Acrylated Performance Products for Floor Coatings With High Scratch and Abrasion Resistance
UV-curable coatings are increasingly being used to design floor finishes because of the higher productivity and performance properties achieved with these systems. In addition, since they do not contain organic solvents, UV coatings facilitate compliance with stringent environmental regulations.
Requirements for UV-curable floor coatings include low viscosity for ease of handling and application; fast cure speed; and high resistance to water, stains, scratch and abrasion. Sealers and topcoats based on acrylated urethanes, epoxies and polyesters have been used with differing degrees of success.1-5
Urethane and epoxy acrylates are characterized by high viscosity, thus necessitating relatively high concentrations of reactive diluents to formulate coatings suitable for application. Whereas the use of polyester acrylates mitigates this problem, scratch and abrasion resistance is normally inferior to that obtained with acrylated urethanes and epoxies.1,4
Cytec Surface Specialties has introduced two acrylated performance products to formulate coatings for wood flooring. The products have been designed with low viscosity for ease of handling, with performance properties targeted to wood floor requirements, and for compatibility with standard acrylated oligomers. Typical properties of these products and of an acrylated epoxy, acrylated urethane and acrylated polyester are shown in Table I.
The products shown in Table I have been tested as part of model flooring systems consisting of sealer and topcoat based on these acrylated products. The UV-curable system was compared with a conventional floor coating consisting of solvent-based polyurethane sealer and topcoat. In both cases the sealer was used as an intermediate coat.

Experimental
Formulations and Testing
UV-curable formulations used for testing are indicated in Tables 2 and 3. The resin concentration in the topcoat is either 70% or adjusted to give a viscosity not higher than 1,000 cP at 25 ºC.Viscosity of the UV-curable formulations was measured with a Brookfield DV-II+ viscometer at 25 ºC. Photospeed was determined by the energy density (mJ/cm2) required to produce a tack-free surface when irradiated with a Fusion EPIQ 6000 curing unit using two H lamps operated at 300 watt/inch. The photospeed was measured on coatings applied on opacity charts with a #12 drawdown bar.
Taber abrasion resistance of the cured coating systems was determined using CS-17 wheels, with 1 Kg weight on each wheel, Hoffman scratch resistance with a Gardco tester, and direct impact resistance with a BYK-Gardner impact tester using a 2-lb weight. The end point for Taber abrasion was breakthrough over 10% of the area in contact with the wheels.
UV-cured coatings were conditioned at 23 ºC for at least 24 hours prior to testing. Following the manufacturer's recommendations, the conventional coating system was allowed to stand at room temperature for at least one week after application of the topcoat. Testing was conducted after conditioning for an additional 24 hours at 23 ºC.
A solventborne floor coating system was applied according to the manufacturer's instructions using materials purchased from a major supplier of wood coatings. The sanding sealer was an oil-modified polyurethane supplied at 36% solids. The topcoat was an oil-modified polyurethane varnish supplied at 50% solids. It was recommended by the manufacturer for its excellent hardness and abrasion resistance.
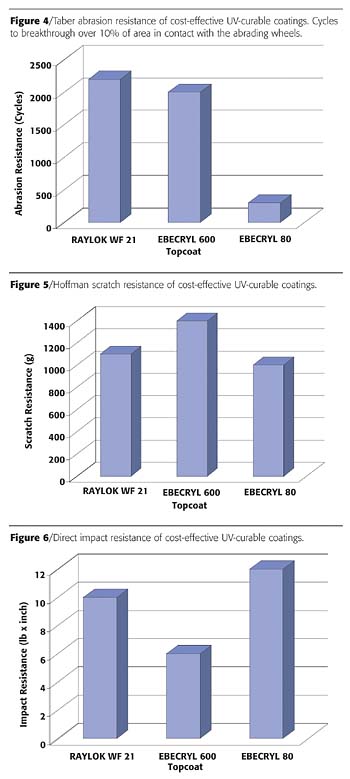
Application
Solventborne coatings were applied by brushing, and dried at room temperature. All applications and drying were conducted inside a hood due to ventilation requirements. Sanding of the sealer and intermediate coat was conducted 24 hours after application. Physical testing was started not earlier than 7 days after application of the topcoat.Dry coat weights were (after sanding) 98 g/m2 for the sealer, 71 g/m2 for the intermediate coat and 14 g/m2 for the topcoat. These coat weights are recommended by the manufacturer for high-traffic applications.
UV-curable formulations were applied with a Barberan BRB-800 roll coater on oak veneer. The process was as follows:
-
_ sanding of the substrate;
_ application of the sealer, two coats wet-on-wet;
_ UV curing;
_ sanding of the sealer;
_ application of two layers of intermediate coat, with pre-gelling between applications;
_ application of final layer of intermediate coat;
_ UV curing;
_ sanding of intermediate coat;
_ application of topcoat; and
_ UV curing.
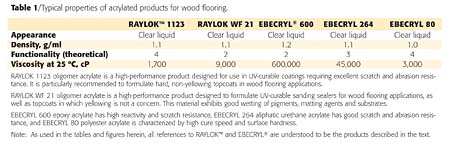
Results and Discussion
Figure 1 shows the results for Taber abrasion resistance as determined by breakthrough to the substrate, and Figure 2 shows the Hoffman scratch resistance for the three systems that were evaluated. The latter test uses a cylinder at 45 degrees to simulate scratching by sharp edges.The higher functionality of RAYLOK 1123 oligomer acrylate (see Table I) leads to a coating with significantly higher scratch resistance than both the conventional system and the finish based on EBECRYL 264 aliphatic urethane acrylate. High Taber abrasion resistance is obtained by high coating resiliency, which is achieved by a proper balance between hardness and flexibility. The higher crosslink density makes the UV coatings more rigid than the conventional system, resulting in lower impact resistance, as shown in Figure 3.
RAYLOK 1123 oligomer acrylate can be blended with more flexible oligomers to obtain a topcoat with higher flexibility but with lower scratch and/or abrasion resistance. Alternatively, since the abrasion resistance obtained with the UV coatings is significantly higher, a lower coat weight can be used to obtain the durability of the conventional system. A lower coating thickness results in higher flexibility due to the reduction in stress associated with higher coat build.
Figures 4-6 present the results obtained with the cost-effective topcoats shown in Table 3. In these experiments, the topcoat based on RAYLOK WF 21 oligomer acrylate is applied over the sealer based on RAYLOK WF 21 oligomer acrylate, whereas the topcoats based on EBECRYL 600 epoxy acrylate and EBECRYL 80 polyester acrylate are applied over the sealer based on the acrylated epoxy/polyester combination (see Table 1).
Scratch resistance of these topcoats is similar to that obtained with the conventional solventborne coating, whereas RAYLOK WF 21 oligomer acrylate and EBECRYL 600 epoxy acrylate can be used to formulate UV-curable coatings with significantly higher abrasion resistance. Based on the viscosity of the products used to formulate cost-effective UV-curable topcoats (Table 1), we conclude that the system based on RAYLOK WF 21 oligomer acrylate represents the best compromise between low viscosity, and high scratch and abrasion resistance.
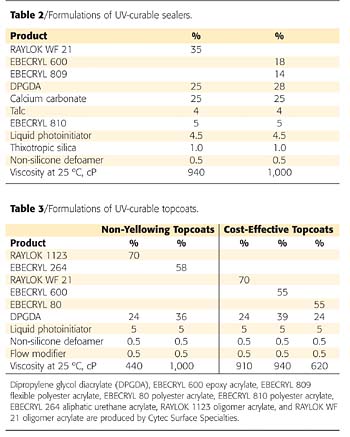
Conclusions
RAYLOK 1123 oligomer acrylate is a suitable product to formulate high-performance coatings for wood flooring applications. A system composed of a topcoat based on RAYLOK WF 21 oligomer acrylate and RAYLOK 1123 oligomer acrylate, with the sealer and buildcoat based on RAYLOK WF 21 oligomer acrylate show superior scratch and abrasion resistance, with values significantly higher than those obtained with a commercial high-abrasion-resistance polyurethane finish. Topcoats based on these performance products show similar or higher abrasion resistance than topcoats based on standard UV-curable oligomers, and also have lower viscosity and are easier to handle.Acknowledgements
The author gratefully acknowledges the following from Cytec Surface Specialties: Mr. Greg Bryant, formerly Senior Technical Specialist, for his collaboration with the experimental work, and thanks Dr. Jo Ann Arceneaux, TS&D Manager for Radcure-Americas, and Dr. Jonathan Shaw, TS&D Manager for Industrial Coatings/Radcure-Americas for their thorough review of the manuscript.References
1 Fei, H. RadTech Asia 2003 Conference Proceedings, 443-447.2 Burak, L. Paint & Coatings Industry, October 2001.
3 Valdes-Aguilera, O. Paint & Coatings Industry, March 2001.
4 Dulany, L. RadTech North America 2000 Conference Proceedings, 103-112.
5 Ross, J. S.; Leininger, L.W.; Sigel, G.A; Tian, D. RadTech North America 2000 Conference Proceedings, 241-250.
Looking for a reprint of this article?
From high-res PDFs to custom plaques, order your copy today!