
The industrial finishing market today wants it all: corrosion protection and performance under increasingly demanding conditions, a preference for cost-effective application, and more and more often, an eye toward environmentally safe application with a minimum of waste. Automotive and appliance OEMs and parts manufacturers have voluntarily adopted more stringent environmental requirements that metal finishers must meet, and governmental regulations also have motivated fabricators to look worldwide for coating technologies that are “green,” and at the same time improve performance.
Greenkote is an example of one such “green” technology, but until 2007, the process has only been available in Europe and Israel. The now-patented coating concept was developed and tested as part of an incubator program sponsored by the Israeli government, and initially the process was applied as solution to corrosion issues in military and marine applications. After three years of rigorous testing at one of the world’s recognized testing sites on Miyakojima Island, Japan, it was clear that the coating had a broader commercial application in conjunction with ferrous substrates used in a number of applications for construction, automotive, appliance and general industry.

Figure 1. a) The coating layers adjacent to the metal substrate contain zinc-iron- aluminum (Zn-Fe-Al) intermetallics.
Improving the Surface
At its core, Greenkote is a thermal diffusion coating process (thermo-chemical surface modification, or TCSM) that modifies and improves the basic surface characteristics of metals. This task is accomplished through a multiphase structure, whereby the layers adjacent to the metal substrate contain zinc-iron-aluminum (Zn-Fe-Al) intermetallics. The thermo-chemical exchange of Fe, Zn and Al atoms facilitates the introduction of aluminum into the corrosion barrier, and particles of those alloys and intermetallics are distributed as Al-rich inclusions, which serve as sacrificial phases, mainly on the surface of the coating (see Figure 1). These inclusions tend to help heal fissures, cracks or porosity of the part surface, which typically become the paths of least resistance for corrosion to attack the component’s surface. The zinc powder in the formula adds a sacrificial characteristic, thereby providing additional protection to the substrate.
Figure 1. b) The thermo-chemical exchange of Fe, Zn and Al atoms facilitates the introduction of aluminum into the corrosion barrier.
Since the essential Greenkote raw material is a powder and it is applied in an economical bulk process, there is no liquid chemistry to monitor, adjust and dispose of as is found in traditional electroplating processes. Furthermore, the process provides an extremely consistent coating layer that is ideal for components like fasteners, where torque/tension performance and control are extremely important.
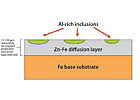
Figure 1. c) Particles of those alloys and intermetallics are distributed as Al-rich inclusions, which serve as sacrificial phases, mainly on the surface of the coating. These inclusions tend to help heal fissures, cracks or porosity of the part surface.
From an environmental standpoint, the coating contains no harmful substances, and the process was designed so that all excess materials can be recycled or reused.
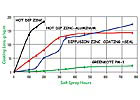
Figure 2. Failure is reached when the area of red corrosion exceeds 5% of the total sample area.
A Proven Process
After more than a year of encouragement from companies like Volkswagen, Motorola, HP and Audi in the European market, Greenkote launched its business development effort in North America in April 2007 with the acquisition of Industrial Powder Coatings (IPC), a multi-plant custom coater providing e-coat, powder coating and rack plating (Zn and nickel-chrome [Ni Ch]) services. The result has been a faster time to market, as opposed to building a plant from scratch, plus the ability to prove the process to companies interested in seeing the attributes of the coating as applied to parts they currently process and have been plating, hot-dip galvanizing, or coating with multilayer dip-spin processes.Metal components for today’s markets must withstand harsher conditions and more intensive usage than those from as little as 10 years ago. Furthermore, the rising cost of raw materials, especially stainless steel, has caused manufacturers to turn to alternative substrates, which require more robust coatings. Greenkote is an eco-friendly technology that can help address some of the issues the market is facing.
For more information, visit www.ipcoatings.com.
Report Abusive Comment