Mass Flow Measurement in Varnish Production
KROHNE has developed a revolutionary patented technology known as
“Adaptive Sensor Technology” (AST).
Mixing, dosing and grinding are essential processes in
paint and varnish production. In order to ensure a high level of automation, it
is essential to be able to measure flows accurately and reliably. As some raw
materials used in the manufacturing processes are very expensive, product
wastage and equipment downtime can lead to considerable losses. This is doubly
annoying because the measuring technology currently available on the market can
effectively prevent or at least help prevent these losses. This is illustrated
in the example of BASF Coatings AG (Figure 1), who uses KROHNE’s Coriolis
flowmeters to detect leakages.
As the Coriolis principle allows an exact measurement of fluid and gaseous media, mass flowmeters are becoming increasingly popular. Coriolis measuring technology is already the second most common modern measuring method behind electromagnetic flowmeters and, together with ultrasonic flow measuring technology, boasts the fastest growth rates.

The media have viscosities of 7000 mPas and over, and
are generally also shear thinning; in other words, their behavior changes with
the flow rate. In addition to the high viscosity, DN 40 flowmeters also have to cope
with high pigment contents. Moreover, BASF Coatings did not want to risk any
further pressure loss by installing the flowmeter; otherwise, they would have
to increase the performance of the pump. BASF Coatings thus opted for the
OPTIMASS, a mass flowmeter that is virtually made for this application thanks
to its straight-tube design (Figure 3).
· less pressure loss;
· less abrasion;
· suitable even for large flow volumes;
· wide measuring range; and
· no risk of blockage.
Straight-tube meters are also easy to clean, self-draining and suitable for measuring high-viscosity media such as those processed at BASF Coatings because of their ideal proportions; i.e., a short measuring tube with a large inner diameter.

Every 90 seconds, the PLC saves a flow measurement and
compares it with the subsequent values. If there is a difference of 360 kg/h,
the system is automatically shut down (Figure 5). When testing the measurement,
the lowest detectable leak flow using the flow output signal was calculated to
be 36 kg/h. Because the flow fluctuated during operation when a heat exchanger
was connected, the leakage value was raised to prevent false alarms. At
present, further tests are underway to halve the leakage value. These involve
analyzing the flow fluctuations in various operating modes.
If you take the measuring accuracy for a flow of this
magnitude, the smallest leakage calculated corresponds to the measuring
accuracy of the OPTIMASS (Figure 6). Engineers at BASF Coatings took a sample
in test mode, after which the process was immediately halted. Because the
company was so satisfied with the pilot project using the KROHNE OPTIMASS, BASF
Coatings wants to use other appliances of this type in the grinding process.
In traditional straight-tube mass flowmeters, so-called absorber masses (vibration dampers) are often used to mechanically isolate the measuring system from the process. An absorber mass is a spring-supported mass on the inner cylinder.
Instead of an absorber mass (vibration damper) and the spring, however, KROHNE’s OPTIMASS uses an integral spring mass system incorporating the dynamic elements of the measuring system. As the absorber masses and the rigidity of the spring are constant in conventional straight-tube meters, but the density of the medium – and consequently the resonance frequency – changes, the vibration damper can only compensate in tight density limits. KROHNE’s patented AST design, on the other hand, comprises an inner cylinder, with the ends of the connection pipes serving as a spring for the absorber mass system. The main advantage of this is that the spring (i.e., the measuring tube ends) is self-compensating. As the fluid density changes, so too does the dynamic behavior of the measuring tube ends (or the spring), depending on the mass of the inner cylinder. This produces a fully balanced system optimized accordingly under all process conditions. As no vibration energy is transferred outwards, the zero-point stability and measuring accuracy are excellent.
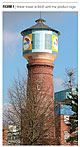
The Coriolis Measuring Principle
Coriolis flowmeters can be used to calculate the mass flow rate from the deformation of the measuring tube caused by the inertia. The media density can also be derived from the resonance frequency of the vibrating tube. The sensor in the OPTIMASS comprises a straight measuring tube, which is caused to vibrate by a field coil attached to the center of the tube. The excitation is controlled in such a way that the measuring tube always vibrates in its resonance frequency. Two sensor coils record the Coriolis effect, each of which is fitted equidistant from the field coil on each side. If there is no flow, both sensors record the same sinusoidal signal coming from the natural vibration of the measuring tube. As soon as a flow begins, the Coriolis force acts on the flowing mass particles of the medium and deforms the measuring tube, thus causing a phase shift between the sensor signals. The sensors measure the phase shift of the sinusoidal vibrations. This phase shift is directly proportional to the mass flow.As the Coriolis principle allows an exact measurement of fluid and gaseous media, mass flowmeters are becoming increasingly popular. Coriolis measuring technology is already the second most common modern measuring method behind electromagnetic flowmeters and, together with ultrasonic flow measuring technology, boasts the fastest growth rates.

OPTIMASS in Varnish Grinding
BASF Coatings AG uses KROHNE’s OPTIMASS mass flowmeters in the color pigment grinding process. In the past, however, mobile paddle mixers (Figure 2) with a volume of 12 m3 were guided and connected to the mill using a hose. The mobile mixer supplies the components before the medium goes into the mill and out again. This usually happens several times to ensure that each pigment particle is pumped through the mill at least once. Due to the time taken to complete this process – between 36 and 48 hours in some cases – the system also operates nights and weekends. BASF Coatings wanted a solution to allow unsupervised operation of the mill by connecting a hose. This would have run the risk of potential leakages. As the whole process takes the form of a circuit, there was the option of integrating a flowmeter in the outlet, which would trigger a leak alarm in the event of a sudden deviation from the regular flow and automatically shut the system down. Although this type of leakage rate measurement only requires one meter, this meter must fulfill high specifications in terms of its accuracy. In the case of BASF Coatings, the properties of the media made things even more difficult. The raw materials for varnishes are, for the most part, high-viscosity media which, moreover, are processed at a low flow rate.
OPTIMASS Straight-Tube Design
KROHNE has always relied on the straight-tube design because it offers obvious advantages compared to mass flowmeters with curved or twin tubes. A range of media, such as viscous, non-Newtonian, shear-sensitive fluids and fluids containing solids, cause high-pressure losses in twin tube meters. Abrasive media can corrode flow splitters and bent tubes, whereas process liquids containing fibers, such as palm oil or cellulose, can accumulate in the flow splitter and cause blockages. The main advantages of straight-tube meters include:· less pressure loss;
· less abrasion;
· suitable even for large flow volumes;
· wide measuring range; and
· no risk of blockage.
Straight-tube meters are also easy to clean, self-draining and suitable for measuring high-viscosity media such as those processed at BASF Coatings because of their ideal proportions; i.e., a short measuring tube with a large inner diameter.

Measuring Leakage Rates with OPTIMASS
The varnish grinding system at BASF Coatings is designed for a flow rate of approximately 5000 kg/h (Figure 4). This system grinds pasty preliminary products, which are subsequently let down and processed to become finished products. Communication with the PLC takes place via the OPTIMASS’s 4 - 20 mA signal output.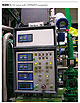

Adaptive Sensor Technology
With its third generation of straight-tube mass flowmeters, KROHNE has developed a revolutionary patented technology known as “Adaptive Sensor Technology” (AST), which has been successfully implemented time and again. KROHNE has taken a quantum leap in Coriolis technology with AST, which has rendered every OPTIMASS insensitive to system vibrations and external process conditions.In traditional straight-tube mass flowmeters, so-called absorber masses (vibration dampers) are often used to mechanically isolate the measuring system from the process. An absorber mass is a spring-supported mass on the inner cylinder.
Instead of an absorber mass (vibration damper) and the spring, however, KROHNE’s OPTIMASS uses an integral spring mass system incorporating the dynamic elements of the measuring system. As the absorber masses and the rigidity of the spring are constant in conventional straight-tube meters, but the density of the medium – and consequently the resonance frequency – changes, the vibration damper can only compensate in tight density limits. KROHNE’s patented AST design, on the other hand, comprises an inner cylinder, with the ends of the connection pipes serving as a spring for the absorber mass system. The main advantage of this is that the spring (i.e., the measuring tube ends) is self-compensating. As the fluid density changes, so too does the dynamic behavior of the measuring tube ends (or the spring), depending on the mass of the inner cylinder. This produces a fully balanced system optimized accordingly under all process conditions. As no vibration energy is transferred outwards, the zero-point stability and measuring accuracy are excellent.
Looking for a reprint of this article?
From high-res PDFs to custom plaques, order your copy today!