A Uniform Cure
Many different features and designs influence curing uniformity, including the thermal insulation, accuracy of the temperature controller and thermocouple, thermocouple placement, location of exhaust outlets and fresh air inlets, through-metal heat transfer, and chamber pressure. Although each parameter affects the ability of the equipment to achieve a given temperature tolerance, factors such as the air volume, distribution of the air through the work chamber, and shell losses play a key role in keeping the heat uniform within the work chamber, ensuring that each area within the oven receives the same air temperature regardless of its location.
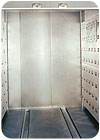
Veterans of the finishing industry agree that temperature uniformity and proper airflow design have a large impact on obtaining consistent, top-quality curing results for powder coatings. But while these characteristics are closely related, it is important for buyers to evaluate them separately. You can buy an oven with excellent empty oven chamber temperature uniformity and still not obtain acceptable results if the airflow is not designed for the way you load your parts inside the oven.
Oven temperature uniformity is defined as the overall temperature variation from a given setpoint. Acceptable uniformity tolerances are stated as a deviation - for example, ±10°F, which means that the temperature of all points that are measured within the work chamber need to be within a 20°F band around a specific setpoint.
Temperature tolerances within the work chamber seem to become more stringent each year. Back in the days when most finishing was liquid-based, uniformity was rarely an issue. The vast majority of liquid-based coatings 15 years ago would tolerate temperature variances of ±15 to 25°F. It seemed like any old box with some heat would provide a satisfactory cure. Today’s powder-based coatings, as well as some of the specialty liquid paints, require a much tighter tolerance. Most powder coatings require a tolerance of ±10°F from setpoint to obtain ideal curing conditions.
Uniformity is typically measured through a web of thermocouples located inside the work chamber. The most common arrangement is a nine-point survey, in which one thermocouple is located near each corner of the work chamber, and another is located in the center (see Figure 1). After the oven is heated to the required temperature and allowed to come to equilibrium, the points are recorded, most often with a chart recorder. If there are points outside the acceptable tolerance, adjustments are made to bring the points into spec.
There are many different features and designs that influence uniformity, including the thermal insulation, accuracy of the temperature controller and thermocouple, thermocouple placement, location of exhaust outlets and fresh air inlets, through-metal heat transfer, and chamber pressure. Although each parameter affects the ability of the equipment to achieve a given temperature tolerance, factors such as the air volume, distribution of the air through the work chamber, and shell losses play a key role in keeping the heat uniform within the work chamber, ensuring that each area within the oven receives the same air temperature regardless of its location.
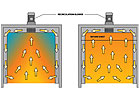
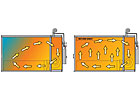
A common type of airflow pattern used throughout the finishing industry is combination (or uni-flow) airflow, where air is introduced into the work chamber along each lower side of the work chamber near the bottom. This design provides a combination of horizontal and vertical-upward airflow through the chamber.
Both schematics in Figure 2 illustrate combination airflow, but the oven on the right has a return sheet, which distributes the return air over the entire ceiling of the chamber and helps ensure that the air flows in a more vertical direction after it exits the supply plenum. Even a partial return plenum is better than none. Equipment without a return sheet will be prone to cool areas, as shown in the schematic on the left.
Another common batch oven design is where the heating plenum is located on the rear of the oven (see Figure 3). Again, the addition of a return sheet helps ensure even airflow through the entire work chamber. The oven on the bottom has a return sheet, which distributes the return air over the entire ceiling of the chamber. Equipment without a return sheet will be prone to cool areas, as shown in the schematic on the left.
Many finishing shops coat a variety of products, which can range from small parts (measured in inches) to much larger parts (measured in feet). In many cases, combination (uni-flow) airflow will provide the necessary flexibility to handle this wide range of parts. However, if the majority of parts are cured on a multi-tiered rack, where air cannot easily rise vertically upward through the tiers, then an oven with horizontal airflow will be a better choice. Ovens with horizontal airflow will typically have a supply duct located on one entire side of the work chamber, and a matching return duct located on the opposite side.
The quality and quantity (thickness) of the insulation must be considered. A general rule of thumb to follow is 1 in. of 6-lb density insulation for every 100°F oven temperature. An oven rated for a maximum continuous temperature of 300°F typically will have 3 in. of insulation. Some companies use a higher-quality, more dense insulation to reduce the insulation thickness. For instance, 4 in. of 6-lb density insulation is sufficient for 500°F ovens.
For more information about oven design, call 262.642.3938, e-mail sales@wisoven.com or visit www.wisoven.com.
Unfortunately, “quality” means different things to different people. Some finishing shops might use excellent temperature uniformity as their quality measure. Others might put an emphasis on durability, heat-up rates, or service. Yet others will use the initial cost investment or the length of warranty as a way to gauge quality.
Regardless of the criteria, every buyer should have a clear idea of what they are looking for in a quality piece of equipment. If you are looking to buy a new oven and currently have one, talk with the finishing operators and the supervisor. What do they like about their current oven? What would they like to be different? If the existing oven has any quality issues, what are the causes?
Based on the answers to these questions, you should have a good idea of what your quality measurements will be when you begin to look for your next oven. Simply make a list of items in the order of importance that you feel adds quality to an oven. Bring these points to the attention of the oven vendors you will be considering, and document what each vendor offers in each area. This information will give you a solid basis for comparison when making your final decision.
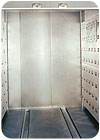
An example of an oven with combination airflow.
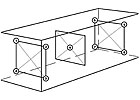
Figure 1. In a nine-point survey, one thermocouple is located near each corner of the work chamber and another is located in the center.
Oven temperature uniformity is defined as the overall temperature variation from a given setpoint. Acceptable uniformity tolerances are stated as a deviation - for example, ±10°F, which means that the temperature of all points that are measured within the work chamber need to be within a 20°F band around a specific setpoint.
Temperature tolerances within the work chamber seem to become more stringent each year. Back in the days when most finishing was liquid-based, uniformity was rarely an issue. The vast majority of liquid-based coatings 15 years ago would tolerate temperature variances of ±15 to 25°F. It seemed like any old box with some heat would provide a satisfactory cure. Today’s powder-based coatings, as well as some of the specialty liquid paints, require a much tighter tolerance. Most powder coatings require a tolerance of ±10°F from setpoint to obtain ideal curing conditions.
Uniformity is typically measured through a web of thermocouples located inside the work chamber. The most common arrangement is a nine-point survey, in which one thermocouple is located near each corner of the work chamber, and another is located in the center (see Figure 1). After the oven is heated to the required temperature and allowed to come to equilibrium, the points are recorded, most often with a chart recorder. If there are points outside the acceptable tolerance, adjustments are made to bring the points into spec.
There are many different features and designs that influence uniformity, including the thermal insulation, accuracy of the temperature controller and thermocouple, thermocouple placement, location of exhaust outlets and fresh air inlets, through-metal heat transfer, and chamber pressure. Although each parameter affects the ability of the equipment to achieve a given temperature tolerance, factors such as the air volume, distribution of the air through the work chamber, and shell losses play a key role in keeping the heat uniform within the work chamber, ensuring that each area within the oven receives the same air temperature regardless of its location.
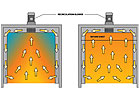
Figure 2. Illustrations of combination airflow. The oven on the right features a return sheet, which distributes the return air over the entire ceiling of the chamber.
Airflow Volume
Airflow through the oven is typically stated as either cubic feet per minute (CFM) or as the number of air changes (CFM divided by the internal volume of the work chamber). The more air changes there are, the faster the air flows through the chamber, resulting in increased air circulation and decreased heat loss. However, caution needs to be given to avoid too much velocity through the chamber, which can dislodge powder from the surface of the product.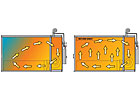
Figure 3. A batch oven with the heating plenum located at the rear. The return sheet on the bottom oven distributes the return air over the entire ceiling of the chamber.
Air Distribution
The next consideration is how the air is distributed into the work area, and how it is collected from the chamber on its way back to the heating plenum. An oven with more CFM (a greater number of air changes) will not always have better temperature uniformity. Unless the air is distributed evenly throughout the chamber, and then returned to the heating plenum in a controlled manner, uniformity will suffer. Airflow means heat. If you have areas within your chamber that have dead air, they will not reach the same temperature as the areas where there is airflow. It sounds obvious, but this fact is often overlooked in oven design.A common type of airflow pattern used throughout the finishing industry is combination (or uni-flow) airflow, where air is introduced into the work chamber along each lower side of the work chamber near the bottom. This design provides a combination of horizontal and vertical-upward airflow through the chamber.
Both schematics in Figure 2 illustrate combination airflow, but the oven on the right has a return sheet, which distributes the return air over the entire ceiling of the chamber and helps ensure that the air flows in a more vertical direction after it exits the supply plenum. Even a partial return plenum is better than none. Equipment without a return sheet will be prone to cool areas, as shown in the schematic on the left.
Another common batch oven design is where the heating plenum is located on the rear of the oven (see Figure 3). Again, the addition of a return sheet helps ensure even airflow through the entire work chamber. The oven on the bottom has a return sheet, which distributes the return air over the entire ceiling of the chamber. Equipment without a return sheet will be prone to cool areas, as shown in the schematic on the left.
Many finishing shops coat a variety of products, which can range from small parts (measured in inches) to much larger parts (measured in feet). In many cases, combination (uni-flow) airflow will provide the necessary flexibility to handle this wide range of parts. However, if the majority of parts are cured on a multi-tiered rack, where air cannot easily rise vertically upward through the tiers, then an oven with horizontal airflow will be a better choice. Ovens with horizontal airflow will typically have a supply duct located on one entire side of the work chamber, and a matching return duct located on the opposite side.
Shell Losses
In a house, areas that are not well insulated (i.e., windows, doors, etc.) allow a greater transfer of energy than well insulated areas. The same is true of ovens. Areas that are not well insulated, or with large amounts of through-metal, will transfer heat energy out of the equipment. Such heat transfers not only can create problem areas regarding uniformity, but they also make the oven less energy efficient, which means it will cost more to operate the equipment. Tongue-and-groove panels with punched rails are a common way to reduce the through-metal area, as well as the overall shell losses.The quality and quantity (thickness) of the insulation must be considered. A general rule of thumb to follow is 1 in. of 6-lb density insulation for every 100°F oven temperature. An oven rated for a maximum continuous temperature of 300°F typically will have 3 in. of insulation. Some companies use a higher-quality, more dense insulation to reduce the insulation thickness. For instance, 4 in. of 6-lb density insulation is sufficient for 500°F ovens.
A Quality Finish
Airflow volume, air distribution and insulation are a few of the key factors that affect temperature uniformity in work chambers. If you buy an oven with acceptable temperature uniformity and the proper airflow design, you will be on your way to maximizing your production rates and improving your product quality.For more information about oven design, call 262.642.3938, e-mail sales@wisoven.com or visit www.wisoven.com.
SIDEBAR: Defining "Quality"
“Quality” is a word used nearly every day by nearly every individual involved in the finishing industry. It starts with the customers, who demand a quality product. In order for finishing shops to produce quality products for their customers, they need quality equipment - a quality washer, quality application equipment, and a quality oven. Luckily for you, every industrial equipment manufacturer produces self-proclaimed “quality equipment.” Wouldn’t it be nice if it were that simple?Unfortunately, “quality” means different things to different people. Some finishing shops might use excellent temperature uniformity as their quality measure. Others might put an emphasis on durability, heat-up rates, or service. Yet others will use the initial cost investment or the length of warranty as a way to gauge quality.
Regardless of the criteria, every buyer should have a clear idea of what they are looking for in a quality piece of equipment. If you are looking to buy a new oven and currently have one, talk with the finishing operators and the supervisor. What do they like about their current oven? What would they like to be different? If the existing oven has any quality issues, what are the causes?
Based on the answers to these questions, you should have a good idea of what your quality measurements will be when you begin to look for your next oven. Simply make a list of items in the order of importance that you feel adds quality to an oven. Bring these points to the attention of the oven vendors you will be considering, and document what each vendor offers in each area. This information will give you a solid basis for comparison when making your final decision.
Looking for a reprint of this article?
From high-res PDFs to custom plaques, order your copy today!