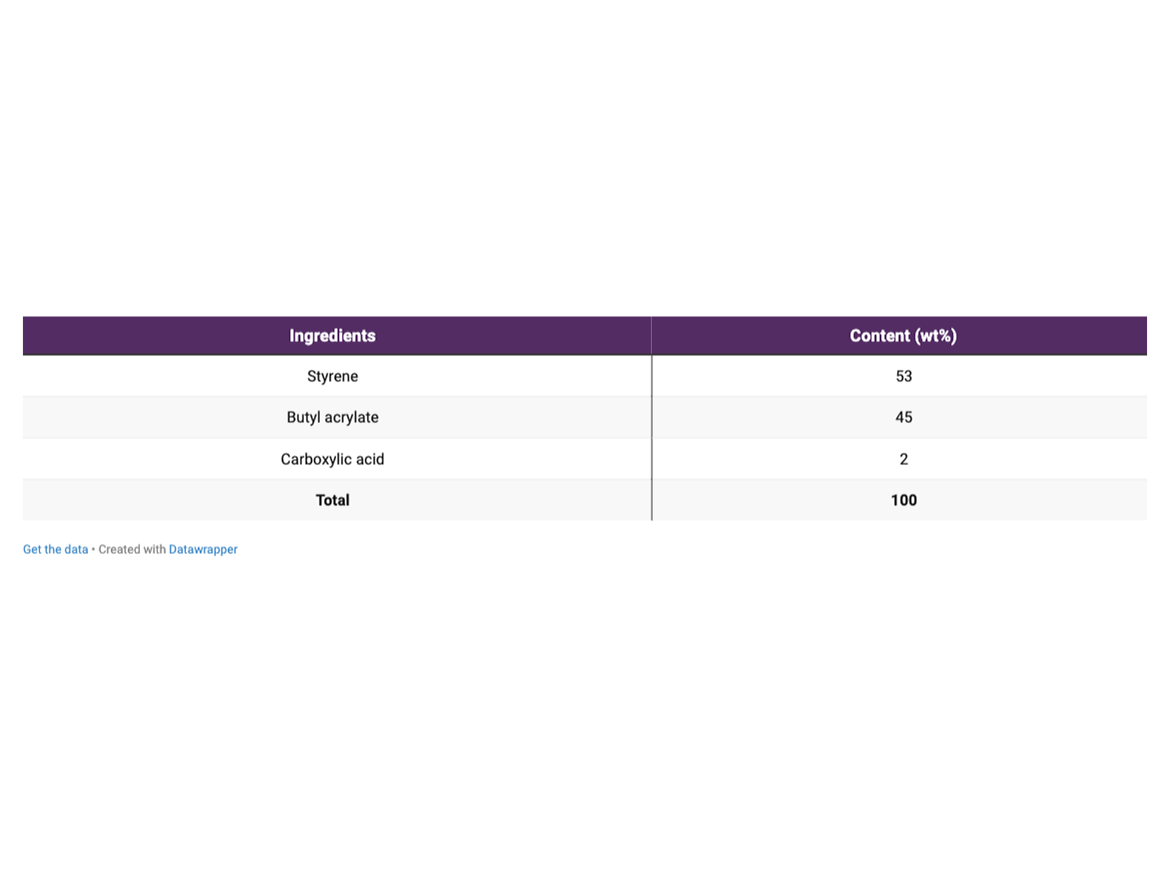
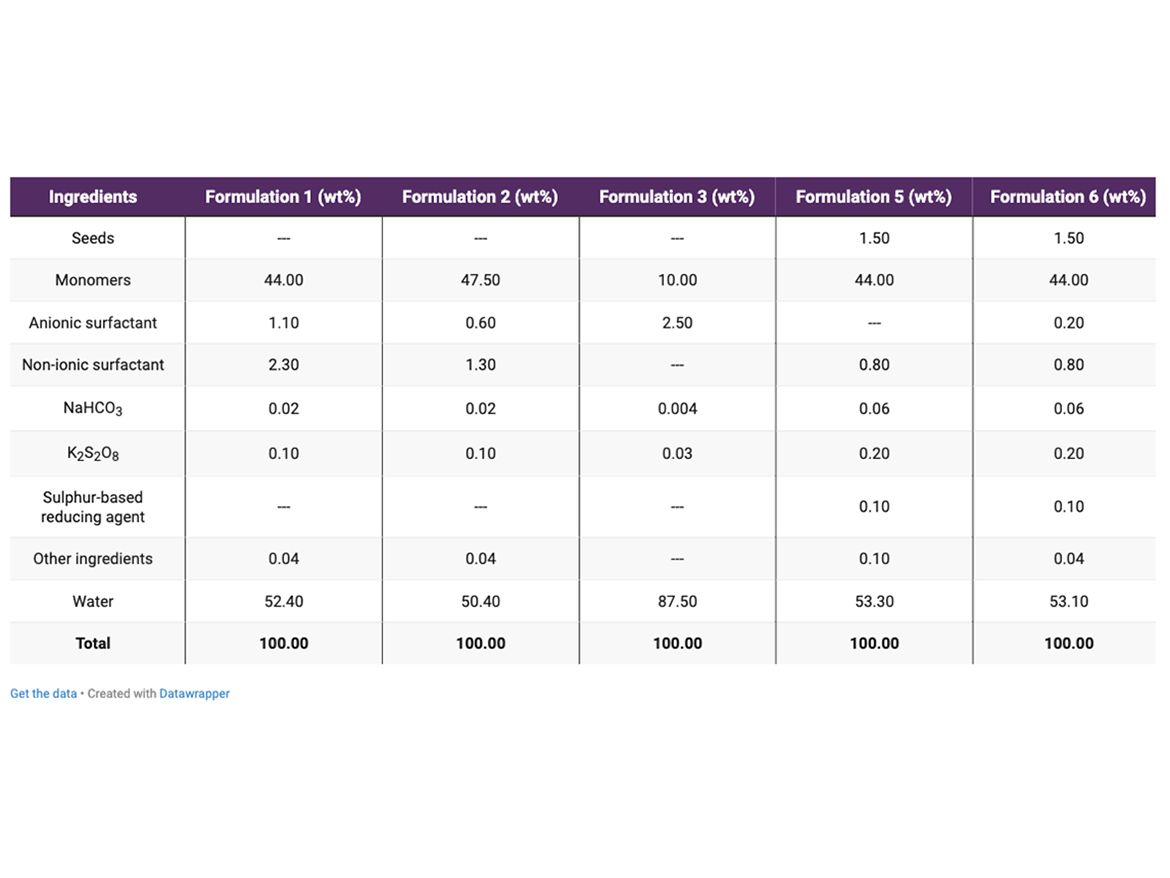
All emulsion polymerizations were performed using the active content of anionic and non-ionic surfactants described in Table 2.
Formulations 1 and 2 followed Process 1, while Formulations 3 to 6 followed Process 2. Formulation 3 shows the preparation of seeds generated in the first step of Process 2. Formulations 5 and 6 were performed according to the second step of Process 2. The general discussion about the differences between Process 1 and Process 2 will be presented in the next column.
For more information, e-mail Michael.Praw@us.indorama.net.
Looking for a reprint of this article?
From high-res PDFs to custom plaques, order your copy today!