Shear-Free Dispersion Process for Automated Production

Starting with the fundamental idea of wetting finely dispersed powder in a large liquid surface, the Ψ-MIX® (Psi-MIX) inline disperser was developed by NETZSCH Feinmahltechnik GmbH. Effective wetting of solid particles by high-quality dispersion improves quality and enables operation of the machine at high production rates.
The Ψ-MIX combines a new dispersion method with an emission-free inline process. The solid components are dispersed on a large liquid surface created by a high-suspension flow through the narrow process zone. Since the new machine is capable of processing both low- and high-viscosity suspensions, the entire application range of dispersion technology is covered. Applications for temperature-sensitive or shear-thickening materials are easily achieved within the design of the process chamber.
Compared to conventional rotor-stator systems, this machine uses significantly less energy for dispersion. Temperature-sensitive products and materials with a broad viscosity range can be processed. The Ψ-MIX can be integrated into automated plants that process large batches. It is also suited for emission-free and explosion-proof operations (Figure 1). The design of the machine is distinguished by the fact that foreign bodies in the pigment suspension do not cause damage to the system. The deaeration function occurs automatically within the operating method, which helps to process waterborne suspensions.
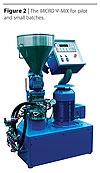
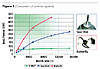
Comparison of Different Dispersion Methods
For highly viscous products, there are low-speed systems like butterfly mixers and high-speed mixers with finely toothed discs based on cavitations (cavitations disk). These systems are used to wet out dry particles with liquid components, but no defined measurement can describe their efficiency factor. A method described as sub-level feeding shows energy savings.The wetting process, as such, cruises as a black box with the pseudonym dispersing process, which defines only the quality of the result. The future may find a new definition such as coating- or wetting-process of micro powders.
When comparing the variety of different dispersing systems, relevant literature does not support production parameters. Equations mainly support mechanic layout of mixing systems to determine power requirements. The field of efficiency linked to the applications and information about specific energy remain undefined. Figure 3 shows the most common system groups with saw disks and butterfly tools in comparison to the Ψ-MIX, specified by installed power, which seems to be an indication for installation and running costs.
The energy input on the Ψ-MIX relates only to the powder feeding time. The volumetric dosing rate of up to 5 m³/h, together with the bulk density of the dry components, results in the batch time. Additional rework, in most cases, is not necessary.
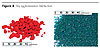
This wide distribution of dry agglomerates (Figure 4) results in an obvious difference in the required specific energy input to achieve a specific degree of dispersion. Considering the processes that may follow, such as fine grinding (fine dispersion) on bead mills, the energetic differences inherent in the type of pre-dispersion process become even more obvious.
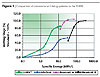
Example:
• Conventional System: EHS-Disk 70 kWh/t + EBM B 180 kWh/t = 250 kWh/t
• Ψ-MIX System: EΨ-MIX 10kWh/t + EBM A 90 kWh/t = 100 kWh/t
The combination of the Ψ-MIX process with the bead mill process (BM A or BM B) shows significant energy savings, which result in half-installed power or machinery costs. The total calculation is complete if maintenance and cooling systems are taken into consideration as well. The new process is very delicate to the pigments in use and is expected to develop new quality standards in the future.
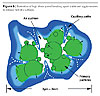
Achieving Optimum Dispersion
The advantages of in-line processing of solids into liquids are well known. What is new, is the treatment of the solids and liquids during initial wetting. The solid material is no longer just dumped into the liquid phase, but is now atomized under dry conditions before being shot into the liquid.The goal is to control the formation of wet agglomerates, with the aim of an “optimum dispersion”, that is to achieve the required degree of dispersion. In contrast, one could define an “ideal dispersion” where every primary particle is completely wetted. In most cases, the ideal dispersion is not the same as the quality specification – the required degree of dispersion or fineness of grind developed by conventional methods.
One problem for an effective wetting process is the quantity of micro air included in the charge of solid components. This air is inherent in the dry agglomerates. When the dry agglomerate is immersed into the liquid, the capillary path on the exterior of the particle is filled, sealing the interior of the dry agglomerate. In the core, an air pocket is created that stops the wetting process.
High shearing speeds break apart these stable, wet agglomerates (Figure 6) and new dry solid surfaces are released. Sub-level vacuum feeding or the condensation principle with gas exchange can be an acceptable solution to this problem.

Dispersion Technology
By connecting the individual process stages within a small space, all processes are achieved within milli-seconds to create an optimum dispersion.Figure 7 shows details of the process. The rotary valve attached to the solids feeding station seals off the dispersion chamber from the atmosphere and serves for dosing the powder. In the feeding tunnel under vacuum, the dry agglomerate is deaerated and fed to the atomizer. A hydro cyclone effect, similar in concept to a liquid ring vacuum pump, produces the vacuum effect. The pump transports a liquid stream tangentially to a ring-shaped acceleration chamber where it is hydraulically accelerated into rotation.
The rotation corresponds approximately to the speed of the rotor, which prevents the liquid from splashing into the solids feeding tunnel. A “free-falling liquid curtain” is created and leveled by centrifugal forces. After about 100 mm, this liquid layer merges with the rotor, forming a seal and is discharged at high speed. The rotor rotates the finely atomized solids falling from above. It spins them towards the outside onto the liquid layer.
Wetting occurs during the immersion of the individual solids and is assisted by the immediate increase in pressure. At the discharge of the machine, wetting is already perfect and cannot be improved by further processing with a disperser. The necessary rotary motion of the rotor leads to slight shearing, but this is negligible due to the wide gap between the rotor and the housing. These are also the reasons for the low induced specific power input of this technology.
Micro cavitation occurs in a rapid transition from vacuum vapor phase to process overpressure, further improving the dispersion process. Also, the quickly flowing liquid surface, which is available with a surface of more than two square meters per second, aids the wetting process. The high liquid surface in relation to the specific surface of the atomized solid agglomerates explains the basic principle of the Ψ- MIX.
Continuous dosing of liquids and solids or batch circulation with continuous powder feed are possible. Batch circulation is the most favorable method because it is easier to control the quality of the end product.
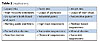
Variety of Applications
This technology is ideal for processing products with a high-solids content, a low-solids portion in large liquid batches, difficult-to-wet solids and extremely fine solids. It processes temperature-sensitive products as well as low- to high-viscosity suspensions that are barely pumpable.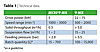
Conclusion
Innovative dispersion technology sets new benchmarks for modern production processes in all fields where micronized, pulverized solids have to be mixed as fine and as homogenously as possible. If the impression within the industry is that the development of dispersion technology has reached a standstill, the invention of the Ψ-MIX shows promise for the future.It may be difficult to fully integrate the concept of this new invention, but from a technical point of view there are no objections. This new concept may raise some conflicts with conventional mixing systems. For established dispersion systems, it may define a new era in the market for dispersing equipment, and manufacturers of mills will need to make adaptations to accommodate the higher throughput rates. This concept prompts rethinking about the dispersion process and a look at an innovative dispersion technology.
For further information, e-mail info@nft.netzsch.com, visit http://grinding.netzschusa.com/, or call 484/879.2020, fax 610/280.1299.
Looking for a reprint of this article?
From high-res PDFs to custom plaques, order your copy today!