Non-Leaching Reactive Surfactants for Architectural Latex Binders

In the transition to waterborne coatings, emulsion polymers – often referred to simply as latex – have served as one of the most common binders in architectural applications due to the achievable low VOC levels. While relatively environmentally friendly and easy to apply, commercial latex coatings have been known to be susceptible to some performance limitations unique to waterborne systems. The use of water as the carrier requires the use of a variety of water-soluble species, which can cause water sensitivity of the coating once applied. These water-soluble species are mostly surfactants, including wetting agents, colorant dispersions and emulsifiers. These emulsifiers are necessary for the process of emulsion polymerization in the synthesis and required for the stabilization of the latex binder. During the drying of coatings and in moist or humid conditions and even once fully cured, traditional surfactants are released from the emulsion particles, and being surface active, tend to migrate to the surface. This surfactant migration can cause leaching, visible as discoloration or a “snail trail” pattern, as well as a reduction in barrier properties, water resistance and adhesion. Non-leaching reactive surfactants, which can be permanently co-polymerized into the latex, offer the efficiency needed during emulsion polymerization without the negative effects on end-use performance of the coating.
Surfactants in Emulsion Polymerization
Surfactants or emulsifiers are one of the key ingredients in emulsion polymers, and their functions,1-3 can be summarized as:
- Adsorption onto the monomer/water interface to reduce the interfacial tension so that monomer can be emulsified in water upon mixing
- Facilitation and control of the particle nucleation during polymerization
- Adsorption onto the polymer/water interface to provide stability of the growing latex particles and the final polymer dispersion (Figure 1)
- Improvement of compatibility with other ingredients in paints and coatings formulations
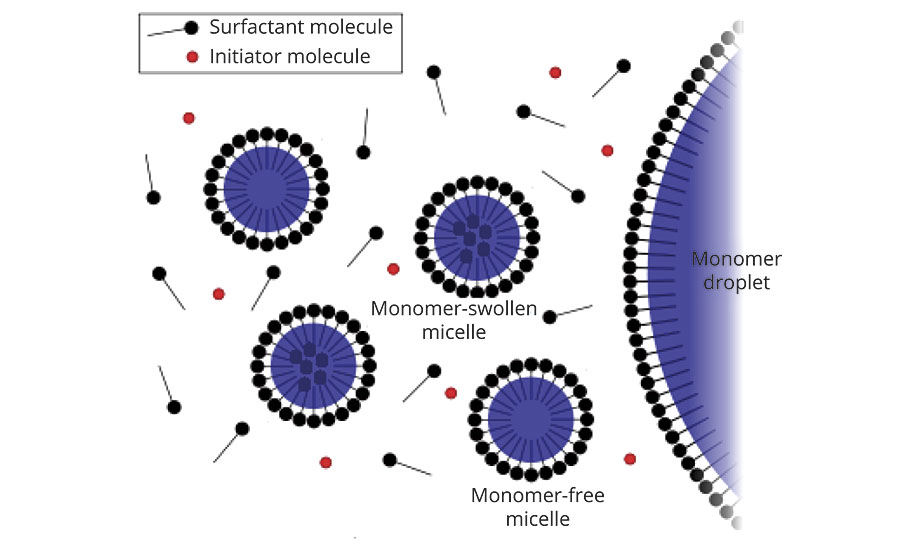
A combination of anionic and non-ionic emulsifiers is most commonly used in emulsion polymerization to control the particle size and to impart enhanced colloidal stability.4-6 Anionic emulsifiers are very effective in providing stabilization via electrostatic repulsion mechanism. They are usually used in the initial reactor charge for “seed” process to control particle size of the emulsion. However, they are sensitive to electrolytes and to change in pH or temperature. Non-ionic emulsifiers tend to have better performance in these areas. Non-ionic emulsifiers function via the steric interference stabilization mechanism, against to the van der Waals attraction between polymer particles (Figure 2). Moreover, they can also improve the shear stability. Non-ionic surfactants are seldom used alone except in non-pigmented systems like primers or top coats.
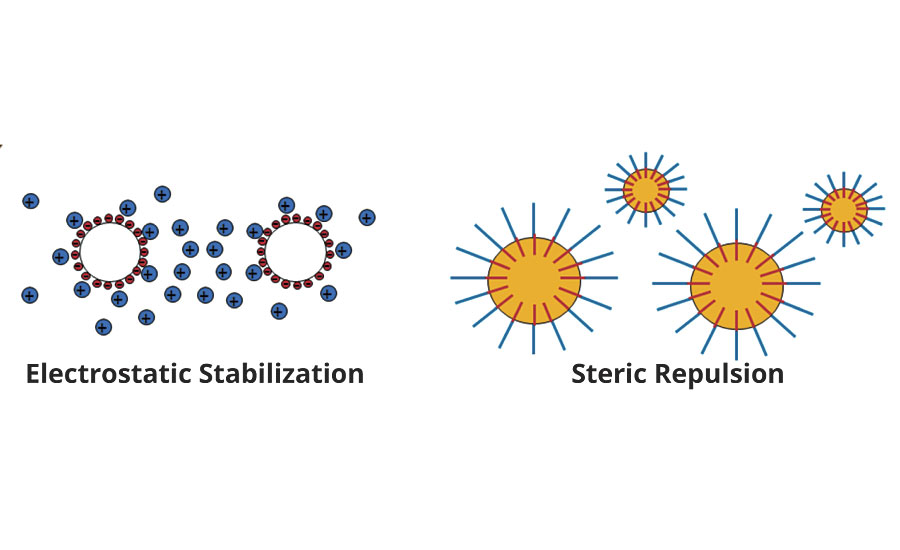
Conventional surfactants accumulate at the polymer particle surface via physical adsorption, forming an energy barrier that protects particles from flocculation and coagulation by either electrostatic repulsion and/or steric hindrance. Nevertheless, the physical interaction between the hydrophobic (hydrocarbon) portion of the surfactants and the polymer particle surface is relatively weak and reversible. Surfactants at interfaces are in equilibrium with surfactant dissolved in the water. This equilibrium can be shifted by external stresses generated by storage conditions, such as freezing/high temperature, or from shear stresses produced during pumping, mixing or high-speed applications. Formulating emulsion polymers in pigmented or plasticized coatings can cause surfactant desorption and preferential redistribution. This leaves interfaces unprotected and results in irreversible coagulation of the colloids. Additionally, the incompatibility between the hydrophilic part of the surfactant and the polymer matrix can result in phase separation during film formation. This leads to the formation of hydrophilic surfactant domains at the film surface and inside the polymer film, as illustrated in Figure 3.
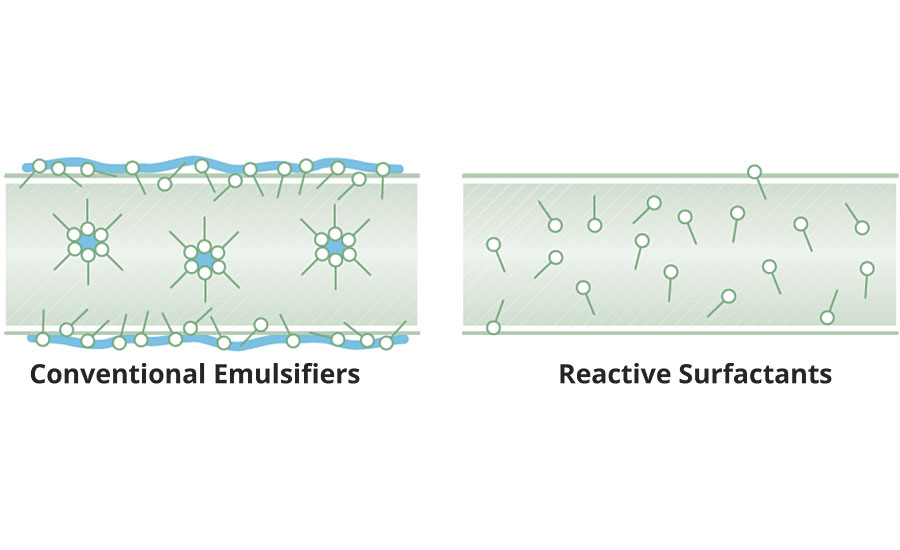
Reactive Surfactants in Emulsion Polymerization
The use of reactive surfactants, also referred to as co-polymerizable or non-migratory emulsifiers, has been studied for some time. Irreversibly anchored surfactants produce emulsion polymers with superior colloidal stability. They function in a similar manner to conventional surfactants in adsorbing at the interfaces to provide colloidal stability. However, instead of remaining as only physically adsorbed, they copolymerize with the monomers and are covalently anchored onto the surface of latex particles during the polymerization. The formation of hydrophilic domains of surfactant is avoided, resulting in dry films with better water repellency and adhesive properties.
In order to optimize formulation successfully with reactive surfactants to copolymerize with vinyl unsaturated monomers, the following strategies are recommended:
- A semi-continuous emulsion polymerization process, with a minimum amount of (anionic) reactive surfactant during particle nucleation and the majority added during particle growth, as a pre-emulsion or separate surfactant stream. This is to avoid excessive burial of the surfactant during the particle growth phase.
- Polymerization in acidic conditions; pH 3.5-4 is usually preferred. This is to avoid copolymerization of the reactive surfactants with (meth)acrylic acid, often part of the co-monomer composition in the aqueous phase. In general, aqueous phase polymerization should be minimized, as this can cause formation of water-soluble oligomers, which may flocculate growing polymer particles or affect shear or freeze/thaw stability of the latex.
A starved monomer feed is preferred, as it has shown higher conversion of the surfactant.
Experimental
Reactive surfactants have been analyzed as replacements for traditional emulsifiers (Table 1) in a variety of copolymers, including those listed in Table 2.
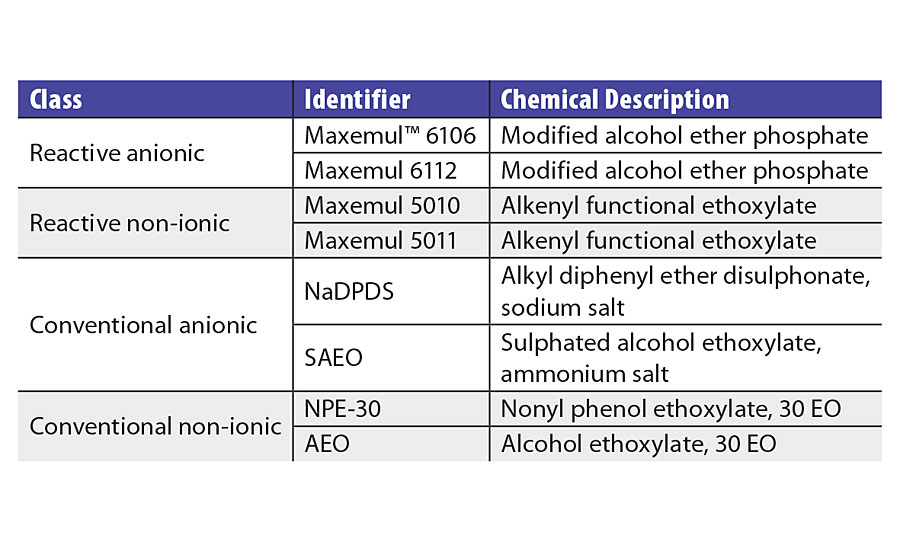
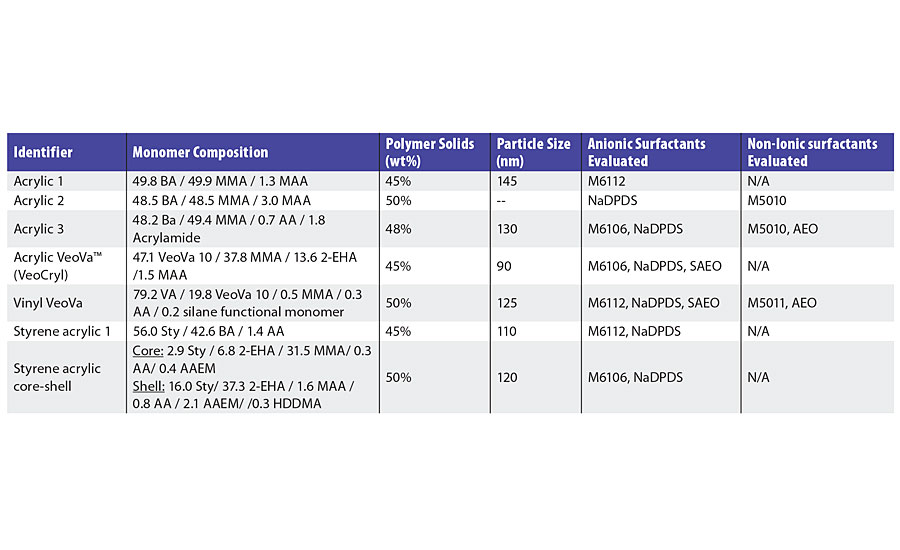
Demonstration of Reactivity
Reactivity, or conversion, of the surfactants can be quantified based on the fraction remaining in the aqueous phase after polymerization. One suitable method for the anionic reactive surfactants studied is the quantification of phosphorus via ICP-MS after ultracentrifugation of the latex. In one such study (Acrylic 1), in a butyl acrylate/methyl methacrylate/methacrylic acid (BA/MMA/MAA) copolymer, the final conversion of the anionic reactive surfactant was found to be greater than 90%.
The copolymerization of the non-ionic reactive surfactants has also been studied in detail using latex Acrylic 2. Here, a seeded butyl acrylate (BA)/methyl methacrylate (MMA)/acrylic acid (AA) copolymer system was analyzed.7-8 Free surfactant was separated from the latex via ultrafiltration and quantified via HPLC. When polymerization is carried out under monomer-starved conditions, 70% of non-ionic reactive surfactant is converted by the end of the monomer addition.
The successful copolymerization of reactive surfactants can also be determined by more observational means. For instance, a latex in which the emulsifier has been grafted to the polymer particles will show significantly less foaming than an emulsion with a comparable concentration of conventional surfactants (Figure 4).
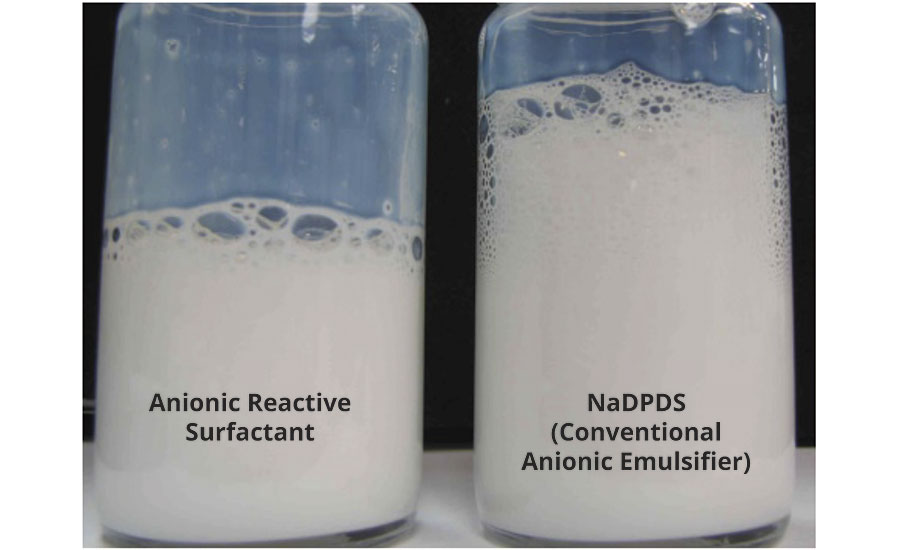
More significantly, the non-migratory nature of the reactive emulsifiers can be confirmed by assessment of dried films of the polymer. Conventional surfactants aggregate at the polymer/air interface during drying. The presence of these surface active agents can be quickly determined by a measurement of the contact angle of a droplet of water on the dry polymer film. The contact angle of a Veocryl polymer dried at room temperature for 24 hrs was measured on Attension Theta from Biolin Scientific (Figure 5). The contact angles were 71° and 43° for Maxemul 6106 and NaDPDS respectively. This supports the theory that during film formation, emulsion particles release conventional surfactants that migrate to the film surface, but reactive surfactants are chemically grafted and remain in the polymer matrix.
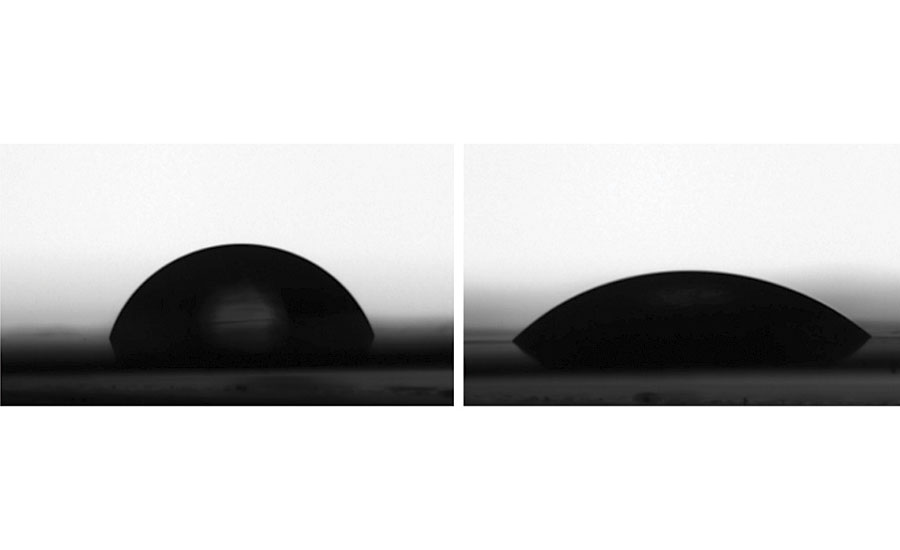
The effects of conventional surfactants on a polymer or coating persist even after washing away from the surface. Figure 6 is an atomic force microscopy image visualizing the effect of surfactant exudation on the surface of a styrene (Sty)/BA/AA latex produced via a seeded semi-continuous emulsion polymerization. A sodium alkyl diphenyl ether disulphonate (NaDPDS) conventional surfactant was used for the generation of seed latex. Separately, starting from the same seed latex, a non-ionic reactive surfactant (right) was used during the particle growth stage and compared to nonyl phenol ethoxylate (NPE-30, left). The AFM image was taken after water washing of the dry film surface of both polymers. Pinholes were observed from extraction of surfactant aggregates with water washing in the conventional surfactant example. No surfactant aggregation nor pinholes were present where the reactive surfactant was employed.9
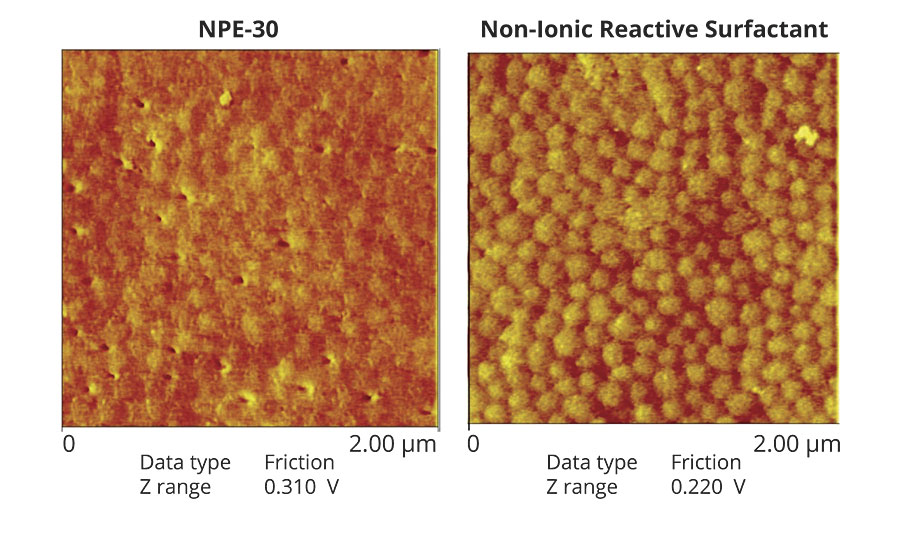
Water Resistance
High porosity and low film density of a dry polymer film are results of the formation of these microvoids or hydrophilic channels. This causes the dry film to have high water uptake and water diffusion rate. There are two possible mechanisms by which conventional surfactants may contribute to the formation of these tiny holes:
1. As discussed previously, surfactant is released from the emulsion particle surface during the drying and film formation of the emulsion polymer. The excess of surfactant in the latex that phase separates aggregates into inverse micelles in the dry film. Water can then accumulate in the inverse micelles.
2. Polymer particles flocculate during water evaporation at low surfactant concentration, or when the surfactant has poor affinity to the polymer surface. The capillary forces cannot close the voids that are formed resulting from flocculation.
The presence of microvoids or inverse micelles in the film results in poor barrier properties. Water is able to penetrate and swell the film, and the diffusion rates of water through the coating increase sharply. Surfactant accumulating at the polymer/substrate interface disturbs adhesion of the binder. Rapid whitening or blooming of the dry film in humid conditions is due to water accumulating in microvoids in the bulk of the film. These water pockets scatter light, causing visible whitening when they become sufficiently large. Furthermore, diffusion of surfactants to the film surface disturbs the packing of the polymer particles and gloss reduction can result.
In one test, Vinyl VeoVa films were cast in identical 9-cm-diameter glass Petri dishes by drying equal amounts by weight (12.00 g) for one week, resulting in clear films of equal thickness. The film was then covered with deionized water and photographed after 24 hrs. Both film samples, originally transparent, are shown in Figure 7 over an image to demonstrate the change in opacity. The logo beneath the sample prepared with reactive surfactant (right) is still clearly visible, while the one prepared with conventional surfactant (left) turned completely white.
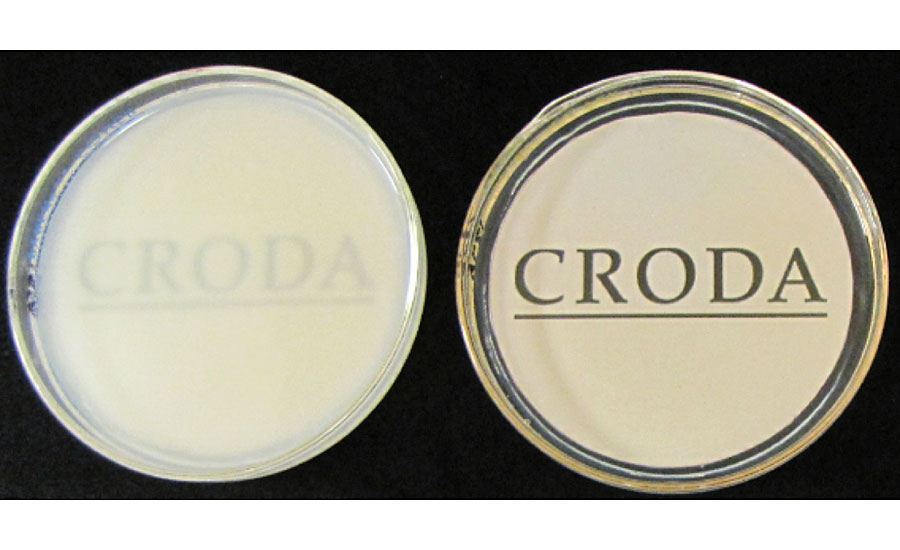
A styrene acrylic core-shell latex was formulated to Tg1 -16 °C, Tg2 64 °C for blocking resistance in wood coatings. Three coats of the latex were applied to cedar panels of standard dimensions (17x3.5 cm). The panels were dried for 1 day between coats and 7 days after the third. Following ASTM D7433 (Cobb test), the water absorption rates of the coated wood panels were assessed gravimetrically. Figure 8 shows the difference in absorption rates between reactive surfactant and sulphated alcohol ethoxylate stabilized polymers.
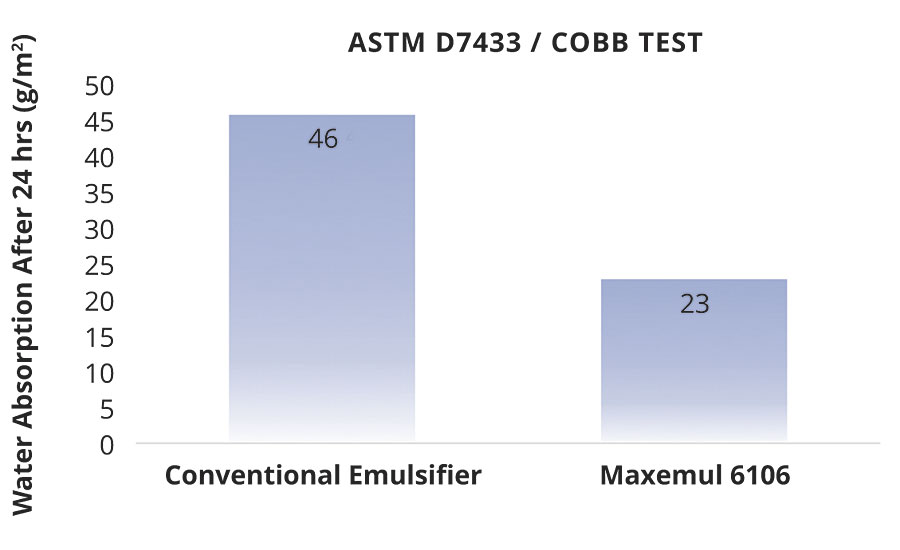
Similar resistance to water permeation, in the vapor phase, was demonstrated in the Veocryl copolymer, as quantified by ASTM D1653B. Two coats of latex, 11.4 µm each, were applied on unbleached porous Kraft paper and dried at 50 °C. A standard perm cup was filled with deionized water, and the evaporation of water out of the sealed cup under standardized conditions was measured gravimetrically (Figure 9).
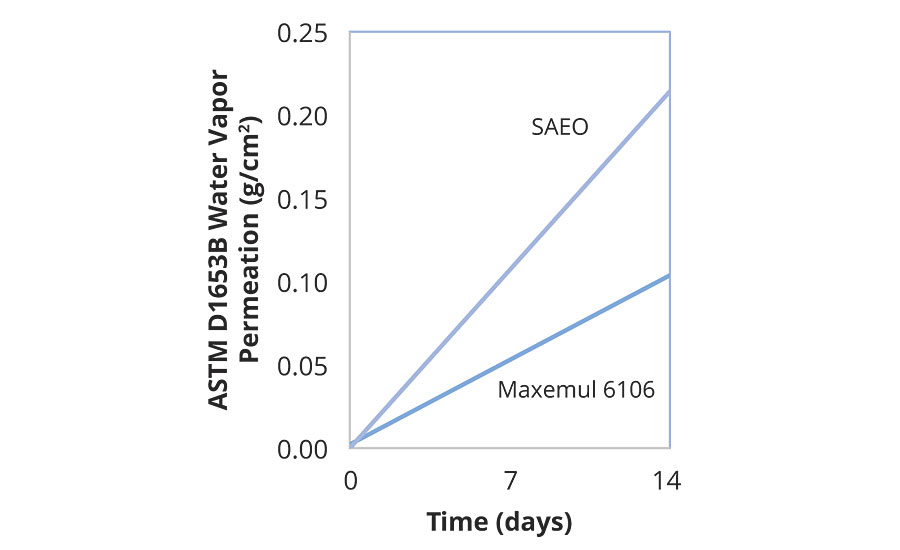
Surfactant Leaching/Snail Trail
A Sty/BA/AA latex at 45% polymer solids was produced via a seeded semi-continuous emulsion polymerization using anionic reactive surfactants or NaDPDS. Binders were formulated into a 20% PVC white enamel with 2% blue universal colorant added. The paint was applied on a glass plate with a 150-µm wire bar applicator and let dry at room temperature for 7 days. After drying, the panels were positioned at a 30° angle, and 5 mL water was applied with a pipette and allowed to evaporate. As shown in Figure 10, a snail trail is visible due to surfactant leaching, but only in the case of conventional NaDPDS.
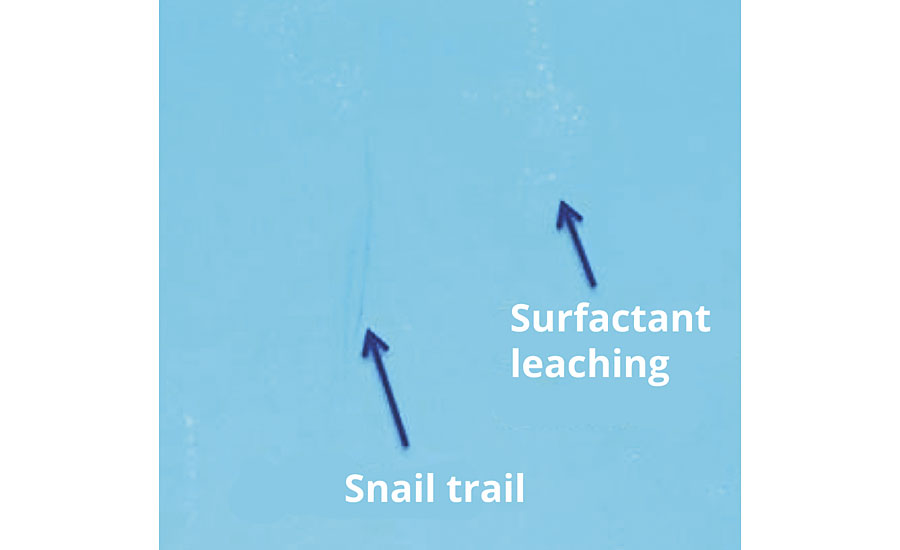
Efflorescence
In concrete coatings, the diminished barrier properties from conventional surfactants can accelerate efflorescence. Porosity and water uptake accelerate the process of migration of alkali to the surface, which is converted to visible salts on the surface. In ASTM D7072, freshly prepared cement panels of uniform size are painted to a uniform thickness and exposed to 100% humidity in a 50 °C condensation chamber for 48 hrs. The acrylic and Veocryl polymers both showed complete efflorescence resistance, while samples prepared with conventional surfactant latexes show discoloration, fading, and salt buildup.
Water Immersion
Porosity and permeability of the binder can also lead to blistering and delamination of the coating. Coatings of a variety of copolymer compositions and PVC were applied to glass panels at a wet film thickness of 178 µm. Figure 11 shows the surface appearance of the coatings after 7 days of immersion in water at ambient conditions.
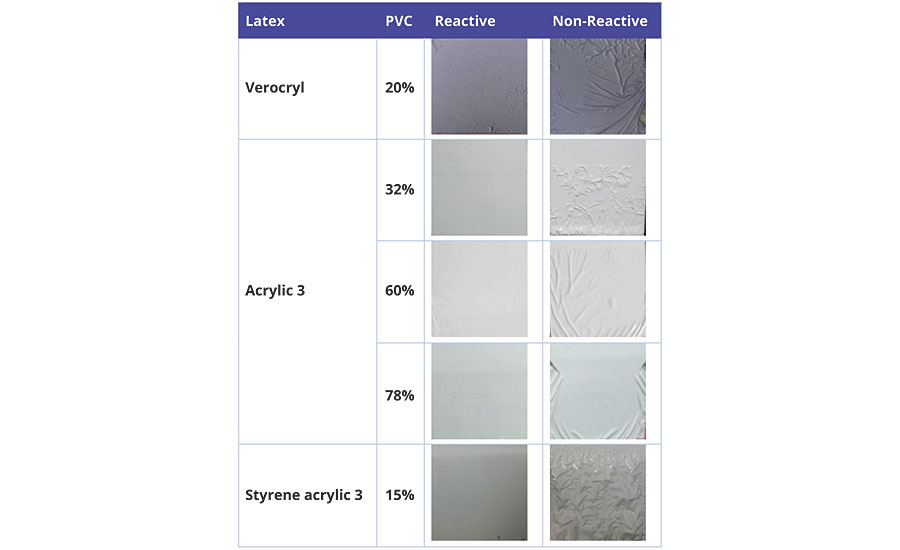
Commercial Reactive Surfactants
It is worth noting that a handful of co-polymerizable surfactants are available in the industry, with some of the most popular chemistries listed being allyalcohol-modified ethersulphates of nonyl phenols or alcohol ethoxylates, as well as styrenated phenol ethersulphates.
Surfactants based on these chemistries are known to have some drawbacks of their own, including negative effects on reaction kinetics, degradative chain transfer, and low or selective reactivity.
The reactive surfactants discussed to this point belong to another, based on the incorporation of a reactive segment within the unsaturated hydrophobe. The presence of labile hydrogen around the unsaturation allows the possibility of grafting via chain transfer. After adsorption at the particle interface, it is readily accessible for copolymerization. Both anionic phosphate ester functional modified alcohol ethoxylates and non-ionic alkenyl functional ethoxylates fall into this class. Schematic structures of both chemistries are given in Figure 12.
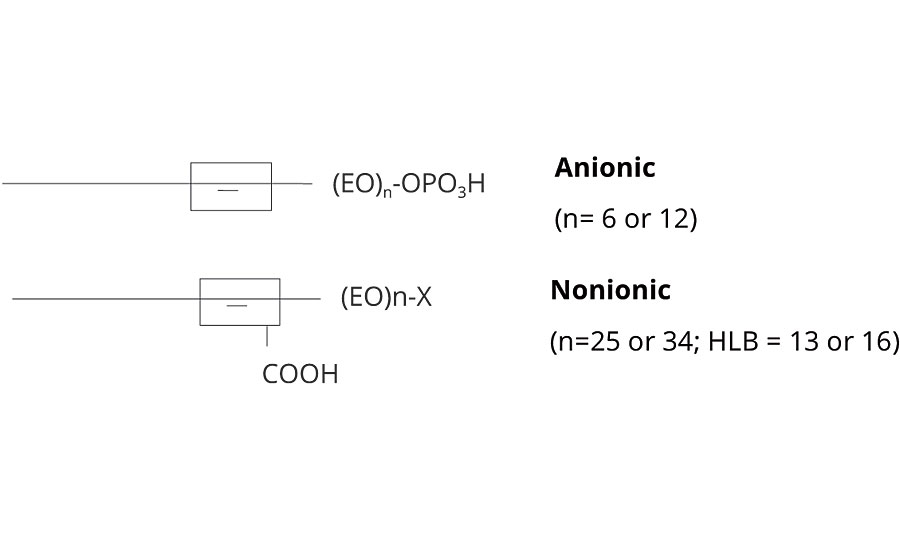
These products have been developed for use as sole emulsifiers during the polymerization process. They can be used in combination with conventional surfactants, but is not needed, and in fact the presence of conventional surfactants will dilute the benefits of the reactive emulsifiers. The anionic reactive emulsifier is micelle-forming and behaves comparable to conventional phosphate ester surfactants. Nucleation efficiency of the non-ionic reactive surfactant is somewhat lower, as with other non-ionic surfactants, and thus these products are predominantly used during the particle growth stage. Surfactant use levels are comparable to those required with conventional surfactants.
Effect of Reactive Surfactant Selection on Molecular Weight
BA/MMA/MAA latices were prepared via a seeded semi-continuous emulsion polymerization. Maxemul 6112 anionic reactive surfactant was used during particle nucleation. Seed latex composition was constant for all experiments. All formulations had equivalent particle sizes of approximately 145 nm. Types of surfactant and concentration from 1.5 to 3.5 parts per monomer (phm) were varied. Reference commercially available reactive surfactants are allyl or propenyl glycidyl ether-modified nonyl phenol ether sulphates, sodium neutralized.10 Molecular weights of the final polymers were determined via GPC.
As shown in Figure 13, the degradative chain transfer of both allylic and propenylic reactive surfactants is clearly demonstrated, such that molecular weight decreases with increasing concentration of surfactant. Molecular weights for polymers obtained with Maxemul 6112 are comparable to a reference binder using a linear alcohol ether phosphate. The linear alcohol contains no labile hydrogen, and hence effects on reaction kinetics are avoided.
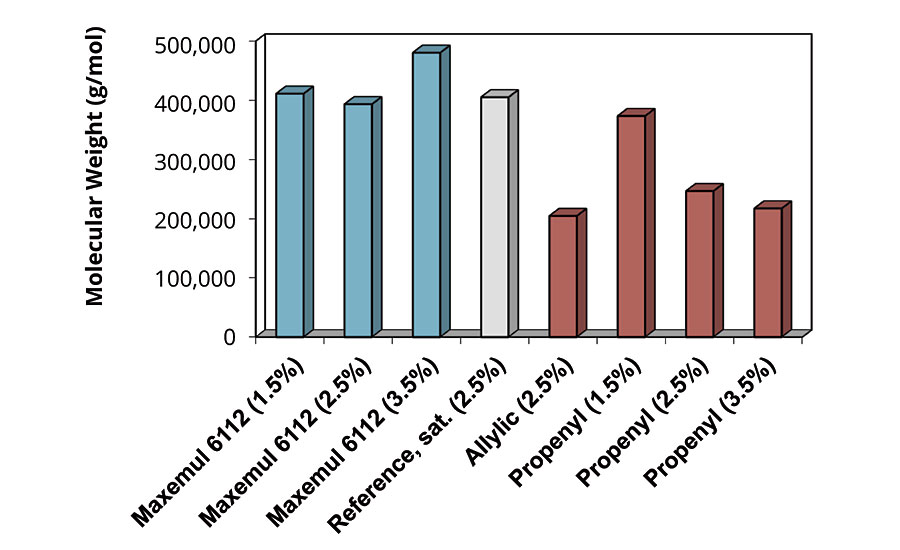
Scrub Resistance
The scrub resistance of low-PVC (pigment volume concentration) coatings (gloss or semi-gloss) is dictated by bulk effects attributed to inherent properties of the polymer, such as molecular weight, gel content, film formation capability, and glass transition temperature or hardness. Maxemul reactive surfactants do not impact bulk binder properties, in contrast to alternative reactive surfactants that may lower mechanical properties by the demonstrated reduction of molecular weight from degradative chain transfer. Additionally, some conventional migratory surfactants negatively affect the dry film properties by plasticization. Coatings formulated with permanently surfactant-grafted binders tolerate a high degree of scrubbing, washing and other damage in gloss paints. Especially in more highly filled systems, the durability benefit of Maxemul reactive surfactants can be most dramatically observed (Figure 14). In higher PVC flat paints, surface effects play a more critical role in the ability of the coating to withstand damage.
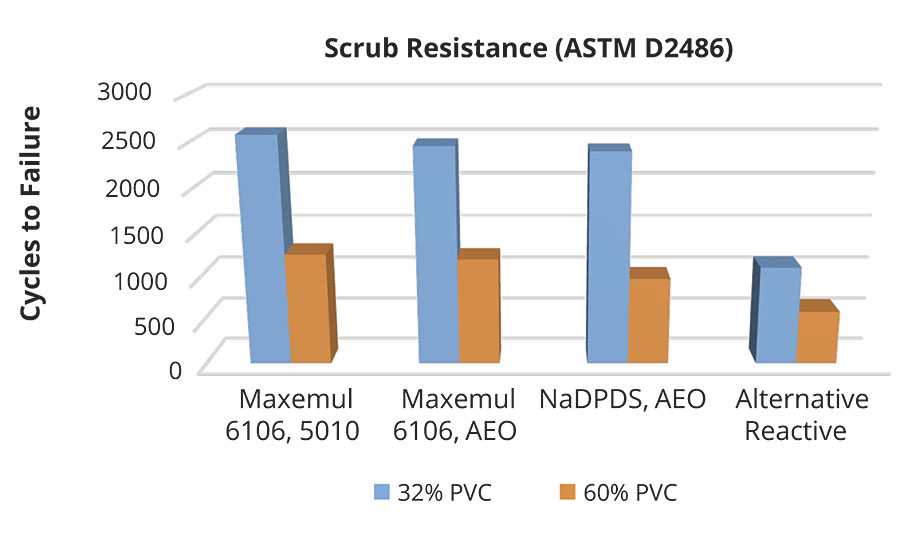
Conclusion
The Maxemul reactive surfactants act as efficient emulsifiers providing colloidal stability and are chemically bonded to the polymer particles during free radical polymerization. The enhanced stability and mitigation of surfactant leaching during and after film forming significantly improve water resistance and barrier properties of the latex binder as a replacement of conventional surfactants. Absence of exudation of surfactant to the coating surface or aggregation in the bulk improves on dry film properties. Furthermore, improvement in performance such as scrub and water resistance carries to formulated pigment coatings and paints. The improvement in water resistance brought about by use of reactive surfactants aids substrate protection, including improved salt spray resistance for metal protective coatings, stain resistance for wood protection and, as demonstrated in this study, efflorescence resistance for coated cement and concrete. Reduction in surfactant leaching also improves early rain or humidity resistance in freshly applied coatings. In addition to the emulsions mentioned, detailed formulation and performance data are available for vinyl acrylic copolymer in architectural coatings. Polymerizable emulsifiers are not limited in application only to architectural latex binders as presented here, but can also be effectively employed in pressure sensitive adhesives, elastomeric coatings, and other emulsion polymer systems where water resistance, barrier properties, corrosion resistance and mechanical integrity are critical.
For more information, email nathan.noyes@croda.com or marc.chan@croda.com.
Acknowledgement
The author wishes to thank Jo Grade, Jagdish Patil and Akshay Manekar for their contributing to application data and for all the thoughtful discussions.
References
1 Blackley, D.C. Emulsion Polymerization, Theory and Practice, London: Applied Science Publishers, 1975.
2 Piirma, I. Emulsion Polymerization, New York: Academic Press, 1982.
3 Erbil, H.Y. Vinyl Acetate Emulsion Polymerization and Copolymerization with Acrylic Monomers, Florida: CRC Pres., 2000.
4 Chern, C.S. Emulsion Polymerization Mechanisms and Kinetics, Prog. Polym. Sci., 2006, 443-486.
5 Lijen, C.; Shi, Y.L.; Chorng, S.C.; Shuo, C.W. Critical Micelle Concentration of Mixed Surfactant SDS/NP(EO)40 and Its Role in Emulsion Polymerization. Colloids and Surfaces A, 1997, 161-168.
6 Chern, C.S.; Lin, S.Y.; Chang, S.C.; Lin, J.Y.; Lin, J.F. Effect of Initiator on Styrene Emulsion Polymerization Stabilized by Mixed SDS/NP-40 Surfactants, Polymer, 1998, 2281-2289.
7 Aramendia, E.; Barandiaran, M.J.; de la Cal, J.C.; Grade, J.; Blease, T.; Asua, J.M. Journal of Polymer Science Part A: Polymer Chemistry, Vol. 42, Issue 17, 2004, 4202-4211.
8 Aramendia, E.; Barandiaran, M.J.; Grade, J.; Blease, T.; Asua, J.M. Journal of Polymer Science Part A: Polymer Chemistry, Vol. 40, Issue 10, 2002, 1552-1559.
9 Aramendia, E.; Barandiaran, M.J.; Grade, J.; Blease, T.; Asua, J.M. Langmuir, 21 (4), 2005, 1428-1435.
10 Kinya, Y.; Akinobu, I. U.S. Patent 4,814,514, 1986 (to Dai-Ichi Kogyo Seiyaku Co., Ltd.).
Looking for a reprint of this article?
From high-res PDFs to custom plaques, order your copy today!