A Turn for the Best
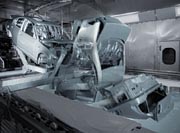
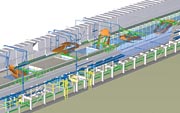
The first of these new pretreatment and electrocoating plants to be installed anywhere in the world is now in operation at the BMW Group factories in Munich and Dingolfing. The hanging conveyor technology for the spray coating system in Munich and the vertical vehicle body immersion system in Dingolfing have been replaced by a conveyor technology that rotates the vehicle bodies as they pass through the dip tank. In addition to the plant engineering benefits, this system also offers advantages in terms of process improvements for the treatment of the vehicle bodies. Flexibility while passing over a tank, an even flooding of cavities and minimum material carryover are only a few of the innovations that were achieved by this new conveyor technology, which, at first glance, seems amazingly simple.
In addition, the new technology offers a further advantage that should not be underestimated. Compared to a pendulum conveyor system, the new system can be made much shorter because the bodies are rotated to enter the tank vertically, which means that the slopes that are necessary in pendulum conveyor systems to move the bodies into and out of the tanks are no longer required. This reduces plant construction costs considerably. All of these benefits persuaded the BMW Group to install RoDip-3 technology.
For the first time, the process ensures that no moving parts or drives should be used above or in the tank areas. This ensures that the drag-in of caked material or wear from the chain drive, which would otherwise appear sooner or later as inclusions in the body finish, is avoided.
Regarding the mechanical system, the bodies are mounted onto a skid carrier, which is attached to a chain at a specified cycle distance. The carrier allows the body to be rotated 360 degrees around its own axis. The turnstile mounted on the side is steered by guide rails so that the body can be tipped at any specified angle up to a complete rotation. Due to their straight-line motion compared to an overhead conveyor, chain drives can be expected to have a longer service life and lower maintenance costs. The prerequisite for this, however, is that the chain is kept as far away as possible from aggressive tank materials.
The body-in-white is attached to the body carrier by fixture shafts. These are bolted to the vehicle and are locked to the body carrier at the handover point from the floor conveyor to the RoDip-3 unit. The locking is electrically monitored to ensure that the body cannot be released from the carrier. If any parts should fall from a body--a door distance rod or a boot or bonnet lid, for example--cables stretched across the floor of the tank set off an alarm. The lost parts can then be retrieved before any damage is caused to subsequent vehicle bodies. The vehicle's doors, as well as the boot and bonnet lids, are held open by steel rods to ensure that the interior of the car can also be more easily covered by the tank material. A testing station is necessary to guarantee the process reliability of these distance rods. The automatic testing station intensively shakes the doors and lids to ensure that they are locked firmly in place.
"Somersault" through the tank
For the new construction of the coating line, the process sequence in the pretreatment and electrocoat area was designed in collaboration with the chemicals supplier to achieve optimum quality. The degreasing zone consists of a total of four different cleaning stages. In the first zone, the body, which is in a vertical position, is rinsed through from one end to the other using a large quantity of water under low pressure. By this means, swarf, sanding dust and other coarse dirt, especially that remaining in the cavities, is removed. The subsequent washing station, which has brushes at the top and sides, mechanically removes any dirt or contamination adhering to the outer skin of the body, thus providing a smooth and well prepared surface for the coating process.
This is followed by two degreasing zones (with a total of five minutes of treatment time at an increased temperature), which dissolve any oil or grease residues. For this purpose, the body "turns a somersault" in one of the dip tanks, meaning that it is rotated out of the tank and immediately rotated back in again. This produces a turbulent flow of liquid in the cavities, supporting the cleaning effect.
After chemical activation of the surface, a dip process adds a phosphate coating. Here, a "minimized coat" process is used for treating larger aluminum surface areas. Minimized coat phosphatizing involves a lower degree of pickling of the aluminum surface, resulting in the production of less cryolite sludge. This means that treatment of different substrates with an aluminum proportion of less than 30% is possible during the dipping procedure. The rinsing zones after degreasing and phosphate coating are each equipped with two dip tanks and a subsequent fresh-water spray ring.
Virtually no material carryover
The special flexibility of the RoDip-3 unit becomes particularly apparent during phosphate coating. If it should become necessary in the future to spray certain substrates instead of dipping them, a set of points can be used to select whether a body is dipped in the tank or guided over the tank for spraying in the treatment zone, depending on the body's requirements.
Aluminum treatment in the tank is also supported by direct filtration, pointed funnels in the tank floor and flood nozzles on the sides. The above-mentioned rinsing zone is followed by a passivating zone and a zone with deionised (DI) water. In all cases, the rotation of the body and the optimized lengths of the transfer zones result in minimum material carryover and reduced water and chemicals consumption.
Process engineering highlights
The entire process engineering was strongly influenced by the chemical process, and therefore has a number of special features that cannot be found in conventional systems.
Starting with the design of the dip tanks, one notices the special shape of the tank floor, which has pointed funnels exclusively in those areas where dirt or sludge collect. This allows dirt or chemical agglomerates that cannot be kept suspended in the tank to settle in the lower tank area, where they can be directly removed from the process in a concentrated form using suction pipes.
The tunnel above the process tanks was specifically designed with a 30-degree roof angle. As a result, any condensate that collects on the ceiling runs toward the side walls of the tunnel, and therefore away from the process tank. This rules out the possibility of the body's outer skin being contaminated by media dripping from the tunnel ceiling.
The dip tanks, conveyors and tunnels, as well as most of the peripheral equipment are all made of stainless steel (1.4301). The phosphate coating area and the subsequent rinsing zones use higher-grade stainless steel, since the treatment of aluminum components involves the use of large quantities of free fluoride in the phosphate tank. Under such conditions, V2A steel would fail at an early stage. This unit, however, is designed to have a lifetime of 20 years.
Cleaning the body-in-white
The sophisticated design of the cleaning zones allows a total cleaning time of seven minutes. The deluge cleaning station, a brush washing unit, two immersion degreasing zones and the three-stage rinsing zone provide all the basic requirements for ensuring optimum cleaning of even heavily soiled bodies. Intensive cleaning in the body shop is no longer absolutely necessary.
The new deluge cleaning station was also designed in accordance with the requirements of the process. The body is placed vertically in the empty tank and is flooded from the rear to the front with large quantities of water under low pressure. As a result, dirt particles are efficiently washed out from inside the body and even from concealed cavities. The body is then rotated through 180 degrees and, with the front end pointing up, the rinsing procedure is repeated.
Once the body has been lifted out of the deluge cleaning station, the outer skin is mechanically cleaned in the brush-cleaning zone. Brushes at the sides and at the top clean the large, visible surface areas of the body-in-white, removing any incrustations that might still adhere. This is followed by immersion degreasing tanks, which thoroughly remove any oil and dirt residues, especially from inside difficult-to-access cavity areas.
The position of the body in the phosphate tank is very important for proper treatment. The RoDip-3 system allows the body to pass through the tank upside down, or at any other angle if so required. This means that dirt particles settle on the underside of the body, where they do not disturb the subsequent finishing process. Such inclusions on the outer skin of the body would result in considerable reworking.
New method of sludge processing
Another special feature of the system is the processing of the sludge in the phosphate coating area. Besides the above-mentioned pointed funnels, two simultaneously operating filter presses are responsible for direct filtration to ensure the even removal of phosphate sludge. The presses work one after the other, so that while one press is being cleaned, the other is able to maintain the process.
Furthermore, if cryolite sludge is produced in the phosphate coating tank, separation using filter presses with a membrane system is absolutely necessary. The fine, gel-like sludge quickly blocks the pores of the filter cloths and can only be converted by further pressing by the movable membranes to form a dry filter cake (50% residual moisture), which can then be easily removed from the filter cloth.
For the treatment of aluminum surfaces, additional flood nozzles integrated into the sides of the treatment tank are required. These nozzles direct the phosphate medium specifically against the outer skin, thus creating turbulences at the moment of immersion and allowing a rapid exchange of medium at the metal surface. This makes it easier for the tank medium to attack the aluminum surfaces and avoids the inclusion of sludge particles.
Much less reworking
The electrocoat line at BMW's Munich assembly plant, which also uses RoDip-3 technology, meets all the requirements regarding the coating process: an even distribution of the film thickness over the outer skin, virtually no inclusions in the electrocoat and the avoidance of run-outs in critical body structures.
Altogether, the process optimization substantially reduced rework. These improvements were achieved using RoDip-3 technology with an optimized tank design, including all the necessary integrated and peripheral parts. The rotation of the body ensures that all cavities are flooded and that no air bubbles remain. Moving the bodies upside down through the tank prevents the sedimentation of particles on the up-facing horizontal surfaces of the body. Furthermore, rotating the body as it leaves the tank makes sure that all cavities are completely drained, thus preventing marking by dripping material.
The combination of pretreatment and electrocoat in RoDip-3 technology offers two basic advantages. First, fewer dirt particles are carried over into the electrocoat tank because the RoDip-3 process ensures that dirt is almost completely removed from the bodies in the pretreatment tank.
Second, a very uniform phosphate coating is achieved, forming the basis for a correspondingly homogeneous electrocoat layer.
A special feature of the tank design is the flood nozzles integrated into the sides, which ensure that even unusual body shapes are coated with a high level of process reliability. The electrocoat material, supplied by DuPont, showed excellent results after slight modifications to adapt it to the new system.
Overall, the more even film thickness distribution over the vehicle body made it possible to optimize the material consumption.
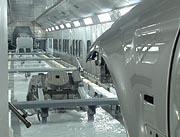
One advantage of the RoDip-3 design is that the process tunnel is wide enough to allow inspection from the inside. This greatly facilitates cleaning and allows access to the unit if a breakdown occurs. A disadvantage is the coupling of the process tanks with the conveyor equipment, which results in contamination of the transport chain, although this has no effect on its operation. Furthermore, no moving parts are located above the process tanks, which means that any dirt that collects on the chain, for example, will fall into the tunnel and not into the tank. The body carriers are returned underneath the unit. The space required for returning them can be provided either by raising the unit on a steel frame or by feeding the chain back below floor level.
The accessibility of the spraying system in the tunnel was a great challenge at first. Due to the rotation of the bodies, the spray rings can reach a height of up to three meters above the rim of the tank, making them difficult to reach from the tank rim. The installation of simple steel walkways in the tunnel at the same height as the spraying systems allows both access to the spray nozzles and the disassembly of the entire spray rings for maintenance. The conveyor chain is fed back below floor level.
Improved surface quality
The quality requirements to be met by the new pretreatment and electrocoat lines were very high and are fully achieved today. Both the number of inclusions on the bonnets and the particle size were reduced. The phosphate coats achieve very uniform film thickness results visually and in laboratory tests, not only on the outer skin but also in the cavity areas. Images made using scanning electron microscopes show a very fine crystalline and fully closed phosphate layer on all of the substrates--aluminum, steel, electrogalvanized, and hot-dip--used in the BMW Group. This made it possible to once again substantially improve the surface quality achieved at the Dingolfing and Munich factories, especially in view of the variety of substrates used.
Wastewater and chemical consumption cut
Optimizing wastewater and chemical consumption were the main goals for constructing the new plants. A substantial improvement was achieved in two ways.
First, the new conveyor technology changes the draining of the bodies. Rotating the body empties all the flooded cavities, as far as the holes in the body allow. Material carried over from tank to tank is therefore reduced to the water that is retained on the surface of the bodies. Chemical consumption is reduced by approximately 30%.
Second, the rinsing zones with at least three stages are arranged in a cascade system and the conductance of the rinsing tanks is additionally monitored by the plant control unit.
Furthermore, the degreasing tanks are replenished with rinsing agent, the final rinsing with deionized water is cascaded with the phosphate rinsing tanks, and the entire electrocoat unit is operated as a closed circuit. Altogether, this results in a 50% reduction in the quantity of wastewater generated and a reduction in the disposal of phosphate sludge by about 20%.
Summary and outlook
The new construction of the pretreatment and electrocoat lines in Munich and Dingolfing is an impressive demonstration of the technical possibilities offered by a modern and flexible production plant. The combination of innovative conveyor technology (RoDip-3, supplied by Dürr Industries Inc.), the optimum process cycle and the early integration of experienced plant operators and plant manufacturers resulted in a system that sets new standards in the field of pretreatment and electrophoretic coating.
The new lines improved the quality of the surface treatment, created flexibility in the treatment of the most varied body types and substantially reduced the consumption of chemicals and the generation of wastewater. Future plants can be made even more flexible by replacing the drive chain with self-propelling transport systems. However, the high reliability and the low maintenance requirements of a RoDip-3 unit with a chain drive can hardly be surpassed.
Looking for a reprint of this article?
From high-res PDFs to custom plaques, order your copy today!