Winning with Automotive Interiors
How UV Coatings Give OEMs an Edge

Cars have become more than just a mode of transportation for consumers. Improved fuel economy, safety and drivability are welcome additions, but drivers are looking for more in their driving experience. They view their automobile as an extension of themselves and look for an interactive, customized, luxury experience, which is why new technologies have been brought in to meet that very demand. Knobs, buttons and overhead lighting have been replaced by touchscreens, capacitive sensing and mood lighting, allowing the driver to be encapsulated in his or her own styling preferences.
In order for automakers to maintain or capture market share, it is essential for them to focus on what customers want, through product customization, and more specifically that of automotive interiors that most influence the consumer’s overall driving experience. Product customization is, however, one of several considerations original equipment manufacturers (OEMs) have to take into account to remain competitive in the market. Productivity, cost control and environmental concerns also come into play.
The switch from metal to plastics in automotive interiors illustrates the growing importance of those factors very well. By reducing the overall weight of the vehicle, plastics allow for a much lower carbon footprint and energy consumption from a production perspective. This in turn translates into reduced fuel consumption and CO2 emissions for consumers, which also happen to figure among their top buying requirements.
For all those reasons, automakers are now looking for coatings that offer performance, robustness, specific haptic and aesthetic effects, as well as improved productivity. Energy-curable coatings are able to deliver all these features, while simultaneously tackling the heat sensitivity issue commonly associated with plastic substrates. Indeed, traditional coatings for automotive interiors are two-component systems (urethane and acrylic blends) that require at least 20 minutes of curing at or above 80 °C, which is unfavorable for plastics as it potentially damages the substrate. Furthermore, the conventional two-component systems are limited in their ability to maximize efficiency and productivity that is constantly driven by the automotive industry. A shift to energy-curable coatings would therefore allow both OEMs and suppliers (Tier 1 and 2) to benefit from a wide range of advantages:
- Performance. UV technology would allow coating suppliers to capitalize on the intrinsic value of scratch, abrasion, stain and chemical resistance, as well as weathering.
- Sustainability. Significant reductions of volatile organic compound (VOC) emissions make UV technology more environmentally friendly. As the curing process is faster than conventional thermal curing, it also saves more energy.
- Productivity. Thanks to an almost instantaneous cure when exposed to ultraviolet light or an electron beam, higher efficiency and more robust throughput are achievable with energy-curable technology, thus decreasing manufacturing costs.
- Versatility. Using UV technology also means more flexibility in terms of choice of substrates, therefore eliminating the need for pre-treatment or the use of a primer in some cases.
While allnex produces binders for traditional UV coatings and hardcoats, the company also offers, amongst others, a product portfolio of waterborne UV- and dual-cure coating solutions for plastics.
This article will discuss various energy-curable technologies that can be used for automotive interior applications for film and thermoplastic substrates: protective coatings, functional coatings, in-mold decoration (IMD) and vacuum metallization (VM).
Protective Coatings
OEMs have realized the benefits of improved productivity and efficiencies of energy-curable coating technology for more than two decades in headlamp and reflector applications. They can be formulated to have outstanding scratch, UV, chip, abrasion and chemical resistance. Expanding such technology to automotive interior parts such as decals, buttons, knobs, steering wheels and decorative trims creates synergy between productivity, efficiency and performance. Compared to traditional one- and two-component chemistries, energy-curable coatings can provide similar and, in many cases, better scratch resistance and hardness than many conventional chemistries. In Table 1, energy-curable technology is compared to conventional water- and solvent-based technology.
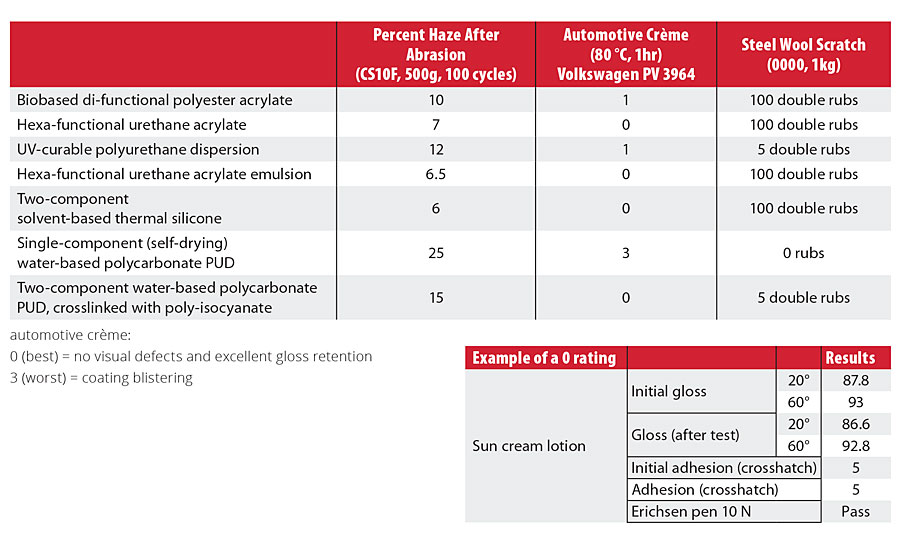
TABLE 1 » Hardness and chemical resistance.
The thermally cured silicone was cured at 120 °C for 20 min; the water-based polycarbonate polyurethane dispersion (PUD) was cured for 30 min at 80 °C. The energy-curable coating technology was cured with 1200 mJ/cm2 using 236 watt/cm fusion lamps equipped with two Mercury-doped bulbs. All curing was done after solvent or water removal from the coating. For the silicone hardcoat, the dry coating thickness was between 3-5 microns and the dry film thicknesses of the remaining coatings were between 10-12 microns. The coatings were applied to polycarbonate substrates for testing.
Thermally cured silicones are well known for their superior protection of various parts that exceeds many specifications. This makes them ideal for many automotive applications. This is accomplished at one-third of the dry coating thickness of waterborne and energy-curable technology. Single-component water-based PUDs offer very little protection, requiring further crosslinking and additional curing time (as much as 72 hrs) to achieve comparable chemical resistance. Characteristically, single- or two-component water-based PUDs cannot achieve scratch and abrasion resistance of energy-curable technology or thermally cured silicones. Neither thermally cured silicones nor conventional polyurethane dispersions offer the fast cure response that is observed with energy-curable technologies. It can offer similar performance with less time by offering a nearly instantaneous cure after exposure to a UV light source. High gloss and chemical resistance are staples of the energy-curable chemistry, which can be seen through testing with many automotive crèmes, including 24-hr exposure to those crèmes at elevated temperatures.
As sustainability and long-term environmental concerns continue to grow, the drive to alternative solvents, lower power consumption and more sustainable products will remain present needs. Energy-curable technologies are designed to fit these needs. Water-based UV needs enough power to get the water out, followed by exposure to a UV light source. No additional oven time is required to get sufficient cure. Further advances in waterborne energy-curable technology, such as UCECOAT® 7200 (polyurethane emulsion), can achieve high gloss retention (mirror-like finish), scratch, abrasion and chemical resistance properties of thermally cured silicones, conventional solventborne or 100%-solids energy-curable coatings. Biobased products such as EBECRYL® 5781 can achieve excellent chemical resistance and low haze development after abrasion delivered in a low-viscosity package, eliminating the need for solvents and performance comprises to meet higher coating solids needs.
The intrinsic chemistry benefits of energy-curable technology can be used to improve the performance of conventional one- or two-component systems as well as creating a hybrid curing coating. In Table 2, water-based energy-curable technology is blended (1:1) with single-component water-based polycarbonate PUDs and retested. After water evaporation, the dry coating thickness was between 10 and 12 microns and was cured with an energy density of 1200 mJ/cm2. The incorporation of energy-curable technology reduced the haze after abrasion by 25% and significantly improved automotive crème resistance. The failure mode changes from coating blistering to a loss of gloss (~20% drop in 20º gloss retention). This similar improvement can be expected for similar one- or two-component solvent- or water-based materials blended with energy-curable chemistries.
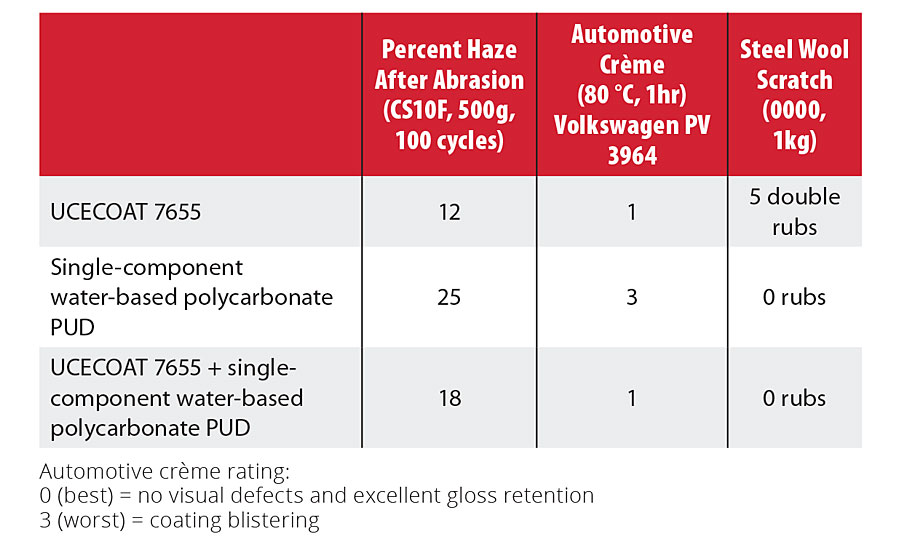
TABLE 2 » Hardness and chemical resistance.
For automotive interior coatings, conventional chemistries allow designers some freedoms that traditional energy-curable technologies do not. Conventional chemistries provide the ability to form after cure, be embossed and cut after cure, along with the advantage of being tack-free before cure. Technology advances now enable formulators to marry conventional and energy-curable, bringing their formulations to the next level of performance. The amalgamation of electrophiles (isocyanates, epoxies, malonic esters) and acrylated chemistries allows formulations to have the best of both worlds. Formulators can use traditional nucleophile (hydroxys, thiols, acids) or nucleophile/acrylate and electrophile acrylate chemistry, taking advantage of thermal and energy-curable kinetics. The implementation of such additional reactions can create a coating with similar hardness of higher functional acrylates at lower acrylate crosslink density with greater ductility. Another benefit of employing combined chemistry is overcoming line of sight limitations with energy-curable chemistry on complicated three-dimensional objects where the coatings in the shadow areas do not cure (excluding electron-beam cure). Incorporating these technologies can reduce this effect through a two-component curing process or single-component moisture-cure process. Figures 1-3 compare a traditional acrylate hardcoat with a combination of electrophile acrylate (NCO-bearing acrylate) and nucleophile chemistry (OH-bearing acrylate) poly-addition reaction, followed by curing with UV light sources.
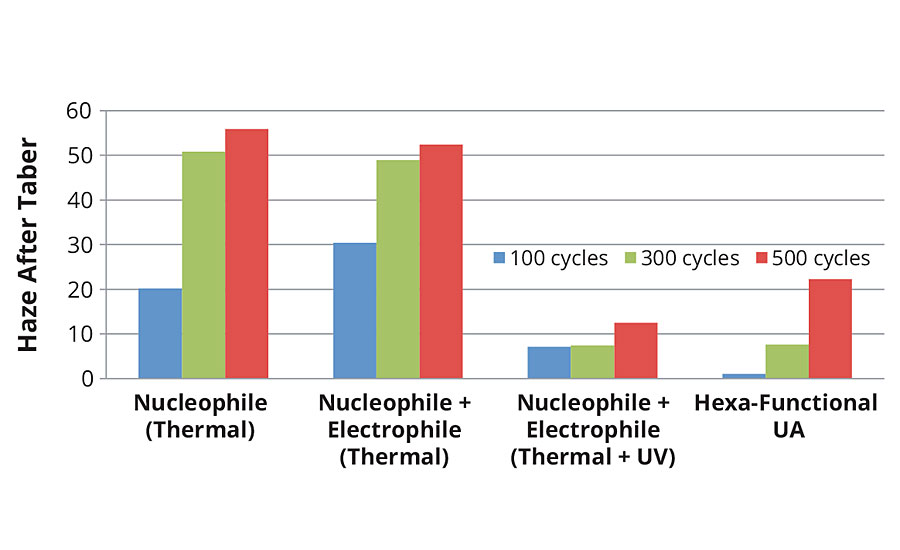
FIGURE 1 » Haze after abrasion.
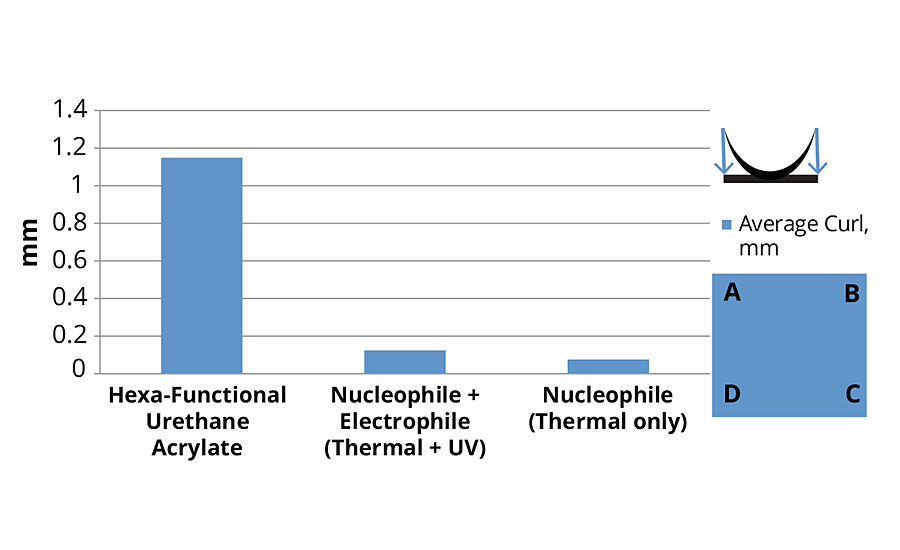
FIGURE 2 » Curl upon cure.
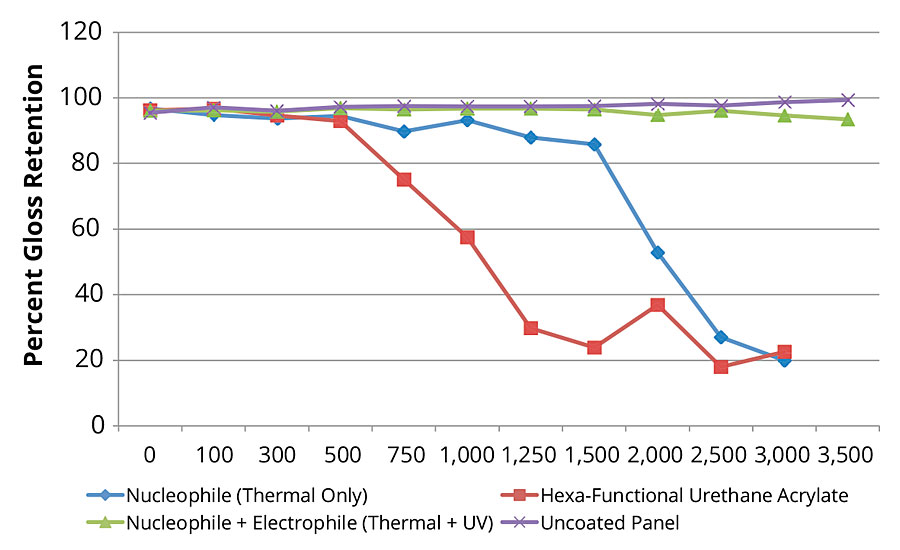
FIGURE 3 » Accelerated weathering.
Thermally curing only the nucleophile does not offer many performance benefits, such as chemical and solvent resistance. However, combining thermal technology and energy-curable technology is a performance game changer. Combining nucleophiles and electrophiles creates a coating that has half the acrylate crosslink density of hexa-functional acrylates, yet offers overall lower haze values after abrasion. Dual-cure technology introduces ductility that is customarily not observed in a highly functional system. Higher functional systems are most often too brittle to coat and require special blending with lower functional acrylate chemistries to reduce cracking upon cure with a minimum increase in weatherability. Figure 2 examines the curl as a functional of ductility. The higher the curl, the more likely it is that the coating will be brittle upon cure after UV exposure.
One of the drawbacks of many highly functional (five acrylate functional or higher) coatings is poor weatherability. In Figure 3, the weatherability of a coating crosslinked by a dual-cure mechanism is shown to be four to five times better than a standard hexa-acrylate used in automotive headlamp applications. To get similar performance, three to six percent of a light stabilizer package would need to be added to be comparable to this coating system that does not contain any light stabilizers and is able to achieve more than 3,500 hours in QUVA. Traditional hardcoat systems tend to not perform well in accelerated or natural weathering testing. Typically, they fail early in the testing process due to a loss of gloss. High levels of light stabilizers have to be added to reduce the cracking tendency upon exposure (natural or accelerated). It is clear that a combination of acrylate functionality with conventional chemistries can create a system that delivers superior weatherability with hardcoat properties, and excels at doing so. In addition to pure performance advances, the use of dual-cure resins results in crosslinked, tack-free surfaces prior to exposure to UV light. This opens up a number of potential applications such as high-scratch-resistant coatings for thermoforming applications, which will be discussed later in this article.
Functional Coatings
With consumers asking for more from their cars than ever, functional coatings provide automakers with the possibility to differentiate in ways never seen before. By offering upgraded features such as soft-touch and easy-to-clean properties, automakers can capture the market, although this usually means sacrificing scratch and chemical resistance. Current developments in UV technologies, however, allow them to formulate these unique surface effects, while maintaining the scratch and chemical resistance that only energy-curable materials provide.
Recently, allnex developed a set of soft-feel products that enable customers to fine-tune formulations to get the special haptic feel each application demands. The soft-feel urethane acrylate oligomer can provide an excellent rubbery feel for automotive parts. It can be used alone or in combination with the recommended acrylate functional performance modifier to boost the scratch and hydrolysis resistance of the final coatings. In comparison with the previously recommended materials, a significant increase in the scratch and abrasion resistance is seen along with improved hydrolysis resistance. Together, these newly developed materials can be used to create tunable formulations that maintain chemical and scratch resistance for automotive parts such as steering wheels, gear shifts and hand grips.
As the current market is heading towards more touch screens and capacitive sensors in place of standard buttons and knobs, the need for easy-to-clean coatings is on the rise. Fluorine-containing acrylates with higher functionalities are proven to provide coatings that are both stain and scratch resistant. By creating a lower contact angle on the surface, unwanted materials aren’t able to wet the surface of the coating and are therefore more easily removed. This enhanced property is available without any sacrifice made on the scratch resistance of the final part. A recently developed silicone-modified urethane acrylate provides the same lower contact angle of the coated part. More importantly, this material can be formulated to achieve lower gloss level without any detrimental effects on the easy-to-clean properties of the coated part, such as instrument panels and consoles. One of the major advantages of silicone-modified urethane acrylates is the long-lasting performance. A 10 micron-thick coating that is made with this material can be subjected to surface degradation and still maintain the ability to easily remove unwanted materials (Figure 4).
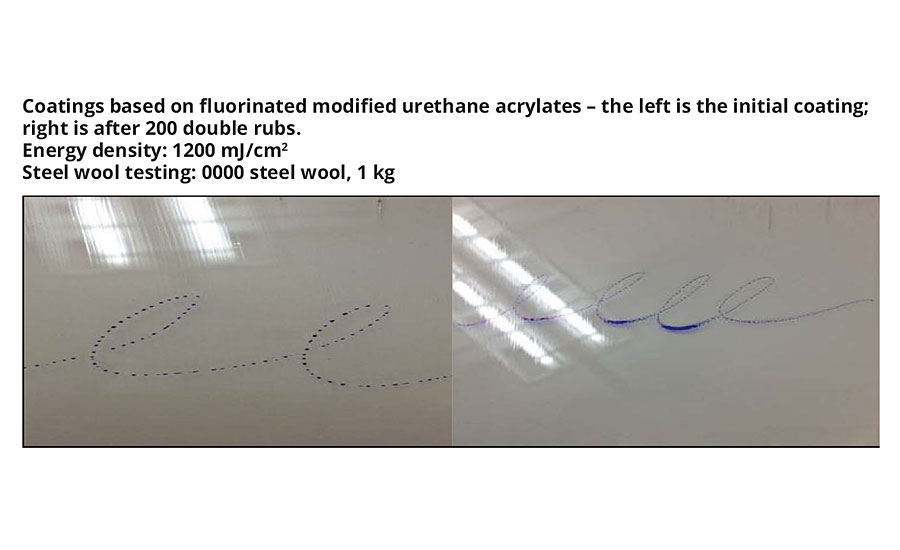
FIGURE 4 » Long-term performance.
In-Mold Decoration (IMD) Application and Coatings
IMD has been a part of the plastics market in the United States for a considerable amount of time, especially in consumer electronics, because of the increased productivity and the ability for customization. With recent federal regulations to reduce carbon dioxide emissions, automakers are looking for ways to decrease the weight of cars more than ever. Replacing standard materials with plastic parts allows for the fuel efficiency of vehicles to be increased, with the added benefit of increased customization of the car interior. Each part can be decorated differently in an incredibly efficient and cost-effective way, through the use of either In-Mold Labeling (IML) or In-Mold Film (IMF). When considering IML, a patterned film is inserted into the injection-molding machine and a resin is then injected into the mold and adheres to the film. IMF processes form the 3D part first and then cure it after inserting it into the injection-molding machine for molding to the resin. As always, all of these advantages must come without the sacrifice of any performance properties, which is where energy-curable materials come into play.
Generally, IML is used for two-dimensional or simple structures, like flat panels. This process allows the use of materials such as hexa- or nona-functional acrylates, which are not incredibly flexible but have high surface hardness and scratch resistance. As with the majority of automotive applications, there is a need for materials that have good outdoor durability due to where the parts are in use. Lower functionality aliphatic urethane acrylates have the advantage of providing good scratch resistance and weatherability, while having a lower viscosity. Using two classes of materials together delivers coatings with both fantastic scratch resistance and weatherability.
IMF, unlike IML, requires increased elongation and flexibility to form around complex three-dimensional parts. Flexibility can be obtained through the use of materials that have a high amount of elongation. Acrylates with high elongation provide systems that are high in elongation after being cured, which allows for forming around complex parts while providing scratch resistance. Another avenue to pursue is using materials that can be thermally cured in an initial step and then formed. The use of thermally cured nucleophile materials in combination with electrophiles will provide a coating that is flexible enough to be formed after the thermal step, while offering a scratch resistance equivalent to that of a hexa-functional urethane acrylate after UV curing. Another advantage of this type of system is the decreased amount of shrinkage that can be seen when compared to hexa-functional materials, as shown previously. It is important to note that the use of waterborne dispersions can provide similar performance properties to the materials we previously mentioned. UCECOAT 7655, along with other dispersions, are both tack-free after driving off the water and can be formed around complex three-dimensional parts. After forming, the materials can be UV cured to provide scratch-resistant coatings that can be used for a multitude of automotive applications.
Vacuum Metallization (VM) of Plastics
An important aspect of customization is automotive trim and pillars. Metallized surfaces are an absolute must in automotive interior design, giving the cockpit a modern and luxurious look. As automakers now wish to reduce weight but have a more sustainable production process, they like to avoid certain heavy metal ions. VM has become a proper alterative to creating light-weight metal-appearing parts. The use of energy-curable technology is a common process in this application space that helps provide a light-weight and metallic appearance of automotive interior parts such as trims and door handles. The key resins requirement is excellent adhesion to both the substrates for the primer layer, the vacuum-metallized layer to the primer and the topcoat to the vacuum layer. The final product has to offer good gloss, scratch and abrasion resistance, and excellent adhesion at all interfaces, which can be achieved by using adhesion promoters. For this, phosphoric acid resins like EBECRYL 168 or 170 are widely used in the market. In energy-curable coatings, polymeric adhesion promoters provide lower shrinkage upon cure. This is important in energy-curable coatings because adhesion is typically achieved through hydrogen bonding unlike conventional chemistries, where chemical bonding can occur via a catalyst or isocyanate used in the curing process. Figure 5 is a metallized polycarbonate. The primer for the metallization layer and the topcoat are an energy-curable polymeric adhesion promoter such as EBECRYL 8213. Polymeric adhesion promoters must be designed to have glass transition temperatures greater than 25 °C because low glass transition temperatures or soft coatings can cause visual distortion or iridescence. In the figure, the coating and topcoat demonstrate high gloss retention before and after hot water testing.
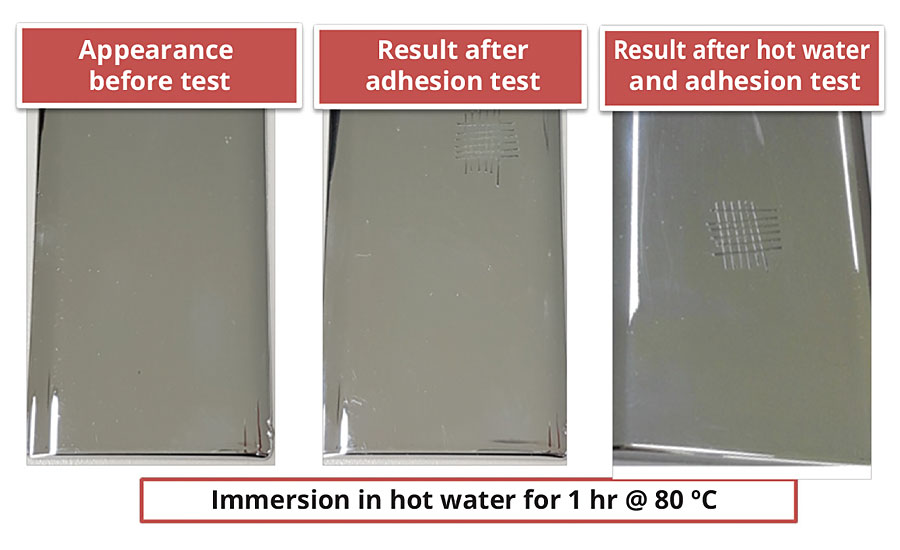
FIGURE 5 » Hot water resistance.
Conclusion
Automotive customization and energy-curable technology are an excellent complimentary pair. On top of its fast cure, energy curing offers excellent chemical resistance that can pass many of the automotive crème standards and can also be tailored to have a wide variety of properties. Thanks to the breadth of energy-curable technology, the development of a multitude of aesthetic finishes for parts is made possible, while simultaneously exercising a positive influence on the environment with lower VOC generation and energy consumption, through shorter drying and curing times. At allnex, we truly believe that the energy-curable technology and the automotive sector have a very bright future ahead of them. The use of energy-curable technology, with its incredible versatility for different applications and resonance with both the consumers’ demands and the various constraints and challenges automakers are faced with, is undeniably providing OEMs with a decisive and long-term competitive edge in the market.
Looking for a reprint of this article?
From high-res PDFs to custom plaques, order your copy today!