Achieving Performance and Sustainability Objectives with Biobased Polyols

Achieving sustainability objectives has increased in importance for those in the coatings industry. This includes the use of biobased raw materials in the production of resins. The use of biobased materials in coatings is certainly not new; shellac is based on a resin secreted from the lac bug, and some of the first polyurethane chemistry practiced was based on castor oil, both of which are still in use. The key limitation with such natural products was often performance. As application performance demands increased, more “engineered” solutions were developed based upon materials that were typically derived from petrochemicals. Today, the industry is pursuing more sustainable raw material sources that don’t compromise performance as end customers’ demand for greener products increases.
The use of dicarboxylic acids in coating applications is common, especially in the production of polyester resins via condensation polymerization, including polyester polyols for polyurethane coating applications. Aliphatic polyester polyols are typically produced based on petrochemical-derived adipic acid, which is experiencing environmental pressure due to the potential for NOx emissions. Biobased adipic acid is not currently commercially available. However, there are alternative biobased diacids available, such as the nine carbon chain diacid, azelaic acid, which can offer end products with equivalent or improved performance with the added benefit of sustainability.
Physical properties of a, w-alkane dicarboxylic acids are dependent upon the carbon chain length, and physical characteristics can be quite different if the diacid has an even or an odd number of carbons, as outlined in Table 1. Diacids with an even number of carbons have much higher melting points and lower boiling points than the adjacent odd carbon numbered acids. The even-odd effect can also be seen in water solubility, but here chain length masks the effect. Chain lengths of greater than seven carbons have low water solubility independent of the even-odd effect.
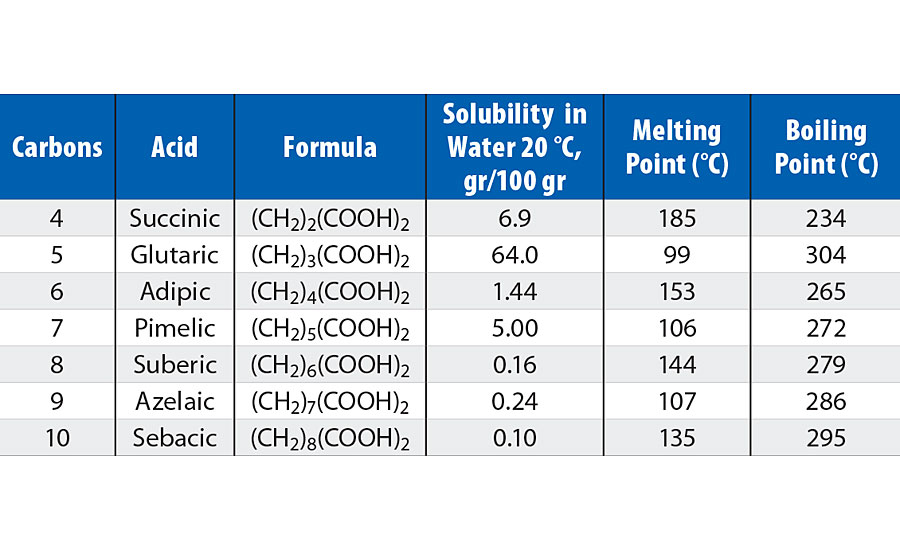
TABLE 1 » Physical characteristics of dicarboxylic acids.
Only a few of the diacids in Table 1 are of significant commercial interest in polyester polyols. Historically, adipic acid is the most prevalent of the alkane dicarboxylic acids, but it is only commercially available via petrochemical processes. Succinic acid is commercially available via both petrochemical and biobased processes. The shorter length of succinic acid produces polyesters with effectively increased relative carbonyl group concentration, and therefore, results in a more hydrophilic backbone that is more susceptible to hydrolysis (on a molar basis) than esters based upon adipic acid. On the longer end of the spectrum, azelaic acid is commercially available and is produced solely from biobased feedstock. The longer chain length of azelaic acid reduces the relative carbonyl group concentration and provides for a more hydrophobic backbone than comparable esters based on adipic acid, a trait that this technical article demonstrates to be a benefit in polyurethane coatings derived from azelaic acid-based polyester polyols.
Source of Azelaic Acid and Production of Polyols Derived from Azelaic Acid
Azelaic acid is produced via an ozonolysis process of oleic acid, as shown in Figure 1. Ozonolysis technology is a well-established, large-scale commercial production process; it was first developed in the 1950s by Emery Oleochemicals to produce the respective dibasic and monobasic azelaic and pelargonic acids.
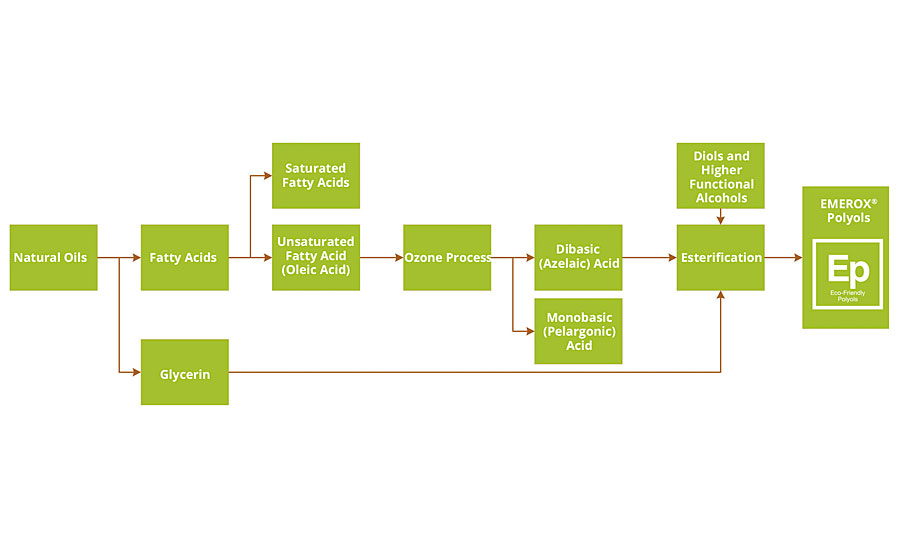
FIGURE 1 » FIGURE 1 » Process flow chart, from natural oils to polyols based on azelaic acid.
The process begins with natural oils that are hydrolyzed (split) into glycerin and the corresponding mixture of resulting fatty acids. The fatty acids are then separated and purified into saturated (e.g. stearic) and unsaturated (e.g. oleic) fatty acids. Next, azelaic acid is produced via ozonolysis of the purified oleic acid, as shown in Figure 2. Oleic acid is a C18:1 monofunctional acid with unsaturation between the C9 and C10 positions. When reacted with ozone, the unsaturation is cleaved, forming acid groups on both sides of the unsaturated site. The result is a mix of monobasic and dibasic acid compounds, which are separated and further purified.
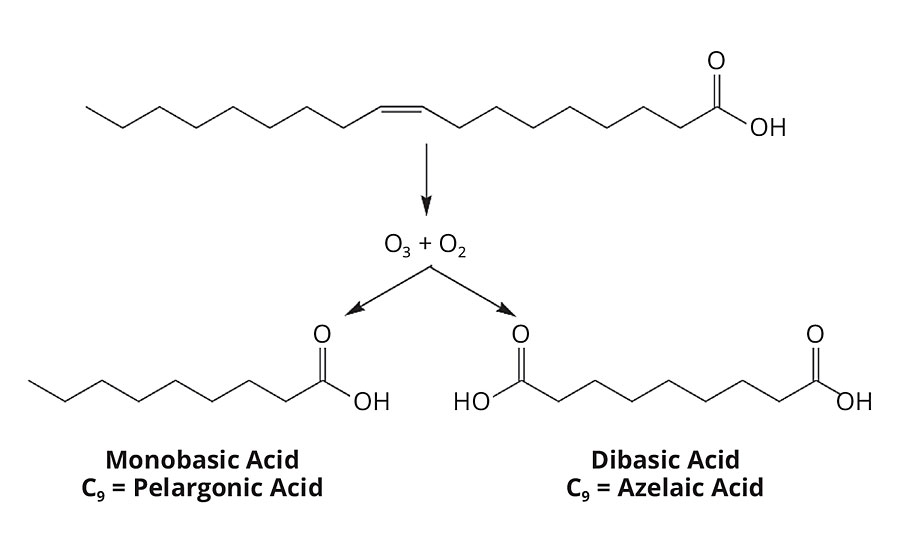
FIGURE 2 » Oleic acid is cleaved at the unsaturation with ozone and oxygen, resulting in a mix of pelargonic acid and azelaic acid.
The azelaic acid produced from the ozonolysis process is then converted to polyols by reaction with diols, glycerin, or higher functional alcohols via esterification, exactly the same way petrochemical-based ester polyols are produced. Azelate polyols produced in this manner have all the design freedom of a petrochemical process but with the added benefits of a more hydrophobic backbone and the high biobased content from their feed streams. Unlike castor- or soy-based polyols, this ozonolysis process enables biobased polyols that can be better optimized for specific applications by controlling composition, functionality, hydrophobicity, hydroxyl placement (primary or secondary) and resulting molecular weight. Additionally, the ozone process has been demonstrated over a broad range of natural oils with high unsaturation contents and eliminates seasonality effects that can be present in more traditional, (e. g. castor and/or modified soy) natural-oil polyols.
Comparison of Azelate and Adipate Polyols - Polyol Structure and Physical Properties
The most commonly used aliphatic acid-based polyester polyol structure is a DEG adipate (diethylene glycol - adipic acid reaction product). Ethylene glycol adipate (EG adipate) polyols are also commonly available, but EG adipate polyols tend to be solid at room temperature, whereas DEG adipate polyols tend to remain liquid at room temperature, and therefore have been widely adopted. Emery Oleochemicals has introduced a family of azelate-based polyester polyols targeting the C.A.S.E. (Coatings, Adhesives, Sealants and Elastomers) polyurethane markets under the EMEROX® polyol trade name. These products are intended to offer a more hydrophobic and biobased alternative to the traditional DEG or EG adipate petrochemical-derived polyols, and typically have lower viscosity than the equivalent alternative adipate polyols. Figure 3 compares the structure of EG azelate versus DEG adipate polyols, while Table 2 lists their respective physical characteristics. As the figure shows, greater hydrophobicity is expected from an EG azelate polyol structure due to the longer respective carbon chain segments, lower relative polarity achieved from decreased carbonyl concentrations (on a molar basis), and lower oxygen content on the backbone.
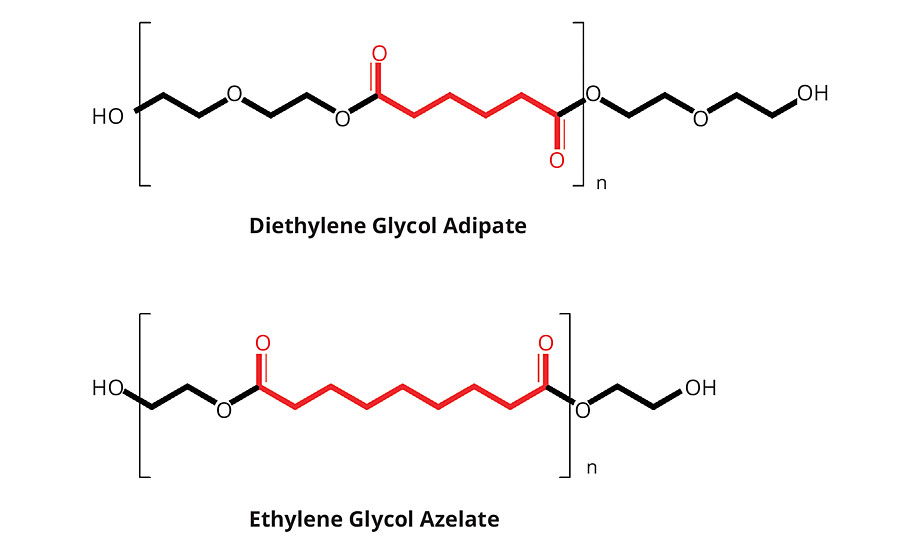
FIGURE 3 » Structure of EG azelate polyol compared to DEG adipate polyol.
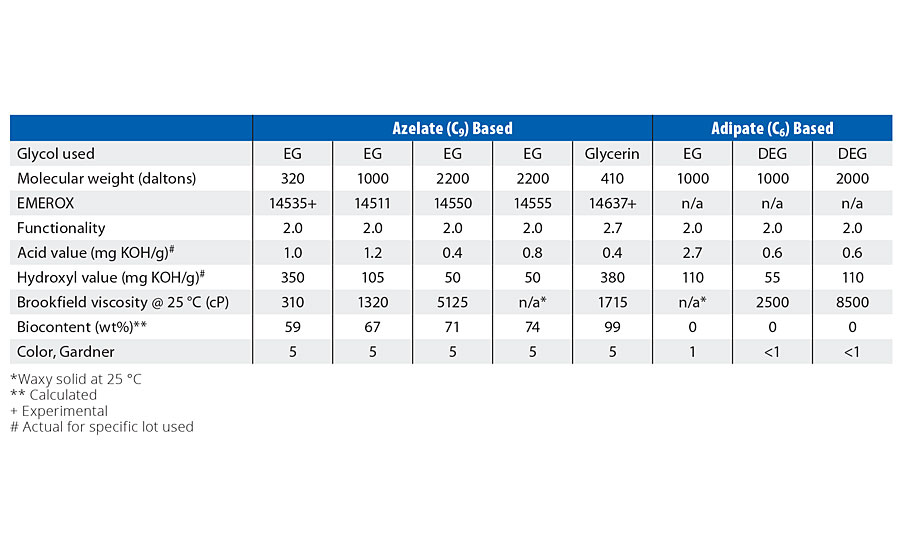
TABLE 2 » Typical physical properties for azelate- and adipate-based polyester polyols.
Polyol Rheology
Viscosity of a polyol is critical for coatings applications, as viscosity is a direct reflection of the ease of use of the polyol in creating coatings precursors as well as of strong influence upon the question of how much solvent must be used for a given coating application. Aliphatic ester polyols are typically either solid at room temperature or liquids that exhibit some shear thinning characteristics. The rheological properties of the azelate polyols in this study were determined and compared to corresponding DEG or EG adipate polyols of similar molecular weights (as defined in Table 2) via both temperature sweep and shear sweep methodology.
Azelate polyols were found to possess lower viscosity than the equivalent molecular weight adipate polyols, independent of whether the competitive adipate polyol was based upon DEG or EG. In fact, comparatively sized EG adipate polyols are typically solid at room temperature.
Rheology studies were conducted using a TA Instruments Discovery HR-2 equipped with Trios software, 40 mm parallel plates and environmental test chamber with liquid nitrogen cooling. For all experiments, a 500 µm geometry gap was used. Samples were equilibrated at the starting temperature for 10 sec prior to data collection. For shear sweep experiments, samples were held isothermal at the target temperature while shear rate was increased from 1-100 s-1. Five data points were taken per decade, with averaging time of 10 sec per point. For temperature ramp experiments, shear rate was constant at 10 s-1 while temperature was increased from 0-75 °C (except as noted) at 5 °C/min, with data points taken every 10 sec.
Viscosity vs. Temperature
Viscosity change with temperature is especially important for high-solids coating formulas, since it reveals the minimum and ideal processing temperatures. Figures 4 and 5 are plots of viscosity vs temperature as measured at a shear rate of 10 s-1 for the aliphatic ester polyols examined in this study. Figure 4 displays the comparative viscosities of those polyols that are 1000 daltons in molecular weight. Figure 5 displays the comparative viscosities of the roughly 2000-dalton polyols. As expected, viscosities were higher for the higher molecular weight products and decreased with temperature. In Figure 4, the comparison of 1000-dalton EG azelate polyol to the respective 1000-dalton DEG and EG adipate polyols shows the EG azelate polyol with lower viscosity than the petrochemical equivalents over the entire temperature range observed. Note, the EG adipate was only able to be measured above its melt temperature of 50 °C.
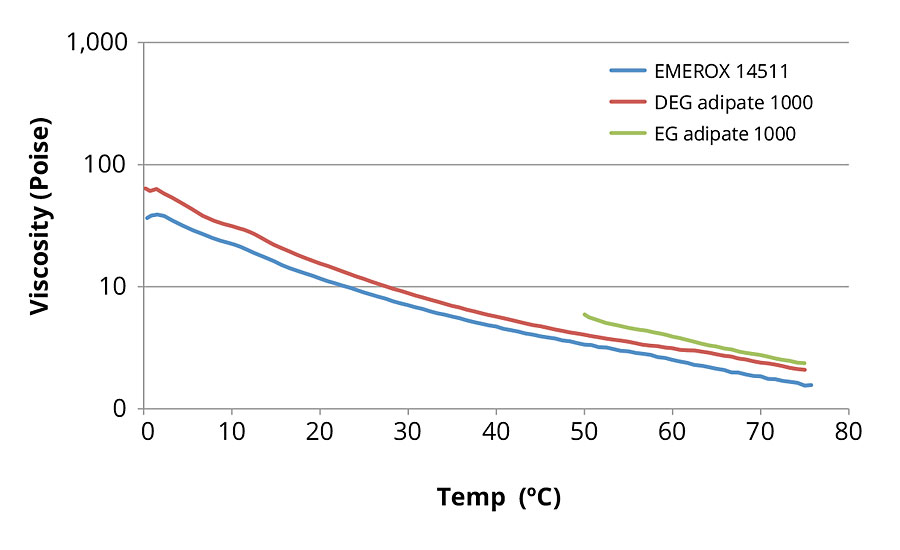
FIGURE 4 » Aliphatic ester polyol viscosity versus temperature curves at a constant 10 s-1 shear rate for 1000-dalton molecular weight polyols.
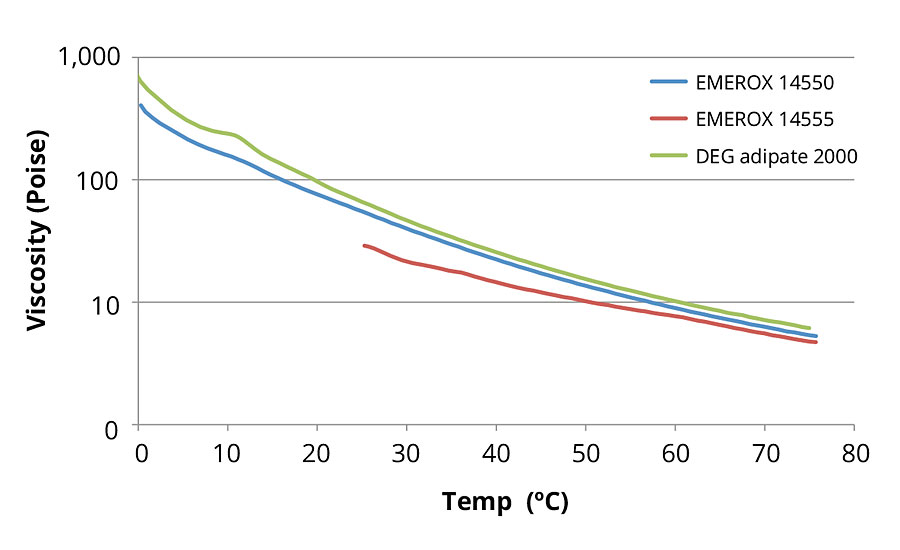
FIGURE 5 » Aliphatic ester polyol viscosity versus temperature curves at a constant 10 s-1 shear rate for 2000-dalton (DEG adipate) and 2200-dalton (EG azelate) molecular weight polyols.
When comparing the 2200-dalton EG azelate polyols to the 2000-dalton DEG adipate equivalent (as shown in Figure 5), the EG azelate polyols again showed consistently lower viscosities than the alternative petrochemical-derived polyester polyol. It is interesting to note that the second EG azelate polyol of similar size but slightly more hydrophobic in nature is a solid at room temperature. To measure the viscosity of this second, more hydrophobic 2200-dalton EG azelate polyol, a sample of the polyol was held at 70 °C to completely melt the material prior to exposure to the 25-75 °C temperature ramp program used for determination of respective viscosity. Since it takes several hours for solidification to occur at ambient temperature, data for this material below 40 °C in the temperature sweep experiment should be regarded as data for a super-cooled liquid or semisolid. Comparing the slightly more hydrophobic EG azelate polyol to the less hydrophobic alternative, we observed that the slightly more hydrophobic alternative displayed a lower viscosity even versus the analogous sister EG azelate material, though it should be noted the material did have a different thermal history.
Shear rate dependence of the respective EG azelate and DEG or EG adipate polyols was also explored. Viscosities versus shear rates ranging from 1-100 s-1 were measured under isothermal conditions of 0, 25, 50, and 75 °C. As expected, all of the polyols in this study displayed some shear thinning behavior across this variety of temperatures. Although further work is needed, indications are present that the EG azelate polyols appear to offer less shear thinning behavior temperature dependence (lower shear rate versus temperature slopes) than the corresponding petrochemical alternatives.
Lower relative polyol viscosities at a given temperature and possible decreased dependence of polyol viscosity upon temperature provide the coatings formulator with materials that display greater ease of use and should allow for more versatility in the design of end coatings formulations, should require less solvent incorporation to apply the coating, should permit higher solids incorporations (thus decreasing the presence of potentially VOC contributing solvents), should be easier to mix or dispense upon application, and could also increase the flow of the material upon a given substrate.
EG Azelate Polyols in Model Coating Systems
To demonstrate the impact upon performance that can result with the use of EG azelate polyol incorporation and to assist coating formulators in the use of EG azelate polyols, a series of model coatings were produced and tested for typical properties of interest for end users.
The model coatings that resulted from incorporating EG azelate polyols were contrasted with model coatings that were based upon the more traditional petrochemical-based adipate polyol chemistries via a series of simple, unfilled 2K coatings. These coatings are not designed to target any particular application but were developed to offer interested parties a simple comparison between the polyol technologies. Polyols included in the model coatings systems study are summarized in Table 2.
The model coating composition included only the respective polyols, chain extender, standard surfactant package, silane adhesion promoter and bismuth neodecanoate catalyst, and is shown in Table 3. The resin side was prepared by mixing with a Melton CM-100 dispersion mixer outfitted with a 2” diameter blade at 1000-1500 rpm for 5-10 min in 200-400 g batches. Brookfield viscosity for these formulated compositions was measured using a Brookfield model LVDV-I Prime equipped with a temperature bath set to control sample temperature at 25 °C with LV #63 spindle at 20-50 rpm.
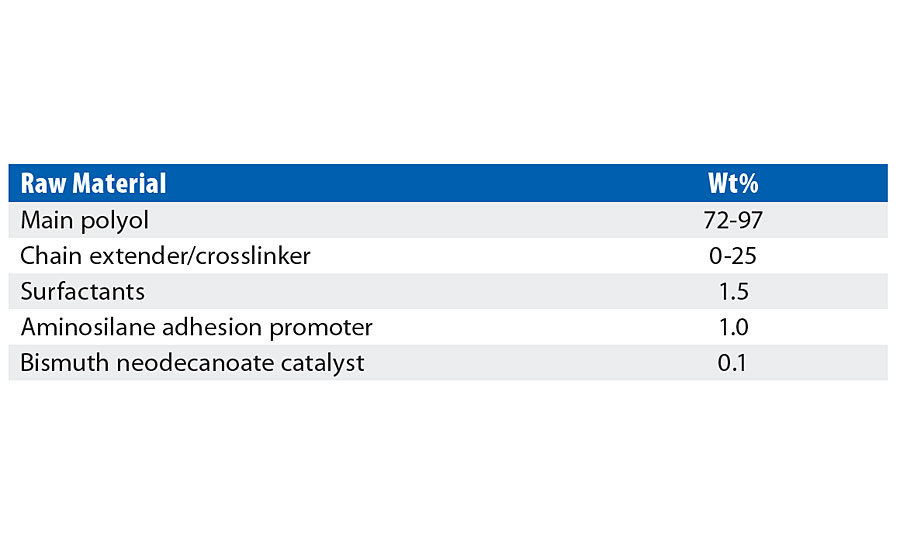
TABLE 3 » Model coating formula used for comparative physical property testing.
The two-part solventborne coating for each of the resin compositions was created in combination with the polyol formula by using an HDI trimer with 21.8 wt% NCO (equivalent weight 193 g/eq), except as noted. Mix ratio of polyol to isocyanate was kept to 1:1 by volume except as noted, with index between 1.02-1.07. Polyol was first dissolved in methyl ethyl ketone before the addition of the isocyanate, with each formula resulting in 50% solids by weight.
In selecting the model formulation for these coatings, the priorities were to use a maximum amount of the main polyol in each formula, keep the mix ratio with the chosen HDI trimer to 1:1 by volume, and create finished coatings with hardness as close to one another as seemed possible. When higher equivalent weight main polyols were used, the higher functional crosslinker was supplemented with 1,4-butanediol to keep reactivity and coating hardness in line. The purpose of this work was not to present optimized final formulas, but instead to offer relative comparisons of performance between EG azelate and competitive ester polyol chemistries in order to demonstrate the potential utility and benefits of EG azelate polyols for coating applications.
Summaries of the physical properties of the model coatings created in this study are shown in Tables 4-6. Each of the tables presents the Brookfield viscosity of the coating formulation at 25 °C, a measure of the gel time for the respective composition, an assessment of the resulting visual quality of the coating after cure, the pencil hardness, the gloss noted for the coating, and the pull-off adhesion strength. Table 4 shows the physical properties achieved by coatings involving the use of an amine tetrol as the crosslinker, while Table 5 shows the physical properties achieved by coatings incorporating alternative crosslinkers such as glycerol or triethanolamine (TEOA). Table 6 shows those physical properties determined for coatings that are based upon varying azelate polyols.
To test the model coatings, both drawdowns and sprayed metal panels were prepared. Drawdowns were applied to Leneta cards using a 20 mil drawdown bar, and gel time was determined with a Gardco Ultracycle Drying Time Recorder model DT-5020. Drawdown cards were cured overnight at 70 °C, and pencil hardness was determined according to ASTM D3363.
Coating formulas prepared as described above were also applied to ground-finish cold rolled steel panels using an air spray gun to 2 mil target dry film thickness, allowed 1-2 hrs to flash at ambient, and cured overnight at 70 °C. Film quality was evaluated qualitatively. Gloss was measured using a TQC PolyGloss® GL0030 at a 60 degree angle. Pull-off adhesion was determined according to ASTM D4541 using 20 mm dollies and a DeFelsko Posi-Test® AT-A automatic adhesion tester at 150 psi/s pull rate.
EG azelate-based formulas showed good compatibility with all of the crosslinkers, while the formula containing DEG adipate was problematic with the amine tetrol and with the TEOA. EG adipate is a solid at ambient conditions, and the resulting coating was waxy with low gloss. Gel time/pot life was primarily controlled by selection of crosslinker. For comparison, one coating was attempted from an azelate-based polyol using polymeric MDI (29.8% NCO, 2.2 functionality) rather than HDI trimer at 0.75:1 polyol/isocyanate. As expected, this formula had much shorter gel time than the comparable HDI trimer-based coating but gave otherwise comparable performance.
Comparing the test results in Table 4 for the amine tetrol-crosslinked model coatings, EG azelate-based coatings offered good clear films, with excellent gloss, high adhesion as measured by pull-off testing, reasonable system viscosities and cure times when compared to DEG or EG adipate alternatives. Similarly, in Table 5, testing of glycerol- and TEOA-crosslinked model coatings yielded results that again demonstrates the EG azelate-based polyols offered good, clear films with high adhesion pull-off values. While the gloss was reduced for the 320-dalton EG azelate/glycerol system, it was still deemed reasonable for a coating. In Table 6, physical properties of coatings based on a higher functional azelate polyols are presented. Again, good-quality film is obtained, though some shrinkage was observed when no chain extender is used with HDI trimer as the isocyanate. Adhesive strength and gloss are both noted as very desirable. Chemical resistance of the systems outlined in Tables 4-6 was evaluated with spot testing, and results are summarized in Tables 7-9 respectively. Coated panels had 2-3 drops of the test chemicals applied. The drops were covered with plastic caps, and left for 24 hrs at ambient conditions. Resistance was as noted in the respective tables. Chemical resistance was evaluated with a matrix of 30 common substances. Spot resistance results are provided in Table 7 for the amine tetrol-crosslinked coatings, while Table 8 shows results for the glycerol- and TEOA-crosslinked coatings. Table 9 lists spot results for coatings involving functional azelate polyols.
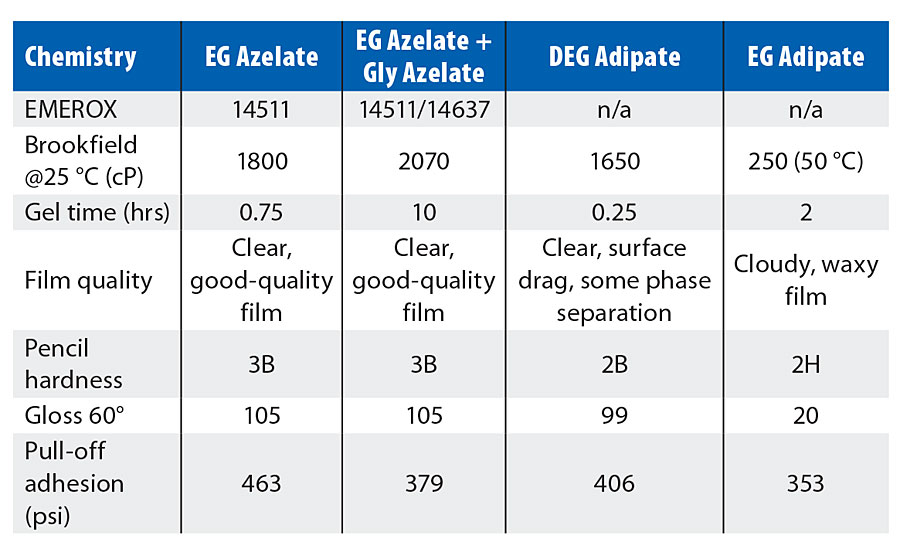
TABLE 4 » Physical properties of model coatings based upon 1000-dalton polyester polyols with amine tetrol as the crosslinker.
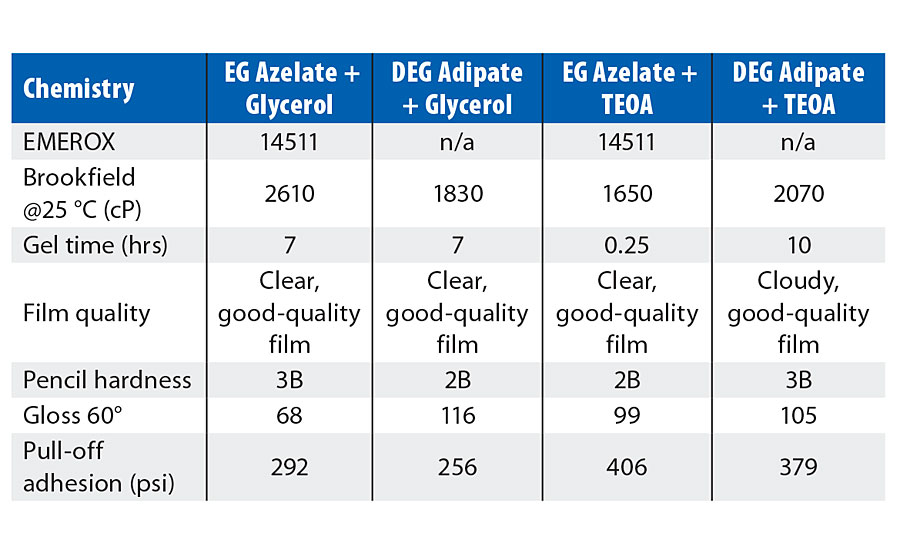
TABLE 5 » Physical properties of model coatings based upon 1000-dalton polyester polyols with glycerol and TEOA as the crosslinker.
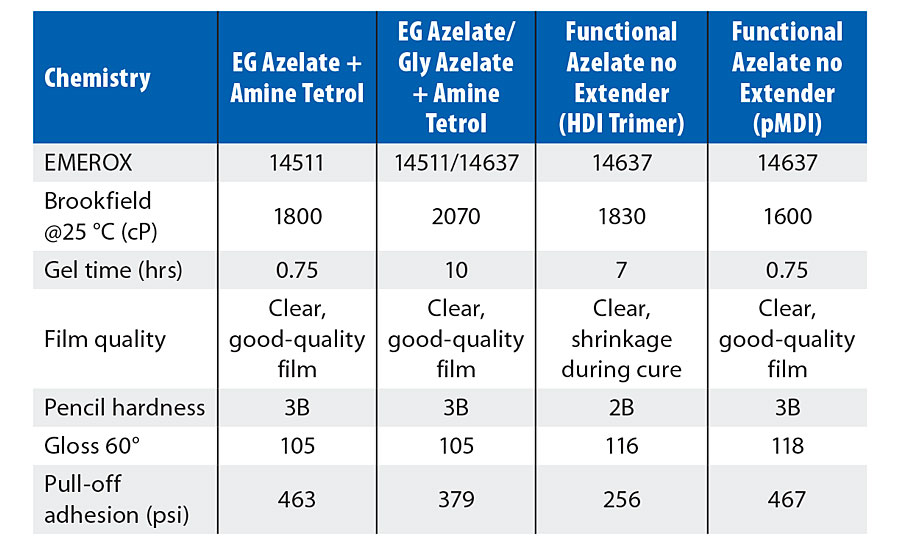
TABLE 6 » Physical properties of varying 1000-dalton azelate model coatings including 410-dalton functional azelate polyol.
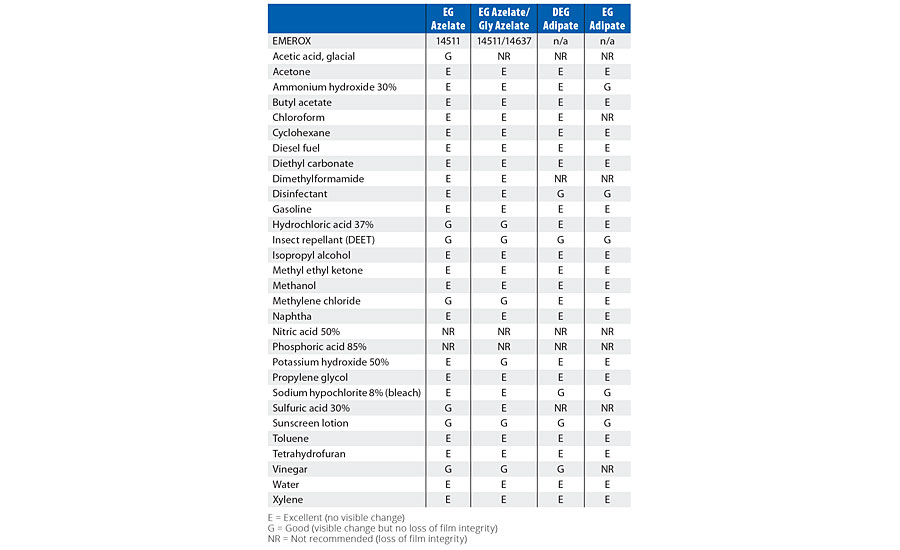
TABLE 7 » Spot chemical resistance results of model coatings based upon 1000-dalton polyester polyols with amine tetrol as the crosslinker.
Comparing the spot resistance test results in Table 7 for the amine tetrol-crosslinked model coatings, overall, azelate polyol-based coatings offered excellent chemical resistance. Similarly, in Table 8, glycerol- and TEOA-crosslinked model coating testing results are presented, and again, the EG azelate-based polyols offered at least equivalent if not improved (some solvents and protic acids) performance. In Table 9, the properties of coatings based upon functional azelate polyols are presented. In general, these coatings displayed acceptable values against a variety of chemicals. Overall, strong acids were the most problematic for the coatings, while hydrocarbons and mild solvents had little effect on any of the coatings. Examining the resistance to varying chemicals can help the coatings formulator understand the suitability of a coating into a target environment, as it is helpful to document the response to materials that the coating might potentially encounter in the end-use field environment.
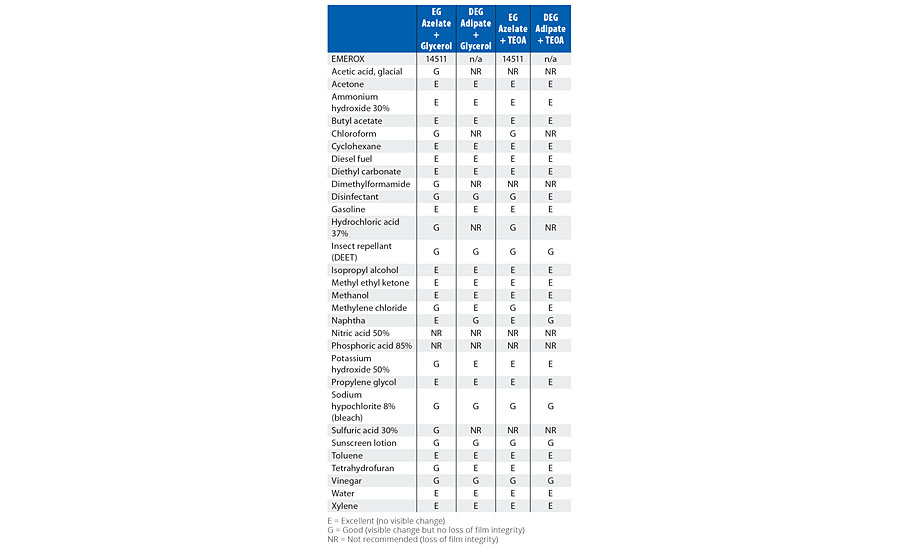
TABLE 8 » Spot chemical resistance results of model coatings based upon 1000-dalton polyester polyols with glycerol and TEOA as the crosslinker.
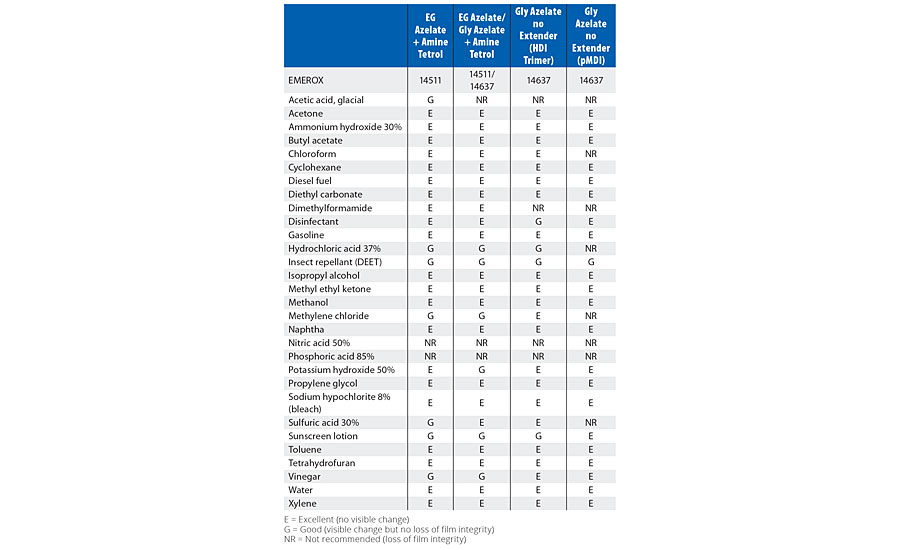
TABLE 9 » Spot chemical resistance results of model coatings based upon functional azelate polyester polyols.
Solvent Compatibility and Hansen Solubility Parameters
Structure-property relationships can give some guidance in solvent selection, but a quantitative evaluation that can provide a formulator with a better idea of which solvents is also valuable data to have. Hansen Solubility Parameters (HSP) is a method often used in coating systems to predict the solubility of one material into another. The method seeks to estimate how alike the material and solvent are by estimating the distance between them in a three-dimensional space defined by parameters of dispersion, polar and hydrogen bonding forces. The EG azelate polyols were evaluated for their HSP according to a procedure adapted from a publicly available source.1
The three HSP for these forces are:
- dd – Energy from dispersion forces between molecules,
- dp – Energy from dipolar intermolecular force between molecules, and
- dh – Energy from hydrogen bolding between molecules.
A fourth parameter, interaction radius, Ro, is also required. If HSP values are plotted in a three-dimensional space, the region of good solvency is defined by a center point of (dd, dp, dh) for the solute, and a sphere of radius Ro encompassing the successful solvents. By knowing HSP and Ro values for a solute, the formulator can select solvents most relevant for his specific application. Coating formulators often use mixtures of solvents for compatibility, safety or regulatory requirements. However, this complicates the formulation and leads to questions about whether the components will stay solvated. Solvents outside, but on opposite sides, of the HSP solubility sphere may combine to give a successful solvent that provides more flexibility in the formulator’s choice of solvents.
To predict if a material will be soluble in a second material or not, the HSP of both materials are needed and the distance between the two molecules (Ra) is calculated as follows:
Ra2 = 4(dd1 - dd2)2 + (dp1 - dp2)2 + (dh1 - dh2)2
Next, the Relative Energy Difference (RED) is calculated to determine if the material is in the solubility space or not.
RED = Ra/Ro
RED is <1: the materials are alike and will form a solution
RED equals 1: the system will partly dissolve
RED is >1: the material will not form a solution
To determine the HSP for the EG azelate polyols in Table 2, a selection of 20 solvents was used. HSP values for the solvents were taken from reference 1. For each case, 8 g of solvent were weighed into a 20 mL glass vial, to which 2 g of the respective polyol were added. The vial was shaken manually for 10 sec and allowed to settle overnight at ambient conditions. Samples were then evaluated for solubility; clear solutions were deemed soluble while cloudy or phase-separated samples were deemed insoluble. HSP values for the successful solvents were averaged to determine HSP values (dispersive dD, polar dP, and hydrogen bonding dH parameters) for the polyols. Interaction radius, Ro, was then calculated from the respective results. Figure 6 shows a representative plot of one of the resulting relationships (between the dP polar HSP versus the dH hydrogen bonding HSP) for the EG azelate polyols versus the 20 solvents included in the screening work.
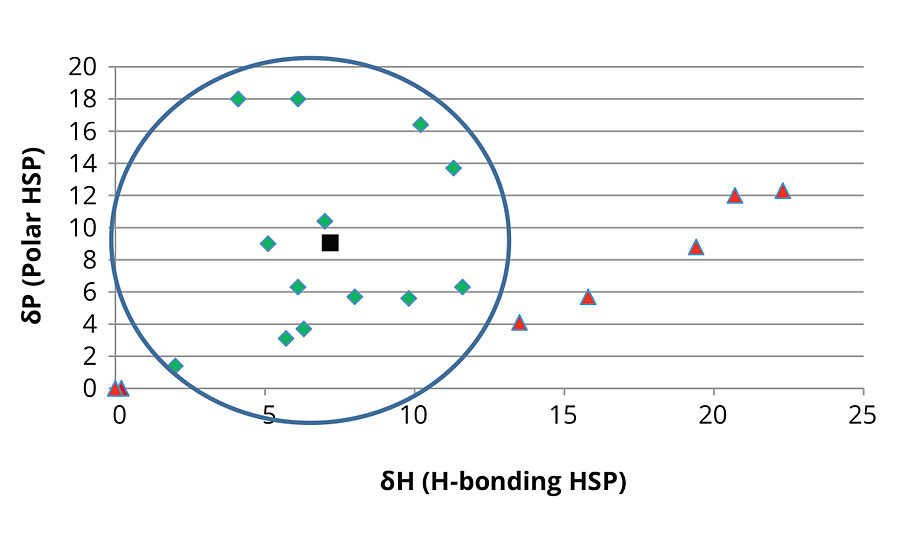
FIGURE 6 » Polar HSP vs. hydrogen bonding HSP plot for the EG azelate 1000- and 2000-dalton polyols. Successful solvents displayed as green diamonds, unsuccessful solvents displayed as red triangles and polyol result displayed as black square. The circle reflects the region of solvency for the polyols and the solvents examined.
As outlined in Table 10, the solubility results for the larger molecular weight EG azelate polyols were identical with the same 13 solvents and seven nonsolvents. All dissolved successfully across a wide range of polarity and in low to medium hydrogen bonding. Aliphatic hydrocarbon and protic solvents were unsuccessful. A lower-molecular-weight EG azelate diol still possesses the similar azelate backbone structure to its larger molecular weight analogs but showed greater polar and hydrogen bonding affinity. Only hydrocarbons failed to dissolve it. However, a higher-functional azelate polyol with a branched structure but similar molecular weight to the shorter-chain diol showed even more polar and hydrogen bonding behavior. Some overlap in the solvent/nonsolvent boundary was seen for this latter polyol in the lower dP vs. dH region.
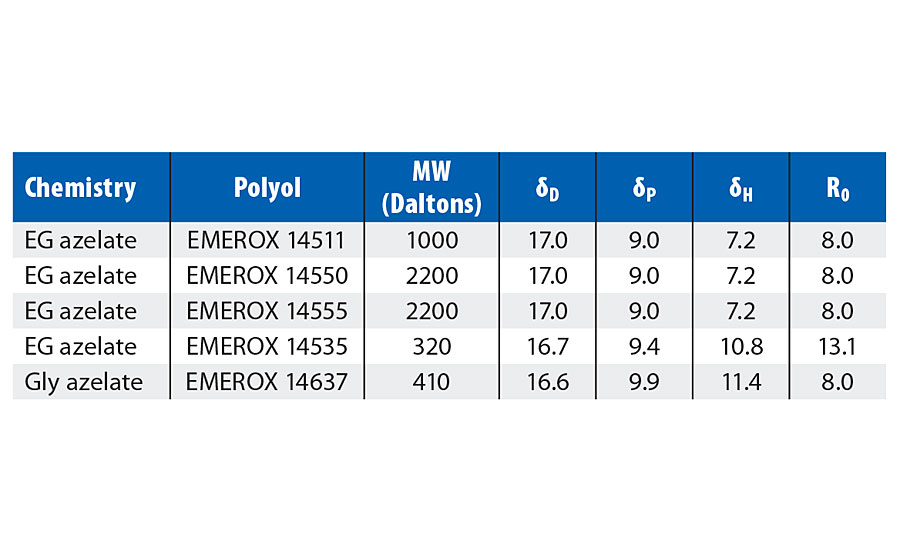
TABLE 10 » Hansen solubility parameters for EG azelate polyols.
A large Ro indicates a solute with more forgiving solvency; that is, it can dissolve successfully in a wider variety of solvents. By this measure, the functional azelate polyol is similar to the larger molecular weight azelate polyols in its range, while the shortest molecular weight diol is notably more forgiving than the others. This suggests that it may be a good reactive diluent.
Water Solubility in Aliphatic Acid-Based Polyester Polyols
Results of an investigation into the solubility of water in the aliphatic polyester polyols of this study are displayed in Table 11. The water solubility was investigated through the addition of a small amount of water into the respective polyester polyol, stirring until combined, and visual inspection of the resultant blend. This process was continued until a hazy separation was observed between the water and the polyol, which was then judged to be the limit of solubility. As the results in the table indicate, significant difference in the water solubilities were observed between azelate- and adipate-based polyester polyols and are reflective of the differing hydrophobicity of these chemistries.
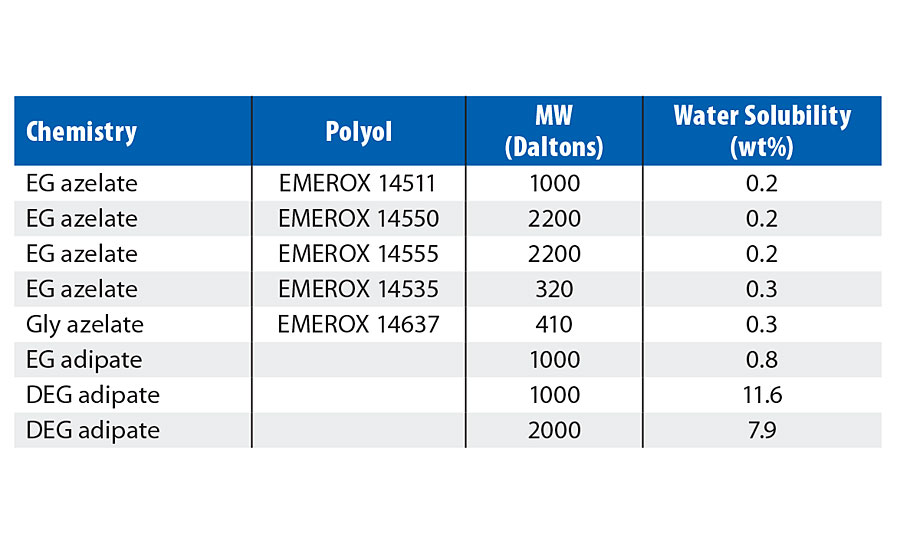
TABLE 11 » Water solubility of aliphatic polyester polyols.
Conclusion
In response to the demand for high performance and biobased polyols for coatings systems, Emery Oleochemicals has launched a family of new azelaic acid-based polyester polyols specifically intended for the C.A.S.E. polyurethane market segments with particular emphasis on coatings applications as discussed in this article. These biobased polyols were tested in a manner to provide data enabling the effective use of the products by the coatings formulator and compared to aliphatic acid petrochemical-based polyester polyols.
The EG azelate polyols showed good solubility in common solvents across a wide range of polarities and hydrogen bonding strengths. Compared to analogous DEG or EG adipate polyols, EG azelate polyols show lower viscosity. While a 1000 dalton molecular weight EG adipate diol solidifies at ambient conditions, the EG azelate polyol of similar molecular size remains liquid. Polyurethane coatings based upon EG azelate polyester polyols showed better compatibility with TEOA and a standard tetrafunctional amine crosslinker polyol than coatings based upon DEG adipate polyols and yielded clear, glossy, high-quality films when cured with HDI trimer. Chemical resistance for coatings based upon EG azelate polyols were observed to be equal to, or superior to, DEG adipate-based coatings.
For the azelate-based polyester polyols, their water solubility, chemical compatibility to potential solvents of interest, rheology and the physical property performance of model coatings were outlined, and through lab testing, it was demonstrated that azelate polyester polyols can bring performance benefits for the coatings formulator. The benefits include ease of use in handling and/or processing as polyester polyols or as formulated coatings materials, high biocontent to provide materials of increased renewable content and greater sustainability, improved compatibility to solvents to help increase the amount of solids of possible coatings products and/or decrease the amount of solvent needed to work with coatings based upon these polyester polyols, and improved physical properties including chemical resistance, clear coatings of high gloss and pull-off strengths.
The initial use of biobased polyols in the polyurethane industry transitioned to petrochemical-based polyols due to performance considerations. As the study results presented here demonstrate, today’s coatings formulators can utilize biobased azelate-based polyol chemistry to achieve both sustainability and performance objectives.
References
1 Hansen, C.M. Hansen Solubility Parameters: A User’s Handbook, 2nd edition, ISBN 0-8493-7248-8, CRC Press (2007).
Looking for a reprint of this article?
From high-res PDFs to custom plaques, order your copy today!