Tailored Pigments - The Foundation for Outstanding Inks

The first inkjet printers were introduced to the market in the early 1950s. In the 1980s, inkjet office printers set out to conquer the printing market. Since then, the basic principle of inkjet printing has remained the same. Ink droplets are produced by different methods (see Sidebar below) and propelled through nozzles onto the substrate. The targeted positioning of the droplets creates a dotted image whose resolution (measured in dpi = dots per inch) is determined by the droplet size. The droplets are so minuscule that they are not visible to the naked eye.
Inkjet printing has been an ongoing success, although today’s printers have not much in common with the first models. Numerous new developments, both in the field of printing technology and ink quality, have opened up a wide range of applications. Inkjet is mainly used in three areas. There is no other printing technology that can provide simple prints at costs as low as inkjet. But even for high-quality prints, inkjet is the method of choice because it provides images with highest resolution and top quality. And, last but not least, inkjet printing is also in high demand for wide-format printing, not only for indoor applications, but also for outdoor posters, billboards, films and tarpaulins.
The success of inkjet relies on the color pigments in the inks. A new generation of organic pigments for inkjet inks from the Pigments & Additives Division of Clariant offers colors that are not only brilliant and colorfast, but also lightfast and weatherfast. Their advantageous property profile is rounded off by easy dispersibility in ink systems with low viscosity.
Triple S: the Formula for Optimal Pigments
The chemical properties of pigments are determined by their chemical structure. However, latest research demonstrates that the physical properties also have significant influence on pigment quality. Decisive parameters are pigment size, pigment shape and pigment surface. The ”Triple S“ (Size, Shape, Surface) concept demonstrates how the targeted modification of these three parameters can optimize pigment properties.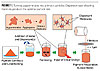
Particle Size: Middle is Optimum

Surface Properties: Charged or Neutral
The polarity, and thus the hydrophilic or hydrophobic properties of pigment particles, depends on their morphology, which is determined at the pigment synthesis stage. It is possible to produce pigments with a surface that is positively or negatively charged to varying degrees, or neutral. The surface charge influences the dispersion behavior. Highly charged pigments are hydrophilic and feature outstanding wettability in aqueous systems (Type B in Figure 2). Neutral pigments are hydrophobic; they float at the surface of aqueous systems (Type A in Figure 2) and are easily dispersible in solvent-based systems. The choice of dispersion agent depends on the charge of the pigment. For optimal wetting behavior and the best possible dispersion of the pigment in the ink, the surface properties of the pigments must be perfectly matched to the individual application.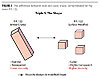
Rods or Cubes?
The third determining parameter of the Triple S concept is the crystalline shape of the pigments. Typical crystalline shapes are needles, flakes, rods or cubes. The pigment synthesis and the finishing determine the crystal shape. Figure 3 compares and contrasts two different crystalline shapes of Pigment P.R. 122 and their impact on properties. The rod-shaped pigment has lower viscosity, while the cubic pigment features higher transparency, which is usually favored.From Raw Pigments to Ready-To-Use Inks
High-quality raw pigments are a solid foundation for the production of superior inks. However, ink manufacturers today prefer to buy pigment preparations, which are usually easier to process, rather than raw pigments. In the past, mainly solid preparations were used, but the demand for liquid pigment preparations is increasing. Dispersions with pigment content of around 20% in solvents such as PM acetate are available. The main advantage of the liquid preparations is easy processing. They are simply incorporated into the mixture, which significantly reduces the preparation time for inks.Both solid and liquid pigment dispersions can be used to produce solvent- and water-based inks. Water-based inks are primarily used indoors because they do not release any solvent vapors. The preferred choice for outdoors is solvent-based inks because they dry quickly and can also be applied onto non-absorbing substrates, such as sheeting or films and tarpaulins. Solvent-based pigment preparations have a longer shelf life and require few biocide and fungicide additives.
Sidebar 1: Different Inkjet Printing Technologies
The most commonly used inkjet technology is drop-on-demand. There are different ways of droplet generation.In droplet generation using piezoelectric material , the application of electricity changes the shape of the platelets or rods, which generates a pressure pulse in the inkjet channel. This forces a droplet of ink through the nozzle, forming a droplet. The main advantage of this technology is the absence of high temperatures, allowing the use of heat-sensitive components.
In the bubble-jet method , ink droplets are generated by a small heating element next to the nozzle that causes the ink to evaporate. This is followed by a spontaneous increase in volume, which propels the release of a droplet. In the following, the gas re-condensates and sucks in more ink. The colorants and other components of the inks used in this technology must be thermally stable, as the temperature reaches peaks of 400 °C.
Much less common are printers with continuous inkjet flow . A high-pressure pump produces an inkjet that a pulsating piezoelectric transformer breaks into droplets of equal size at equal distance. The droplets that are not to be applied onto the substrate are deflected from the inkjet. These ”undesired“ droplets are electrically charged in their trajectory by a charging electrode. The droplets that are meant to reach the substrate remain uncharged. In addition to ink, the continuous flow method can be used for other liquids, such as coatings, and even adhesives.
Sidebar 2: Inkjet Inks Must Fulfill an Impressive Array of Requirements
Ink droplets of the correct size are necessary to obtain satisfactory printing results. The ink must have a certain viscosity and surface charge, while both parameters must perfectly match the printing technology and the nozzle.On the printed material, the ink must create an image with high contrast, which can only be achieved with a high colorant content. However, if the pigment content in the ink exceeds a certain maximum, the pigments may precipitate. Inks for bubble-jet printers must also be heat-resistant up to 400 °C.
Immediately after printing, the ink must be smudge-proof but it must not dry out when the printer is inactive. Prints must also be lightfast and water-resistant over a long period of time. Modern inks must also be non-toxic and not contain carcinogenic substances.
Looking for a reprint of this article?
From high-res PDFs to custom plaques, order your copy today!