Selecting the Best Resin for Your Recipe
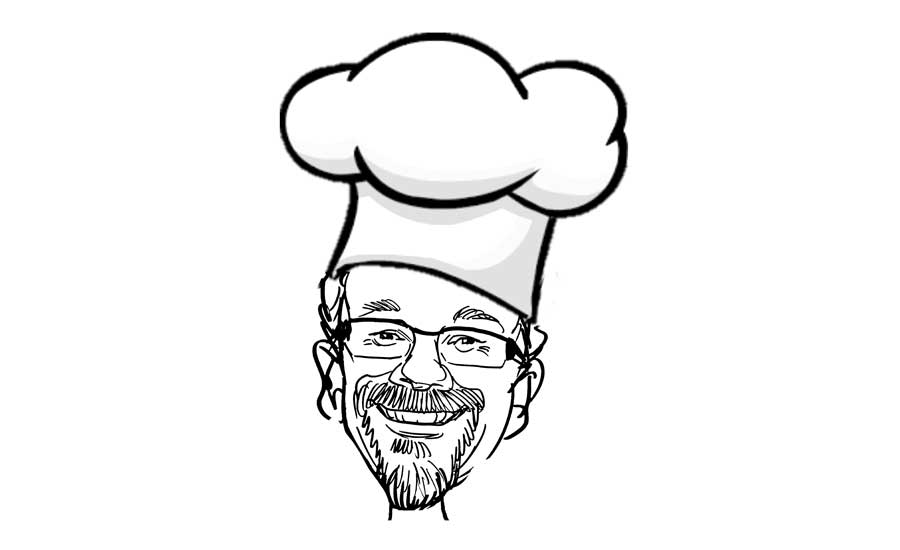
This marks the inaugural edition of the PC Kitchen. No, it won’t be the “Politically Correct” Kitchen, but the Powder Coating (formulator’s) Kitchen. Perhaps it may appear a bit odd to present a culinary theme in this coatings technology magazine, however a coating formulator’s quest very closely parallels the endeavors of a top chef. Early in my career my boss and I engaged in a casual conversation regarding our weekend exploits in the kitchen. After exchanging stories regarding the perfect roux or the finer points of searing a blackened salmon we both realized that you can’t be a good formulator and a bad cook. And so my journey as a powder coating formulator and amateur iron chef took flight.
What I would like to present in this and the ensuing editions is an appreciation for careful selection of raw materials (ingredients), process conditions (whisking, folding and mixing) and curing techniques (stovetop and oven). Like any great dish, only the freshest ingredients, the most careful food processing and precise cooking conditions will yield something your guests will truly cherish. This closely parallels your experience as a formulator. So let’s get cooking.
Selecting the protein portion of a meal creates a focal point of the dinner, and as a formulator, choosing the right resin serves a similar purpose. The resin (cut of meat) determines the overall performance of the coating, and the additives (spices), fillers (grains, pasta, etc.) and colorants/pigments (vegetables) augment the resin for color and more specific properties such as speed of cure, viscosity, etc. If we survey the world of resins available to the powder formulator we see everything from fluoropolymers (Kobe beef) to acrylics (filet mignon) to epoxy polyesters (ground turkey). In some cases a simple burger will do; in other cases a monumental dish is required. Table 1 shows a rundown of resin choices.
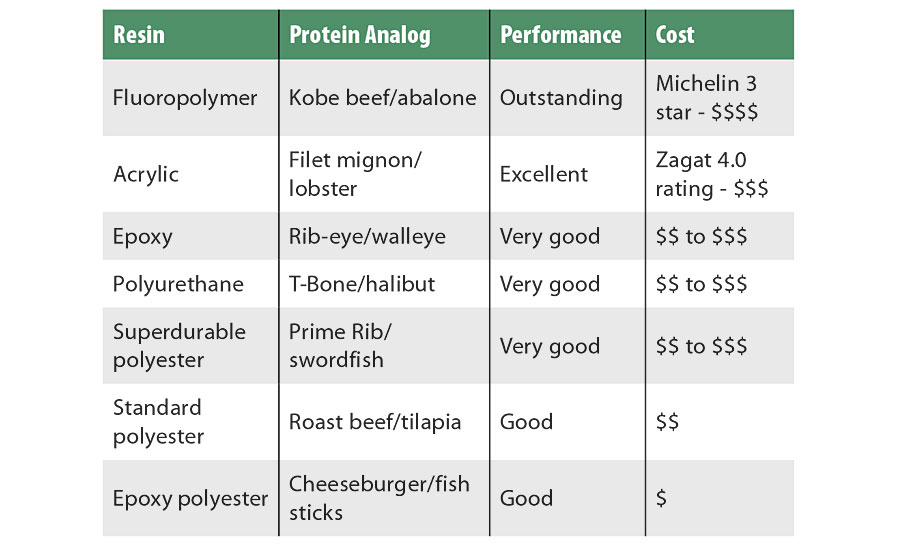
TABLE 1 » Resin options for powder coating formulators.
The resin choices listed in the table are ranked mainly for their overall performance, with a focus on outdoor durability. In reality, all of these products perform well and are very suitable for the appropriate end use. Delving into more specific properties helps hone in on how to make the proper choice for your customer’s expectations. As we all know, a product has to meet a customer’s budget, hence the selection of the lowest cost resin that meets the specification. Volume also has a major impact on the cost of a powder coating. Short runs of specialty colors and/or visual effects also drive up costs.
Outdoor durability is normally graded based on expected durability in southern Florida. Specifications have been established by independent organizations to assist an architect or specifier in stipulating the performance of a coating. The American Architectural Manufacturers Association provides voluntary specifications that differentiate between “entry” level (one year FL), “high” performance (five years FL) and “superior” (10 years FL) performance. A more rigorous system requiring inspections and audits has been established by the Swiss-based Qualicoat organization. Companies that gain their approval are granted a license that requires regular renewal. Approvals granted include Class 1 (one year FL), Class 1.5 (two years FL), Class 2 (three years FL) and Class 3 (10 years FL).
Table 2 details expected outdoor durability of various resin systems available to the powder coating formulator. One huge caveat when considering outdoor performance, especially products in the high-durability ranges - please be critically aware that every component in a coating affects performance. This includes colorants/pigments, fillers and additives (waxes and matting agents in particular). Even the best performing resin can’t make up for a weak pigment or additive, much like spoiling a dish by over or under seasoning.
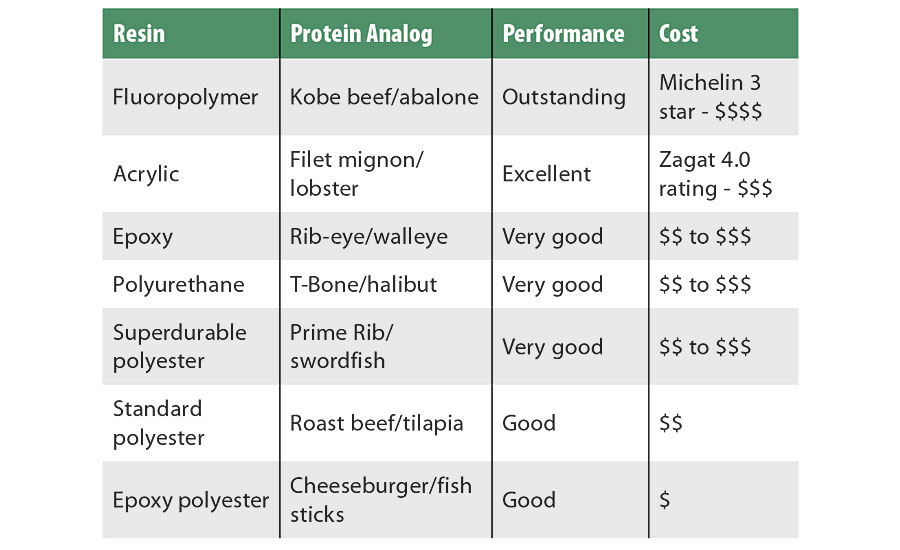
TABLE 2 » Outdoor durability performance of various resin systems for powder coatings.
Other properties influenced by your resin choice are important to note. In particular, chemical and corrosion resistance are features routinely specified by coatings users. Chemical resistance is pretty straightforward – specifiers require resistance to compounds the coating is expected to come into contact with during the service life of a product. For appliances this may mean detergent, bleach and food stain resistance, depending on the machine. For automotive components it can be acid rain, gasoline, cleaners and the insidious brake fluids.
As you can see from Table 3, toughness as represented in chemical and corrosion resistance does not always follow outdoor durability. Consequently many end users will specify a combination of two coats – an epoxy-based primer followed by a polyester or fluoropolymer-based topcoat.
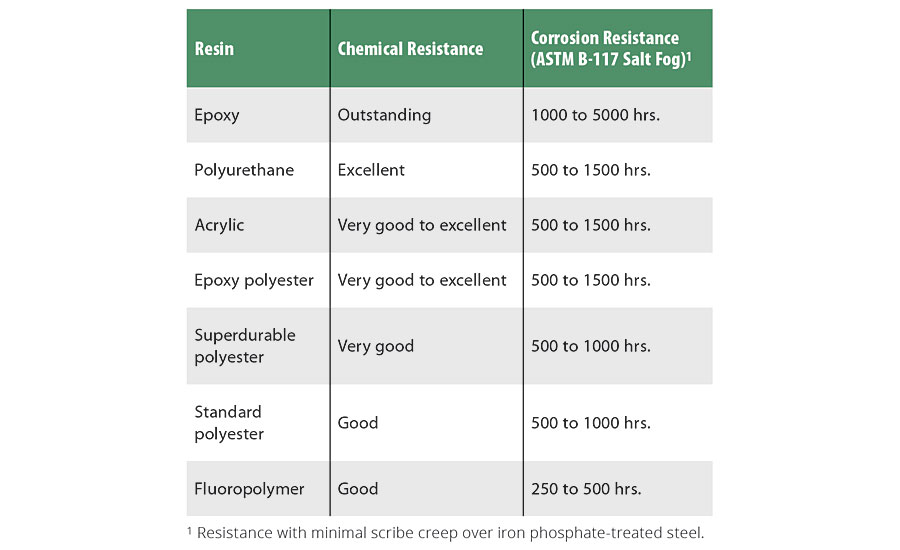
TABLE 3 » Chemical and corrosion resistance of various resins used in powder coatings.
Before I leave the kitchen, I would like to provide you with recommendations for where to use formulations based on the main course protein (Table 4).
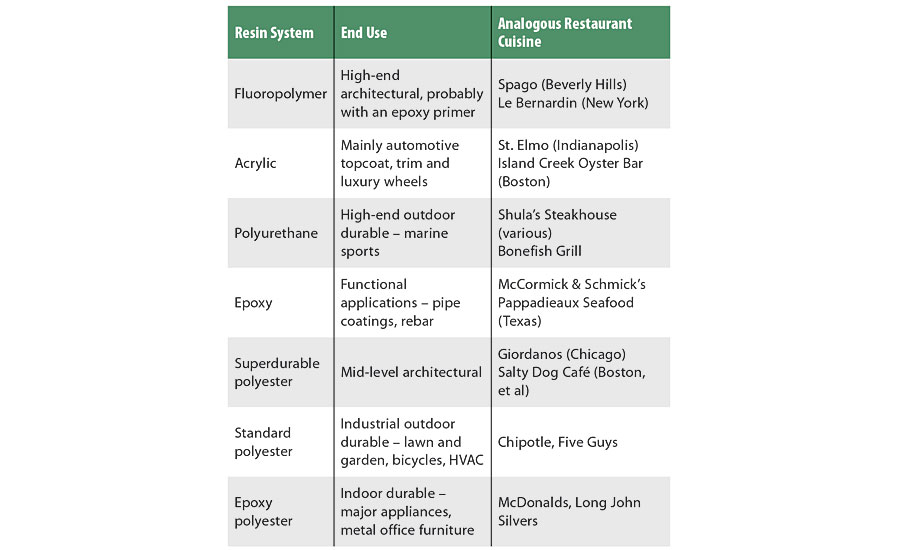
TABLE 4 » Recommendations on which type of resin to use for various applications.
Formulations, like recipes, are the best when they fit the occasion and/or customer specification. The process of creating a product that perfectly fits the end use is quite a rewarding experience and you’ll recognize your customers’ satisfaction from your hard work. Happy cooking.
Looking for a reprint of this article?
From high-res PDFs to custom plaques, order your copy today!