Innovative Black Acrylic Brings Style and Durability to Cadillac
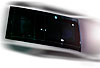
Cadillac designed its SRX crossover SUV to be a sleek and elegant luxury utility vehicle. Its swept-back and angular styling upholds the tradition of the automaker known for its sophistication. Continuing in that tradition is the Crossover sunroof, developed by Webasto, a leading Tier 1 supplier of roof and heating systems, who used an innovative acrylic material from Evonik CYRO LLC that delivered manufacturing and performance benefits to the sunroof appliqué manufacturing process.
Long-recognized for its quality, Webasto wanted to find an alternative to conventional polycarbonate or metal for the appliqués used on the sunroof, offered as part of the SRX’s Premium Luxury Collection package. Webasto project engineer Lisa Pomeroy needed an engineering polymer that could not only deliver the style expected by Cadillac but also simplify manufacturing and control costs.
“In the past we used a TPU (thermoplastic urethane) part and painted it to create the trim panels on cars,” explained Pomeroy. “This always created a lot of issues. We had to deal with costly factors such as overspraying, ‘orange peeling,’ and repainting. Often times, the result was the part became too thick. When you also consider the numerous rejections that follow such issues, you’re dealing with an expensive problem.”
Beyond the cost of imperfections created while coating the appliqués, additional setbacks occurred during the process. Webasto could not paint the material on-site in its Rochester Hills, MI, facility. Rather, the appliqués had to be sent to an outside vendor, who coated the material after the molding process was complete. If there were any imperfections with the coating or if any of the aforementioned issues occurred, the process had to be restarted until the finished product met the quality criteria.
Pomeroy and her team found their solution after meeting with Applied Plastic Products, a molding company based in Fair Haven, MI, that specializes in the automotive industry. Vice President Paul Taylor suggested using a polymethyl methacrylate (PMMA) for the injection-molded appliqués. He believed PMMA was the best material because it molds in one step to yield a clearcoat painted look without the coating step. After careful evaluation, the ACYLITE FT8 piano black acrylic polymer was selected.
“Of all the PMMAs we tested, ACRYLITE FT8 had the best performance. In post-mold tests, after being placed in a hot environment 24 hours after molding where most acrylics shrink, the FT8 had the highest stability,” said Pomeroy. “It had the best performance in -30 °C/+95 °C tests and it was domestically made, making it less expensive than European alternatives.”
The use of ACRYLITE also brought benefits in terms of overall look. Trim panels made from polycarbonate plastic or metal require a protective coating. If (or more accurately, when) the coating is penetrated, the entire trim needs to be replaced, resulting in a pricey and inconvenient repair for the consumer. ACRYLITE FT8 has a robust, high-gloss surface that allows minor scratches to be easily polished away.
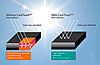
High Durability
Complications from painting aside, polycarbonate and metal often fall victim to Mother Nature. Conversely, ACRYLITE FT8 has exceptional weathering properties so that, in spite of the direct exposure to the sun, the material maintains its high-gloss appearance and deep jet-black color for the life of the car.Warping was also a potential concern that had to be addressed. Webasto, which has won numerous automotive design awards, adheres to strict quality standards. The four-plus foot appliqués had to fit perfectly on the Cadillac SRX’s roof and adjacent metal parts, and maintain that fit, so there would be no rattling or undesirable stress. Additionally, the fact that the acrylic did not warp ensures that the weather strip mounted along a flange over the whole breadth of the frame has no undulation.
The functional strength of the acrylic also proves advantageous during operation of the sunroof. Because the electric motor that opens and closes the sunroof is mounted on the frame, the appliqués must absorb the tensile, compressive and bending stresses associated with its operation.
Synergistic Approach
A successful design takes more than the right materials; there must be synergy between the various companies. That was the case with the design of the sunroof appliqués.Evonik Cyro provided Webasto with detailed mold and gate analyses for each of its products tested, including the ACRYLITE FT8. Evonik Cyro worked closely with Applied Plastics Products throughout the entire process and offered consultation on all molding issues. In fact, the working relationship led to the blending of certain materials that improved the properties of the polymer for this specific application.
“Evonik Cyro was very helpful during the entire testing and molding process. In regards to appearance and performance, our high expectations have been met. We were looking for an acrylic that could provide a black sheen exterior free from imperfections. Between an acrylic and a painted coating, the difference is night and day. The molded acrylic provides a much nicer, easily distinguishable final product,” said Pomeroy.
A project that set out to maintain the high standard of quality associated with the Cadillac brand and continue the reputation of Tier 1 supplier Webasto was ambitious. Using innovative materials and working as a team, sunroof appliqués were developed that offered improved quality and a robust stylish appearance, while also improving manufacturing efficiency.
Evonik Cyro LLC is an Evonik Degussa Corporation group company. Headquartered in Parsippany, NJ, Evonik CYRO is a leading manufacturer of durable solid surface sheet and molding compounds, and bulk and performance monomers. Evonik Cyro manufactures and markets its durable solid surface sheet products under the ACRYLITE® trade name in the Americas. These same products are manufactured and marketed under the PLEXIGLAS® trade name throughout the rest of the world.
Looking for a reprint of this article?
From high-res PDFs to custom plaques, order your copy today!