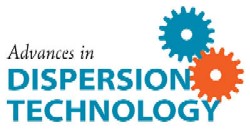
The advantages of more "efficient" dispersion can be translated into different benefits for the coatings manufacturer, depending on the company's situation and priorities. Lower process time, reduced energy consumption and better quality output are the results.
Fillworth (UK) Ltd. is a medium-sized specialist manufacturer of industrial mixing equipment. This equipment is supplied to customers throughout the manufacturing industry with focuses on coatings, chemicals and adhesives. A particular area of focus is the coatings manufacturing industry, where efficient mixing and dispersion requirements are key to the profitability of its operations. In 2001, Fillworth developed technology targeted specifically at coatings dispersion that could subsequently be extended to other industrial sectors. The point of departure was the traditional "sawtooth" impeller, which enjoys widespread use, but which, in spite of several attempts over the years, has never been significantly improved beyond the original design.
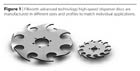
Conventional Dispersion Process
In a conventional dispersion process, an area of high shear flow exists up to a boundary one third of the blade diameter away from the blade tip. The primary objective of the dispersion process is to circulate the bulk of the slurry into this high-shear zone enough times to build sufficient total residence time to achieve dispersion.A conventional high-shear ("saw tooth") impeller uses the flat area of the disk to generate the differential laminar acceleration and flow patterns necessary to build the boundary layers; these produce shear within the slurry in the area of high acceleration. Circulation of the batch is left to (is driven by) the sawtooth-shaped blades at the periphery of the disk. These function as vanes to propel the material radially from the tip of the blade. It can be observed that circulation is frequently concentrated on part of the total mixture resulting in uneven dispersion, or in correspondingly longer process times to achieve satisfactory dispersion throughout the mixture.
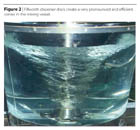
New Technology
Recently new dispersion technology, introduced by Fillworth, has largely overcome these difficulties by an innovative disc design (Figure 1) that achieves much improved circulation of the slurry (from the low-shear into the high-shear zone), while simultaneously maintaining a high degree of shear and attrition in the high-shear zone. This is demonstrated visually by a more pronounced vortex while the process is running (Figure 2). In addition to the advantages listed above, one effect of more "efficient" circulation is that the Fillworth disc can be mounted nearer to the base of the vessel. This improves shear performance while maintaining wetting (pulling in) of the undispersed powder. It also reduces dust in the surrounding atmosphere.The disperser impeller discs will generally create less turbulence (in contrast to maintaining laminar flow) for a given set of conditions compared with the traditional "sawtooth" blade. Turbulence is often confused visually with efficient dispersion but this is misleading. Fillworth technology can be "tuned" to generate a more or a less aggressive dispersion action to suit individual situations.
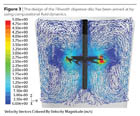
Extensive trials were conducted with a radical new design of a high-speed disperser disc whose main advantage lay in its ability to improve the tank or batch circulation flow characteristics of the traditional design while maintaining the shear performance. The two aspects complement each other within the total dispersion process, but improvement of one can run counter to the effectiveness of the other. Results were tested and evaluated at the University of Manchester leading to the optimization of the final profile (Figure 3).
Following the conclusion of the development work, the coatings manufacturer converted the dispersion impeller discs in its main production plants to use the new Fillworth technology. Improvements in efficiency ranged from 25 - 50%, depending on the process.
The "Fillworth dispersion effect" has been demonstrated in test conditions in a short video.
For more information, contact Denny Stidham, CB Mills, 1300 Northwestern Avenue, Gurnee, IL 60031-2348; phone 847/662.4000; or e-mail jds0520@aol.com.