UNOXOL™ Diol
A new cycloaliphatic diol, UNOXOL™ Diol, is available for use in high-performance and low-VOC coatings applications. The new diol is an approximate 1:1 mixture of (cis, trans) 1,3-cyclohexanedimethanol and (cis, trans) 1,4-cyclohexanedimethanol. Because of its unique structure and composition, UNOXOL Diol is liquid at room temperature. It contains two primary hydroxyl groups that lead to excellent reactivity during the preparation of condensation polymers and curing of the polymers with typical melamine and polyisocyanate crosslinkers. Condensation polymers can be prepared from the new cycloaliphatic diol with low viscosity, excellent solubility in organic solvents and resistance to crystallization. Thermoset coatings prepared from these condensation polymers have an extraordinary balance of hardness and flexibility compared with traditional coatings. As a result of its cycloaliphatic structure, UNOXOL Diol also imparts excellent acid etch resistance, hydrolytic stability and weatherability. The new diol affords all the benefits of the cycloaliphatic backbone structure, while removing the limitations to incorporation, solubility, storage and usage observed when using the 1,4 isomer alone. This article discusses the use and performance advantages of using UNOXOL Diol in high-solids, waterborne and powder coatings.
Introduction
VOCs have been a driving force behind the emergence of waterborne, powder and high-solids technologies since the 1970s. Polyester resins are widely used in the coatings industry to formulate low-VOC coatings based on these technologies. Typical polyester resins are prepared from the condensation reactions of isophthalic acid and/or adipic acid (due to their low cost and the excellent range of properties they impart to polyesters) with a variety of diols.1 Typical diols include 2,2-dimethyl-1,3-propanediol (neopentyl glycol), 2,2,4-trimethyl-1,3-pentanediol, hydroxypivalyl hydroxypivalate, and 1,4-cyclohexanedimethanol.1,2 These diols are all solids at room temperature. Due to its unique cycloaliphatic structure, 1,4-cyclohexanedimethanol (1,4-CHDM) results in polyester resins with higher glass transition temperatures (Tg) and faster curing rates when compared with neopentyl glycol and 2,2,4-trimethyl-1,3-pentanediol.2 Coatings prepared from 1,4-CHDM-based resins also offer better salt spray, Cleveland humidity and detergent resistance, as well as the best balance of hardness and flexibility.2 A major disadvantage of polyester resins prepared from 1,4-CHDM is their high viscosity (high VOC), lower solvent solubility and tendency to crystallize.3,4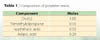
High-Solids Coatings
Composition of Polyester ResinsIn testing, Dow used a typical polycondensation procedure to prepare polyester resins. The esterification reaction was monitored by the acid number, which was controlled to a value of approximately 1-2 mg KOH/g resin to keep the degree of reaction very similar for the different polyesters. The compositions of the polyesters are given in Table 1. The diols used in the preparation of the polyester resins were neopentyl glycol (NPG), 1,4-CHDM, UNOXOL Diol, a 1:1 molar mixture of 1,4-CHDM/NPG, and a 1:1 molar mixture of UNOXOL Diol/NPG. In all the compositions, the polyol/diacid molar ratio was 1.10 to 0.84, to ensure the resins were hydroxy-terminated.
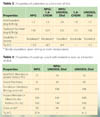
In contrast, polyesters containing UNOXOL Diol have excellent solvent solubility, making them very amenable for use in high-solids coatings. The Tg for the polyester resins increases as NPG is replaced with either 1,4-CHDM or UNOXOL Diol. By replacing NPG with UNOXOL Diol, the Tg increases by 11.6 ºC, due to the presence of the cyclohexyl structure. Hence, by using UNOXOL Diol in place of NPG in the polyester, the hardness and chemical resistance of the resulting coatings are expected to improve. Little difference is observed in the Tg of the resins when comparing UNOXOL Diol to 1,4-CHDM, indicating that the cyclohexyl structure has the dominant effect on Tg, as compared to the individual positional isomers.
Coating Formulations and Film Preparation
The polyester resins were diluted in xylene to 60 weight percent solids and then mixed with either a hexa (methoxymethyl) melamine crosslinker (CYMEL 303) or a polyisocyanate crosslinker (DESMODUR N-3390) and a flow additive (BYK-320). The melamine-cured coatings were catalyzed with an amine-blocked dodecylbenzene sulfonic acid, whereas the polyisocyanate-cured coatings were uncatalyzed. For the melamine-cured coatings, the weight ratio of polyester resin to melamine crosslinker was 3:1. For the polyisocyanate-cured coatings, a 5% molar excess of isocyanate groups to hydroxyl groups was utilized. The films were cast on zinc phosphate pretreated steel panels by a drawbar and baked at either 120 ºC for 20 minutes (polyisocyanate-cured coatings) or 140 ºC for 20 minutes (melamine-cured coatings) to give a dry film thickness of approximately 1.5 mils.Properties for Melamine-Cured Coatings
The film properties of the melamine-cured coatings as a function of diol are given in Table 3. The acid etch resistance is highest for the coatings containing UNOXOL Diol as measured by the temperature (using a temperature gradient oven) at which the film was first attacked by a 10% solution of sulfuric acid. The hardness of the films (both Sward and Pendulum hardness) increases as higher levels of UNOXOL Diol are used in the polyester resin, relative to NPG. The overall impact resistances of the films are excellent, and independent of whether NPG or UNOXOL Diol is used. Hence, the coatings based on UNOXOL Diol have the best overall balance of hardness and flexibility (tougher coatings), compared with NPG. The Tg of the crosslinked films was determined by using dynamic mechanical analysis. The Tg was taken as the temperature of the maximum in the tan plot.5 The coating based on UNOXOL Diol has a higher Tg than the coating based on NPG, which explains the higher acid etch resistance and hardness of the coating.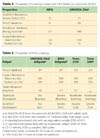
The film properties of the polyisocyanate-cured coatings as a function of diol are given in Table 4. The acid etch resistance is similar for the coatings containing UNOXOL Diol and NPG, and the polyisocyanate-cured coatings have higher acid etch resistance than the melamine-cured coatings. The hardness of the films (both pencil and pendulum hardness) increased when UNOXOL Diol is used in place of NPG in the polyester resin. The impact resistance for both coatings was comparable. Hence, the polyurethane coatings based on UNOXOL Diol have the best overall balance of hardness and flexibility (tougher coatings), as compared to NPG.
Waterborne Coatings
Waterborne polyurethane dispersions (PUDs), a 30-40% weight solids colloidal dispersion of polyurethane micelles in a continuous water phase, are experiencing high growth due to their low VOCs and exceptional performance properties.6,7 In all these PUD applications, polyols that offer improved hydrolytic resistance are highly desirable.
A series of PUDs were prepared to compare the performance properties of a polyol based on UNOXOL Diol to polyols commonly used as raw materials for PUDs. The PUDs were prepared by a batch process using N-methyl-2-pyrrolidone as the solvent, isophorone diisocyanate as the diisocyanate and were anionically stabilized by using 2,2-dimethylolpropionic acid.8 The coating properties of the PUDs as a function of the polyol are compared in Table 5. In all cases, the toughness (balance of hardness and flexibility) and abrasion resistance of the coatings were excellent, which are characteristic properties of PUDs. The PUD prepared from the UNOXOL Diol-based polyol resulted in a coating with the best hydrolytic and acid etch resistance, as shown in Figure 1. These exceptional properties are attributed to the increased hydrophobicity of the polyol prepared from UNOXOL Diol.

Powder Coatings
Polyester powders have gained great market share since their commercial introduction in the mid 1960s and subsequent widespread acceptance.9-11 It has been difficult to package both good flexibility and a high degree of surface hardness in a powder coating, mostly due to the inherent properties of monomers (high Tg) that are required to prevent the powder resin from sintering during storage. There has been some success with 1,4-cyclohexanedimethanol (1,4-CHDM) in affording a better balance of the desired properties to powder coatings. However, it has inherent usage limitations in powder resins. Incorporation of increasing levels of 1,4-CHDM gradually increases the crystalline fraction of a powder resin and raises its melt viscosity, eventually impairing the ability to fully process the resin into a coating. UNOXOL Diol, with its unique composition, allows polyester resins to be prepared with no crystallinity and low-melt viscosities.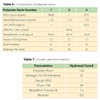
Synthesis of Polyester Polyols
The polyester polyols used in this investigation are based on trimethylolpropane, terephthalic acid and glycols.12 Details of the polyester compositions are given in Table 6. Excess glycol of 1-2% was added in addition to the charges indicated below. Straight 1,4-CHDM/TPA polyester could not be made to completion, due to crystallization issues. Therefore, it was necessary to dilute the monomer with an equivalent molar amount of NPG.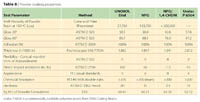
Preparation of Powder Formulations
The powder formulation is shown in Table 7. A blend made of polyester resin, isocyanate hardener, small amounts of a flow agent and a degassing agent were mixed in a premixer, and then extruded in a Prism extruder. The extrudate was milled and sieved. The fraction smaller than 90 µm was used for the powder paint. The typical batch weight was 1430 g. A Prism Pilot 3 mixer at 2300 revolutions per minute (rpm) was utilized for pre-mixing the formulation ingredients to a homogeneous dry blend. Mixing time was slightly less than one minute. The resulting blend was fed into the Prism twin-screw 24 mm extruder at 400 rpm. The temperature zones were set at 35 °C at the feed; the middle zone set at 70 °C; and the head temperature was 90 °C. Extruded material was collected in a flat rolled sheet, and eventually was ground using an ACM 2 grinder at 9500 rpm rotator speed and 3500 rpm separator speed. The feed zone was set at 10 rpm, yielding an average particle size of 43-micron diameter.Results and Summary of Powder Resins
The use of UNOXOL Diol can lead to a significant improvement in the performance properties of cured powder coatings, when compared with both NPG and with 1,4-CHDM. The melt viscosity of a polyester polyol prepared from UNOXOL Diol was significantly lower than the comparable polyester polyols prepared from either NPG or a 1:1 mixture of NPG and 1,4-CHDM, as shown in Table 8. This can result in better flow and leveling of the final coating and lead to improved appearance and aesthetics. The powder coating prepared from the UNOXOL Diol-based resin had a significantly better balance of hardness and flexibility than the coating prepared from either the NPG or 1:1 NPG/1,4-CHDM resins. The powder coatings based on UNOXOL Diol also had excellent adhesion, gloss, chemical resistance properties and conical mandrel flexibility.
Conclusions
Dow has commercialized UNOXOL Diol, a new liquid cycloaliphatic diol for use in high-performance and low-VOC coating applications. The new diol is an approximately 1:1 mixture of (cis, trans) 1,3-cyclohexanedimethanol and (cis, trans) 1,4-cyclohexanedimethanol. Polyester polyols prepared from the new diol can be used in high-solids, waterborne and powder coatings. These coatings have been shown to have an improved balance of hardness and flexibility, better hydrolytic and acid etch resistance than coatings prepared from conventional diol monomers.Acknowledgements
The authors would like to recognize the contributions of Marty Beebe and Bill Dellinger for the preparation and evaluation of the various coatings. The authors are also grateful to Rodolfo Bayona and Paul Foley for their many contributions.
Looking for a reprint of this article?
From high-res PDFs to custom plaques, order your copy today!