Polyester Polyols Based on Polymerized Fatty Acids From Renewable Resources
High-performance
materials such as solventborne coatings have been produced from polyurethanes
for many years. However, with current regulatory pressures, a move to water
systems and to materials from bio-based renewable resources is necessary.
Although it is possible to formulate waterborne polyurethane systems, the
widely used adipate polyester backbones often cause problems, such as reduction
in storage stability and hydrolytic resistance. Additionally, the water
evaporation rate of polyurethane dispersions is seen as a drawback in certain
applications such as UV-curable coatings and adhesives.
However, a range of hydrolytically stable polyester polyols using bio-based technology has overcome these deficiencies. The reduced number of ester bonds and the hydrophobic environment make these polyols practically immune to water, while maintaining thermal- and UV-resistance characteristics.
In this paper, it is demonstrated that these polyester polyols, produced from C-36 dimer fatty acids, improve the hydrolytic and storage stability of polyurethane dispersions. Additionally, results will show that UV-curable polyurethane dispersions produced from these polyols exhibit these same properties, as well as significant improvement in water evaporation that leads to improved cure time.
Finally it will be demonstrated that the adhesion properties of coatings on different plastic substrates improve considerably.
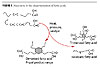
Starting from the C-18 acids that nature typically provides, the dimer acid is a molecule with 36 carbon atoms, which makes it by far the longest dioic acid available. This hydrocarbon nature makes the dimer acid and polymers in which it is included extremely hydrophobic. In addition, the combination of hydrocarbon character and non-crystallinity provides lubricity and flexibility, even at very low temperatures.
Dimerized fatty acids have found their application in areas such as polyurethane, UV-curable and polyester coatings, both solvent and waterborne systems. In all these applications, the value of the dimerized fatty acid is related to the features mentioned: flexibility and impact strength, wetting and flowability, and hydrophobicity and hydrolytic resistance.
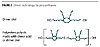
When comparing polyurethanes based on dimerate polyesters to adipate polyesters, polycaprolactone polyols and polyether polyols, it becomes clear that they form a category of their own. Compared to the adipates, the dimerates exhibit much lower moisture absorption, lower hydrolysis rate, and greater flexibility. In comparison with polyethers such as polyethylene glycol (PEG), polypropylene glycol (PPG), or polytetramethylene glycol (PTMEG), the absence of ether linkages makes dimer-based polyurethanes much more resistant to degradation by radical-type attack, such as heat, oxidation or ultraviolet radiation.
This combination of stability against both hydrolysis and radical-type attack is unique, and is highly relevant for applications like heavy-duty coatings and adhesives, and automotive elastomers. Additionally, it has been found that dimer technology brings low-temperature flexibility, flowability and affinity for low-energy surfaces. No monomer comes closer in composition to a polyolefin than dimer acid.
A range of dimer-based polyester polyols is commercially available, and these materials have been tested in polyurethane dispersions. The fact that dimer fatty acids are hydrophobic makes it challenging to disperse them in water, but this can be resolved by using the correct addition method during processing.
The polyurethane dispersions based on the dimer acid technology exhibit mechanical strength, adhesion, grain enhancement, gloss and chemical resistance. Especially noticeable is the improved resistance to water when compared to adipate-based polyester polyols. The dimer fatty acid-based polyol shows no damage to the surface, where the adipate shows severe damage after hydrolytic exposure to the surface.
Additionally,
the water uptake of the polyurethane films has been evaluated. In Figure 3, one
can clearly see that the hydrophobic character of the dimer fatty acid has a
positive impact on water uptake. The adipate-based polyurethane film absorbs up
to 8% water at 23 °C and the PTMEG-based films even up to 10% versus only 1-2% for
dimer fatty acid-based polyols.

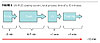
UV-polyurethane dispersions were prepared using the prepolymer process route in which the addition reaction between the dimer-based polyester polyols, dimethylolpropionic acid and isocyanates takes place in the presence of water-dilutable solvents such as ethyl acetate. The formation of the prepolymer takes place in the organic phase and after the theoretical NCO content has been reached, the prepolymer is further reacted with pentaerythrytol triacrylate. Before transferring the polymer into the water, the carboxyl groups are neutralized with a tertiary amine. Once successfully dispersed into water, the low-boiling solvent is removed by gentle distillation, to give a solvent-free UV polyurethane dispersion with a solids content of approximately 35%.
For this study polyols with a Mw of 2000 were used. These were hexanediol adipate, PTMEG-diol, a semi-crystalline dimerate and an amorphous dimerate. The coatings were cured using 4 passes 80 Watt/cm at a speed of 15 m/min for the evaluation of the chemical and mechanical resistance at a thickness of 50 µ dry coating.
A major disadvantage of UV-PUDs is that an additional step of drying is required to remove the water from the system. Keeping in mind the hydrophobic nature of the dimer fatty acid-based polyester polyols and the need to evaporate the water before UV curing, the influence of the hydrophobic dimer-based polyols was screened.
For this we looked at a drying cycle used in the industry when UV-PUDs are applied. As can be seen in Figure 6 the drying step in the oven for the water evaporation is a time-consuming step. If one could increase the evaporation rate of the water, this time could be shortened. The UV-PUDs prepared in this study were evaluated on the loss of water during the drying. For this a thermographic analyses was used, using the same weight and solid content of the dispersions. IR-drying was used for the oven, at a temperature set at 60 °C. The results in Figure 7 show that both polyesters containing dimer fatty acid exhibit a definite advantage in terms of faster water evaporation over the adipate ester and the polyether.
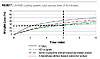
The
adhesion of uncrosslinked PU dispersion is highly improved upon addition of
dimer into the polyol. For crosslinked PU dispersions, the adhesion is
comparable for all PU dispersions.
The PU dispersion based on the adipate polyol gives a low adhesion to tested substrates and fails almost immediately. Dimer improves the adhesion significantly, probably due to the increased flexibility of the coating, resulting in increased stress absorption. The test results are shown in Figure 8.
Furthermore, the morphology of the dimer fatty acid structure within the polyester polyol leads to significant improvement in the adhesion on plastic substrates such as PET, ABS and PE in comparison with adipate-based polyols.
Polyester polyols based on dimer fatty acids from renewable bio-based resources form a class of versatile raw materials for polyurethane dispersions that allow the resin producer to overcome some of the major challenges of this technology.
This paper was presented at the Waterborne Symposium sponsored by The University of Southern Mississippi School of Polymers and High Performance Materials and The Southern Society for Coatings Technology, 2009, New Orleans, LA.
However, a range of hydrolytically stable polyester polyols using bio-based technology has overcome these deficiencies. The reduced number of ester bonds and the hydrophobic environment make these polyols practically immune to water, while maintaining thermal- and UV-resistance characteristics.
In this paper, it is demonstrated that these polyester polyols, produced from C-36 dimer fatty acids, improve the hydrolytic and storage stability of polyurethane dispersions. Additionally, results will show that UV-curable polyurethane dispersions produced from these polyols exhibit these same properties, as well as significant improvement in water evaporation that leads to improved cure time.
Finally it will be demonstrated that the adhesion properties of coatings on different plastic substrates improve considerably.
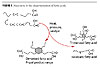
Dimer Fatty Acids
Natural oils and fats have for years provided the polyurethane chemist with a variety of building blocks, such as glycerine and castor oil. Less well known is the use in polyurethane chemistry of a fatty acid derivative, the so-called dimerized fatty acids. These are obtained by the conversion of unsaturated fatty acids (from sources like soybean oil or tall oil) by a combination of pressure, temperature and catalysis. This process generates a mixture of products, the most important being dimerized fatty acid. Others are trimerized fatty acid, and isostearic acid (Figure 1).Starting from the C-18 acids that nature typically provides, the dimer acid is a molecule with 36 carbon atoms, which makes it by far the longest dioic acid available. This hydrocarbon nature makes the dimer acid and polymers in which it is included extremely hydrophobic. In addition, the combination of hydrocarbon character and non-crystallinity provides lubricity and flexibility, even at very low temperatures.
Dimerized fatty acids have found their application in areas such as polyurethane, UV-curable and polyester coatings, both solvent and waterborne systems. In all these applications, the value of the dimerized fatty acid is related to the features mentioned: flexibility and impact strength, wetting and flowability, and hydrophobicity and hydrolytic resistance.
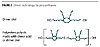
Polyurethane Dispersion Based on Dimer Technology
The dimer fatty acids provide polyester and polyurethane coatings with a range of favorable features, such as flexibility and hydrolytic resistance. Clearly, other coating systems could benefit from the introduction of dimer acids as well. Conversion of dimerized fatty acid to the corresponding diol, or by building dimerized fatty acid into hydroxyl-terminated polyesters, makes it suitable for incorporation in polyurethanes (Figure 2). The dimer fatty acid-based polyester polyols can be semi-crystalline or amorphous type, depending on the choice of polyol monomer.When comparing polyurethanes based on dimerate polyesters to adipate polyesters, polycaprolactone polyols and polyether polyols, it becomes clear that they form a category of their own. Compared to the adipates, the dimerates exhibit much lower moisture absorption, lower hydrolysis rate, and greater flexibility. In comparison with polyethers such as polyethylene glycol (PEG), polypropylene glycol (PPG), or polytetramethylene glycol (PTMEG), the absence of ether linkages makes dimer-based polyurethanes much more resistant to degradation by radical-type attack, such as heat, oxidation or ultraviolet radiation.
This combination of stability against both hydrolysis and radical-type attack is unique, and is highly relevant for applications like heavy-duty coatings and adhesives, and automotive elastomers. Additionally, it has been found that dimer technology brings low-temperature flexibility, flowability and affinity for low-energy surfaces. No monomer comes closer in composition to a polyolefin than dimer acid.
A range of dimer-based polyester polyols is commercially available, and these materials have been tested in polyurethane dispersions. The fact that dimer fatty acids are hydrophobic makes it challenging to disperse them in water, but this can be resolved by using the correct addition method during processing.
The polyurethane dispersions based on the dimer acid technology exhibit mechanical strength, adhesion, grain enhancement, gloss and chemical resistance. Especially noticeable is the improved resistance to water when compared to adipate-based polyester polyols. The dimer fatty acid-based polyol shows no damage to the surface, where the adipate shows severe damage after hydrolytic exposure to the surface.
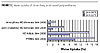
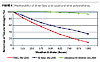

Hydrolytic Resistance
One of the challenges of water-based systems is the hydrolytic stability on storage. This is especially the case when polyester polyols are incorporated within the backbone of the polyurethane. Several polyurethane dispersions were exposed to storage at 50 °C after which the retention of the film strength was re-evaluated. Figure 5 shows that inclusion of dimer fatty acid-based polyester polyols in the backbone significantly improves the storage stability over an adipate-based polyester polyol. This can be explained through the hydrophobic nature of the dimer-based polyester polyols, protecting the ester-bonds from hydrolysis.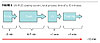
UV-Curable Polyurethane Dispersion
As demonstrated, polyurethanes based on dimer-based polyester polyols exhibit significantly improved hydrolytic stability and weatherability. These improvements are also relevant to the UV polyurethane dispersions.UV-polyurethane dispersions were prepared using the prepolymer process route in which the addition reaction between the dimer-based polyester polyols, dimethylolpropionic acid and isocyanates takes place in the presence of water-dilutable solvents such as ethyl acetate. The formation of the prepolymer takes place in the organic phase and after the theoretical NCO content has been reached, the prepolymer is further reacted with pentaerythrytol triacrylate. Before transferring the polymer into the water, the carboxyl groups are neutralized with a tertiary amine. Once successfully dispersed into water, the low-boiling solvent is removed by gentle distillation, to give a solvent-free UV polyurethane dispersion with a solids content of approximately 35%.
For this study polyols with a Mw of 2000 were used. These were hexanediol adipate, PTMEG-diol, a semi-crystalline dimerate and an amorphous dimerate. The coatings were cured using 4 passes 80 Watt/cm at a speed of 15 m/min for the evaluation of the chemical and mechanical resistance at a thickness of 50 µ dry coating.
A major disadvantage of UV-PUDs is that an additional step of drying is required to remove the water from the system. Keeping in mind the hydrophobic nature of the dimer fatty acid-based polyester polyols and the need to evaporate the water before UV curing, the influence of the hydrophobic dimer-based polyols was screened.
For this we looked at a drying cycle used in the industry when UV-PUDs are applied. As can be seen in Figure 6 the drying step in the oven for the water evaporation is a time-consuming step. If one could increase the evaporation rate of the water, this time could be shortened. The UV-PUDs prepared in this study were evaluated on the loss of water during the drying. For this a thermographic analyses was used, using the same weight and solid content of the dispersions. IR-drying was used for the oven, at a temperature set at 60 °C. The results in Figure 7 show that both polyesters containing dimer fatty acid exhibit a definite advantage in terms of faster water evaporation over the adipate ester and the polyether.
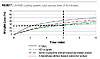
Adhesion Properties
The adhesion properties of the polyurethane dispersions were evaluated, not using normal coating adhesion test methods but a method used in the adhesive industry. This has been done to distinguish in an alternative way the adhesive strength of the PU dispersions. The method used is a lap shear adhesion test, where the polyurethane dispersions were tested on several plastic substrates.
The PU dispersion based on the adipate polyol gives a low adhesion to tested substrates and fails almost immediately. Dimer improves the adhesion significantly, probably due to the increased flexibility of the coating, resulting in increased stress absorption. The test results are shown in Figure 8.
Conclusion
It has been demonstrated that the polyester polyols based on dimerized fatty acids offer several unique properties to polyurethane dispersions. The hydrophobic nature of these products significantly improves the hydrolytic stability of the polyurethane dispersions and, therefore, improves the storage stability of these products. The same hydrophobic properties also enhance the evaporation rate of the water during the drying cycle of UV- polyurethane dispersion systems.Furthermore, the morphology of the dimer fatty acid structure within the polyester polyol leads to significant improvement in the adhesion on plastic substrates such as PET, ABS and PE in comparison with adipate-based polyols.
Polyester polyols based on dimer fatty acids from renewable bio-based resources form a class of versatile raw materials for polyurethane dispersions that allow the resin producer to overcome some of the major challenges of this technology.
This paper was presented at the Waterborne Symposium sponsored by The University of Southern Mississippi School of Polymers and High Performance Materials and The Southern Society for Coatings Technology, 2009, New Orleans, LA.
Looking for a reprint of this article?
From high-res PDFs to custom plaques, order your copy today!