A Little Dirt Can Hurt: The Importance of E-Coat Filtration
A substantial amount of time in the e-coat process is spent on cleaning - and for good reason. A clean vehicle improves the phosphate quality, which leads to better paint adhesion and improved corrosion performance. However, for many plants, the cleaning stages aren’t as effective as they should be. Using effective filtration technologies in automotive pretreatment systems can substantially reduce bath contaminants and e-coat defects.

A typical automotive pretreatment system comprises 12 process stages. The first five stages (deluge, car wash, spray cleaner, dip cleaner and rinse) clean the vehicle body by removing oils and dirt prior to painting. These stages are followed by a conditioner stage, a phosphate stage and five rinsing stages (two directly following the phosphate, one post-treatment, a de-ionization [DI] rinse and a DI dip rinse) prior to electrocoat (e-coat) application (see Figure 1). All of the pretreatment stages are outfitted with filtration equipment, and the goal is to provide three to four tank turns per hour through this equipment.
A substantial amount of time is spent on cleaning - and for good reason. A clean vehicle improves the phosphate quality, which leads to better paint adhesion and improved corrosion performance. Besides the obvious benefits to vehicle quality, effective cleaning of the vehicle body and removal of the contaminants from the process stream has many in-plant benefits. The removal of oil from the vehicle and the process lowers bacteria growth in water rinse stages. The removal of solids from the vehicle and the process reduces the amount of dirt in the e-coat, which minimizes sanding (and therefore labor), improves coating appearance and leads to fewer in-plant repairs. In the future, a cleaner vehicle and process will enable new pretreatment chemistries to be used by providing a consistent substrate surface quality and by allowing for the use of materials that are less tolerant to the presence of contaminants.
However, for many plants, the cleaning stages aren’t as effective as they should be. Problems such as the buildup of solids and oils in the cleaner stages, inconsistent cleaner chemistry, insufficient dwell time in the cleaning stages and ineffective filtration cause dirt, oil and other contaminants to enter subsequent pretreatment stages. In one analysis of the deluge, cleaner, rinse and DI dip stages, dirt was present in the filter bags of all stages tested (stages 1, 3, 4, 5 and 12). Oil was also discovered in the filter bags of all stages tested (stages 1, 3, 4, 5 and 12), with the largest amounts found in the cleaner dip filter bag. Additionally, sealer was present in the filter bags of stages 1 and 3, as well as in the DI dip (stage 12) just before the e-coat - a serious problem.
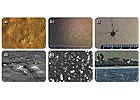
Most plants refresh their tanks at various pretreatment stages on a regular basis to reduce the buildup of solids and oils in the tanks, but this is neither an efficient nor environmentally friendly solution. On average, automotive plants use about 180 million gallons of water each year, with approximately 75 to 80% of that total being used in paint operations. A significant portion of the water used by paint operations is used in the pretreatment process. Although reductions in water usage are being made through the use of techniques such as counterflowing fluid to prior stages in the process, methodologies that conserve both water and chemicals are needed.
Cleaner bath chemical consistency is another problem. A significant variation in cleaner chemistry can be found as the bath ages due to the effect of oil accumulation in the tank. Oil removal is required to maintain a consistent level of vehicle cleaning throughout the life of the bath.
If oil and solids are not removed effectively before the phosphate process, defects such as starbursts, mapping and pinholes can occur in the coating (see Figure 2). Starbursts are caused by weld balls in the e-coat layer and typically aren’t observed until after the topcoat has been applied. Mapping, which is caused by contaminants on the surface that prevent good phosphate coverage, can take on many forms and often is observed after the e-coat. Other defects also have been traced back to ineffective cleaning or contaminants deposited with the e-coat. Clearly, removing these contaminants in the cleaning stages could significantly reduce in-plant rework.

At another plant, hydrocyclones provided a significant reduction in the starbursting defect after topcoat application (see Figure 4). Using hydrocyclones at specific locations in the pretreatment process minimizes filter bag changes at the targeted stages, and plants experience fewer clogged spray nozzles in those stages compared to conventional filtration technologies.
Another method that can improve cleanliness is the use of cartridge filters in the final rinse stages of the phosphate system to capture any fine material prior to e-coat. A trial of a Pall cartridge filter with a 70-micron absolute efficiency resulted in substantially cleaner fluid in the bath throughout a production week. Results of the trial showed not only the improvement in rinse fluid quality from Monday to Friday (see Figure 5), but also a significantly longer life, with the cartridge filter lasting five times longer than conventional filters.
Bacteria control also remains a challenge. The current standard is to use peroxide and biocides on a regular basis. However, alternate methods, including ultraviolet (UV) lights and ultrasonics, are being reviewed for both DI water storage tanks and process rinse tanks. With the UV lights, the fluid requires direct exposure to UV for the treatment to be effective; the longer the contact time, the better. Trials of an ultrasonics system called Sonoxide® (supplied by Ashland Inc.) also has shown promise at reducing biofilm from process tank walls and piping.
For more information about Krebs hydrocyclones, visit www.krebs.com. Additional information about Pall cartridge filters can be found at www.pall.com, and more details about the Sonoxide ultrasonics system can be found at www.ashland.com. Ford Motor Co.'s website is at www.ford.com.

No dirt here - effective filtration helps Ford Motor Co. ensure a high-quality, defect-free e-coat on the Mustang and other models.
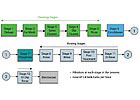
Figure 1. A typical automotive pretreatment system comprises 12 process stages.
A substantial amount of time is spent on cleaning - and for good reason. A clean vehicle improves the phosphate quality, which leads to better paint adhesion and improved corrosion performance. Besides the obvious benefits to vehicle quality, effective cleaning of the vehicle body and removal of the contaminants from the process stream has many in-plant benefits. The removal of oil from the vehicle and the process lowers bacteria growth in water rinse stages. The removal of solids from the vehicle and the process reduces the amount of dirt in the e-coat, which minimizes sanding (and therefore labor), improves coating appearance and leads to fewer in-plant repairs. In the future, a cleaner vehicle and process will enable new pretreatment chemistries to be used by providing a consistent substrate surface quality and by allowing for the use of materials that are less tolerant to the presence of contaminants.
However, for many plants, the cleaning stages aren’t as effective as they should be. Problems such as the buildup of solids and oils in the cleaner stages, inconsistent cleaner chemistry, insufficient dwell time in the cleaning stages and ineffective filtration cause dirt, oil and other contaminants to enter subsequent pretreatment stages. In one analysis of the deluge, cleaner, rinse and DI dip stages, dirt was present in the filter bags of all stages tested (stages 1, 3, 4, 5 and 12). Oil was also discovered in the filter bags of all stages tested (stages 1, 3, 4, 5 and 12), with the largest amounts found in the cleaner dip filter bag. Additionally, sealer was present in the filter bags of stages 1 and 3, as well as in the DI dip (stage 12) just before the e-coat - a serious problem.
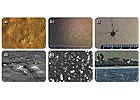
Figure 2. Oil and solids in the phosphate process can cause problems such as pinholes (a), mapping (b), starbursts (c) and other defects (d) in the coating.
A Closer Look at the Problem
An analysis of the pretreatment system indicates that a significant amount of contaminants exist in the process (including oil, dirt, weld balls, rust and sealer). These contaminants need to be removed efficiently to maintain the production of a quality vehicle.Most plants refresh their tanks at various pretreatment stages on a regular basis to reduce the buildup of solids and oils in the tanks, but this is neither an efficient nor environmentally friendly solution. On average, automotive plants use about 180 million gallons of water each year, with approximately 75 to 80% of that total being used in paint operations. A significant portion of the water used by paint operations is used in the pretreatment process. Although reductions in water usage are being made through the use of techniques such as counterflowing fluid to prior stages in the process, methodologies that conserve both water and chemicals are needed.
Cleaner bath chemical consistency is another problem. A significant variation in cleaner chemistry can be found as the bath ages due to the effect of oil accumulation in the tank. Oil removal is required to maintain a consistent level of vehicle cleaning throughout the life of the bath.
If oil and solids are not removed effectively before the phosphate process, defects such as starbursts, mapping and pinholes can occur in the coating (see Figure 2). Starbursts are caused by weld balls in the e-coat layer and typically aren’t observed until after the topcoat has been applied. Mapping, which is caused by contaminants on the surface that prevent good phosphate coverage, can take on many forms and often is observed after the e-coat. Other defects also have been traced back to ineffective cleaning or contaminants deposited with the e-coat. Clearly, removing these contaminants in the cleaning stages could significantly reduce in-plant rework.

Figure 3. At one Ford plant, the use of Krebs hydrocyclones reduced the number of weld balls in the e-coat by more than 60% in the first six months of operation.
Improving the Process
One technical solution for the removal of solid particulate from the process is the use of hydrocyclones. When used in the phosphate cleaning process, hydrocyclones are effective at removing metallic particles before automotive components reach the e-coat stage. These systems are capable of capturing particles down to a 10- to 12-micron size. At one Ford plant, the use of Krebs hydrocyclones reduced the number of weld balls in the e-coat by more than 60% in the first six months of operation (see Figure 3).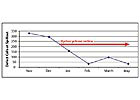
Figure 4. At another Ford plant, hydrocyclones provided a significant reduction in the starbursting defect after topcoat application.
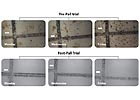
Figure 5. Using a Pall cartridge filter with a 70-micron absolute efficiency resulted in substantially cleaner fluid in the bath throughout a production week.
Additional Work
While both hydrocyclones and cartridge filters substantially reduced particulate contamination, testing results were mixed with regard to oil removal. Using ultrafiltration on the cleaner stages removes surfactant along with the oil, which can hinder the cleaning process. The liquid/liquid hydrocyclone appears to have potential for removing oil from the process, but system design is critical for success. The proper location of the skimmers in the tank and the operation of the oil decant tank are key factors.Bacteria control also remains a challenge. The current standard is to use peroxide and biocides on a regular basis. However, alternate methods, including ultraviolet (UV) lights and ultrasonics, are being reviewed for both DI water storage tanks and process rinse tanks. With the UV lights, the fluid requires direct exposure to UV for the treatment to be effective; the longer the contact time, the better. Trials of an ultrasonics system called Sonoxide® (supplied by Ashland Inc.) also has shown promise at reducing biofilm from process tank walls and piping.
A Successful Strategy
Technologies exist that can allow plants to remove solid contaminants and oil early in the pretreatment process and maintain a consistent pretreatment system, while also minimizing the maintenance requirements of the process (filter changes, pump stress, plugged spray nozzles, tank cleanings, etc.). Additional investigations are likely to yield non-chemical treatment methodologies for minimizing and controlling bacteria growth. By implementing these technologies, automotive finishing professionals can keep dirt and other contaminants out of their pretreatment systems and ensure a high-quality e-coat finish.For more information about Krebs hydrocyclones, visit www.krebs.com. Additional information about Pall cartridge filters can be found at www.pall.com, and more details about the Sonoxide ultrasonics system can be found at www.ashland.com. Ford Motor Co.'s website is at www.ford.com.
Looking for a reprint of this article?
From high-res PDFs to custom plaques, order your copy today!