Pre-Treating Various Woods with High-Performance Light Stabilizers

Waterborne clear coatings have been developed to address the concerns of high VOCs that are normally associated with conventional solvent-based coatings.1 To preserve the beauty of wood grain, waterborne clearcoats containing UV absorbers and light stabilizers are commonly applied to the surface for protection. However, sunlight and UV radiation can penetrate coatings on wood surfaces, causing yellowing. The yellowness comes from both the coating and lignin. Lignin, when exposed to the sunlight, can easily be degraded. Wood, as a composition of lignin, cellulose and hemicellulose, appears to yellow due to the photodegradation of lignin.2-6
Eversorb® AQ (EV-AQ), a blend of UV absorber and HALS, has been developed specifically for waterborne clearcoats. Eversorb SB (EV-SB) is a lignin stabilizer designed for wood pretreatments to protect lignin from UV light degradation.
According to our studies, pretreatment of a wood surface prior to the application of a clear topcoat can effectively extend the protection of lignin from UV light degradation. This article is a comparison study using an accelerated weathering method to test different wood types pretreated with and without Eversorb SB in different co-solvents. Design of Experiment (DOE) was used in this study.
Lignin is a complex organic polymer that contains hydroxyl functional groups (-OH). To check if solvents can affect the protection performance of Eversorb SB, different co-solvents were mixed with Eversorb SB in the experiment.
Theoretically, Eversorb SB pretreatment should have better performance on softwoods than on hardwoods due to higher lignin content. Softwoods contain 25-35% lignin and hardwoods contain 18-25% lignin.9 This article discusses five different types of woods, including softwoods (Southern pine and Douglas fir) and hardwoods (Cedar, Southern beech and African teak).
Experiment
The three model formulations used in this study were an acrylic-based waterborne clear coating, wood pretreatments and co-solvents. Their detailed compositions are shown in Tables 1-3. Five different woods were chosen in the region. DOE was used to design test runs as well as to analyze test data. DOE techniques allow us to validate the data.
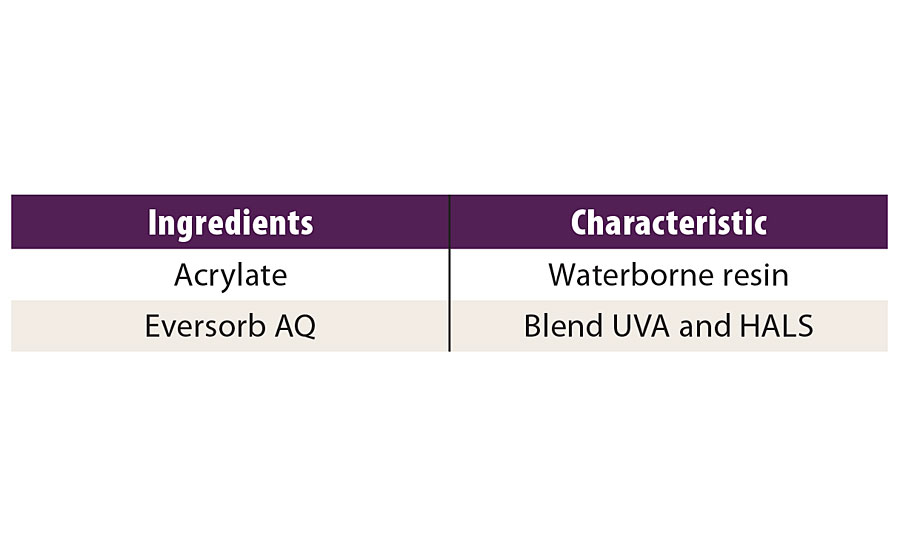
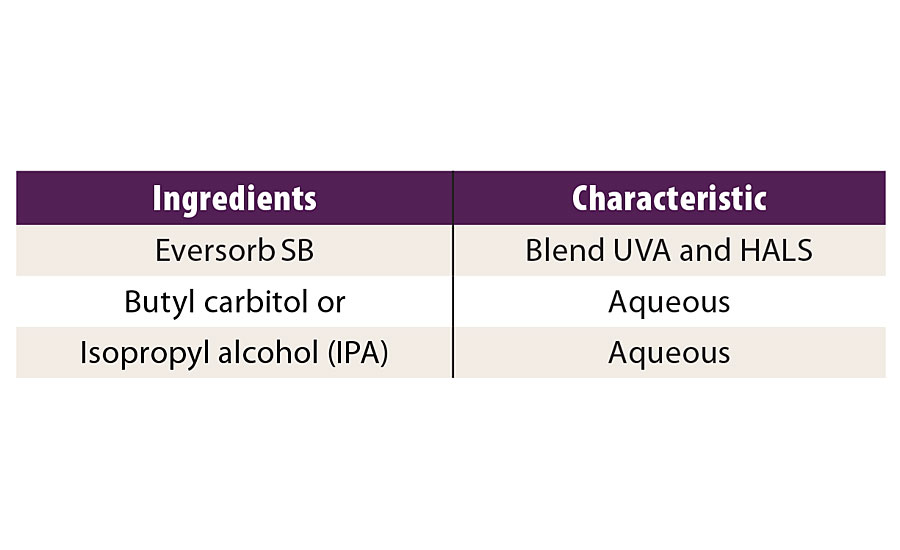
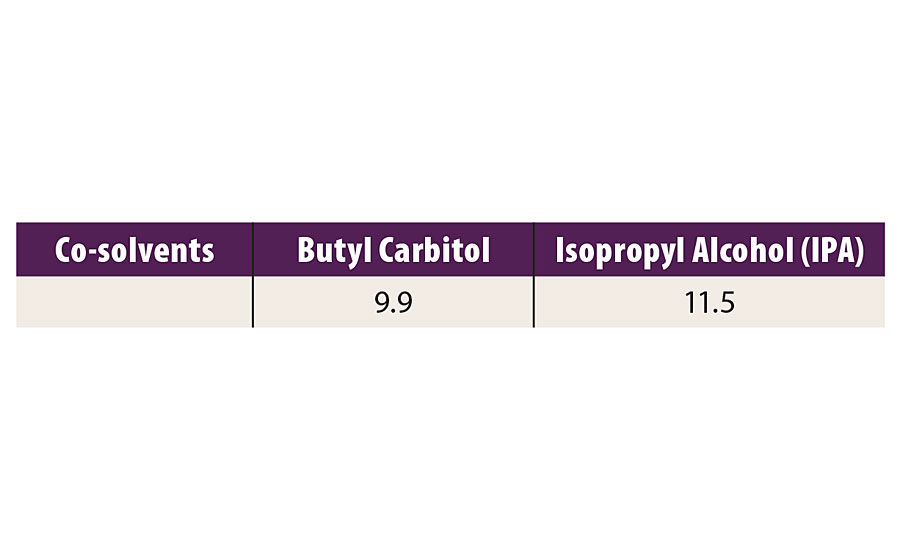
Wood Protection Using Waterborne Light Stabilizer and Lignin Stabilizer
According to our DOE, EV-SB offers good performance in Southern pine’s pretreatment. Before and after exposure of delta E measurements (Tables 4 and 5), using EV-AQ in the topcoat over EV-SB in the pretreatment resulted in different degrees of protection. Evidently, EV-AQ plus EV-SB was able to provide better protection.
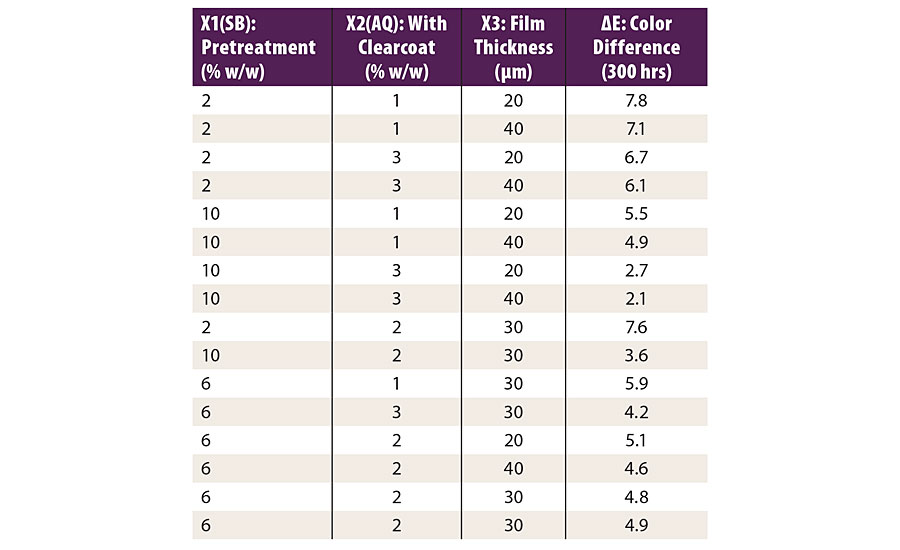
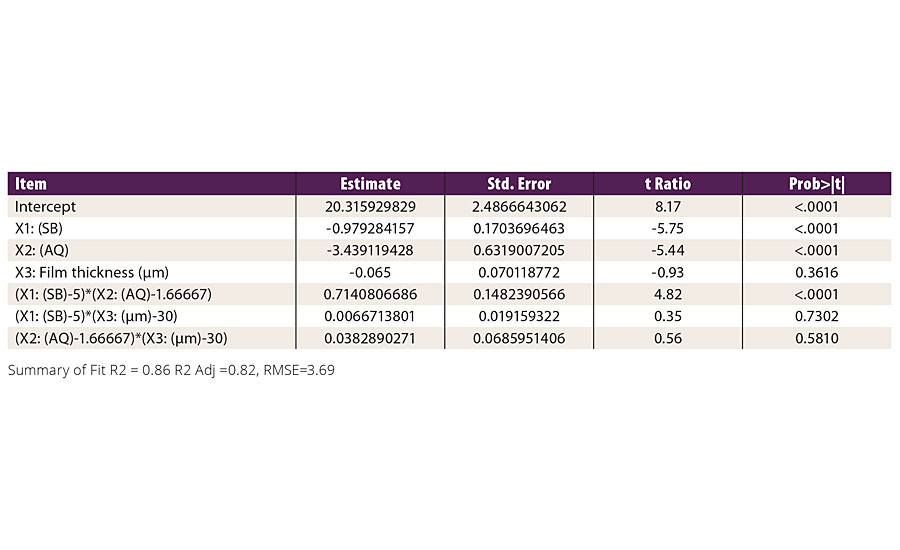
For EV-AQ, the effect factor of wood protection was about 14.69%. For EV-SB, the effect factor of wood protection was about 13.35%. EV-AQ and EV-SB interact, and the effect factor for this is 10.9% (Figure 1). Both EV-AQ and EV-SB offer good performance for wood protection. From Table 5, we can get the equation of color difference (DE) in Figure 1.
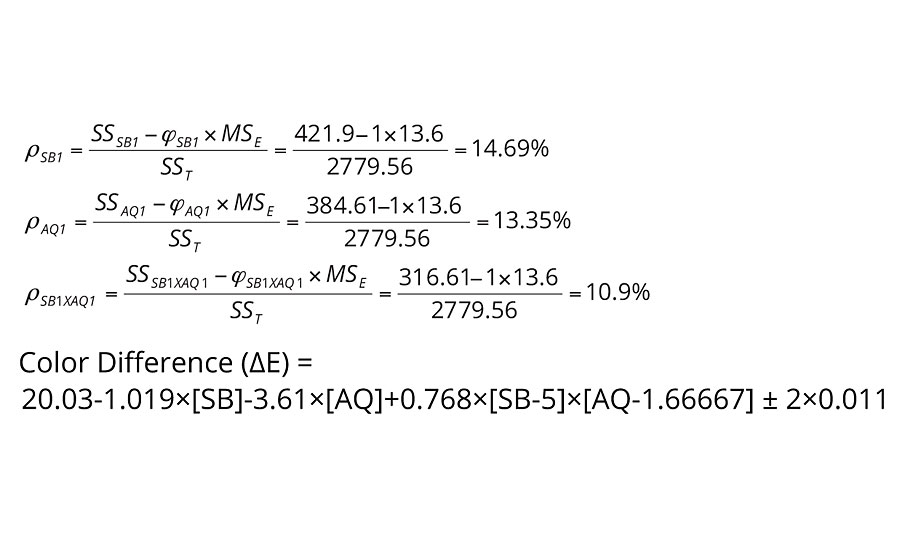
Screening Design of Different Type of Woods and Co-Solvents Using EV-AQ and EV-SB
A screening design (Table 6) was used to identify factors that have the most minimal color change after weathering tests. The mathematical model derived from data indicates all factors: X1- five different types of wood (Cedar, Douglas fir, Southern beech, African teak and Southern pine); X2 - three types of treatments (X2-1: topcoat: waterborne acrylic resin, X2-2: wood pretreatment: butyl carbitol mixed with EV-SB, topcoat: EV-AQ mixed with acrylic resin and X2-3: wood pretreatment: IPA mixed with EV-SB, topcoat: EV-AQ mixed with acrylic resin). Tables 7-9 show the analysis of variances, parameter estimates and effect tests.
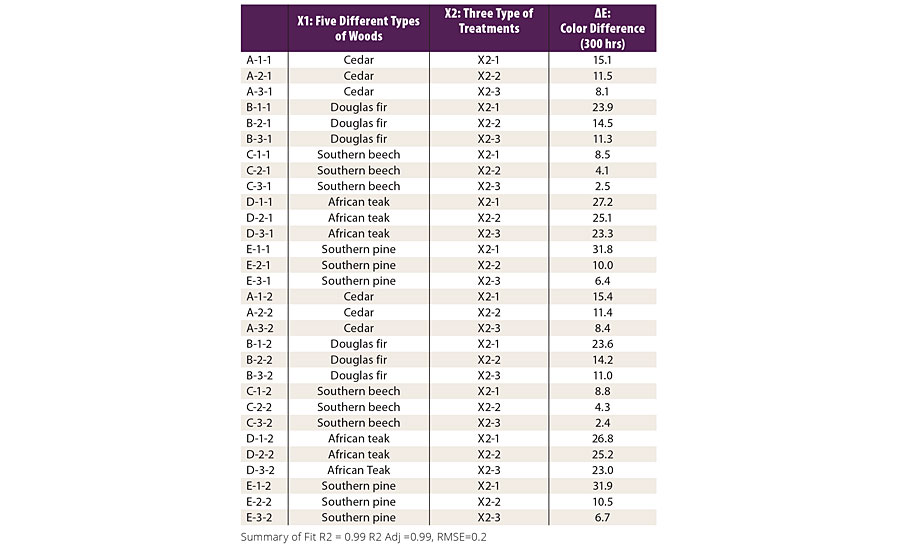
X2-3: Wood pretreatment: IPA mixed with 10% EV-SB, Topcoat: 2% EV-AQ mixed with acrylic resin
X2-1: Waterborne acrylic resin
X2-2: Wood pretreatment: Butyl carbitol mixed with EV-SB, Topcoat: 2% EV-AQ mixed with acrylic resin .
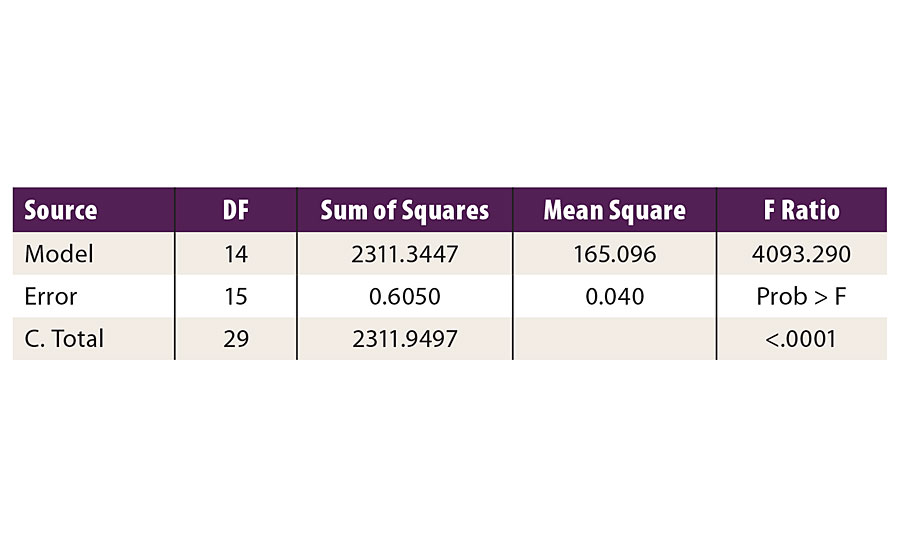
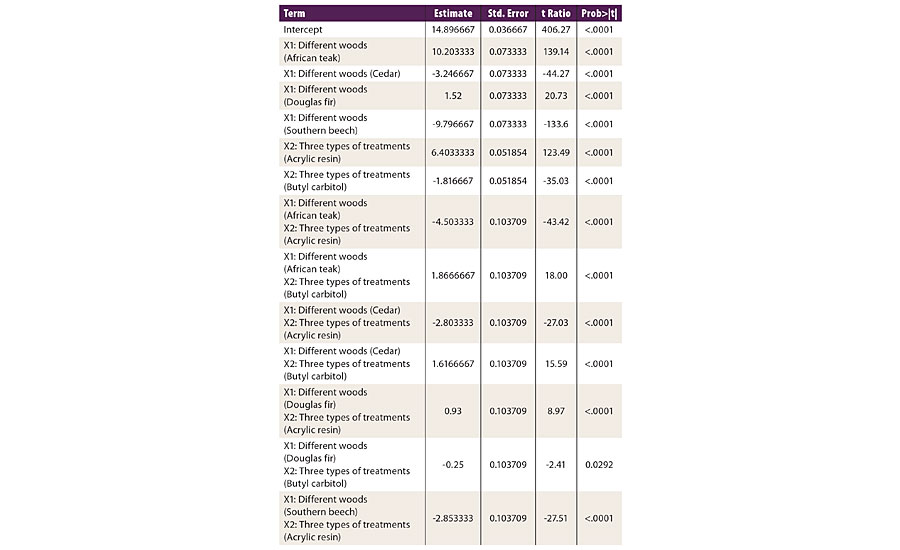
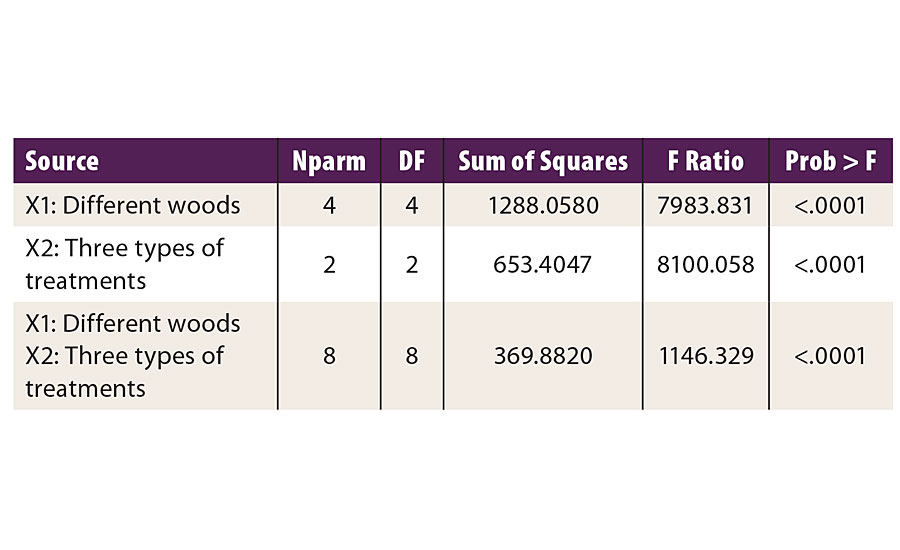
The Optimal Prediction Profiler
The prediction profiler (for example, Southern pine) shows the effect of three types of treatment after weathering testing for 300 hrs. For the item that uses waterborne acrylic resin only, the yellowing after weathering testing is significant (Color difference DE=31.85) (Figure 2). The 10% EV-SB mixed with butyl carbitol in the pretreatment and 2% EV-AQ in the topcoat. The performance is better than the blank (Color difference DE=10.25) (Figure 3). The 10% EV-SB mixed with IPA in the pretreatment and 2% EV-AQ in topcoat. The light fastness of Southern pine is the best (Color difference DE=6.55) (Figure 4). Photos of different types of wood after weathering testing are shown in Figures 5-9.
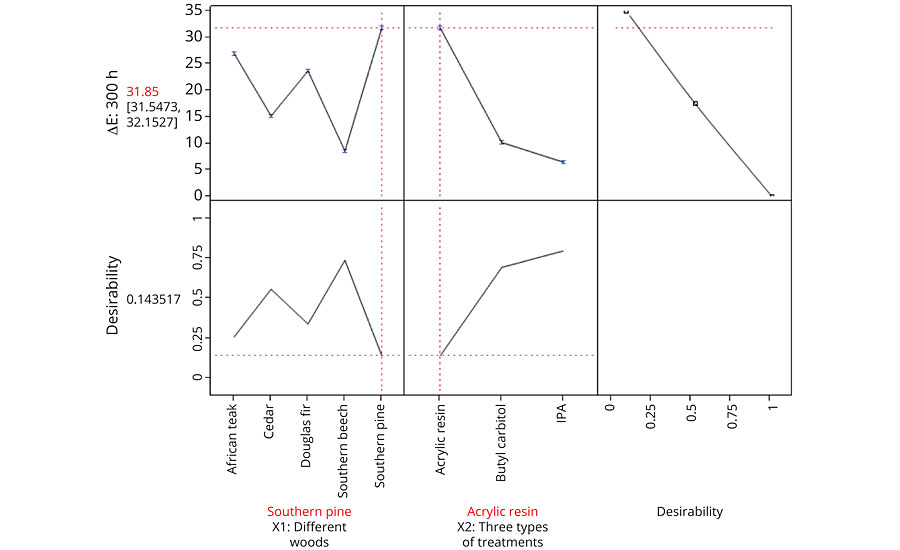
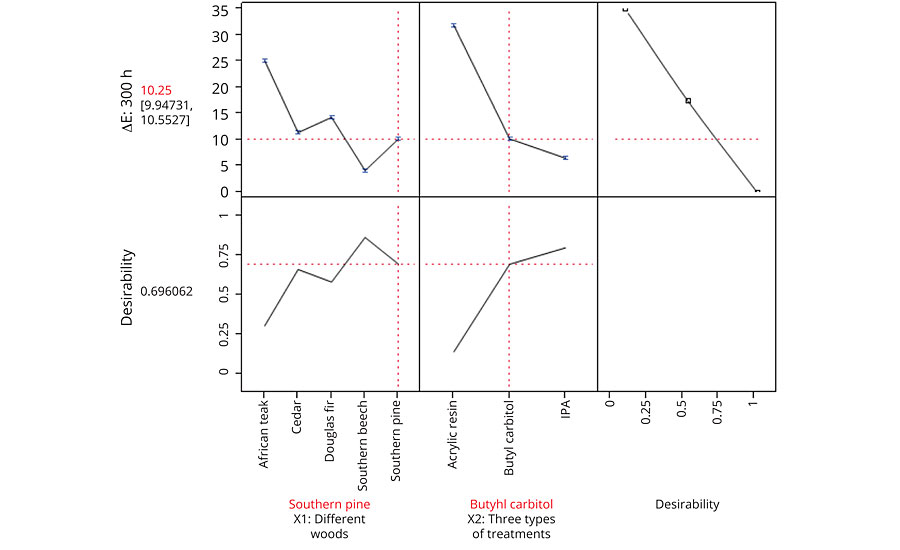
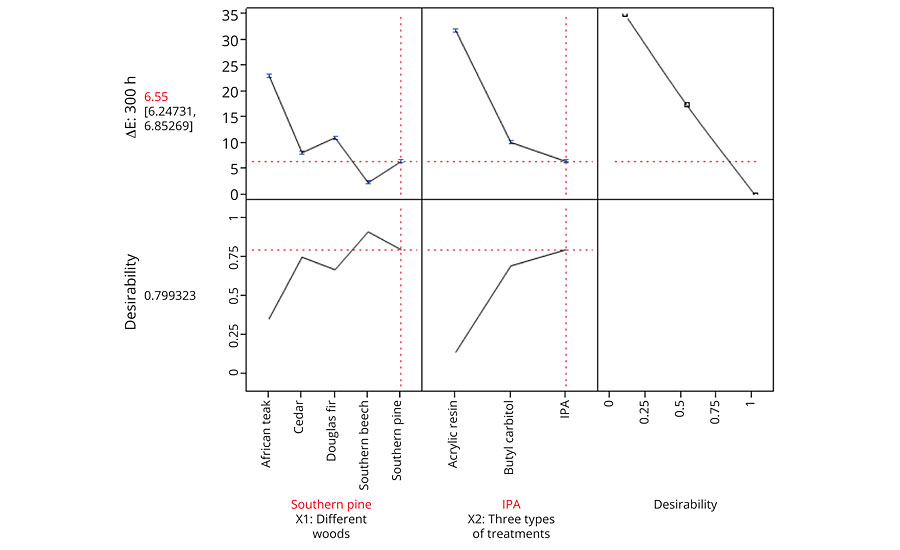
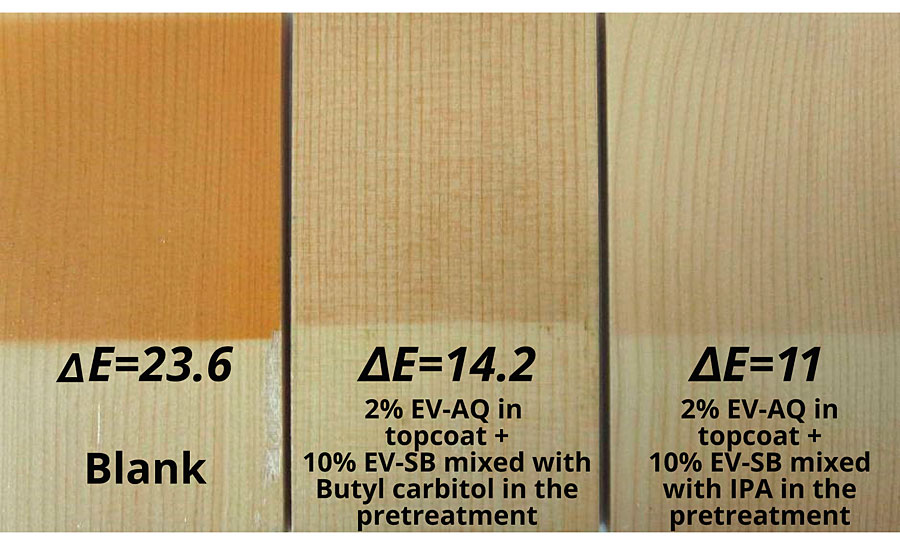
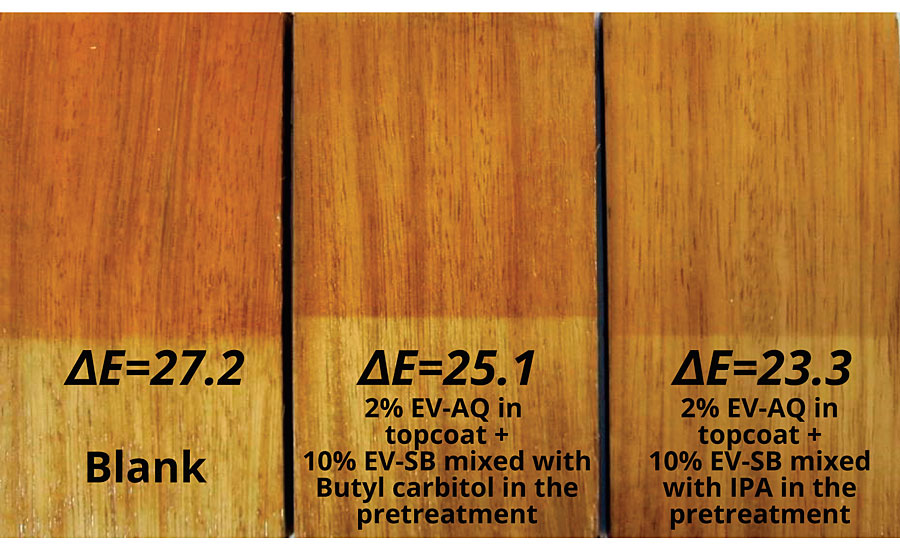
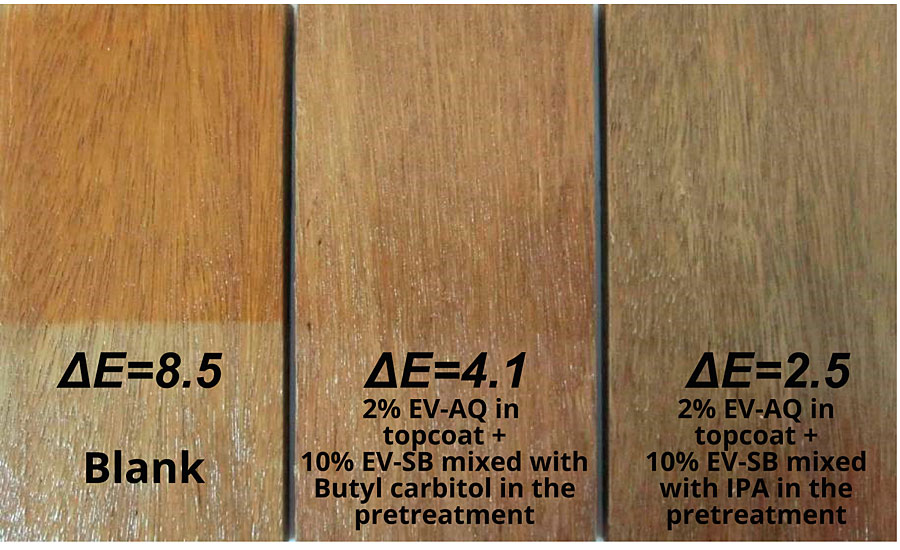
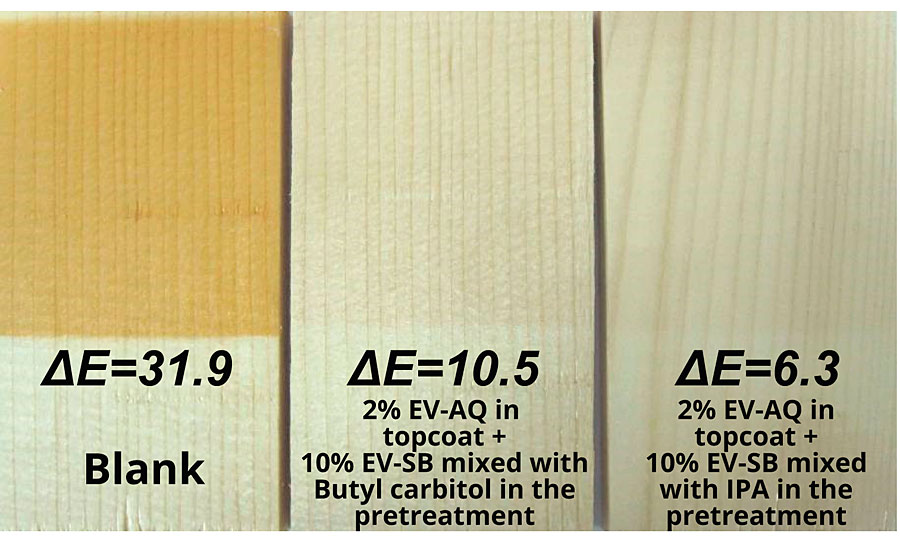
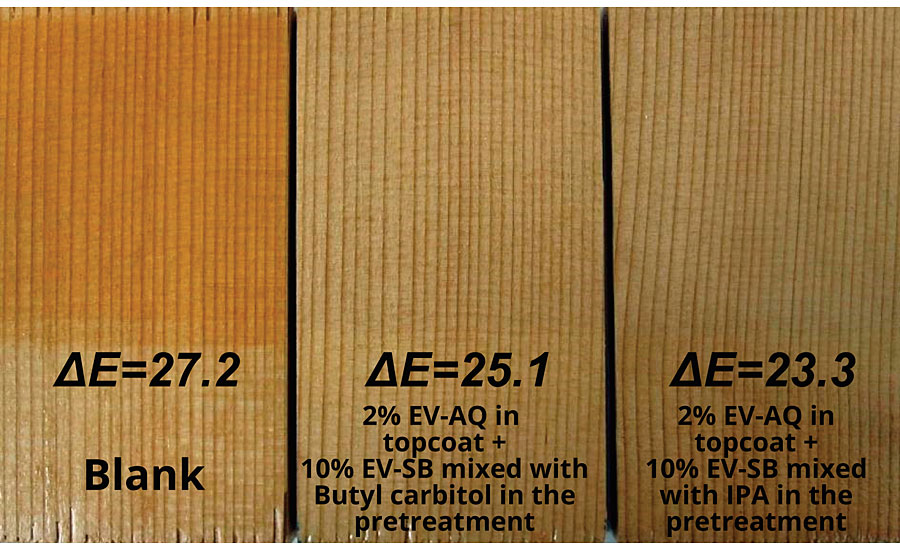
Results
Test data confirmed that increasing the concentration of Eversorb AQ in the clear topcoat can effectively protect Southern pine from UV light degradation. Further experiments show that the pretreatment on Southern pine with Eversorb SB prior to the application of a clear topcoat provides better weatherability than the one without Eversorb SB pretreatment. After weathering tests, the results show that the mixture of Eversorb SB and Eversorb AQ can significantly protect wood surfaces from yellowing. In addition, Eversorb SB mixed with isopropyl alcohol can provide better performance than Eversorb SB mixed with butyl carbitol.
Furthermore, data also suggests that by increasing the coating thickness, the light fastness of Southern pine can also be improved to some degree, but not as effectively as other methods, such as increasing the dosage of light stabilizers in the clearcoat or pretreating the Southern pine prior to the clearcoat application.10
Conclusion
Environmentally friendly coatings are the trend for future development. We have developed several unique products specifically for coatings. Eversorb AQ, a blend of UV absorber and HALS, is designed for waterborne clearcoats. Eversorb SB, designed for wood pretreatments, can protect lignin from UV light degradation.
Lignin is a complex organic polymer that contains hydroxyl functional groups (-OH). The solubility parameters of isopropyl alcohol and butyl carbitol are 11.5 and 9.9, respectively. After weathering testing, the results show Eversorb SB can provide better performance in isopropyl alcohol than in butyl carbitol. In other words, the higher solubility parameter of the solvents can offer better protection.
Due to higher lignin content in softwoods (25-35%) to hardwoods (18-25%), theoretically Eversorb SB pre-treatment could offer better protection to softwoods. Our data indicates that pre-treatment with Eversorb SB provides significant protection in softwoods (Southern pine and Douglas fir) compared with hardwoods (Cedar, Southern beech and African teak).
Coating manufacturers may still need to run the experiments to confirm their coating systems’ compatibility. Also, a tailor-made UV absorber and light stabilizer package can be designed to fulfill your special needs.
References
1 Huang, Y.H.; Yang, Y.C. Light Stabilizers for Clear Coatings. Polymers Paint Colour Journal, 2010, 2000(4544):38.
2 Evans, P.D.; Wallis, A.F.A.; Owen, N.L. Weathering of Chemically Modified Wood Surfaces. Wood Science and Technology, 2000, 34(2): 151-165
3 Chang, S.T.; Hon, D.N.S.; Feist, W.C. Photodegradation and Photoprotection of Wood Surface. Wood and Fiber Science, 1982, 14(2): 104-117.
4 Evans, P.D.; Wallis, A.F.A.; Owen, N.L. Weathering of Chemically Modified Wood Surfaces. Wood Science and Technology, 2000, 34(2): 151-165.
5 Heitner, C. Light-Induced Yellowing of Wood-Containing Papers. In “Photochemistry of Lignocellulosic Materials” (C. Heitner and J.C. Scaiano Ed.) [A]. American Chemical Society. Washington D.C. 1993, pp.2-22.
6 Schmidt, J.A.; Heitner, C. Light-Induced Yellowing of Mechanical and Ultra-High Yield Pulps. Part3. Comparison of Softwood TMP, Softwood CTMP, and Aspen CTMP. Journal of Wood Chemistry and Technology, 1995, 15(2): 223-245.
7 Heitner, C. Light-Induced Yellowing of Wood-Containing Papers. In “Photochemistry of Lignocellulosic Materials” (C. Heitner and J.C. Scaiano Ed.) [A]. American Chemical Society. Washington D.C. 1993, pp. 2-22.
8 Schmidt, J.A.; Heitner, C. Light-Induced Yellowing of Mechanical and Ultra-High Yield Pulps. Part3. Comparison of Softwood TMP, Softwood CTMP, and Aspen CTMP. Journal of Wood Chemistry and Technology, 1995, 15(2): 223-245.
9 Himmel, M.E.; Baker, J.O.; Overend, R.P. Enzymatic Conversion of Biomass for Fuels Production, ed. By M.J. Comstock, American Chemical Society, Washington, DC (1994).
10 Yang, Y.C.; Huang, S.C.; Chein, C.H.; Dr. Huang, Y.H. Light Stabilisers for Wood Pre-treatment Applications. Polymers Paint Colour Journal, 2011, 201(4565):21-22.
For more information, e-mail iuva@ecic.com.tw.
Looking for a reprint of this article?
From high-res PDFs to custom plaques, order your copy today!