Influence of Functional Monomers on Latexes and Coatings
The difficulty during development is not generally getting an appropriate formulation - the big problem is the optimization of the final formula to obtain high film property requirements. This report shows that the copolymerization of small quantities of functional monomers in a normal core/shell formulation can improve certain properties of binders and coatings.
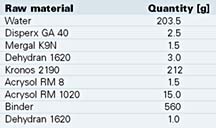
Experimental
Small quantities of functional monomers were used either in the core or in the shell for the polymerization of a formula containing acrylics and the vinylester of versatic acid. Therefore, different emulsions were produced, and one after the other was added into the reactor. We used an anionic phosphate ester as surfactant. The polymerization was done at 80 deg C, and in the post reaction the temperature was increased to 90 deg C. After polymerization we measured the content of coagulum by filtering the dispersion through a 100m filter. A film was produced and dried at 50 deg C. The water uptake was determined by storing the film for 24 hours in water. The particle size was measured in a Coulter N4 plus analyzer. Table 1 contains a typical formula for a wood coating. With these coatings we determined the blocking resistance.
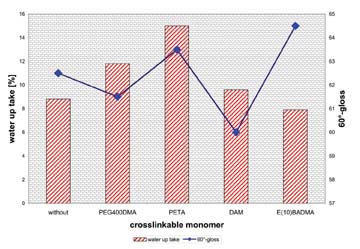
Results and Discussion
The original latex showed a particle size of 108 nm. The water uptake of the dried film was below 10%, and the storage stability of the formulated coating was excellent. It was important to increase the blocking resistance and the gloss of the coating. To optimize these properties, we first replaced the phosphate-containing surfactant with different polymerizable types. This led to an increased water resistance of the coatings, caused by a reduction of the water uptake of the film. Due to a strong increase in the particle size, the gloss of the coatings was unacceptably low. Poor storage stability and high coagulum content also eliminated these raw materials from further studies.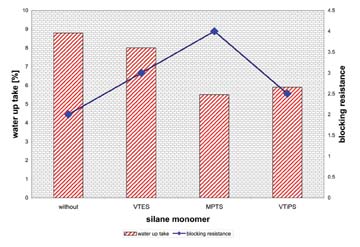
We clearly saw an increased blocking resistance at a constant particle size. Only with polyethyleneglycol 400 dimethacrylate (PEG400DMA) the particle size increased to 150 nm and is a little bit higher. The values from water uptake of the dried films and the gloss of the formulated coatings (Figure 2) were not affected. The storage stability of all coatings was acceptable - the viscosity of all coatings remained constant after a storage time of 14 days in an oven at 50 deg C. The coagulum content was approximately 0.2%, which is similar to systems without crosslinkable monomer.

In the next step we looked at silane monomers. Silane monomers are known to increase the wet adhesion, or the scrub resistance, of paints3. Figure 3 shows the water uptake and the blocking resistance of different silanes copolymerized in the core of the original dispersion.
All silanes that were used, vinyl triethoxy silane (VTES), (3-methacryloyloxy propyl) triethoxy- silane (MPTS) and vinyl triisopropoxy silane (VtiPS), led to improvements. Although the particle sizes remained constant, the gloss of all coatings increased. In contrast to the above-mentioned crosslinkable monomers, the silanes that copolymerized in the shell showed a much lower influence. The storage stability was also acceptable for the silanes. When measuring the content of coagulum, the methacrylic silane had a very high quantity.
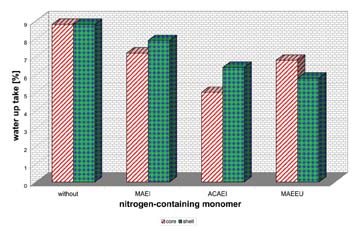
In the last step we used nitrogen-containing monomers. Such monomers are also known to optimize the wet adhesion and the scrub resistance of paints4. We tried 1-(2-methacryloxethyl)imidazolidin-2-one (MAEI), N-(2-allylcarbamato) aminoethyl imidazolidinone (ACAEI) and methacrylamido ethylethylene urea (MAEEU). Figure 5 shows the water uptake of these monomers, copolymerized either in the core or in the shell.
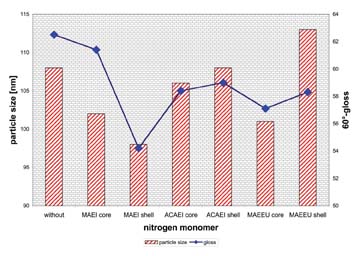

Conclusion
The use of functional monomers in core/shell latexes increases the properties of the binders and of the formulated coatings. While crosslinkable monomers are efficient in the shell of these latexes, silane monomers need to be copolymerized in the core to increase the parameters. Nitrogen-containing monomers are affecting the blocking resistance when copolymerized in the core or in the shell, but they also reduce the gloss of the coatings, while reducing the particle size. The different results of these monomers are shown in Figure 7.For more information, contact Dr. Christof Arz, Collano AG, CH-6203 Sempach-Station, Switzerland; e-mail christof.arz@collano.com.
This paper was presented at the 7th Nurnberg Congress, European Coatings Show, April 2003, Nurnberg, Germany.
References
1 BASF, EP 0 184 051; BASF, EP 0332 011; Rohm & Haas, DE 28 11 4812 Tradename Veova, Resolution
3 Wacker, DE 43 06 831, Development results Resolution
4 Rohm GmbH, DE 39 02 555; Rohm GmbH, EP 0379 892; Rohm & Haas, US 5 212 225; Nacan Products; EP 0 383 592
Looking for a reprint of this article?
From high-res PDFs to custom plaques, order your copy today!