New Lamp Monitor for UV Curing
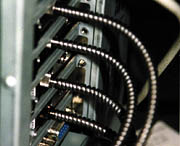
The most important physical component of the UV curing process is the lamp. The lamp is responsible for converting the liquid-like coating into a dry, solid protective layer. If the lamp's performance is not optimal, the UV curing process can fail.
To help ensure that the UV curing process is as efficient as possible, UV Process Supply Inc. has developed the CON-TROL-CURE LM-9000 UV continuous lamp monitor. This highly modular, software-based, full-spectrum UV data acquisition and management system provides both real-time display and data storage of UV lamp output characteristics. Through the lamp monitor's exclusive optical probe and fiber optic sub-systems, it allows permanent sensor placement inside the curing zone, reflector housing or even directly on the lamp. Unlike conventional monitoring methods that only collect data when the user requests it, this system provides continuous monitoring to identify problems immediately, and prevent costly errors or product loss.
As a computer software- and hardware-based data acquisition system, the LM-9000 captures data through the installation of one or more high-temperature optical probes within the lamp reflector housing. The sensor is connected, by way of fiber optic cabling, to an optical bench installed on an internal PC card or in an external housing. The data collected is displayed and managed by custom Windows lamp monitoring software.
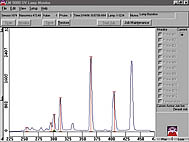
Why Continuous Lamp Monitoring?
The UV lamp is the most important variable of the UV curing process. Lamp performance has been conventionally measured by the use of two distinct methods.1) Indirect mechanical testing (testing product following manufacture); and
2) Direct (but limited) radiometric measurement.
Although both methods serve a purpose, the mechanical test occurs too late in the process to prevent poor results, and the radiometric method only takes a snapshot of lamp output when it is used. While both of these methods can yield valuable information, continuous monitoring of lamp performance throughout the curing process is the only method that provides constant, real-time evaluation. Therefore, costly product failures are avoided, and more consistent end product is produced.
Many factors influence the level of cure within the UV curing process. As more powerful lamps are developed, newer coating formulations are invented and new trends in cooling and IR/UV filtering are implemented. These new trends push the envelope of technology in the hopes of higher profits, better throughput, and less wasted time and product. But, if the UV lamp itself is not providing long-term, reliable, stable output at the required wavelengths, the entire process is compromised, or even completely inhibited.
Over the total lifespan of a given UV lamp, its output varies and ultimately declines. When a lamp is new, it should produce perfectly stable and repeatable results. But, why do product failures continue to occur? When whole or partial jobs fail quality control, it is possible that the lamp, even when new, is responsible. The LM-9000 can identify such lamp problems before they generate waste in time and money.
With the help of the lamp monitor, it was discovered that an individual lamp loses intensity at various wavelengths at different rates over its operating life. Also, two lamps with the same specifications, the same arc length and used on the same machine, perform with different wavelength intensity distributions. Some older lamps perform fractionally better than a new lamp of the same specification.
These and other factors affect the efficiency of production and the quality of the end product. To operate a comprehensive and continuous lamp monitoring system, CON-TROL-CURE LM-9000 software was developed.
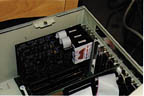
LM-9000 Lamp Monitor Software
The LM-9000 software is Windows 3.1/95/98/NT/2000 compatible and provides the user with many features and benefits, including a real-time display of wavelength intensity distribution between 200 and 450 nanometers, selective wavelength monitoring, and a saved baseline display."We tried to incorporate more features than anybody would ever ask for," says Stephen Siegel, president and founder of UV Process Supply.
One major advantage of the software is consistency of test results. With conventional UV lamp monitoring, the results can vary from test to test due to any number of factors, including mis-calibration, unstable environment and multiple lamps. With the LM-9000 software, testing is more precise.
There are certain wavelengths on which UV lamps consistently transmit increased energy levels. The LM-9000 is programmed to monitor these wavelengths and use them as a point of reference. For example, UV lamps transmit a very strong energy output at 365 nm. The LM-9000 checks where 365 nm is anticipated on the spectrum of frequencies. It then analyzes the surrounding frequency range (+/- 7 nm) to find the strongest signal. If the sensors determine that the strong signal is peaking at 363 nm, it calibrates the sensors to accept that reading as 365 nm. Every time the software is used, it will locate this peak in the readings, identify it as 365 nm and calibrate the other readings accordingly.
Another way this software ensures accuracy is by averaging its UV scans. During the UV curing process, the lamps may experience occasional vibrations from the surrounding machinery or environment. These movements, no matter how subtle, can result in inaccurate readings. To minimize this effect, the LM-9000 makes repeated scans and calculates their average. This eliminates the anomalous readings that can occasionally occur in an unstable environment.
Multiple lamps can also affect accuracy. Individual lamps are often located at different distances from the sensors on the optical bench. When making precise measurements, these distances can slow down the signal and produce a faulty reading. The LM-9000 automatically adjusts for this variable and changes the frequency to standardize the readings from all lamps connected to the testing system.
A second major advantage of monitoring UV lamps with this software is its ability to record and analyze the performance of a UV curing system over an extended period of time. Most UV monitoring systems provide readout only when an operator presses a button; the LM-9000 captures all the performance characteristics of your UV lamp output throughout the course of each and every job you produce.
The collected data can be analyzed to show the performance of the lamps over a span of time. The data, presented visually in line-graph form, can, for example, show the user a gradual decline in the lamps power output. This allows the user to take preemptive action to correct the problem before it affects productivity.
The LM-9000 even saves information so you can keep process and machine settings, job characteristics and system state information to help duplicate the exact conditions of a specific job required at a later date. After installing a new lamp into the curing system, the LM-9000 will establish the baseline performance characteristics of the lamp. It will then keep track of lamp performance throughout its life span. As lamp hours accrue, it can then show when to replace the lamp with a new one.
Thirdly, since the LM-9000 constantly monitors the UV lamps, the software can provide instant warning of malfunctions or other problems. While running a job, the LM-9000 can alert operators to energy output events the instant they occur, allowing mid-job correction of press settings or temporary pausing of the job until the problem can be corrected. Setting intensity levels on any monitored wavelength so fluctuations of 25% or 50% of lamp baseline trigger an alarm, users will no longer suffer from inconsistent production runs, wasted product or time.
Also, when the curing system is turned on, the LM-9000 will indicate when the system has stabilized and is ready for use. No more production runs wasted because the UV system wasn't ready to properly cure.
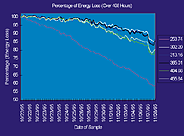
LM-9000 Lamp Monitor Hardware
Regardless of the quality of the software, it is useless if it is not supported by high-quality hardware. The LM-9000 is a complete monitoring system. In addition to the superior software, the LM-9000 monitoring process is facilitated by top-quality hardware, including the optical bench, optical probes and optic cabling.The optical bench, which is the "brain" of the LM-9000, can be connected to the PC either internally or externally. The internal instrument is mounted directly to the PC as a PC card (16 bit ISA Bus). Externally, the instrument is housed in an impact-resistant case, connected to the PC by way of a standard serial cable or USB cable.
Both units allow direct connection of the UV-enhanced fiber optic cable to the PC, bringing the full spectrum of ultraviolet light (200-450 nm) into the system. The incoming "Light Sample" is broken up into individual wavelengths and reflected onto a CCD array containing 1,100 individual sensors. Data from each sensor (each wavelength) is then interpreted by the computer for display, and maintained in an accessible database. Multiple lamp configurations can be created by incorporating additional cards (either internal or external) and sensing units into the system.
The basic optical probes are available as small as 1/4" diameter by 3/4" long. They intrude only 3/8" into the curing system, and are easily installed anywhere inside the curing zone, and anywhere around the lamp. Using a proprietary lens system and interface to the connecting fiber optic cabling, basic probes will withstand temperatures up to 400 degC, and are available in four levels of optical attenuation, each designed to address the very high UV light levels used in high energy (300+ watt) UV systems.
The connecting fiber optic cabling is designed for industrial applications, and is specially enhanced to transmit all the UV energy in the 200-450 nm range without loss of signal. Jacketed and encased within a flexible stainless steel covering, the fiber is designed to function at up to 300 degC continuous operation and will not solarize over long term UV exposure. Cables install easily on industrial processing equipment and are protected to prevent damage to the fiber.
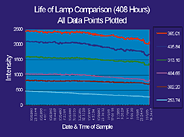
Conclusion
The LM-9000 is the most comprehensive and accurate UV lamp monitoring system available. The integration of both software and hardware applications makes it the most complete monitoring system available for UV curing systems.For more information about lamp monitor, contact UV Process Supply, phone 800/621.1296; fax 800/99FAXUV; e-mail at info@uvps.com; visit www.uvprocess.com; or Circle Number 85.
Looking for a reprint of this article?
From high-res PDFs to custom plaques, order your copy today!