Design and Properties of a New Easy-to-Clean Additive for Epoxy Topcoats

Epoxy (EP) resin coatings are characterized by their high chemical and mechanical resistance and are generally applied in thick layers. The cured EP coatings also exhibit extremely high adhesion to the substrate. However, EP resins based on bisphenol-A and F show limited UV resistance. Thus, they are usually recoated for outdoor applications with a UV-stable polyurethane (PU) topcoat. Wherever a topcoat can be avoided, the benefits of EP coatings compared with PU coatings are uncontested. They are excellently suited to coating machinery, plants, railway car construction, pipeline and tank construction, and for coating construction parts and concrete floors with high mechanical or chemical stress. For this reason, it is essential to develop customized surface additives for one-coat EP coatings. In addition to leveling additives that are used to improve film formation, additives to prevent dirt pick-up and to facilitate surface cleaning are becoming increasingly important. Particularly in applications where functional surfaces play a major role in preventing contamination such as in containers, tanks and conveyer systems, or for safety or aesthetic reasons such as in tunnels and corridors (Figure 1), easy-to-clean surfaces bring huge economic, environmental and time advantages.1, 2
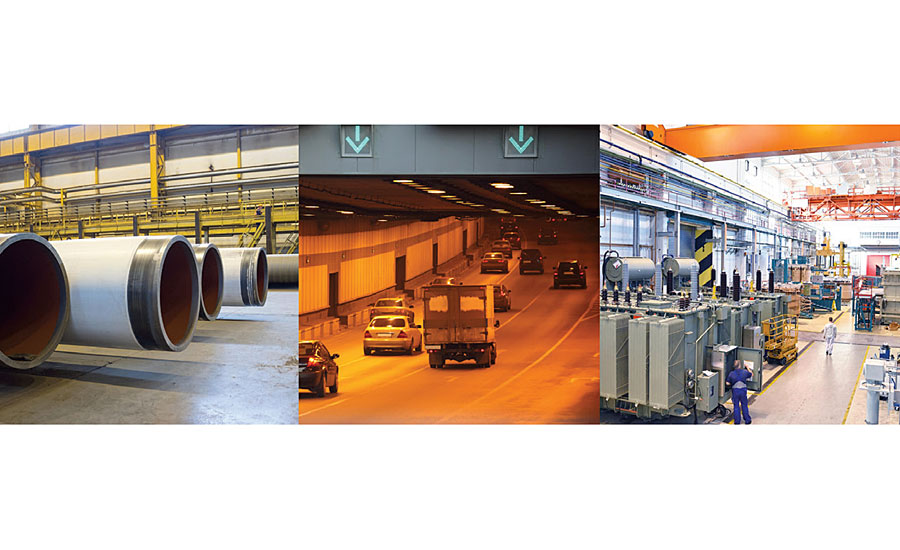
FIGURE 1 » Possible applications of EP monolayer coatings. (Source: www.fotolia.de)
The easy-to-clean effect can be achieved by using self-cleaning or easy-to-clean coatings. Such easy-to-clean surfaces are created using two different technologies, (super)hydrophilic surfaces and (super)hydrophobic surfaces. (Super)hydrophilic surfaces are characterized by a contact angle to water from 0 (“super”) to 30°.3
In comparison, (super)hydrophobic surfaces have a contact angle of at least 140° to water, and water therefore simply drips off.4 This effect can be achieved by creating hierarchical structures (Lotus effect®) which, however, is characterized by a time-consuming application process and only lasts a short time as a result of loss of the surface structure.5 The use of powerful surface tension-reducing and hydrophobizing additives for coatings that include fluorinated hydrocarbon compounds and silicone oils provides a second, simpler method. As a result of the adverse environmental impact of fluorinated hydrocarbons, their use is undesirable.6 Traditional silicone oils only display a short-term effect and may also cause leveling problems.7 Silicones that are modified with polar groups result in better leveling, but the easy-to-clean effect is not persistent. These silicone additives lose their effect after a few (max. two) cleaning cycles.
Our goal was to develop and optimize a new polymeric additive with a careful balance of polar to nonpolar groups that combines easy-to-clean effects with superior leveling (Figure 2). In order to reach persistent effects, anchor groups that can form covalent bonds with the coating also had to be introduced.
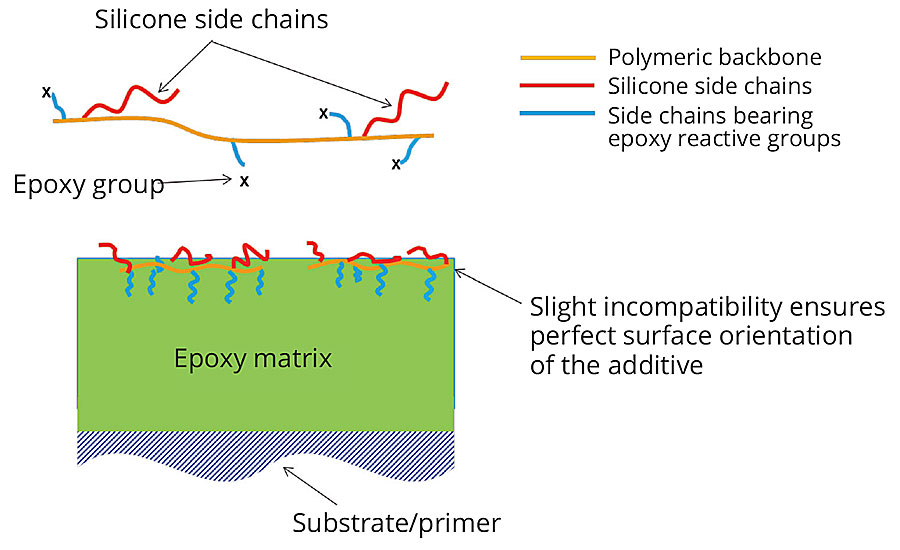
FIGURE 2 » General schematic of the new easy-to-clean additive as well as an illustrative schematic showing its orientation on the surface of a coating.
Experimental
For testing the easy-to-clean properties, metal sheets were coated with a conventional EP topcoat. In some sheets, the coating contained up to 2% of the new additive (all specified percentages are weight percentages). The contamination was simulated with carbon black powder, with a 2% carbon black powder-water suspension and with 1% carbon black powder in hand cream. The carbon black powder was sprinkled on the surfaces. The aqueous carbon black suspension and the carbon black hand cream were applied to the surface using a laboratory paper towel that was wetted with the suspension or hand cream. The sheets were then stored for 1 hr at 50 °C. After being washed using a commercially available dishwasher with a standard program (2.5 h at 50 °C), the samples were visually assessed, photographed, re-contaminated and washed again as described above. This process was repeated several times.
The adhesion test was carried out by using two layers of coating. A red, conventional two-pack EP primer was applied at 200 µm wet film thickness to sand-blasted steel (Sa 2 ½) and, after 30 days drying, it was coated with 100 µm of a white two-pack EP topcoat containing 2% of the new easy-to-clean additive. After a further 14 days of drying, the pull-off test was performed according to DIN EN ISO 4624. Color measurements were made by using BYK-Gardner® color guide in indices in accordance with ASTM E313.
Results and Discussion
Generalized Structure
We developed a new polymer that combined silicone macromonomer technology and anchor groups that are compatible with epoxy resin and form covalent bonds with the coating, enabling long-lasting easy-to-clean properties. The additive is characterized by a strong surface orientation, whereby the polar portion of the copolymer remains in the inside of the polymer film and the reactive groups form a covalent bond with the binder, thereby embedding themselves. The additive has also shown compatibility with most EP systems, such as conventional, high-solids or solvent-free systems.
The hydrophobic effect generated by surface enrichment of the silicone block results in a surface that strongly repels dirt in solid, liquid or mixed form irrespective of whether the contamination is of a hydrophobic (oil-based) or hydrophilic (aqueous) nature.
Easy-to-Clean Properties
In addition to the “control” (coating without additive), a conventional silicone additive was used in the tests as a comparison. Figures 3-5 show the exceptional easy-to-clean effect and retained effectiveness of the new additive, irrespective of the polarity of the contamination. The effect could be demonstrated after up to 10 cleaning cycles.
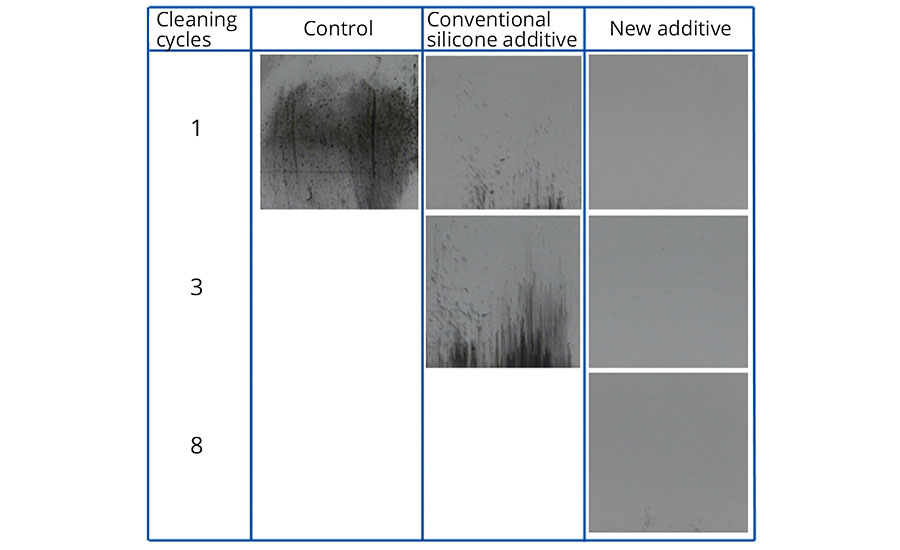
FIGURE 3 » Easy-to-clean effect in conventional EP topcoat without additive, with 0.5% conventional silicone additive, and with 0.5% new additive after contamination with carbon black powder and cleaning in washing machine.
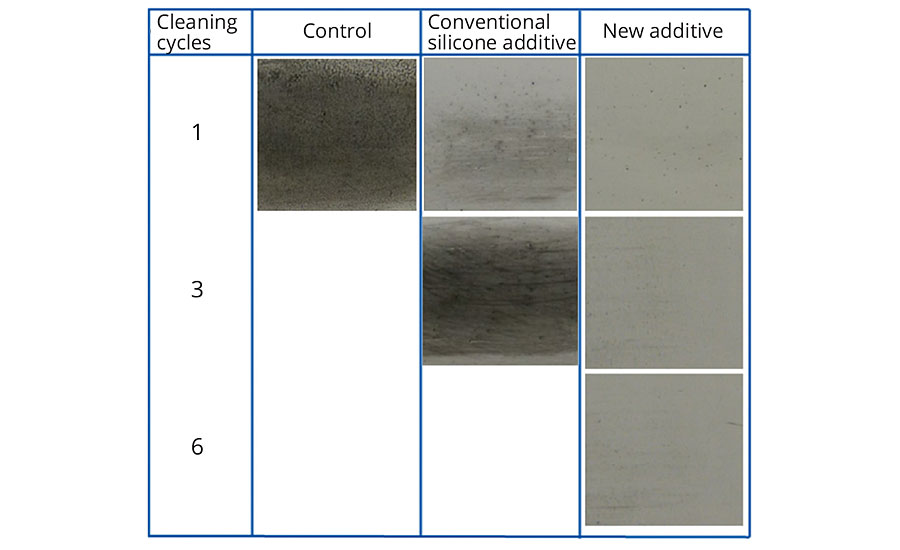
FIGURE 4 » Easy-to-clean effect in conventional EP topcoat without additive, with 1% conventional silicone additive, and with 1% new additive after contamination with 2% carbon black suspension in water and cleaning in washing machine.
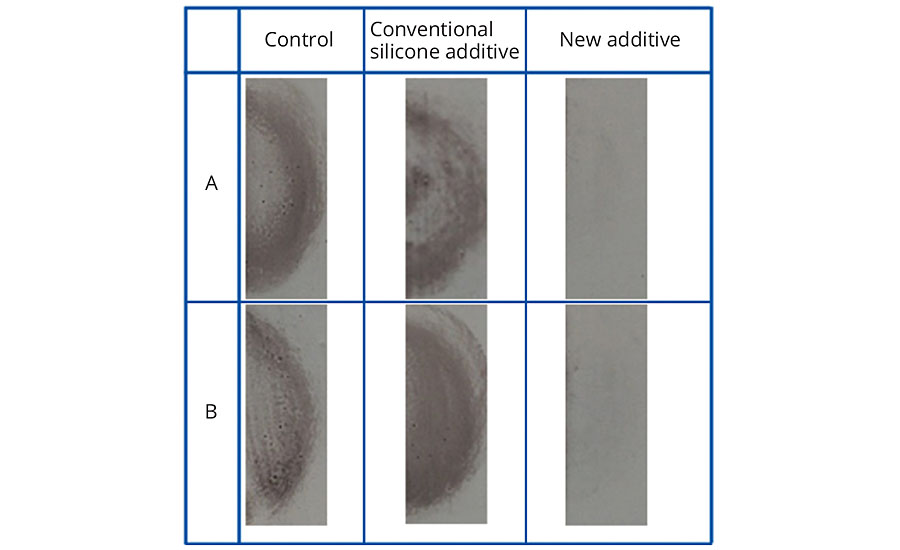
FIGURE 5 » Easy-to-clean effect in conventional EP topcoat without additive, with 2% conventional silicone additive, and with 2% new additive after contamination with 1% carbon black powder in hand cream A - directly after wiping, B - after 10 contaminations and cleaning cycles.
While the simulated contamination and cleaning cycles do not entirely correspond to real-life conditions, they nevertheless prove the effectiveness of the additive under harsh conditions. In addition, these tests were able to demonstrate the significant difference compared to conventional silicone additives.
Adhesion
The new additive was developed as an easy-to-clean additive and is therefore recommended for use in topcoats. However, as it is also a surface-active substance, it is important that there is no negative influence on the intercoat adhesion, i.e. no reduction in adhesion between the topcoat and the basecoat. Figure 6 illustrates the result of the pull-off test in accordance with DIN EN ISO 4624 and shows that cohesive failure only occurs in the primer, which indicates extremely good adhesion between the primer and the topcoat.
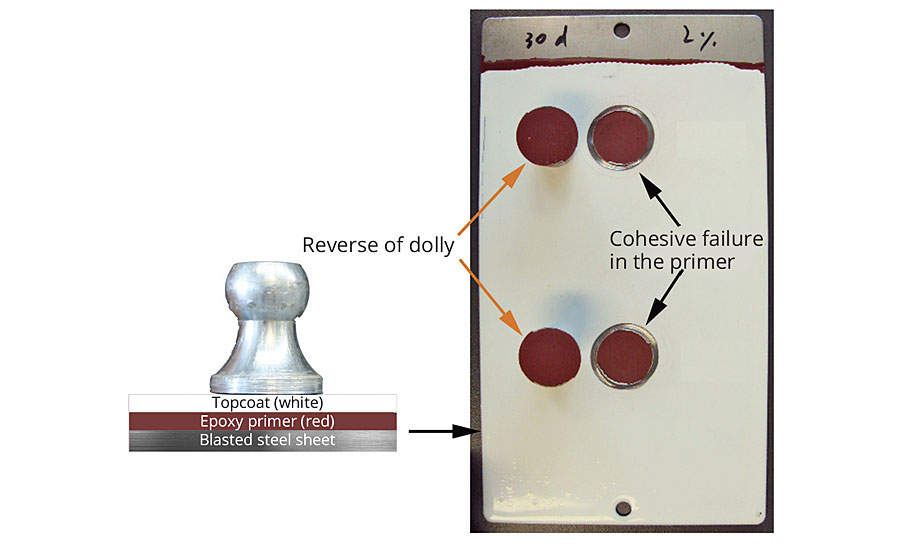
FIGURE 6 » Schematic coating structure for the pull-off test (left) and pull-off test according to DIN EN ISO 4624 (right). No negative impact on the intercoat adhesion.
Gloss and Smoothness
Another key property of coatings is film formation or film integrity, which is especially ensured by optimum leveling. Silicone additives can cause leveling issues as a result of high incompatibility with the system. For this reason, the new additive was used at different concentrations in the EP coating systems, and its effect on leveling was tested. Leveling measurements for the samples without the additive (control) and with 0.5% to 2% of the new additive showed similar values. We deduced that an additive quantity of up to 2% does not cause any leveling issues. Larger quantities were not tested, as the easy-to-clean effect can be fully deployed at 2% addition.
To test surface slip, experiments were conducted with the same range of samples as for the leveling test. Figure 7 shows that the coefficient of friction decreased strongly even at a low additive quantity. As little as 0.5% additive was sufficient to significantly improve the slip.
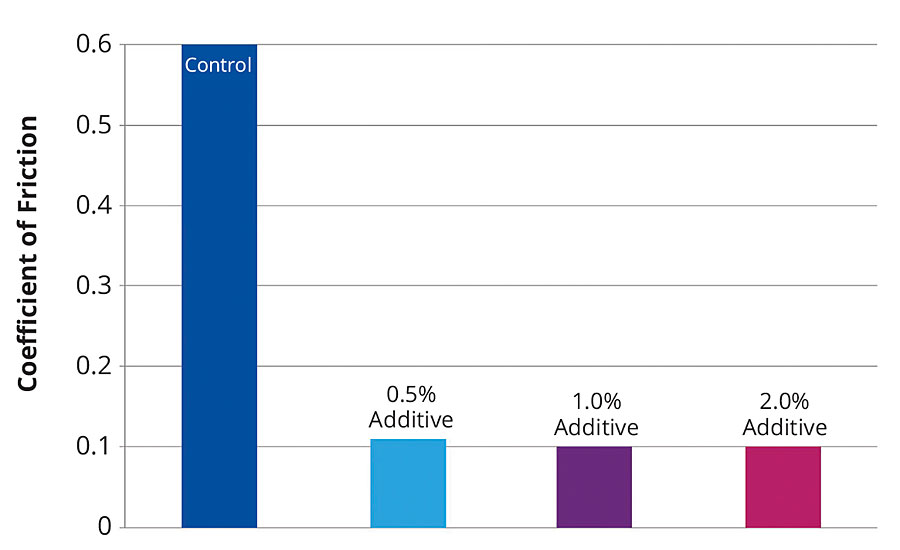
FIGURE 7 » Influence of the new additive on slip for a conventional EP coating without additive (control) and with 0.5-2% additive.
Defoaming
The defoaming property of epoxy systems is very important because of the often relatively high viscosity. The additive was used at 2% in a two-pack epoxy system. A defoaming effect was compared to the sample without the additive. We find that as a result of its specifically low incompatibility, the additive does not stabilize foam and can even support defoaming.
Storage Stability and Pot Life
In two-component systems, the pot life always plays an important role. When using the new additive, initially there may be a slight increase in viscosity. However, there is no impact on the pot life.
Further Benefits
When curing two-component coatings (epoxy-amine), a significant reduction in carbamate formation was observed. Carbamates, which are the cause of the so called “amine blush”, are chemical compounds that form through the interaction with air, especially in ambient-curing EP systems under the influence of high air humidity and carbon dioxide. The result is haziness of black or brilliant surfaces.8
Three panels were coated with a black EP-amine coating. The samples were cured at room temperature and at an air humidity of 85%. Following curing, the color of the sheet metal without the additive displayed strong graying. Adding 2% of a common silicone additive slightly reduced the gray discoloration. Using 2% of the new additive meant that there was virtually no graying. The visual evaluation was also confirmed using measurements taken with the BYK-Gardner color guide. The lightness L* values (CIELab system) of the control, of the sample with the silicone additive and of the sample with the new easy-to-clean additive were 33.7 for the control, 29.5 with the standard additive and 27.0 with the new additive.
In addition to the protection against carbamate formation, the EP coating with the new additive also survived 550 hrs of QUV-B exposure with just minor alteration. The DYI values (the difference between the yellowness indices in accordance with ASTM E313) were determined with the BYK-Gardner color guide for the samples without additive, with the conventional silicone additive and with the new additive, before and after QUV exposure. The differences (same order) were 17, 11 and 8.57.
Low surface tension can reduce the ice adhesion to coating films or improve the deicing of the surface. To establish if this was the case for the new additive, we had the material tested by an independent institute. Tests were performed in a defined atmosphere, in which ice water was sprinkled on the samples at -5 °C, defined wind speed of 11.5 m/s and humidity of 66%. Immediately and after 5 min, an image of the sprinkled samples was taken to evaluate the degree of icing (Figure 8). The sample that contained the additive displayed a considerably low degree of icing. This result suggests the additive could be used for surfaces that require deicing for technical, economic or safety reasons.
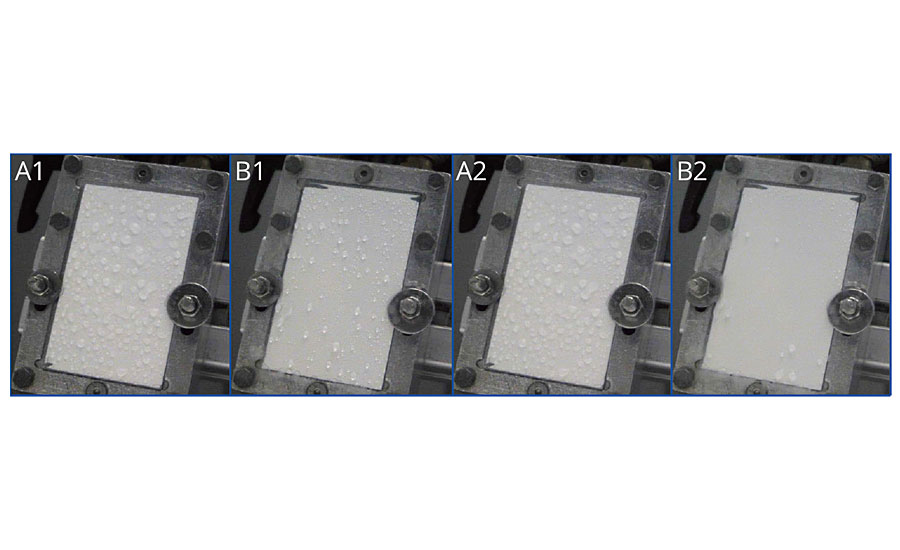
FIGURE 8 » The use of the surface additive prevents ice formation in topcoats – immediately after sprinkling with ice water (A1 without additive, B1 with 2% additive) and 5 min after sprinkling with ice water (A2 without additive, B2 with 2% additive).
Conclusions
By combining an advanced polymeric additive structure with macromonomer functionality with functional groups that can covalently bond to an epoxy system, a new type of additive with superior properties could be generated. The macromonomer functionality leads to a strong easy-to-clean effect in EP coating systems effective against both hydrophobic and hydrophilic contamination. The covalent anchor group leads to a long-lasting easy-to-clean effect that survives multiple dishwasher cycles at 50 °C. In addition, coatings that contain the new additive showed no cratering, no foam stabilization, normal pot life, a reduction in carbamate formation and excellent adhesion to a primer. Surprisingly, addition of the additive also led to decreased ice adhesion and improved deicing.
Acknowledgements
The authors thank Ms. Kathrin Möllers and Mr. Lin Xie for significant contributions in the development of this product.
References
1 Lienhard, J.; Knippers, J.; Cremers, J.; Gabler, M. Atlas Kunststoffe und Membranen, Institut für internationale Architektur-Dokumentation, 2013, Munich, 47.
2 Gniecko, J.; Helfand, D. Modern Paint and Coatings, 1994, 84(3), 26-28.
3 Tölke, T. Photokatalytische Schichtsysteme für hochtransparente selbstreinigende Gläser, Dissertation, 2009, Friedrich Schiller University, Jena.
4 Greßler, S. et al.: Selbstreinigende, schmutz- und wasserabweisende Beschichtungen auf Basis von Nanotechnologie, nano trust dossiers, 2010, 20, p. 3.
5 Solga, A. et al., “The Dream of Staying Clean”; IOP Publishing Ltd; 2007, p. 126.
6 AssTech. Newsletter – Perfluorierte Kohlenwasserstoffe (PFC); http://www.asstech.com/de/downloads/newsletterPFC.pdf (14.05.2014).
7 Bieleman, J. Lackadditive; Weinheim, 1998, 177.
8 Bell, J.P.; J.A.R. and Reffner, P. Journal of Applied Polymer Science, 1977, 21, 1095-1102.
By Horst M. Sulzbach, Guillaume Jaunky, Majdi Al-Masri and Wolfgang Griesel, BYK-Chemie GmbH, Wesel, Germany
This paper was published in the European Coatings Journal and was presented at The 2017 Waterborne Symposium in New Orleans.
Looking for a reprint of this article?
From high-res PDFs to custom plaques, order your copy today!