Solving Temperature Issues Found in Fresnel Reflecting Solar Concentrators
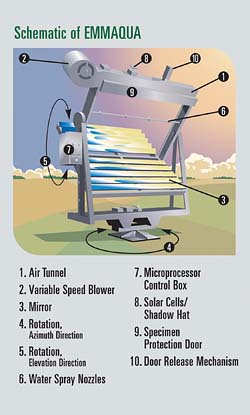
However there is one catch, the prospect wants greater assurance that the materials you have selected will stand the test of time...and they want the results within the next four months. In particular, they want you to further validate the durability of plastics used in your product when it is subjected to extreme levels of direct UV light.
True enough, the materials used in your formulation have already been subject to numerous and extensive UV light tests in a state-of-the art xenon weathering instrument. And while the manufacturer said they were impressed with these testing methodologies and corresponding results, they also want an outdoor "real world test, just to be sure." Of course you say "no problem" and make arrangements to get back in touch over the next few weeks to let them know what you're doing.
Obviously you want some weathering data, and a Fresnel reflecting solar concentrator, such as the EMMAQUA® test from Atlas Weathering Services Group, has proven to provide great correlation for your product over the years. However, the formulation change is not completed until the end of the summer and you really want summer conditions to "test" your coating. A standard EMMAQUA would only provide cooler, winter temperatures.
In addition to this, of course, there are other challenges with this standard testing methodology that delineate control of temperatures such as temperatures too high for temperature-sensitive thermoplastics, changes in environmental patterns that occur during the day and maintaining constant temperature at night. All these challenges pose serious preventive barriers to your current task, and there appears to be serious doubts about your ability to address your blockbuster prospect's request within four months. So you thought!
As you look at developments that have transpired in the testing industry, it becomes evident that strong progress has been made to address temperature control issues in outdoor accelerated weathering equipment - developments that greatly improve repeatability and reproducibility of outdoor accelerated exposures in environments while simultaneously offering controls that broaden the range of samples that can be tested.
For example, with the new temperature-controlled EMMAQUA, new patented technology from Atlas Weathering Services Group, you can now set summer test temperatures over the winter months so accelerated testing can proceed and you can get to market faster. You can now get a one-year equivalent of UV over three to four months in the winter time, but at summer test temperatures.
With this technology, perhaps there is a chance you can meet your new prospect's request after all! To do so, though, you will need to consider four new testing approaches that provide a dynamic range of testing parameters to decrease testing timelines, while also delivering exceptional levels of repeatability and reproducibility. They include the following items.
-
Static Temperature Control - helps overcome the effects of starting tests at different times of year.
Dynamic Temperature Control - approximates intermittent temperature patterns found in natural exposures on an accelerated test.
Night Temperature Control - approximates summer nighttime temperatures during winter exposures.
Variable Irradiance - enables temperature-sensitive materials to maintain stability in extreme accelerated outdoor weathering concentrators.
Static Temperature Control allows the user to select a test temperature and maintain that temperature throughout the exposure or the duration of the test. This feature greatly reduces the temperature intermittency effects caused by clouds as well as the difference found when starting tests in different seasons. It can also maintain consistent sample temperatures throughout the day, eliminating the difference between cool morning and hot afternoon ambient air temperatures.
If one were to conduct an exposure on an EMMAQUA during the summer months in Arizona, the specimens would have a relatively high test temperature due to the cooling air being around 100+ °F. If the same person were to conduct an exposure of like specimens in the winter, the cooling air would be much lower, perhaps 50 °F to 60 °F. The result would include a lower specimen test temperature, which, depending on the material, could be different than that seen in the summer exposure.
Static temperature is controlled in a similar manner to a thermostat in your home. A controller is programmed by the operator to the desired temperature, and a sensor, such as a test material with an imbedded thermocouple, is mounted in the exposure target area. The controller speeds up or slows down a cooling blower if the target temperature fluctuates upward or downward. This is how the target board exposure maintains the "set" temperature throughout the day and throughout different seasons.
Dynamic Temperature Control uses a remote sensor to define the "Set Point" temperature for the controller. This can be a black panel, the hood of a car, a section of a roof or a sample on a static rack. As the remote sensor responds to the environmental patterns during the exposure period, these same patterns are duplicated on the target area. Additionally, the sensors can be linked in a "chain" or "daisy" configuration. When used with a temperature offset inserted in the controller, replicate specimens can be tested at different temperatures while maintaining the environmental patterns of the exposure period.
The standard EMMAQUA uses a single-speed blower, and the specimen temperature is simply the result of whatever the ambient air temperature is at the time of exposure. This does not allow the researcher to test materials at different temperatures or to duplicate the temperatures found in an end-use configuration. It is often the case that products see a wide and dynamic set of temperatures while in service, and a standard EMMAQUA cannot replicate this dynamic profile.
A key element to this technology is that a remote temperature sensor establishes the set point for the controller. This enables the controller to compare the temperature on the target exposure area and the remote sensor and adjusts the cooling blower speed until the target sensor temperature equals the remote sensor temperature.
Night Temperature Control counteracts the heat absorbing power of the night desert sky and low winter nighttime sample temperatures. When used in conjunction with the other temperature-controlled exposures, specimens can be tested in the winter, but experience the same temperature profile, both the day and nighttime, of a summer exposure.
Night temperatures in the desert often approach freezing in the wintertime. When specimens receive a water spray, the cold temperature may affect the chemistry in a different way than would be seen during the warm summer months. This, and the simple fact of the cold night temperatures, can very well lead to different results seen in summer and winter exposures on the same specimens.
Night temperature control concentrators use special heater platens that are mounted behind specimens on the target area. The heater platens are connected to a thermostat with a set temperature, and a heating system is connected to a timer that turns on at night and off in the morning. Specimens in the target area receive radiative, convective and conductive heating through the unexposed side, and users can specify time, duration and set temperature of heating platens.
Variable Irradiance allows temperature-sensitive materials to be exposed to an accelerated test without suffering from elevated temperature effects. By using more mirrors in the winter months and fewer mirrors in the summer months, dark thermoplastics can be tested year round. It also permits investigation of effects from different solar irradiance and temperature levels while maintaining the natural intermittent patterns of light and temperature.
The very hot air temperatures found in the summer desert can cause unrealistic thermal effects on temperature-sensitive plastics. A standard EMMAQUA-type exposure can easily cause temperatures beyond the heat deflection temperatures, causing warping and deformation. This makes it difficult to perform instrumental gloss and color readings.
The number of mirrors installed on the solar concentrator should be adjustable to between two and 10, and set accordingly depending on the exposure requirements of the material. The UV radiant exposure is calculated and reported according to the number of mirrors. The reduction in solar concentration results in reductions in heating of materials and allows temperature-sensitive material to be successfully exposed. Furthermore, the number of mirrors may be changed at different times of the year to account for seasonal variances in irradiance. For instance, more mirrors during colder winter exposure and fewer mirrors during hotter summer exposure.
Conclusion
Each of these new technologies has the ability to solve some of the issues concerning the lack of temperature control in past outdoor accelerated exposures. When they are combined, they offer powerful tools to researchers to gain rapid and accurate information about their materials. The ability to control the exposure temperature eliminates the variability seen in outdoor testing to date, and provides for consistent, year-round testing.With the control of solar irradiance, moisture and now sample temperature, there are several innovative solutions controlling the primary factors that degrade materials. These innovations greatly improve the repeatability and reproducibility of outdoor accelerated exposures, a revolution in weathering testing.
Looking for a reprint of this article?
From high-res PDFs to custom plaques, order your copy today!