Due to their high chemical stability, low price, excellent balance of physical properties, possible recycling, etc., the amount of polypropylene (PP) and TPO consumed by automotive parts, household electrical appliances and molded general goods businesses is increasing. However, PP and TPO are materials with low surface energy that make painting and adhesion problematic, hence chlorinated polyolefin (CPO) has found wide use as an adhesion promoter. Solventborne CPOs have been traditionally used, and many studies have been conducted to clarify the adhesion mechanism of the solventborne CPO to TPO substrates.1-8 Excellent adhesion between TPO substrates and CPO can be obtained as the result of good wetting and higher dispersion interaction, which are affected by the properties of CPO's chlorine content, crystallinity, melting temperature, molecular weight and its polydispersity.1-5 Solvent composition is also one of the most important factors that determines the adhesion property by dissolving CPO and swelling rubbers near the surface of TPO, leading to morphological changes in the TPO surface and in the possible entanglement between CPO molecules and swelled rubber.6,7 In addition, baking time and temperature are also believed to be important, which affect the surface wettability of the CPO layer and the extent of penetration and interdiffusion of CPO into TPO. Baking may also rearrange the surface morphology of TPO, which can affect the surface adhesion.9,10
In recent years, waterborne coatings applied to TPO substrates have been widely studied for use as both interior and exterior automotive coatings as a result of increasing environmental awareness. Waterborne coatings consist of a colloidal phase in the form of individual spheres dispersed in water, and have a different film formation mechanism from solventborne coatings.11 As the water evaporates, the spherical polymer particles are closely packed where a so-called "honeycomb" structure is formed after further evaporation of water and loss of the voids. The continuous coating film is finally obtained through deformation and coagulation of the particles by further heat treatment or use of coalescing agents. Traditional waterborne coatings used to be baked at 120 ºC (248 ºF) to compensate for the slow evaporation rate of water; high baking temperatures also helped produce good deformation and coagulation of the particles to obtain a continuous film coating.
Currently, the automotive industry is seeking waterborne coatings applicable to TPO substrates that coalesce well at baking temperatures as low as, or lower than, 80 ºC (176 ºF) in order to save energy costs and to avoid thermal deformation of TPO substrates at the higher temperatures. However, waterborne coatings tend to elicit cohesive failure within the coating layer because of the film formation mechanism,3 and this tendency becomes worse at lower baking temperatures. It is important to note that the swelling of rubber in TPO or diffusion of CPO into TPO can hardly be expected without the existence of solvent, therefore, the lack of solvent in waterborne CPO adhesion promoters makes it more difficult for them to obtain good adhesion to TPO substrates.
Chlorine-free adhesion promoters for TPO have also been attractive, and many studies have been reported of such use in automotive TPO parts' coatings.8,12 Current practical use of chlorine-free adhesion promoters seems to be limited to but a few cases, which seems at least partially due to their insufficient adhesion to TPO as measured under the current test condition utilized by automotive OEMs.
The goal of this study was to develop a new waterborne chlorine-free adhesion promoter for TPO substrates that is applicable at acceptable industry standards even at low baking temperatures. A series of adhesion promoters were prepared, and general properties, such as how crystallinity, melting temperature and degree of maleic and acrylic monomer modification of the polypropylene starting material affect coating adhesion to TPO and subsequent gasoline and humidity resistance performance, were investigated.
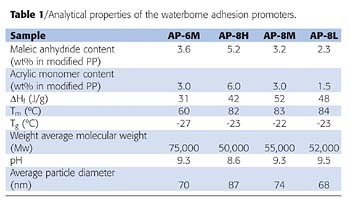
Experimental
For the preparation of waterborne, chlorine-free adhesion promoters, polypropylene was graft modified with maleic anhydride and other acrylic monomers in the melt state. In a flask attached with stirrer and condenser, 100 parts of the modified polyolefin was emulsified at 95 ºC with 20 parts of a nonionic surfactant, 18 parts of methylcyclohexane, 6.5 parts of morpholine, and 280 parts of water. After the evaporation of methylcyclohexane cosolvent and cooling down to room temperature, the solid content was adjusted to 30 wt% by addition of water. The residual amount of methylcyclohexane in the emulsion, determined by gas chromatography, was approximately 0.2 wt%. Four waterborne adhesion promoter samples were prepared; physical properties are shown in Table 1. In Table 1, the sample nomenclature of L, M and H indicate the degree of grafted monomer contents (L, low; M, medium; H, high). Notably, AP-6M was observed to have a lower melting temperature than the samples AP-8L, AP-8M and AP-8H. While crystallinity of the waterborne adhesion promoters is discussed in more detail later in this paper, all four different waterborne adhesion promoters appear to possess much lower crystallinity than traditional maleic isotactic-PPs.
Weight average molecular weights (Mw) were measured with gel permeation chromatography (GPC, Tosoh, HLC8120GPC) against narrow molecular weight polystyrene standards. Maleic anhydride content and acrylic monomers content were measured with Fourier transform infrared spectroscopy (FT-IR, Jasco, FT-IR-350, resolution = 4 cm-1) and acid-base titration methods. The heat of fusion (∆Hf), glass transition temperature (Tg) and melting temperature (Tm) properties were measured with differential scanning calorimetry (DSC, Seiko Instruments, DSC6200, method: first heating; 30 to 200 ºC at 10 ºC/min., cooling; 200 to -60 at -20 ºC/min., second heating; -60 to 200 ºC at 10 ºC/min.). The ∆Hf was determined during the first heating scan, and Tg and Tm were determined during the second heating scan. GPC, FT-IR and DSC of the adhesion promoters were measured before emulsification. Particle size analysis was made with photon correlation spectroscopy (Malvern Instruments, Zetasizer 3000HSA).
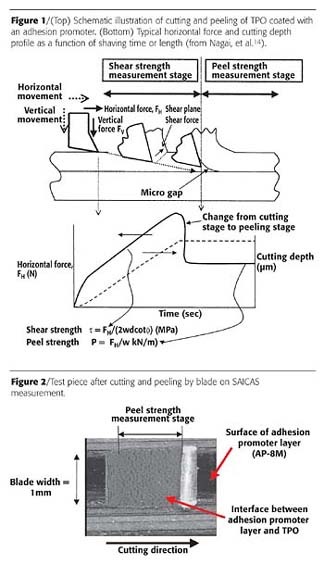
Test Methods
Peel Strength Measurement
Peel strength was measured on the Surface and Interfacial Cutting Analysis System (SAICAS, CN-20, Daipla Wintes) to investigate how the general properties of an adhesion promoter affect the adhesive strength to TPO substrate. The result was compared to the peel strength obtained from a tensile tester. It is well known that peel strength obtained from a tensile tester is not always consistent and does not always reflect the practical film performance, e.g., like high-pressure wash resistance. One of the reasons is that a traditional peel strength measurement using tensile testing can cause adhesion failure not only at the interface between TPO and the adhesion promoter but also at the interface between the topcoat and the adhesion promoter, or, alternatively, cohesive failure within the adhesion promoter or TPO substrate layers. On the other hand, SAICAS possibly enables a more reproducible measurement of the interfacial adhesive strength between an adhesion promoter and a substrate compared to a traditional peel strength measurement.13, 14The peel strength at the interface between the adhesion promoter and TPO can be measured when the depth of the blade is slightly changed stepwise or changed slowly at a constant rate, until the horizontal force decreases abruptly and becomes constant. It is also an advantage that SAICAS has a CCD microscope such that the location of cutting and peeling can be confirmed within the visualized interface of the adhesion promoter and TPO substrate. A peel strength is recorded when the horizontal force starts to become constant, which is also confirmed through microscopic observation that the blade reaches the interface. Peel strength is obtained by dividing the measured horizontal force by the blade width. Figure 1 (top) shows a schematic shaving method of SAICAS. Figure 1 (bottom) shows a typical recorded result of horizontal force and cutting depth profile as a function of shaving time or length. Figure 2 shows an example of the test pieces after cutting and peeling by the blade.
Sample Preparation for SAICAS Analysis
The adhesion promoters were sprayed onto TPO plates (TOPLA NY-10) whose polymer is for injection mold use. The TPO plates, coated with the adhesion promoters, were dried at 80 ºC for 5 minutes, and then kept at room temperature for 10 minutes. The coated TPO was again heated at either 90 ºC or 120 ºC for 20 minutes. The dried film thickness was approximately 10 to 15 µm.Sample Preparation for Tensile Peel Strength
The adhesion promoters were sprayed onto TPO plates (TOPLA NY-10), dried at 80 ºC for 5 minutes, and then kept at room temperature for 10 minutes. The dried film thickness was approximately 10 to 15 µm. A solventborne 1K polyurethane basecoat/solventborne 2K polyurethane clearcoat system was sprayed and baked at either 90 ºC or 120 ºC for 20 minutes. The dried film basecoat thicknesses were nearly 15 to 20 µm and those of the clearcoats were 20 to 30 µm, respectively. A cotton mesh fabric was attached to the clearcoats with a waterborne acrylic adhesive, and then cured at room temperature for three days. It was confirmed that the adhesive strength of the waterborne acrylic adhesive was sufficiently resilient for the peel strength test.Microscopic Studies
Each test piece for SAICAS measurement was also subjected to atomic force microscopy (AFM, Seiko Instruments, SPI3800N). The surface of the adhesion promoter layer was imaged with AFM in the dynamic force (tapping) mode to record the height and the phase images simultaneously (scanning area; 5 µm x 5 µm, cantilever; SI-DF20, resonance frequency; 134 kHz). Darker regions in phase images correspond to the regions with higher crystallinity. Root-mean-square roughness (RMS) was calculated from height image data.Surface Hardness
Glass plates were coated with the waterborne adhesion promoters using a Meyer bar #16, dried at 80 ºC for 5 minutes, then kept at room temperature for 10 minutes. The coated glass plates were again heated at either 90 ºC or 120 ºC for 20 minutes. The dried film thicknesses were from 5 to 6 µm. Hardness of thin adhesion promoter layers on the glass plates was determined with Dynamic Ultra Micro Hardness Tester (Shimadzu DUH-201S, test mode; for soft materials, setting force, 0.5mN; loading rate, 0.014220 mN/sec; hold time, 5 seconds; tip type, 115 three-sided pyramid; temperature, 23 ºC).Film Performance
TPO plates (TOPLA, NY-10) were sprayed with waterborne adhesion promoters and dried at room temperature for 10 minutes. The dried film thickness was approximately 10 to 15 µm. An OEM solventborne 1K polyurethane basecoat/solventborne 2K polyurethane clearcoat system was sprayed and baked at 90 ºC for 20 minutes. The basecoat dried film thicknesses were nearly 15 to 20 µm, and those of the clearcoats were 20 to 30 µm, respectively. Adhesive strength was determined with cellophane tape test according to JIS K5600-5-6 (method: crosshatch pattern with 100 squares, 2 mm square-sided, counting the number of remaining squares after each removal of the tape with 90º clockwise sample rotation after removal of the tape for each of 10 total trials). Gasoline resistance was defined as the time for defects, greater than 2 mm from the edge of the coated TPO, to appear. The coated TPO plates were soaked in a mixture of 90% synthetic regular gasoline and 10% ethanol after the edges of the coated TPO were cut in advance using a knife's edge. Humidity resistance was determined by following the above-mentioned cellophane tape adhesion test after being exposed to a 50 ºC, 98% relative humidity for 120 hours.Results and Discussion
Evaluation of Crystallinity
A PP raw material of lower Tm and crystallinity was graft modified to obtain AP-6M, while a PP of slightly higher Tm and crystallinity was used to obtain the AP-8L, AP-8M and AP-8H samples. Though the two PP raw materials utilized here have much lower crystallinity than a traditional isotactic-PP polymer, their crystallinities are quite similar. Therefore, it was expected that the relative degree of crystallinities of the adhesion promoters would vary as (AP-8L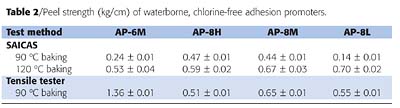
Peel Strength
Table 2 shows the peel strength of waterborne adhesion promoters determined by SAICAS, and the results at 90 ºC baking temperature were compared with the results from a traditional peel strength measured by a tensile testing measurement (180º peel).In the SAICAS measurement at 120 ºC, AP-8L, AP-8M and AP-8H showed higher peel strength than AP-6M. Comparison between AP-8L, AP-8M and AP-8H show that higher peel strengths were obtained with lower maleic anhydride and acrylic monomers contents. SAICAS peel strength from samples baked at 120 ºC was evidently related to sample crystallinity. In this case, the 120 ºC baking temperature was sufficiently higher than the Tm of all four waterborne adhesion promoters so that the adhesion promoters could sufficiently melt and wet a TPO surface. It was assumed that emulsified particles coalesced well after baking for sufficient entanglement of polymer chains at this baking temperature.
Although a 90 ºC baking temperature was nearer to but still higher than the Tm of all the adhesion promoters in this study, the peel strength of all four adhesion promoters was decreased when processed at the lower baking temperature. The baking temperature and time were probably insufficient for the adhesion promoters to melt, coalesce and wet the substrates at their maximum effectiveness. The film formation of AP-8L was obviously insufficient in particular, leading to a great decrease in peel strength. It was interesting to note that the AP-8H and AP-8M samples, of higher degree of modification than AP-8L, showed excellent peel strength at the 90 ºC baking temperature. Although AP-6M had the lowest Tm and should therefore in theory work better than the other adhesion promoters at lower baking temperatures, it showed a greater decrease in peel strength than either AP-8M or AP-8H. Peel strength obtained from SAICAS is supposed to highly reflect the interfacial adhesive strength between TPO and adhesion promoter, therefore it seems that higher interfacial adhesive strength can be obtained from waterborne adhesion promoters with higher crystallinity, as long as the adhesion promoters melt and coalesce sufficiently at a given baking temperature.
On the other hand, peel strength obtained from the traditional peel strength method using tensile testing showed a quite different trend compared to the SAICAS measurement results, as shown in Table 2. In this case, AP-6M showed the highest peel strength. The AP-6M has lower crystallinity and Tm than AP-8H, AP-8M and AP-8L, so interdiffusion with a topcoating and coalescence between the polymer particles are likely to occur easier, which should lead to a higher peel strength.
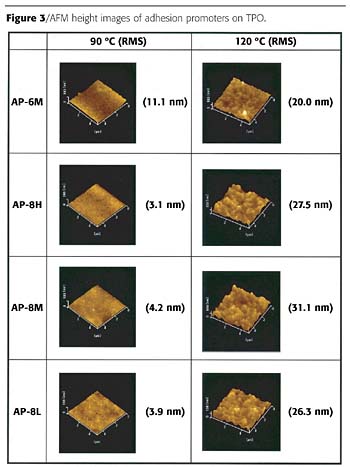
AFM Observation
Figure 3 shows AFM height images of adhesion promoters coated on TPO substrates. RMS values are also shown in the figure. All four waterborne adhesion promoters had a minimum film formation temperature lower than room temperature, and the surfaces of coated TPO were confirmed to be very smooth from an optical microscopic observation. However, it was observed using AFM that:- the use of the 120 ºC baking temperature resulted in relatively rougher adhesion promoter layer than 90 ºC baking;
- after a 120 ºC baking temperature, the roughness of AP-6M coating was smaller than AP-8H, AP-8M and AP-8L;
- at 90 ºC baking, there was almost no difference in surface roughness between the four different adhesion promoter films and that all surfaces were extremely smooth; and
- the differences in the degree of graft modification did not significantly alter the surface roughness.
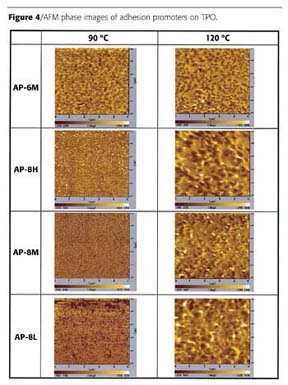
- highly oriented crystalline structures were not seen in any of the images;
- at a 120 ºC baking temperature, the crystalline surface regions were smaller and more evenly distributed in the AP-6M coating than in AP-8H, AP-8M or AP-8L coatings;
- crystalline regions in AP-8H, AP-8M and AP-8L were fewer and smaller at 90 ºC than produced at the 120 ºC baking temperature;
- at a 90 ºC baking temperature, darker regions in AP-6M seem to be larger than in the AP-8H, AP-8M and AP-8L coatings; and
- there was no significant difference in phase images of AP-6M produced by the 90 ºC and 120 ºC baking temperatures.

Hardness Testing
It was difficult to determine directly the degree of crystallinity of the waterborne adhesion promoters coated on TPO substrates by X-ray diffraction methods. The hardness of polyolefins is deeply related to their degree of crystallinity, thus the hardness was measured and its value was used to ascertain the crystallinity of the adhesion promoters. The Dynamic Ultra Hardness Tester is known as a useful instrument to determine the hardness of a thin coating layer. In this method, a thin coating layer is pressed by a tip with a constant pressing force and the displacement of the tip after a given period is recorded to determine the dynamic hardness. Dynamic hardness, DHT 115, is obtained by the following equation,DHT 115 = 3.8584 x P / D2
in which P is a pressing force (mN) and D is a tip displacement (µm). To eliminate the effect of a substrate, a hard substrate must be used in this method. Therefore, the waterborne adhesion promoters were coated on glass plates instead of TPO substrates and the same heat treatment was applied as with other experiments. The results are shown in Table 3.
The results showed that the order of the dynamic hardness was AP-8L > AP-8M
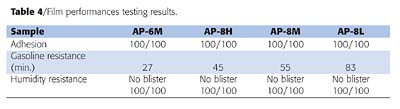
Film Performance
Table 4 shows the results of film performance testing of AP-6M, AP-8H, AP-8M and AP-8L coatings. There were no failures observed in the cellophane adhesive tape testing for any of the waterborne adhesion promoters, despite that there were clear differences in the measured peel strengths. Humidity resistances were also excellent in all cases. Even though the differences in their degree of crystallinity were small as mentioned earlier, better gasoline resistance was obtained when the crystallinity of the adhesion promoter films were higher.
It was found that a balanced film performance could be obtained from a waterborne adhesion promoter with higher crystallinity and Tm as long as film formation occurs at a given baking temperature. This result appears applicable to a general design for lower baking temperature coating systems by adjusting the crystallinity and melting temperature.
Conclusions
Waterborne, chlorine-free adhesion promoters were prepared varying the properties such as crystallinity, melting temperature and degree of maleic anhydride and acrylic monomer graft modification. From the results of the interfacial adhesive strength between the adhesion promoters and TPO substrates, it was found that a waterborne adhesion promoter with higher crystallinity exhibited stronger interfacial adhesive strength as long as it had efficient film formability at a given baking temperature. Also, a better gasoline resistance performance was obtained when the crystallinity of the waterborne adhesion promoter was higher. Therefore a balanced film performance can be obtained from a waterborne adhesion promoter considering Tm, degree of crystallinity, and baking temperature. This study was conducted mainly at 90 ºC baking temperature, but the results and the considerations should be applicable to the design of even lower baking temperature coating systems.Acknowledgements
The author would like to acknowledge all the staffs of Nippon Paper Chemicals Co., Ltd. involved in this study. The technical supports on SAICAS measurement were provided by Mr. Nishiyama of Daipla Wintes Co., Ltd. The technical assistance on AFM measurements by Dr. Kishi of Nippon Paper Industries Co., Ltd. is gratefully acknowledged. The author wishes to thank Dr. Schuman of the University of Missouri-Rolla for critically reading the manuscript and making helpful suggestions.References
1 Ryntz, R.A.; Britz, D.; Mihora, D.M. J. Ctgs. Technol. 2001, 73(921), 107.2 Aoki, Y. J. Polym. Sci. 1968, Part C, 23, 855.
3 Clemens, R.J.; Batts, G.N.; Lawniczak, J.E.; Middleton, K.P.; Sass, C. Prog. Org. Ctg. 1994, 24, 43.
4 Ellis, T.S. Polym. Eng. Sci. 2001, 41(12), 2065.
5 Mirabella, F.M.; Dioh, N.; Zimba, C.G. Polym. Eng. Sci. 2000, 40(9), 2000.
6 Schuman, T.; Thames, S.F. International Coatings for Plastics Symposium, 2004, Troy, MI.
7 Ryntz, R.A.; Xie, Q.; Ramamurthy, A.C. Waterborne, High-Solids, and Powder Coatings Symposium, 1994, New Orleans, LA. 8 Williams, K.A.; Germinario, L.T.; Eagan, R. International Coatings for Plastics Symposium, 2003, Troy, MI.
9 Everson, M.P.; Mikulec, M.; Schmitz, P. ACS Symposium Series, 1998, 694, 141.
10 Schmitz, P.J.; Holubka, J.W. J. Adhesion. 1995, 48, 137.
11 Martens, C.R. "Emulsion and Water-Soluble Paints and Coatings", Reinhold Publishing Corp. P.18, 1964.
12 Hintze-Bruning, H.; Borgholte, H. Prog. Org. Ctg. 2000, 40, 49.
13 Nakauti, H.; Takizawa, T.; Saito, S.; Ono, T. Proceedings of the third International RILEM Symposium, Feb., 2000.
14 Nagai, N.; Imai, T.; Terada, K.; Seki, H.; Okumura, H.; Fujino, H.; Yamamoto, T.; Nishiyama, I.; Hatta, A. Surf. Interface Anal. 2002, 34, 545.
For more information, contact Ken-ichi Fujino at ken.fujino@np-g.com.
This paper was presented at the 8th International Coatings for Plastics Symposium, June 2005, Troy, MI, sponsored by Paint & Coatings Industry (PCI) magazine and organized by Technical Conference Management.