Epoxy Floor Coating Producer Eliminates Processing Step - Prevents Pigment Float and Flocculation
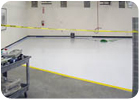
Versatile Building Products Inc. (VBP) manufactures treatment and repair products for cement, concrete and stone floors. These range from epoxy and polyurethane coating systems for commercial and residential applications to stains, sealers, mortar and substrate repair materials. Many of these durable products are offered in colors and special effects such as faux granite.
One such product is the company's 4800 Epoxy Colorseal, a chemical- and abrasion-resistant topcoat for concrete floors specifically formulated to reduce or eliminate color variations associated with epoxy coatings. These variations, explains Mark Glendrange, VBP's technical director, are due to the "float and flocculation" of pigments that occurs in the coating following application, until the point of cure.
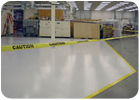
The company overcame float and flocculation problems by switching from in-house processing of dry pigments to purchasing newly developed "Series 22" epoxy color dispersions from Ferro Corporation. According to Glendrange, the formulation exhibits significantly greater pigment stability, eliminating the patchy appearance of coatings associated with conventional liquid and paste dispersions.
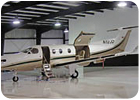
The total cost of grinding and dispersing of pigments in a blend was considerable. "Capitalizing equipment for dispersion of pigment can be prohibitive," Glendrange says. "There are also expenses associated with the safe handling of pigments and additives, especially in dust containment, downtime required for material changeover and equipment cleaning, and the use and disposal of regulated chemicals like solvents for cleaning."
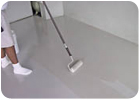
The colorant is comprised of pigments that are broken down into individual particles and wet-out in suspension, preventing re-agglomeration while increasing opacity of the original pigment by 50% to 80%.
The carrier resin is a proprietary, highly stable, 100%-solids, bisphenol A epoxy resin that is reactive with all epoxy formulations. VBP orders four base colors from which it custom blends the 10 colors in the topcoat line: white, black, yellow, blue, green, red, umber, and three shades of gray. The company maintains an inventory of standard colors, and does custom color for an extra charge. Technicians weigh the colorants with a gram scale and produce batches of up to 150 gallons, which are usually supplied in 1.5-gallon pails.
"Colorseal topcoat is typically applied with a brush, roller or squeegee in thicknesses of 4 to 10 mils. The high pigment loadings and stability of the colorant improves handling and application of the topcoat, which increases the quality and value of our product," says Glendrange.
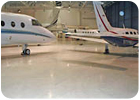
For more information contact Versatile Building Products Inc., 20420 South Susana Rd., Carson, CA 90810; phone 800/535.3325; www.garagecoatings.com; or Ferro Corp., 54 Kellogg Ct., Edison, NJ 08817-2509; phone 800/882.1456 x 2835; www.ferro.com.
Looking for a reprint of this article?
From high-res PDFs to custom plaques, order your copy today!