Calculating the Cost of E-Coat
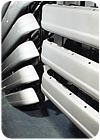
Electrocoat is sold by the gallon, but all gallons are not created equal. The price per gallon and coverage can vary from supplier to supplier. Different products from the same supplier can vary in cost and coverage per gallon. In addition, the amount of coverage and cost per square foot for a specific product can vary depending on operating conditions. The main variables that affect coverage and cost per square foot are film thickness, percent volume solids and film shrinkage (see sidebar).
Each of these variables has other variables that can affect it. The associated variables of percent volume solids and film shrinkage are discussed in detail. Film thickness has so many variables that the scope of such a work is too large for this article. But the impact of film thickness on coverage is presented. In addition, the relationship of percent volume solids and film shrinkage to film thickness also is presented. I will not quote lab work and extensive studies in this article; you do not coat parts in the lab. Lab work is nice to use as a guide but may not represent actual shop conditions. I will try to supply you with procedures and formulas that can be used by the average electrocoat shop to determine their coverage and cost per foot squared.
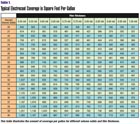
Percent Volume Solids
Percent volume solids are the amount of paint per unit volume that can be applied to a part. They are not the same as percent weight solids. Percent weight solids are the amount of paint per unit weight that is non-volatile. Percent volume solids are available from the paint suppliers. If a gallon of paint has percent volume solids of 50, half of the gallon can be applied to a part. A gallon of paint with volume solids of 50 will cover approximately 800 square feet at 1 mil of thickness. The formula to determine the square feet per gallon is
(% of volume solids for electrocoat x 231) / (144 square inches x coating thickness in inches)
One square foot is equal to 144 square inches.
The factor 231 is the amount of cubic inches in a gallon.
One mil is equal to 0.001 inches.
Table 1 illustrates the amount of coverage per gallon for different volume solids and film thickness.
Volume solids can vary by product and by feed ratio. Resin and pigment will have different volume solids. To determine the combined volume solids, the following formula is used:
(Fed Ratio x Resin Volume Solids + Pigment Volume Solids) / (Fed Ratio + 1)
Fed ratios are generally expressed in parts of resin to one part pigment.
The combined volume solids of a product will vary with the fed ratio. The variation of volume solids can affect the amount of square feet a gallon of electrocoat will cover. An example of the effect fed ratio can have on volume solids is illustrated below in two examples.
Example 1: The fed ratio for a product ranges from 6.8 parts resin to 1 part pigment up to 11 parts resin to one part pigment. The resin has volume solids of 31 and the pigment volume solids are 41.
Volume Solids for a fed ratio of 6.8 to 1 = (6.8 x 0.31 + 0.41)/(6.8+1) = 32.3
Volume Solids for a fed ratio of 11 to 1 = (11 x 0.31 + 0.41)/(11+1) = 31.8
The difference in volume solids illustrated above is approximately 1.5 percent or about 8 square feet per gallon. This may not seem like much until you work the numbers. If a shop is using about 12,000 gallons a year, the difference equates to 96,000 square feet.
Volume solids vary from supplier to supplier and product to product. The above formula can be used to compare supplier to supplier and product to product. An example of the volume solids of a different product are presented below and compared with the previous example.
Example 2: The fed ratio for a product ranges from 4 parts resin to 1 part pigment up to 7.1 parts resin to one part pigment. The resin has volume solids of 34 and the pigment volume solids are 30.
Volume Solids for a fed ratio of 4 to 1 = (4 x 0.34 + 0.30)/(4+1) = 33.2
Volume Solids for a fed ratio of 7.1 to 1 = (7.1 x 0.34 + 0.30)/(7.1+1) = 33.5
The product in Example 2 will cover about 4 percent more area then the product in Example 1.
Electrocoat Film Shrinkage
An electrocoat film will shrink when cured. Electrocoat film shrinkage is defined as the amount or percentage that an electrocoat film will shrink during baking. The thickness of an electrocoat film will physically shrink or reduce during bake. The amount of the shrinkage will depend on the type of electrocoat and the bake temperature. The higher the bake, the larger the film shrinkage. Values for film shrinkage are generally not available from the supplier. There are many factors that influence film shrinkage, making it hard to quantify for general use. The film shrinkage experienced at a particular plant can be quantified using in-plant procedures. The procedures are discussed below.The bake temperature affects the amount of film shrinkage: the higher the temperature, the greater the film shrinkage. Higher film shrinkage increases the amount of electrocoat that has to be applied in the tank to achieve a film build. Increasing the amount of electrocoat applied increases the usage. Shrinkage losses can impact usage significantly.
Higher film shrinkage usually occurs in ovens where parts of different masses are processed. The oven is set up to cure heavy metal parts, the lighter parts get over baked. The lighter parts usually account for the bulk of the production. Improvements in the air flow of the oven can even out the bake, such as concentrating the air on the heavy metal parts. But first the amount of savings for such a change should be calculated. The following method can be used to determine the film shrinkage and the extra shrinkage that might be occurring because of higher bake temperatures. The method described below should be done several times to establish an average.

Determining Film Shrinkage
The following steps should be taken to determine film shrinkage. First, determine the current bake profile of the different parts. Then determine which part has highest bake or the one you want to target. Remove six pieces of the chosen part after phosphate and before e-coat. Bake the six parts in an oven for 30 minutes at 200°F. Then measure the film builds on all the panels.(Note: When measuring e-coat films, use a gage that measures at least to two decimal places. In addition, the gage needs to be properly calibrated with the correct shims.)
Then place each part back on the line and coat. Remove the parts after e-coat and before the oven. Bake the parts in an oven for 2 hours at 200°F. Measure the film builds on all the panels. Place three of the parts back on the line and bake in the production oven. Bake the other three parts in an oven at the new bake curve. Measure the film builds on all the panels. Determine the film shrinkage of each set of panels using the following formula:
(Uncured Film Build - Cured Film Build of Production Bake) / Uncured Film Build
Compare the effect of film shrinkage on coverage and between the two bakes.
Table 1 provided the theoretical coverage for a perfect e-coat system; the amount of e-coat deposited is equal to the amount after the system. Real world system loss, film shrinkage, is not considered. Table 1 can be used to determine actual coverage by adjusting the percent volume solids for film shrinkage. To adjust percent volume solids for film shrinkage, use the following formula:
percent volume solids x (1 - percent film shrinkage) = applied percent volume solids
Use the applied percent volume solids to determine actual coverage. Compare actual coverage with theoretical coverage; it usually pretty surprising.
Determining Cost per Square Foot
The cost per square foot is illustrated in Table 2. Coverage and cost per square foot are affected by many variables. These variables are controllable and/or changeable. The key factor is to identify the variables and determine the impact of changing and or controlling them. The procedures and formulas contained in this article should enable an average electrocoater to do this. Repeat the procedures several times or until there are consistency in the results. Watch for differences in the process when running the tests, try and equate differences to the results. Good decisions are based on good data.The cost of electrocoat is usually a high percentage of the total operating costs for an e-coater. Changes to the applied cost of e-coat can have an impact on operating costs and profits. You are in the business to make money, and profits are important.
For information on reprints of this article, contact Jill DeVries at devriesj@bnpmedia.com.
SIDEBAR: Film Shrinkage Vs. Percent Bake Off
Film shrinkage should not be confused with percent bake off. The two are related but not the same. Film shrinkage is the change in volume of a film that happens during the curing process. Percent bake off is the change in weight of a film during the curing process. Film shrinkage is directly related to film build and its impact on coverage is easy to calculate. When e-coaters start weighting parts to determine film thickness, percent bake off can be used to calculate coverage.Links
Looking for a reprint of this article?
From high-res PDFs to custom plaques, order your copy today!